For more than 40 years, Schenck AccuRate has manufactured volumetric and gravimetric feeding systems, multi-ingredient batching systems, weighfeeders, mass flow meters, bulk bag discharging systems, vibratory feeders and controls to worldwide markets.
More than 90% of all products and systems, including controls, supplied by Schenck AccuRate are manufactured at its facility in Whitewater, Wis., or by its parent, Schenck Process in Darmstadt, Germany.
“Since the first flexible walled feeder was introduced more than 40 years ago, over 9,000 different foods, chemicals, pharmaceuticals, plastics additives and other materials have been systematically tested free of charge for customers all over the world in order to confirm configurations and 2 sigma performance levels,” says Mike Karas, marketing communications manager at Schenck AccuRate, which employs 120 people at facilities from Canada to Central America and is one of Schenck’s 25 worldwide locations, 14 of which are assembly and manufacturing operations. More than 85% of Schenck AccuRate’s customers are in the U.S., but that is changing. “We have seen positive growth in our Canadian and Mexican markets over the last couple years leading to a higher percentage of sales coming from outside the U.S.,” says Karas.
Wired for control
Systems Test Technician Phil Houk wires Schenck’s Disocont controls to a loss-in-weight dry material feeder.
Source: SCHENCK ACCURATE
“The food and pharmaceutical industries typically require a much higher level of sanitary design in the equipment we supply to them,” says Karas. “What that means for us is providing easy wash-down surfaces, electropolished finishes, crack- and crevice-free contact surfaces, completely enclosed motors and easy disassembly for cleaning. Typically, the chemical and plastics industry are looking for robust, durable equipment that can withstand harsh environments.”
Machine control is primarily PC-based because of Schenck AccuRate’s typical customers, but PLCs are an option if the amount of necessary integration is minimal.
“We use PC-based controls for our group control systems,” says Ron Tump, manager of controls development, at Schenck AccuRate. “This allows for a less-expansive solution than using a PLC and SCADA package.
Normally, the PC-based control will handle the coordination and interlocking of multiple pieces of equipment. It also provides recipe management, communication gateway and reporting functions.”
Schenck AccuRate also provides PLC-based group controllers and machine controls. “The group control systems provide the same function as the PC-based controls,” adds Tump. “However, our customers often would prefer having PLC hardware that is the same as what’s being used in their plants. The main disadvantage is that the price is several times higher using a PLC and the HMI from the PLC manufacturer. The PLC is cost-effective when a small amount of integration outside our dedicated controls is required. We call these systems mini-masters. We also incorporate a small PLC in our bag frame product.”
Schenck AccuRate’s main control is a proprietary weight and rate controller. “Because of the high-resolution weight signals, along with specialized filters and algorithms, this gives us the highest performance for the high-accuracy metering we do,” says Tump.
“Our feeders and controls have been designed to easily integrate with most common PLC networks,” he says. “In addition, we now offer Bluetooth and Ethernet communications along with RS232 for connection to our configuration tool.”
Ease-of-use is a driving factor for innovation at Schenck AccuRate. “This means we provide more descriptive messages and easier-to-use operator panels,” says Tump. He also foresees an increase in Ethernet use and network security.
“I see security being built into all equipment that is attached to the network,” he says. “I see wireless still having an acceptance problem, in that it is less secure than hardwired networks. More processing power in embedded processor equipment will improve the ease-of-use for the equipment. In addition, diagnostics and tuning of equipment will continue to improve.”
After a sale, field service engineers and spare parts specialists are available to answer questions, provide on-site training, assist with commissioning or to fill requests for spare parts. “We have an internal staff that handles all parts requests, and most orders can be fulfilled within a 24-hour period,” says Karas. “We also have a staff of field service engineers that are available for on-site commissioning and over the phone trouble shooting.”
CP-3 Telemetry Sentinel
One of Schenck AccuRate’s recent innovations for post-sales service and support is its CP-3 Telemetry Sentinel. “What it does is provide situational awareness of Schenck AccuRate equipment from anywhere in the world by alerting designated personnel of current and potential future problems,” says Ron Tump, manager of controls development.
The Telemetry package consists of temperature and vibration sensors along with the feeder controls, which are connected through RS232, EtherNet or wireless Bluetooth to a CP-3 embedded XP system. “The CP-3 sends notification of events and continuously logs data to an off-site server via Web page access,” explains Tump. “When a local LAN connection is not accessible, a cellular modem can be included. The user can also change what is monitored and who is informed of events anywhere and at any time.”
If on-site maintenance is required, a user-supplied monitor, keyboard and mouse may be connected directly to the CP-3, or the same function can be performed using a remote monitor over the Internet, says Tump.
“This system was designed for diagnosing potential problems before they occur,” explains Tump. “For example, a gradual increase in feeder speed for a given flow rate can indicate material buildup on the helix. The Sentinel can detect and provide alerts to this trend allowing for preventive action before complete loss of flow or control. Tolerances for vibration and temperature can also be set, alerting of imminent bearing failure or even fire.”
The Sentinel also can help keep managers informed of a plant’s progress from anywhere in the world by providing them notification emails at the start and stop of a process or giving them total material tabulation results at the beginning and end of each day, says Tump.
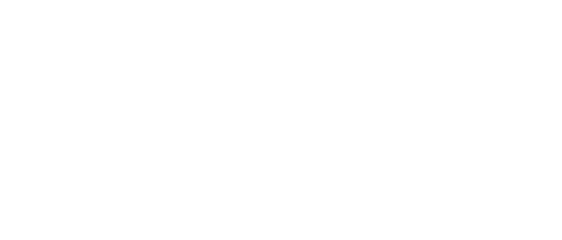
Leaders relevant to this article: