Our control panels include five panel meters that receive from the PLC and display analog parameters like machine speed and temperature to machine operators. Our panel meter manufacturer is going out of business, and we’re wondering if we should just switch to another manufacturer or go to a solid-state graphics display. We know the graphics display could show lots of information besides just five meter readings, but we’re concerned about up-front hardware costs and about controlling software development costs. What's the best way to go?
—from August ’08 Control Design
ANSWERS
It’s All About the Operator
Solid-state graphic display costs have dropped considerably in recent years. The competitive HMI market, coupled with Asian manufacturing, has made it possible to get small LCD micro HMI panels for less than $200, which is less than many panel meters currently on the market. Some suppliers also offer free programming software to reduce development costs. Most of the micro HMI graphic panels support hundreds of screens and also display dynamic alphanumeric text as well as graphical objects such as meters, bar graphs and alarming. You also could consider using objects that allow operators to adjust set points for connected devices that control variables such as temperatures, speed, timing and flow rates. This most often is done using software objects such as a numeric entry keypad or slider objects, greatly expanding the amount of data displayed and the operator’s ability to control the process. If you can improve productivity by allowing more data to be displayed and provide better control for the operators, then a micro LCD HMI panel might be worth using. It is possible to replace your panel meters with lower up-front cost and development time than expected.
Which reading best describes the forthcoming problem?
Source: Yokogawa
Consider whether the HMI you choose meets your application’s requirement for environmental standards and agency approvals. Most panel meters meet NEMA 4X (IP65) requirements for wash-down applications and have UL, CE or similar agency approvals. You should be aware that, even in the industrial automation market, there are some HMI graphical displays that do not meet these standards, so you should review the manufacturer’s specifications carefully. You also need to make sure the HMI graphical panel supports the communication protocol used by the PLC controller being used. Most HMI panels support multiple serial protocols and can be configured easily with the programming software.
Choose how the operator will interface with the application. Many HMI panels allow the operator to press a built-in function key based on what is being displayed on the screen. This can be confusing to the operator if there are several objects on the screen at one time. You might consider an HMI panel that has a touchscreen overlay, allowing the operator to interface with the application by simply touching the object. Touchscreens tend to be more intuitive than function keys. Operators quickly see what needs to be done and instinctively touch the screen to initiate an action.
Since the HMI graphical panels require software configuration, make sure the supplier has a technical support group that provides help in dealing with the learning curve your programmers may have. Also, make sure the supplier stocks the product you choose and carries a solid warranty.
Greg Philbrook
HMI product manager
AutomationDirect
Digital Vs. Analog
It is important to consider what the return on your investment will be and what you require from the instrument. Humans experience the world analogically. Vision, for example, is an analog experience. So, when metering is required, do not eliminate the analog option, but consider the actual application.
We live in a digital society. Decisions often are made to install a digital solution without giving the analog solution consideration because we assume that the digital meter to be more advanced. While the analog readout is harder to read at a glance, it still holds a significant place in an instrument panel. For almost 50 years, generator builders, welder builders, switchgear manufacturers and automobile and aviation groups have argued the differences. In most instances, they side with analog displays, augmented by a digital readout of numerical information. The absolute accuracy of an instrument depends primarily on the transducer and circuitry that measures the physical quantity at interest and not on the display. Also, consider the purpose of the information supplied to the user. Sometimes, a display can be useful primarily as status indicators, simply to tell at a glance if the system is in proper range, or even approaching an undesirable condition. For this purpose, analog instruments are far better than digital.
Keep in mind that the purpose of an instrument is to let you build an image of the world from an abstract output. People are best when dealing with pictorial information. Numerical outputs have to be mentally translated into appropriate visual representation.
As an exercise, try describing a spiral staircase in numerical form or without using your hands. Wouldn’t a simple graphic display be easier?
Of course, some analog displays are superior to others. Style is often the enemy of good information transfer. The recommendation is that if the instruments work and the user knows how to use them, keep them. You could gain little except aggravation by switching from an analog to a digital readout. Better yet, find a vendor that can provide you with either solution.
Rich Westerfield
vice president, meter and instruments, North America
Yokogawa of America
Consider Panel Real Estate
This PLC with a 5.7-in. HMI shows trends of temperature, humidity and relative pressure in a clean room.
It depends upon the breadth of information you’d like displayed, but nowadays panel meters can do a lot more than just offer “meter readings”—and many can do so at a cost-effective price. For analog parameters such as machine speed and temperature, the data is critical to system operation but generally doesn’t require the bells and whistles of a graphics display. In these applications, a panel meter keeps workers informed so that they can make system adjustments when needed, yet the meters are simple enough to operate that existing maintenance staff can support the equipment.
Another advantage to using a panel meter is, of course, its smaller size. With easy-to-read, bright red LED characters, panel meters ensure your line workers can see all critical information at a glance, but they only consume a fraction of the space of graphic displays. This allows you to make efficient use of panel real estate and requires less depth for enclosures, resulting in significant space and cost savings.
Jeff Thornton
indication and control product manager
Red Lion Controls
PLC+Graphical
Yes, graphic operator panels can be used for much more than just showing speed or temperature. From trends and graphs, via alarm management to data entry, the operator panel is your two-way connection to the whole system.
You actually can save on up-front hardware, wiring and programming time by migrating to a PLC that comprises a graphic HMI panel, where the PLC+graphical display are a unified device. It is compact, efficient and saves a lot of cabinet space and wiring. Plus, you won’t have to handle PLC-HMI communication. Hardware cost for a PLC+HMI unit is usually lower than buying separate components.
Some manufacturers provide an integrated software package for programming both the PLC and HMI applications—big time saver.
In many cases, you will find you can program five analog meters—say, gauge, bar graph, LED graph and numerical value—linking directly from the PLC analog input to elements on the HMI panel in 5 to 15 minutes, considerably less than it takes to cut and wire a single panel to five local meters.
These days, PLC+HMI controllers can give you color touch panels, communication options such as Ethernet, as well as a feature that is fast-becoming indispensable to machine manufacturers: wireless communications with third-party devices such as cell phones. This combination can give your machines the competitive edge that you are looking for.
Emil Melamed
technical support manager
Unitronics
Graphics Display Conversion From Discrete Panel Meters
The conversion from discrete panel meters to a graphic display or HMI is simple, cost-effective and the right way to go in almost every circumstance. The PLC has the ability to receive analog and digital data from real-world devices and control output devices depending on certain values. PLC data also can be displayed in raw format or scaled to actual engineering units on a graphical display or HMI. Besides displaying the information that previously was on the panel meters, a user can add alarm information, push buttons, product selection or trend charts. Development cost is minimized because the software used to create and display these values on the HMI is now easy to use.
Programming to design and link HMI elements these days is not complex. If you have mastered the computer skills of drag-and-drop and copy-and-paste, you already have the skills to develop the graphics display yourself. Some HMI suppliers provide libraries of predeveloped graphical templates that the user drags and drops onto the display screen. Often, only the unit number and a few parameters need to be filled into prompted blanks to build the functional links. The software development costs also can be quite low. Depending on the supplier, a single software package provides the combination of HMI graphics development, PLC programming and system simulation. Cost of hardware, installation and maintenance are additional reasons to move away from multiple discrete display devices. From a reliability standpoint, the single connection between PLC and HMI eliminates sources of erratic data displays and reduces wiring labor time and costs. Troubleshooting is much simpler, too, with just one connection. If additional monitoring points are needed in the future, an HMI program can be quickly adapted and expanded without massive rework to existing control panels.
David Kaley
product marketing manager, HMIs/networks
Omron Electronics
Some Product Specs
Several of our digital panel displays or meters can be loop or line-powered. The line-powered displays have the ability to also loop power a two-wire instrument. Most of the displays have keys to configure the instrument, apart from a free software option that is available, too. Some of the displays can perform additional alarm functions like built-in relays, linearization, simple math. Most of the displays are Universal input, i.e., any type of RTD, thermocouple, mV, mA, frequency or pulse input can be hooked up to the displays.
Apart from the single input or channel display referred to above, we have two multichannel displays (3 or 6 channel, 4 up to 20 channel). Apart from having the functionality listed above, these multichannel displays come with options for Ethernet (embedded Web server), Profibus, Modbus, memory card (recording) capabilities. These can also be setup in different display modes such as digital display, instrument display, bar graph or chart. Unlike solid state graphics displays, none of these displays have any software development costs. The software that is used to configure the device is shipped free of charge with each unit and is user-friendly.
Ravi Jethra
recorders & displays product manager
Endress+Hauser
December’s Problem
Too often, the sensor signals and even the HMI of our metal-cutting machines go haywire, largely because of electrical noise interference from many old, large, nearby motors and drives that we really can't replace. One solution suggested is to start using fiberoptic cable, but that's not cheap. Alternatively, there also are dozens of power filters, uninterruptible power supplies and other power conditioning devices out there, ranging in price from less than $100 to more than $1,000. We could use some information about both alternatives to help sort out the best course of action.
We experience the world in analog. When you see something with your eyes, for example, that is an analog experience. Analog has its merits, but when you’re garnering data from a machine operation, the application will dictate whether to go analog or digital. We live in a digital society. Decisions often are made to install a digital solution without giving the analog solution consideration because we assume that the digital meter is more advanced. When obsolescence of components becomes an issue, it might be a perfect time to decide what sort of display is best for your application. You’ll find folks who share your position on this issue and maybe some who disagree at ControlDesign.com/obsolete.
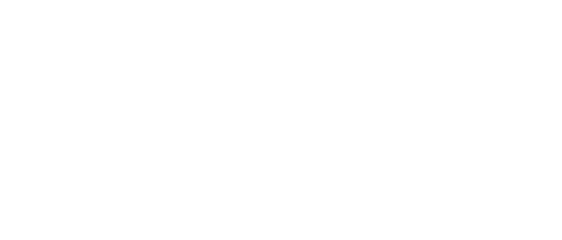
Leaders relevant to this article: