By Don Talend
High-speed, precision industrial applications are benefiting from recent advancements in stepper motors. These units provide reasonable positioning accuracy whether or not they provide feedback to the controller, and because they represent mature technology, prices are trending downward.
Suitable uses include label application and cylindrical plastic joint welding. Advancements in stepper designs beyond variable reluctance (VR) and permanent magnet (PM) designs are finding a niche in these types of high-volume applications without sacrificing positioning accuracy. Hybrid motors, which have a toothed stator and magnet in a salient-pole rotor for a flux boost, are the first step beyond VRs and PMs less-suited to these types of applications.
Despite the increasing popularity of servos and brushless DC (BLDC) motors for many industrial uses, steppers maintain a strong presence where speed and precision are at a premium. Although they typically don’t achieve sub-micron precision to the extent that servos can, steppers are well-suited to tasks such as barcode scanning where reasonable precision is necessary, and at a lower cost than servos. Also, the stepper generally provides greater reliability and precision than the BLDC. A major reason for this is the increasing use of rare earth magnets in steppers.
Resolution and Torque Are Keys
One high-speed industrial application that uses a stepper for considerable precision is the SL1500 Modular Label Applicator from Universal Labeling Systems, St. Petersburg, Fla. “The use of a stepper gives the machine the capability to dispense labels at speeds to 1,500 in./min,” says Frank Gruetzner, senior project engineer at Universal Labeling Systems. “The high starting torque reduces downtime for the machine operator while increasing machine utilization and productivity.”
Oksana Petrova, motion product specialist with Schneider Electric, says that high starting torque makes the stepper motor a better fit than a BLDC for the high-speed labeling machine. “Stepper motors have a higher starting torque than that of a brushless DC motor of a comparable frame size,” says Petrova. “A high starting torque is essential in labeling applications to overcome loads encountered with the label-application process. Stepper motors also provide a higher resolution than brushless DC motors. This higher resolution translates into better positioning accuracy, which is essential for labeling applications. Also, the stepper used in the SL1500 has low resonance. There’s no tuning involved with stepper motor systems, and they historically have a long service life and good speed and torque ratings.”
The permanent magnet design of the stepper used in the labeler is intended to provide high magnetic-field intensity at a reasonable price point, says Petrova, adding that the strong magnetization is caused by the use of rare-earth AlNiCo magnets (Figure 1).
An advancement in steppers that has been used for very-high-speed applications such as wristwatches has been transferred to an industrial application: barcode scanning. Among other technologies, Sick AG (sick.de), Dusseldorf, Germany, manufactures barcode scanners used in tasks such as classifying and sorting products and calculating volumes. This application requires rapid oscillation of a mirror to deflect laser light. A photodetector measures the amount of laser light reflected back by each element of the barcode and the images are decoded into numerical data.
Acceleration and precise positioning are critical performance criteria for barcode scanners, says Christoph Anselment, mechanical design group leader for Sick AG. “We want to switch the focus position in the shortest time,” he notes. In its scanners, Sick AG uses a 16-mm Turbo Disc motor from Portescap, a variation on the stepper motor that uses disc-shaped magnets instead of more conventional cylindrical magnets.
Dave Beckstoffer, product manager for Portescap, explains that the Sick AG scanners can provide greater resolution and thus accuracy because the Turbo Disc motor can achieve 40 steps per revolution—about twice that of conventional steppers. The motor’s disc-shaped magnets provide axial, as opposed to a conventional stepper’s radial, magnetization to yield greater acceleration (Figure 2).
MORE PULSES PER REVOLUTION
Figure 2: A disc magnet design in this stepper motor, which is used in a barcode scanner, allows for a higher number of poles, yielding a higher number of steps per revolution.
PORTESCAP
Disc-Magnet Origins
Both of those applications illustrate a greater suitability for steppers versus a likely alternative: the BLDC. A stepper in general offers advantages over the brushless DC motor alternative for such high-speed precision applications, argues Beckstoffer. “The migration toward the use of steppers for these applications,” he notes, “is directly correlated to the growth of the semiconductor industry. Steppers rely on the number of stages and pole pairs for the number of steps per revolution, whereas the BLDC uses a feedback transducer such as an encoder or a resolver. The stepper offers greater reliability than the mechanical commutation system of DC motors.”
Beckstoffer categorizes the disc-magnet (DM) stepper into one of two basic stepper groups. The first group consists of VR steppers, which work without permanent magnets, and the second is made up of PM motors, hybrid motors and disc magnet motors. Hybrids were developed in an attempt to combine VR steppers’ small step angle advantage with PM steppers’ better performance due to the presence of a magnet in the air gap, says Beckstoffer, adding that the hybrid motor has both a permanent magnet and teeth that physically modify the air gap as the rotor moves, changing the inductance of the phase winding with rotor position.
The use of the DM stepper motor, first in quartz-controlled wristwatches requiring small and efficient motors, grew largely out of the availability of rare-earth magnets such as samarium cobalt and neodymium, points out Beckstoffer. These magnets have high magnetic energy that allows magnetization of a long air gap.
Stepper and Servo Together
Advancements in stepper motors such as the DM stepper are blurring the capabilities between steppers and servos, says Beckstoffer. “Power normally is the first criterion in deciding between the two,” he adds. “Usually, steppers are the choice for applications requiring less than 1,000 rpm, and servos get the nod for applications that need more than 3,000 rpm. But this is changing, especially in the 1,000-rpm range. Despite the fact that servos are broadening their application range, steppers still are about 30% less costly than an equivalent servo system, though not as relatively inexpensive as in the past.”
Although it doesn’t represent an evolution in the design of steppers itself, Extol, Zeeland, Mich., a manufacturer of automated plastic assembly machinery, integrates stepper and servo control to gain precision in its Vortex G Series Servo Spin Welder. This equipment welds together products with cylindrical joints that are used in the automotive and healthcare industries, such as plastic engine oil fill necks. The welder uses a Wago stepper module with a servo drive that integrates both stepper and servo control.
STEP IN TIME
Do you use steppers for applications where others might choose to use servos these days? Share your story at ControlDesign.com/stepper.
“Our application is a little unique in that we’re using a stepper output module, but we’re sending the stepper pulses to a servo drive,” says Rob Bouws, human-machine relationship engineer for Extol. “So it’s kind of a hybrid stepper/servo combination. The servo drive is receiving the pulses from the stepper output and the drive is closing the loop. When the stepper sends pulses to the drive to tell it what position to go to, the drive receives that input, and then it in turn moves the motor, and then the encoder feedback on the motor goes back to the drive, and the drive is making sure that the motor is going to the position that the stepper told it to go to. This is a little different from a straight stepper application in which you’re driving a stepper motor off of a stepper drive. What we’re doing here is controlling a servo motor with a stepper output, and the drive for the servo motor is designed with the ability to accept those stepper pulses from a stepper output card.”
A stepper motor is used, notes Bouws, because of some inherent stepper motor advantages. “One of the most important features we look for with the spin welder is positioning ability and with the stepper we have the ability to finish at a final position, which you wouldn’t have with just an ordinary motor,” he says. “We first developed this product with a small motion controller, which was integral to the servo drive, but it didn’t have the ability to do positioning on the fly. So we recently changed to this stepper module because it was, for one, low cost compared to a lot of servo applications, but it also had all of the positioning capabilities that we needed.”
The integration of the stepper motor and servo drive control into the fieldbus node eliminates the need for a separate motion controller, and this configuration provides a benefit in terms of programming, states Bouws. “We’ve eliminated the second motion controller, so the motion control is integrated with the PLC control within the programmable bus coupler,” he says. “They’re actually together, and it makes programming easier because you only have one application to program. It’s a time savings, but it’s also easier to understand because you see directly how the motion components interact with the discrete logic components and there’s no handshaking that has to go on between the two; they’re integrated seamlessly.”
Don Talend is a publicity and communications project manager specializing in the technical trade media.
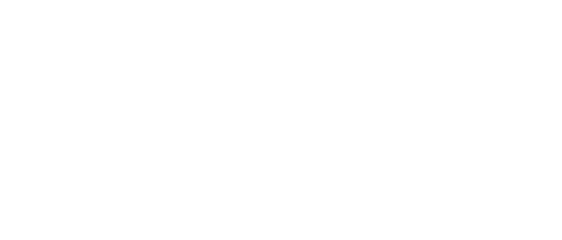
Leaders relevant to this article: