By Mark Lamendola
Have you ever had a conversation with a customer to discuss the value of a machine rebuild project? It can be an obvious alternative to buying a new machine, particularly if the need to physically replace the old one isn’t clear cut. This is particularly true in machine shops.
Our research tells us that the three principal types of rebuild projects are, from least scope to greatest, an automation upgrade, a recondition/rebuild and repurposing an existing machine.
Upgrade the automation. Upgrading a machine’s controls can produce such advantages as improved safety, reduced scrap, reduced setup time, quicker changeovers, lower cost per run and more flexibility in scheduling the work.
Recondition/rebuild. It’s getting harder for the machine user to hold tolerances because the ways are worn on a machine that is otherwise in good condition. Or they’ve had problems because the insulation on the control wiring has degraded over time. At significantly less cost than that of a new machine, you can correct the problems of the existing unit.
Repurpose. The customer uses a given machine to make Product X, but that market has softened. Now the company needs to make Product Y because there’s a demand for it. To do that with the existing machine requires adding a particular feature or two, which, by rebuilding, can be done.
The typical shop doesn’t have the time, space, or expertise to handle rebuild projects. Fortunately, a machine rebuilder, whether a standalone rebuilder or a machine builder that offers rebuild services, does.
Gear Technology, Rancho Cucamonga, Calif., is a precision gear-maker serving the military and commercial aerospace industries. “If you have a piece of equipment you really like, but it's getting old and tired, should you replace it outright?” ponders Tom Marino, president. “Why not just update and refurbish it?”
But wouldn’t you still have an old machine when you’re done? Marino says that’s not the case. “I'm buying a gear hobber that's a 1989 machine,” he states. “This machine is being completely rebuilt and recertified and comes with a one-year warranty.”
Automation Upgrades
Upgrading the controls is perhaps the most common type of project. Guptill Gear, Anaheim, Calif., manufactures a variety of gears—fine pitch, precision, helical, friction, conical, spur, bevel, rack, pinion, and ring—for a variety of industries. It also provides forming and heat treating. “There's a lot of electronics involved with a controls upgrade,” says Ron Guptill, president. “All the wiring is brand new, and you get the latest controller, so that part is really new.”
Controls Refit
This control cabinet replaced the original controls. Classified as a controls rebuild project, in reality, the control system was designed in CAD and custom-manufactured in a factory setting.
(Source: Machine Rebuilders)
Milwaukee Gear Co., Milwaukee, makes custom gears for more than 20 industries including transportation, plastics, energy, refrigeration, defense, food, mining and power. “We had several machines that were mechanically sound and still good technology, and yet would do more for us if upgraded,” reports Rick Fullington, president. “The difference between the existing machines and upgraded versions would consist of the controls, motors, drives and some wiring.”
Retrofitter Trend Machinery, Willowbrook, Ill., recently completed a job on a four-axis, CNC Normac grinder at Sandusky International in Ohio. The machine resharpens the gun drills that put thousands of holes into paper-mill rollers. The grinder no longer held permissible tolerance positions, and replacement parts and service were more difficult to obtain.
Founded in 1976, the company designs and builds custom machines, with a particular expertise in grinders. Trend also performs CNC retrofits to update obsolete controls, as well as motion control systems integration and turnkey machine conversions from manual to programmable operation.
“The machine was sent to us for evaluation,” says Bob Gordon, president of Trend Machinery. “We determined what the equipment needed, including a new CNC to replace the original control, as well as drives and motors. We also customized an entirely new control console and enclosure for Sandusky, and we replaced all the electronic hardware such as starters and relays.” Trend also replaced all limit switches, modified the motor mounts and repaired the grinding spindle.
The machine was returned to Sandusky with full electrical schematics, bill of material and program files; plus the Normac grinder was cleaned and completely repainted to customer specification. Trend supplied a one-year warranty on all parts, backed by Siemens, which was the primary component supplier, including the CNC.
“The work was done on time, in a professional manner and at the price quoted,” explains Ron Gearhart, machining technician at Sandusky. “This was an excellent investment for our company, as the machine has been performing beyond our expectations.” He says this is due in part to the enhanced features on the new CNC, the thorough documentation supplied and the neat appearance of the controls. “The organization of the electrical panels was further evidence of a job well done,” he concludes.
Let’s Get Mechanical
Xtek, Cincinnati, manufactures custom-machined and heat-treated parts and component assemblies for heavy-duty industrial applications. The company produces critical components such as brake wheels, track wheels, crane parts, sheave wheels, gear couplings, u-joints, mill pinions, pinch rolls, work rolls and custom gears.
What drives its decision about a mechanical rebuild? “Reduced performance or reliability,” explains Tom Huth, facility and project manager. “If the machine could cut a gear to AGMA Standard Class 12 when it was new and now cuts only to Class 8 and breaks down a lot, then I would start making the case for rebuild or new. My big question is do I have a good platform to rebuild.”
A partial electromechanical upgrade was part of a gear shaper project at Milwaukee Gear. “In addition to upgrading the controls, motors and drives, we did a complete hydraulic package upgrade,” says Scott Bowman, maintenance supervisor.
If the machine had been purchased new, the builder would have provided run-off data regarding geometry and performance. “In a full mechanical rebuild, the objective would be to return the machine to the original specs,” says Huth. “First you would establish current capability so you can define the scope of work.”
Sometimes, the end user defines the problem and works with the rebuilder to determine what needs to be done. “The gamble you make is you're getting something unknown,” says Guptill. “How do they really know if the worm wheel is worn too much? There's a lot of trust involved. You have to get a rebuilder who is on the same page as you, someone who knows the manufacturing process.”
Referring to a project he’s now evaluating, Huth says the scope “would require replacing/refurbishing ballscrews. It would mean planing and scraping columns and beds. Depending on the severity of the wear, it might require brass or turcite applied to surfaces and scraped in.” A mechanical rebuild can go well past conditioning, says Huth, “It could include replacement of hydraulics, pneumatics, lubrication systems and all critical bearings.”
Considering Cost
A rebuild can produce significant savings over buying new, possibly driving the rebuild decision for specific equipment. “I get the same performance of a new machine at half the cost,” says Marino. “For a small gear shop like mine, this really is the only way to buy capital equipment.”
Measure Twice
This is a major mechanical upgrade in progress. After removing some major components, engineers at Machine Rebuilders took measurements for CAD drawings. No modifications will be done until the engineers review those drawings with the customer.
(Source: Machine Rebuilders)
Sometimes cost isn’t the major consideration. For example, Guptill couldn’t find a machine that allowed the kinds of changeovers he wanted to do. “One of the main reasons I purchased a rebuilt machine is the carcass they used has a tail stock,” he says. “On the machines we looked into, you have to remove the tail stock with a lift truck if you want to cut internal gears. I wanted mine on a set of ways, so it could be retracted to allow me to cut internal gears. The solution was a custom machine.”
Marino has a CNC gear shaper machine and needed a sector gear program for it. “The gear shaper manufacturer wouldn't guarantee the sector program he wrote would actually work,” he states. “I contacted a rebuilder we know, and he told me, in no uncertain terms, that he would write the program and it would work. He said that, if for any reason, I was not happy with his service I did not have to pay him. That program took my cycle time down from 60 min per part to 7 min. The cost savings based on the reduced cycle time was more than enough to pay for the rebuilder’s services.”
Sometimes, the product is available, if you don’t mind waiting. And waiting. “The bottom line is cost and availability,” says Guptill. “We have only one company in the U.S. that will build a gear shaper. There's a German company I like, but the lead time is one year.”
Premier Gear, Corona, Calif., integrates gear manufacturing and precision machining. Its products range from individual components to complete assemblies and from high-volume orders to low-volume custom work.
Steve Golden, production manager at PGI, asserts that rebuilds make the most sense for equipment made by only a few manufacturers. “I don't know that I'd buy a rebuilt lathe or mill,” says Golden. “It's a generic piece of equipment, rather than a specialized one. The advantages of custom work are diminished. There are many manufacturers and the competition makes a difference. You don't have that competition in gear cutters.”
Sometimes, going with a rebuild boils down to the fact that most of the machine doesn’t need to be replaced. “We have two Liebherr LC-1002 machines purchased in the early 1990s,” says Huth. “They’re solid machines and have served us well. We were experiencing reliability issues with the controls and electronic components. We decided to retrofit our machine with new controls and drives.”
Referring to his machines, Golden says, “The basic platform is solid and proven. It’s not always wise to throw out that platform and start over.”
Experience shows that it doesn’t pay to just jump into a rebuild project. Remember, it’s a project and not an off-the-shelf purchase. Work your numbers before deciding. “We approached this upgrade question the same way we would any other capital expenditure, by considering all the options and the ROI,” says Fullington. “The ROI analysis based on preliminary cost data revealed there would be far greater value in rebuilding what we had than in a complete replacement of that equipment.”
Fullington’s next step was to contact a machine rebuilder. “Two engineers from that company came in and worked with us to plan it,” he adds. “This included project scope, scheduling and pre-work.”
Bowman evaluates how upgrades can extend the original investment. “We had a rebuilder retrofit four Liebherr gear hobbers made between 1986 and 1992, and one 1982 Fellows gear shaper,” he says. “The retrofit included complete new control panels with Fanuc controls and all new Fanuc AC motors and drives to replace the original DC motors and drives. The AC motors don’t require the maintenance of DC motors because there are no brushes to wear. These upgrades will extend the lives of the machines. The original controls and drives had become obsolete and parts were hard to find.”
Support is a huge issue. It might seem that if you buy something new, a grateful manufacturer will ensure you’re up and running in a timely manner. The reality is different.
“U.S. manufacturers went out of business,” says Golden. “Gear machine manufacturing worldwide is tight. You basically go to Europe, and doing so creates service issues that haven't been good in our experience. With a rebuild, we can use an old machine to get exactly what we want. We have something we're familiar with and something we can get parts for. Price is actually a secondary concern.”
Bowman says his rebuilds were completed within the timeframe that was promised. “More importantly, our rebuilder was very responsive to problems we encountered,” he adds. “They used readily available parts that we usually can get in a day, so we don’t have extended downtime while waiting for parts from overseas.”
Huth says Xtek had positive experiences with a particular machine rebuilder, so he contacted them again to discuss further needs. Coincidentally, they recently had refurbished machines like his.
“One company I strongly dislike sells to large accounts and lets us little guys go unsupported,” says Golden. “We’ve found with rebuilders, especially the one we use, that we get solid support and fast responses to our questions.”
Referring to his experience with a rebuilder, Huth says, “They did a significant part of the job at their facility. The first machine was back in production in three weeks. The training provided to our operators allowed them to quickly assimilate the new controls. The second machine was completed shortly thereafter with the same expedience and professionalism. I’m pleased with the whole experience. The rebuilder delivered exactly as promised.”
Golden says PGI will rebuild its machines in the future but also might buy new. “After the warranty date, we still need support,” he says. “Our use of the machine doesn't end when the warranty ends.”
Measuring Results
But what kinds of improvement numbers did these guys get? Huth says, “Prior to the retrofit the machine was averaging 38 hrs/wk of production and producing class 8-10 gears. Post retrofit, the average was 59 hrs/wk, and it routinely produces Class 12.”
Golden’s metric focused on output. “We bought an old machine and had it rebuilt,” he says. “By doing this, we added a workhorse machine that increased the output of the gear-shaping department by 25%.”
So, why buy new? “The investment matched the need, and consequently we invested half as much in a rebuild as with a new machine to get the same 25% production increase,” says Golden.
Asked why he didn’t repurpose his existing capacity, he says he could have used more capable machines for the same work, but “that’s like hitting a tack with a sledgehammer. By offloading work from other machines that are more capable, we freed up those machines for work that we would not otherwise be able to take on.”
So, that 25% increase in one department had a cumulative effect that let the company better serve customers. The project seems to serve the operators well, too. “We now intend to rebuild the other machines in this department to standardize the controls to what we did on this project,” says Golden.
Have you thought about rebuilding machinery instead of buying new? How far did you take that idea? Did you find a hurdle you just couldn’t overcome, or are you using rebuilt machines. Let us know at ControlDesign.com/rebuild.
Other ServicesA machine rebuilder might offer other services. Two of the most popular are those of salvage and scavenge. Scavenge means to comb through old machinery looking for parts you need for a particular project or a known future need. Scavenging projects are usually for scrap equipment you are considering purchasing in whole or in part. Maybe you find an old machine at an auction or can pick it up cheaply from a liquidator. If you have your own boneyard, you might scavenge there for parts. Neither of these is a refurbishment project. Either can prove beneficial, if done right. As with refurbishment projects, it usually makes sense to outsource this kind of work. Select a company with experience in salvage and scavenging. Its staff will know what to look for, what’s worth keeping and where to draw the line on resources used. |
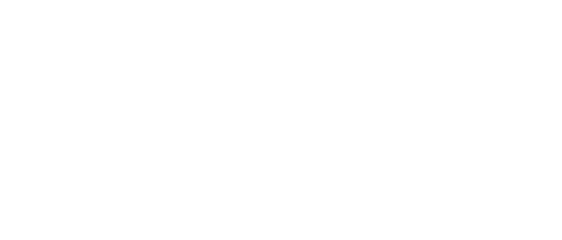
Leaders relevant to this article: