An industrial machine builder is thinking about upgrading to digital networks for communications among the controller, the I/O, sensors and maybe drives, but they’re concerned about diagnosing network faults and monitoring network performance on the machine. Are there software and hardware tools they’ll need to install directly on their machines? Which handheld tools can their techs and their customers’ techs use to check out digital networks? How much training should they expect their support personnel will need?
—from March ’08 Control Design
ANSWERS
Dream Team
No single digital network solution can do it all efficiently. But there is a clear champion team: Ethernet with AS-Interface. Ethernet offers the necessary simplicity and speed that is required to connect complex devices such as drives, HMI devices, RFID systems and the like. In general, Ethernet is the solution of choice for everything that produces large amounts of data. This is because Ethernet has unparalleled raw speed and a large telegram frame that allows big blocks of data to be transmitted quickly. Consequently, putting binary I/O devices on Ethernet is not a good idea. Since the telegram frame is large, transmitting the data from a simple binary I/O device effectively results in sending an empty Ethernet packet—a wasteful process that reduces the possible throughput necessary for the complex tasks of an automation system. This is where AS-Interface comes in.
TROUBLESHOOTING TOOLS
Technicians can use an analyzer and oscilloscope to test the quality of the network.
Source: Procentec
The combination of AS-Interface and Ethernet functions in much the same way as modern air travel. The airline asks customers to drive to the airport; it then flies those customers quickly across the country using planes that can seat hundreds of people. With the Ethernet/AS-Interface champion team approach, AS-Interface is tasked to quickly and deterministically collect all sensor inputs, set relays and electronic outputs, measure voltage levels and activate stack lights. An AS-Interface gateway consolidates this data exchange and enables Ethernet to transmit a single telegram frame containing hundreds of data points. As a result, the throughput on the Ethernet side is not bogged down by data packets that contain virtually no information.
In addition to efficiency and speed, this approach has numerous advantages.
Lower cost—Reducing the number of Ethernet components also means fewer switches and expensive cables are needed.
Flexibility—Ethernet is based on the star topology, unless additional switches are used. AS-Interface is the only topology-free industrial networking solution, thus allowing teeing off wherever needed; there are no limitations.
Processor independence—Currently, there are three dominant flavors of industrial Ethernet solutions promoted by major PLC manufactures: EtherNet/IP, Profinet, and Modbus/TCP. Using the gateway approach AS-Interface supports them all. Irrespective of which Ethernet implementation is used, I/O systems designed with AS-Interface are universally applicable.
Safety—In the past, functional safety was always seen as a necessary evil. With the introduction of AS-Interface Safety at Work, this is no longer the case. Worldwide, more than 50,000 safety installations using AS-Interface benefit from the simplicity and flexibility of AS-Interface, allowing safety to increase productivity at reduced overall cost: less downtime and fewer accidents are clearly desirable.
This automation dream team also shines in terms of diagnostics. Since not having to rely on diagnostics is still the preferred situation, AS-Interface has been designed from the ground up so users rarely depend on its robust diagnostics features. But when things go wrong, powerful tools are available. For instance, detecting welded safe contacts on e-stops and door interlock switches is as simple as adding a couple of rungs of PLC logic. And the hair-raising problem of diagnosing an intermittent safety contact is not even a challenge. In short, not having to use diagnostics should be the goal. Offering powerful but still simple diagnostics is a great addition.
Helge Hornis, Ph.D., manager, intelligent systems,
Pepperl+Fuchs
No Pussyfooting Around
The recommendations for diagnosing network faults and monitoring network performance really depend on the network and control system in use. Using only one network on your machine simplifies maintenance and diagnostic issues. Many machines still use multiple networks since pre-Ethernet fieldbuses were not universal enough to handle all control and communication requirements. From a Beckhoff perspective, the preferred network is EtherCAT with TwinCAT as the control and network management system. Features and functionality that are built into TwinCAT system service permit localization of all network faults and failures including those related to I/O, servos and cabling.
Beckhoff offers libraries for diagnostics and resetting of fieldbus systems that can be implemented through the PLC, meaning one could automate network diagnostics and repair via the PLC and remove requirements for third party tools. Therefore, maintenance personnel can focus more on fixing problems and less on finding them. All of these tools are available through TwinCAT system service and can be passed to the system’s PLC or HMI.
The choice of certain next-generation network systems can help avoid network faults and monitoring concerns in the first place. Users of EtherCAT, for example, achieve media redundancy simply by adding a second NIC card and closing the I/O system back to the controller configuration and actual network comparison, so if a device is plugged into the system in the wrong order, the system can still operate. Also, there is inherent high noise resistance/EMI from the use of Cat5e or Cat6 cables—the primary forms of wiring used in EtherCAT systems. In even noisier environments or where reference voltages differ, such as static or long distance, fiberoptics can be used for perhaps the most environmental tolerant cabling method available.
Corey McAtee, product manager,
Beckhoff Automation
Tools and Training
Troubleshooting and faultfinding are actually easier on digital networks than with conventional wiring by using the available tools. For Profibus networks in North America we frequently see tools from Softing and Procentec, distributed in North America by Grid Connect. Contact information for these companies can be found at us.Profibus.com. The tools speed network troubleshooting compared to poking around with a multi-meter on multiple terminal strips. Both vendors offer training on their tools. If industrial Ethernet is desired, Profinet offers built-in diagnostics including within network infrastructure components like switches. This allows diagnostic information to be easily conveyed to the controller for appropriate action or for forwarding to a display. Whatever network is chosen, training is highly recommended. For Profibus and Profinet, we offer free one-day overview classes and full week certified network engineer classes. One-day certified installer classes are also available on demand. In addition, customized classes can be offered on-site. For scheduled classes, click the training menu item on the website.
Carl Henning, deputy director, PTO,
Profibus and Profinet
July’s Problem
We currently use PLCs for control and a PC-based HMI for operator interface on our packaging machines. We would like to save some money and gain functionality by combining control and HMI into one PC-based platform. Last time we looked a few years backed, we were concerned with the ruggedness and reliability of industrial PCs. Has anything changed for the better?
SEND US YOUR COMMENTS, SUGGESTIONS OR SOLUTIONS FOR THIS PROBLEM. We’ll include it in the July ’08 issue, and post it on ControlDesign.com. Send visuals if you’d like—a sketch is fine. Email us at [email protected]. Please include your company, location and title in the response.
Have a problem you'd like to pose to the readers? Send it along, too.
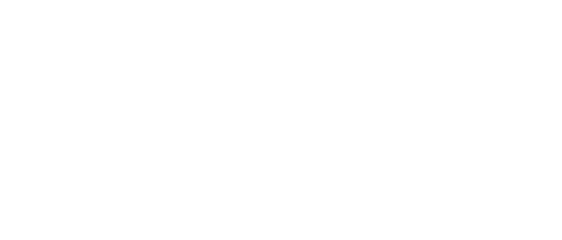
Leaders relevant to this article: