We currently use PLCs for control and a PC-based HMI for operator interface on our packaging machines. We would like to save some money and gain functionality by combining control and HMI into one PC-based platform. Last time we looked a few years back, we were concerned with the ruggedness and reliability of industrial PCs. Has anything changed for the better?
—from May ’08 Control Design
Answers
Time Changes Everything, Hardware Too
In the 1980s and 1990s, there were huge concerns over PC stability in general, and industrial computers at the time simply added cost to a generally unstable platform. There were problems with the hardware, the OS and the software. The hardware all required fans. The dust in industrial environments would clog the fan filters and reduce the cooling ability, or it would get into the systems, build up on components and cause heat and signal quality issues. Additionally, the rotating drive media available was not conducive to industrial environments due to heat and vibration found in those environments. The OS was either some proprietary code or it was Windows-based. The proprietary code usually would perform well but left the owners in a tough spot when they needed to upgrade or make changes. The Windows OS was very new and took several years to become stable.
EXTREMELY RUGGED
Extremes of heat, moisture, vibration and shock require a PC and HMI durable enough for any environment.
GLACIER COMPUTER
With this level of stability in the OS and environmental readiness in the hardware, quality industrial computer systems can be found.
David Gardner, product manager,
Wonderware
In the Heat of the PC
Product requirements for manufacturing computers differ widely based on industry and application. Using computers to do control and HMI tasks on one unit realizes significant cost savings.
Engineering costs can be reduced greatly since they often share the same database. Since both HMI and control are critical to an efficient manufacturing process, obvious care must be given to reliability. There have been significant advancements in recent years to increase the reliability of industrial PC systems.
The primary points of failure in a PC are the moving parts, basically the fan and the hard drive. Different mounting configurations and motherboard design changes help reduce these potential points of failure. Current industrial designs must have shock-absorbed hard drives.
Also check to see if there is a single fan or multiple fans to extend operating temperature from commercial grade PCs. Air flow is critical to disperse heat. The microprocessor should have special thermal designs to dissipate the heat generated by today’s high clock speeds. Extensive heat sinks have been developed to dissipate the heat.
To ensure corrective actions can be taken if problems develop, make sure the PC has built-in software capability for monitoring overheating.
All data and programs can run off compact flash and since the CPU requirements for the operating system are reduced, fans no longer are required. Keep in mind industrial-grade compact flash with 2M write cycles, will cost more than commercial, 100K-write-cycle, grade. Commercial grade shouldn’t be used for control or HMI.
Harold Muma, product marketing manager–HMI,
Siemens Energy & Automation
Cables and Connections
Another technological improvement is industrial displays that can withstand up to 50 °C. For rugged applications, these would be an ideal solution over a commercial display.
On the design side, machine builders should seek out industrial computers with the fewest number of cable connections to the computer, as well as cable connectors that lock in place. Gold plating on cables helps improve connectivity and stands up better to corrosion.
One advantage of industrial computers versus commercial PCs is component stability that benefits hardware longevity. Manufacturers that use commercial computers start with one product and one hardware platform. However, if they want to add another PC a few months later, chances are high that the hardware will be different. This means that they will have to make changes to the software image already loaded on the first product to make it work on the new product. Industrial computers are managed for longer periods, making maintenance much easier and significantly reducing development efforts.
Kari Doyle and Mike Schweiner, product managers,
Rockwell Automation
A PC Is Not a PC
Machine builders must specify the right PC for the job and consider these criteria that distinguish an industrial PC from an office-based PC.
Product shape and ergonomics
- All-in-one device designed for panel, cabinet or rackmount
- Embedded keyboard and/or pointing device (touchscreen)
General and environmental characteristics
1. Open operating system using an AC or DC power supply
A. Qualified to operate with other industrial devices (PLC, drives, software)
B. Bundled with automation products
C. Designed with industrial grade components
2. Industrial environmental characteristics
A. IP65 and NEMA 4
B. Ambient temperature range: 0–50 °C
C. Vibration operating at 1 G, 57-150 Hz
D. Shock resistance 15 G over 11 ms
E. Immunity to interference per EN61131-2, UL/CSA regs
Certification and Service
1. Industrial certification: UL508 and UL1604, CSA, Marine
2. Product availability more than three years with service for four years or more with the same products available worldwide
Haroon Rashid, manager product marketing,
automation and functional safety products,
Schneider Electric
Pair Panel PC With Processor
Industrial PC (IPC) technology advances have permitted the all-in-one combination of control and HMI for several years now. The most popular form of this today is via an IPC directly attached to a TFT screen intended for mounting arm, pole or cabinet mounting. With the increased performance offered by modern dual core processors, it’s no problem for one industrial PC with a built-in display to handle the HMI and all control.
When paired with the appropriate automation software, everything from PLC functions all the way up to complex, multi-axis CNC applications can be on the same IPC as the HMI. Beckhoff IPC users have the choice to select a stand-alone IPC that will run all control and HMI functions and connect to separate TFT displays over 100 m away using a DVI/USB connection. This ability to do more control and HMI with fewer controllers saves a great deal of equipment cost upfront and long-term costs by reducing required controls design time—programming one central controller rather than numerous distributed controllers.
Milo Grika, industrial PC product manager,
Beckhoff Automation
Quality Improves in a Flash
For every 8 °C temperature reduction, the life of an electrical component doubles. Rugged computer vendors are benefiting from cooler components and advanced methods of getting heat out of fanless enclosures. Processor makers such as Intel have introduced Pentium M and, more recently, Dual Core processors, offering low temperatures and high processing power.
And the testing of rugged computers has advanced and now includes not only emissions and safety, but highly advanced life testing, which reduces “infant mortality” and ensures long term 24/7 mission-critical operation.
The use of rugged computers onboard vehicles, including forklifts, over-the-road trucks and construction equipment, has mandated that these computers be capable of withstanding extremes of heat, moisture, vibration and shock. Distributed computing to far reaches of the work environment has forced rugged computer makers to develop reliable units at more affordable prices.
Flash drives are undoubtedly one of the biggest improvement areas of the past five years. Initially designed for cameras and MP3 players, solid-state flash now is a low-priced, wide temperature solution for rugged computers. It is highly common for customers to now request 4 Gb and 8 Gb solid-state drives with XP Pro. This allows units to be installed in any environmental extreme.
John Geary, vice president,
Glacier Computer
SEPTEMBER’S PROBLEMOur metal cutting machines include some low-level robotics, so safety is a huge issue. The more we look into safety components, the more muddled it gets. We can provide a low level of protection easily, but making our machines really safe without crippling output is an expensive and complex proposition. How should we decide what level of safety is right for our custom machinery? SEND US YOUR COMMENTS, SUGGESTIONS OR SOLUTIONS FOR THIS PROBLEM. We’ll include it in the September ’08 issue, and post it on ControlDesign.com. Send visuals if you’d like—a sketch is fine. Email us at [email protected]. Please include your company, location and title in the response. HAVE A PROBLEM YOU’D LIKE TO POSE to the readers? Send it along, too. |
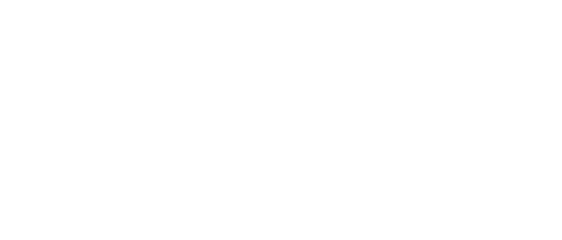
Leaders relevant to this article: