For a complete list of measurement and sensing articles, white papers, news and products on the website, visit ControlDesign.com/measure.
By Paul Miller, Contributing Editor
While silicon wafer fabrication involves many discrete manufacturing operations, there also are process variables being controlled. The critical clean room heating, ventilation and air conditioning (HVAC) systems present some especially interesting closed-loop control challenges.
Semiconductor product yields depend heavily on environmental conditions inside the fab’s clean rooms. Not only must ambient temperature and humidity levels be maintained within very tight tolerances, airborne particulates also must be carefully controlled because they can render semiconductor components worthless.
For these reasons, clean rooms use extensive HVAC systems with high-performance filters to tightly control temperature and humidity, while filtering airborne particles. Typically, powerful recirculation air handlers (RAHs) provide high-velocity air at a uniform temperature. This creates a unidirectional or laminar flow of air through the clean room. The straight parallel streams of air at high velocity carry away airborne particles and prevent wafer contamination. The temperature in the clean room is controlled to ±1.5 ºF. To maintain this accuracy, each RAH relies on a cooling coil, a set of isolation dampers and a fan.
Teaching an Older Fab New Tricks
At one large wafer fabrication facility, more than 160 truck-sized RAHs are aligned in a grid high above the 125,000 ft2 clean room (Figure 1). When the fab was originally built, nearly 100 air handlers were installed. Unfortunately, only a few actually were commissioned before the project was put on hold in the late 1990s, when overcapacity hit the previously red-hot semiconductor manufacturing industry.
Fan Deck
Recirculation air handlers (RAHs) are aligned in a grid to provide the fab’s clean room with tightly controlled and filtered air.
Source: CH2M Hill
The minimal controls installed at the time were inefficient at best. Since the motors ran at a constant speed, workers had to climb several stories to adjust the air regulator that controlled the airflow to the damper solenoids. Not only was this a poor use of labor and a potential safety issue, it also resulted in wasted energy and unnecessary motor strain.
When the decision was made to reopen the fab, the wafer manufacturer also decided to update and coordinate the controls for its critical RAHs. For this accelerated project, it sought help from what was Industrial Design, a global engineering firm in Portland, Ore., for engineering procurement contractor, CH2M Hill.
gt;“For our customers, time to market equals time to profit,” says Gary Mays, the firm’s instrumentation and controls manager. “Our first priority is to get our customer up and running as quickly as possible.”
To save time, CH2M Hill initially considered using the existing motor starters. However, it quickly became apparent that this was neither the best control approach nor the most cost-effective solution for the air handlers.
Instead, it worked with Rockwell Automation to develop and implement an intelligent motor control solution for the RAHs. The solution included intelligent, variable-speed drives, a ControlLogix programmable automation controller, ControlNet networking, and FactoryTalk View human-machine interface (HMI).
“The traditional problem with VFDs used in clean room environments was they had bimetallic overloads that could trip and turn off,” says Steven Goh, marketing director, Asia Pacific, at Rockwell Automation. “In this case, intelligence means adding electronic overloads and presets to avoid those trips. Now, users know when something is beginning to happen to their motors, such as drawing higher current, and they can monitor 200-300 motors on one screen.”
No More Homerun Cabling
Using its existing motor starters, the fab previously would have needed to hardwire each starter back to the controller cabinet. By networking the smart drives, they could install one communications cable between the drive and controller cabinets. The temperature transmitter, control valve, damper position switches and damper solenoids in each RAH unit were all wired directly to the drive mounted on the RAH unit, eliminating the need to homerun these instruments to a central control panel.
Besides reducing wiring and installation costs, this approach created a centralized point for all drive programming and file storage, providing the flexibility and integrated capabilities that would carry the fab into the future.
Drives Pay Their Own Way
“When we evaluated our equipment options, Rockwell didn’t have the lowest initial purchase price,” says Mays. “But when we assessed the total cost to design, develop and deliver the solution, their variable-frequency drives easily paid for themselves.”
Because space is at a premium in a wafer fab, design firms look for innovative ways to reduce equipment footprints. CH2M Hill engineers designed the RAH control system to allow field I/O to be wired directly to a drive’s I/O board, essentially using the drive as a distributed I/O drop. Networking the drive’s I/O back to the controller eliminated the space required for new panels and conduit runs, saving valuable real estate.
Drive operating status and speed are communicated to the programmable controller via the network. When the RAH is in auto mode, the unit is stopped and started from the controller via the network.
The controller closes the temperature PID loop based on the actual temperature in the clean room and the desired setpoint. The controller automatically adjusts the motor speed as needed to keep the clean room pressurized.
An EtherNet/IP connection routes critical operation information to a central control room. From there, the HMI software provides operators with information about each unit’s status including fan speed, supply temperature, setpoints and control valve output percentage.
“Access to information is the foundation of intelligent motor control,” explains Mays. “One of the benefits of using the intelligent drives is that they provide about five times more information than a non-networked drive. That gave our customers the competitive advantage to review trending information and schedule preventive maintenance, a critical step considering these plants often run all day, every day.”
Based on previous experience, CH2M Hill understands how critical network certification is to eliminating and preventing communications issues. Once the ControlNet network was in place, it called on Rockwell’s network engineering specialists to help verify and validate the network.
These specialists tested the network to make sure the signal loss across the network was acceptable, network lengths were not exceeded, and connections were made properly. Network verification reduces the risk of last-minute problems, when they’re often more difficult to identify or can have a big impact on the overall project schedule.
More Than $500,000 Saved
The intelligent motor control solution helped save the semiconductor fab owner more than $500,000 in installation costs, according toCH2M Hill’s estimates. Reduced wiring, as well as centralized configuration and maintenance, generated real savings during the startup and commissioning of the project. The fab owner will continue to reap savings through better control, enhanced diagnostics and easier troubleshooting. For example, if one of the drives needs to be replaced or a unit moved to a new location, configuring it will take just a few minutes, compared to more than an hour in the past.
“Programming the drives and controllers and a couple of hundred motors used to take a couple of months to do, but now we can create software profiles and templates and just paste them into each device with fewer mistakes and more consistency,” adds Goh. “This can save lots of money because downtime costs so much. Users now can save at the design, engineering and commissioning, maintenance and other stages of the lifecycle, especially as they gain more of the benefits of predictive maintenance.”
Discrete manufacturing inevitably leads to process control considerations and vice versa. Elements of one find their way into the other with regularity. Let us know about some of your more challenging and vexing hybrid encounters at ControlDesign.com/hybrid.
For a complete list of measurement and sensing articles, white papers, news and products on the website, visit ControlDesign.com/measure.
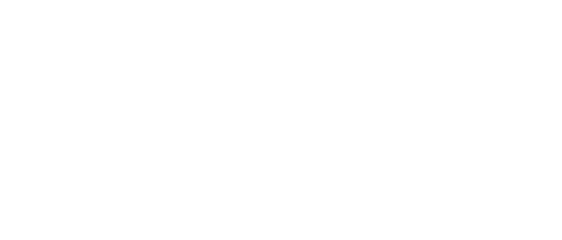
Leaders relevant to this article: