In this two-part series, Wyeth's Gary Forrest discusses the challenges and benefits of implementing fieldbus technologies at a new bioprocess development facility. The second part can be read in the Q3 issue of Industrial Networking or by visiting IndustrialNetworking.net/wyeth2 right now.
By Gary Forrest, PhD, Wyeth Research
In June of 2002, groundbreaking commenced for a new bioprocess development facility at the Wyeth site in Pearl River, N.Y. Primary applications for the new building included process development and manufacturing of high-value products from microbial fermentation. New equipment consisting of 14 skid-mounted fermenters with working volumes of 75-1,000 l represented a key element of the facility design that required each of the process skids to be fully automated through the use of a modern, integrated process control system, which would permit batch automation in accordance with ISAs S88 standard.
It also was essential to equip the fermenters with instrumentation and controls that connected to the process control system via fieldbus technologies.
The Bus to Pearl River
Following the completion of a bid evaluation process for fermentation equipment, Wyeth selected Sartorius BBI of Allentown, Pa., to provide the fermentation skids.
The group responsible for bioprocess development at the Pearl River facility had been using an Emerson Process Management DeltaV process control system for fermentation process control since 1997. This system was installed in a building scheduled for demolition when the new bioprocess development facility was completed and occupied. Wyeth elected to move the license for the existing system and some of the process control system elements to the new building, and so chose Emerson as the automation supplier.
Computer hardware, control cabinets and software versions would be upgraded with the move. Although the DeltaV process control system originally was installed in 1997, an upgrade in 2000 added fieldbus instrumentation and controls. Foundation fieldbus temperature transmitters from Rosemount and pH transmitters from Rosemount Analytical were installed using a DeltaV Foundation fieldbus (FF) H1 communications module, and AS-i bus relay controls were installed using DeltaV AS-i bus communications.
The 2000 upgrade impressed Wyeth operating personnel with the stability and reliability of the FF devices and with the extensive diagnostic and calibration features available when used with the DeltaV system. The simplicity and compact design of the AS-i bus relays compared favorably with the hardwired relays they replaced. Experience with these two fieldbus systems led Wyeth to specify fieldbus designs for the new plant.
The new facility was intended not only to replace existing facilities, but also to add new functionality. For example, the DeltaV system in the new plant was configured to support the manufacture of both clinical and commercial products from microbial fermentation.
Good manufacturing practices dictated that the computer process control system be qualified along with all of its field instrumentation and controls. At Wyeth, the standard for computer control system qualification is based on the Good Automated Manufacturing Practice (GAMP 4) Guide for the Validation of Automated Systems, published by the International Society for Pharmaceutical Engineering in December 2001.
Two-Bus Trip
Sartorius, which provided the fermenter skids, specified the instrumentation and controls in accordance with guidelines Wyeth provided. Because of Wyeths previous experience with FF and the DeltaV system, the company preferred FF transmitters and control elements. However, many of the instruments and controls needed were not available as FF devices.
In those instances, Sartorius chose instrumentation and controls with Profibus-DP connectivity. In general, two-wire devices powered by the fieldbus were available as FF devices, and field-powered, four-wire devices required a Profibus-DP interface.
With these two fieldbuses selected, the fermenter skids could be controlled by two wired connections to the DeltaV control systemone wire for FF and one wire for Profibus-DP. Instrumentation that Sartorius selected for the fermenter skids included Rosemount sensors for pressure and batch and jacket temperature, a Fisher pressure control device and Rosemount Analytical sensors to monitor pH and dissolved oxygen (Figure 1).
Fieldbus-Tidy
The fermenter control cabinet has an uncluttered interior thanks to the use of fieldbuses instead of conventional communications devices.
Source: WYETH
Monitoring and control functions accessed through the fermenter display are based on field devices that communicate through a FF or Profibus-DP network.
The mass spectrometer exhaust-gas-monitoring readings present an exception, as its one of several secondary applications installed in the facility to support microbial fermentation. These secondary applications also include the monitoring and control of a biowaste system, the control of portable clean-in-place systems, the monitoring of ultra-low-temperature freezers, the monitoring and control of product-recovery equipment and the monitoring of an environmental control system.
For each of these secondary applications, fieldbus-based instrumentation and controls were specified whenever possible, but specific instances required conventional instrumentation. PerkinElmer Model 1100 medical gas analyzers perform fermentation exhaust gas monitoring (Figure 2).
These analyzers measure carbon dioxide, oxygen and nitrogen in the fermentation exhaust gases and provide the three measurements as 0-10 V outputs. The three voltages are converted to 4-20 mA and read by a conventional DeltaV analog input module. Exhaust gases are directed to the mass spectrophotometers by a 32-channel exhaust-gas manifold (Figure 3). AS-i bus signals are used to control 20 StoneL dual-relay devices. A complex 32-channel sequential function chart (SFC) program controls the exhaust-gas manifold, reads the data and performs calculations during a fermentation batch.
Gas Gets A Pass
Exhaust gases are monitored and measurements are output by Perkin Elmer Model 1100 medical gas analyzers.
Source: WYETH
Two portable, clean-in-place systems clean the fermenter skids. Connection to the DeltaV system is via a single Profibus-DP wire. Although two 4-20 mA transmitters are mounted on the skids for conductivity and level, Festo CPX analog modules convert the analog signal readings to digital readings for transfer to the DeltaV system via Profibus-DP.
A Yokogawa Daqstation paperless chart recorder for freezer monitoring includes an FF interface. Although the recorder can store data, the FF interface to the DeltaV system permits the use of the DeltaV continuous historian for data archiving. The chart recorder provides a local display of 72 hours of trending in the freezer rooms, while the permanent record resides on the DeltaV system.
32 Channels of Control
A complex 32-channel sequential function chart program controls the exhaust-gas manifold, reads the data and performs calculations during a fermentation batch.
Source: WYETH
The DeltaV system includes 572 I/O points, of which 96% are networked, bus-based I/O. Only 4% of the I/O on the system is analog instrumentation. The DeltaV system control cabinet has three DeltaV M5 controllers mounted on carriers with space for 16 I/O modules.
The second controller mounted on the middle carrier uses only three modules to monitor and control six fermentation skids. The modules include one FF H1 module, which provides two independent, field-network segments and two Profibus-DP modules, which provide a single field-network segment.
The monitoring and control of six fermenter skids represents a loading of 15 devices on each FF H1 segment and 12 devices on each Profibus-DP segment. The third controller on the bottom carrier includes an AS-i bus module and a single, conventional, analog-input module for exhaust-gas monitoring and manifold control. Controller 1 on the top carrier includes two FF H1 modules, three Profibus-DP modules, a digital-input module and two analog-input modules.
The additional modules on this carrier were required for many of the secondary applications described earlier.
Gary Forrest, Ph.D., is associate directorbioprocess development at Wyeth Research, Pearl River, N.Y.
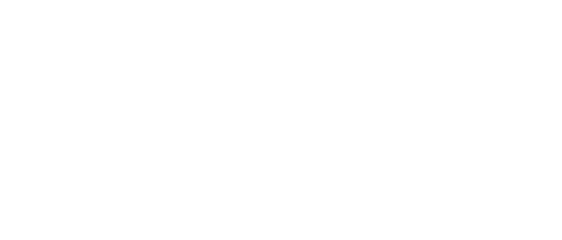
Leaders relevant to this article: