By Mike Bacidore, Managing Editor
Look to the future. That has been the mantra of Concep Machine (www.concepmachine.com) in Northbrook, Illinois, for the past three decades. "All of our machine solutions are custom, so we're looking for a means to make it easier to build the machine and lower the risk of a new technology," says Chris Lovendahl, sales manager. "It's only been in the past 10 years that the technology has caught up. There have been a lot of improvements in CAD technology. We went from basically replicating a drawing on a piece of paper in a 2D world to SolidWorks' 3D world, where you can see the interference of parts bolted together and you can see how the tooling works with the customer's product."
Concep tends to group technologies together, explains Lovendahl. "If you're doing an assembly process where you press two things together, we design that from the outset to be ready to do a whole variety of parts in the future," he says. "All types of processes that we use in assembly machines can be reused, so we've got to baseline that and be able to use it in the future. If we're designing a machine or a station or a technology for the first time, we're always thinking of the future. We might make a design a little bit larger or a little more open."
Concep employs mechanical and electrical engineers. "We have an overall employment of a few dozen employees that are involved directly with technical project activities," says Lovendahl. "Most of our employees have the ability to work in a number of technical disciplines at any one time. For example, our lead machine builders also are experienced tool and die journeyman. Our machinists also are experienced in machine assembly. This allows our staff to shift into different disciplines during the various phases of a machine project."
Concep believes using precision-cut cams to control tooling motions offers the highest repeatability and reliability. By driving all cams with a common drive, these machines offer high efficiency or low operational costs. Concep also favors cam-actuated machines because they provide lower mean time between failure (MTBF) than any other means of process automation.
One of its most recent creations is a medical device assembly and test machine that runs more than 200 assemblies per minute. "It is a successive generation of initial machines we've built before," explains Lovendahl. "It's based on our standard designs and modules for cam-actuated machinery. The fact that we're using cam actuation makes it a very robust machine and makes it very fast. We're marrying a mechanical transport system with all of the electrical devices on the machine. Certain pick-and-place operations, pressing operations and inspection operations really change from product to product. We can reuse those designs over and over again."
Concep prefers building mechanical, cam-operated machines because line-driven machines typically can run faster than their servo colleagues, says Lovendahl. "They require less programming and maintenance. In the medical-device business, validation is a major concern, and validation of programmed devices is more lengthy. The whole drive system is based on our standards. All of the pick-and-place systems and the transport systems are all basic building blocks."
The system works on a mechanical drive system that has an encoder control, which tells all of the electrical components when to activate, what to do and when to shut off, explains Lovendahl. "We're communicating with all the electrical devices on the machine through DeviceNet," he says. "Programming changes and programming controls are all done through Ethernet, all from the central CPU. We're doing an inspection of each product to make sure the subassembly is going correctly and then we have a final inspection of the completed product."
All of the data goes to the HMI, which tells the operator the speed of the machine and other information. "If there are any faults, it'll tell where the fault is happening, and then they can correct the fault from that screen," explains Lovendahl. "Because it's a mechanically operated machine, we don't have I/O controlling the actuation of the machine. It's mechanical, so it's just a verification of that process."
The majority of Concep's machines use PLC-based control systems, explains Lovendahl. "Embedded control systems are used when we are integrating equipment that needs unique processors in order to function correctly," he adds. "These might include PC-based test systems or data storage systems. All of our machines follow all common industrial standards for safety circuitry."
Concep uses a combination of hardwiring and digital networks, depending upon the needs of the devices being integrated into a machine cell. And thus far, wireless applications have been limited to point-of-use devices such as bar code scanners, says Lovendahl.
Concep also provides complete training on its facility floor during the development of a machine. "We also provide training during and after the machine installation at the customer site," explains Lovendahl. "Each customer will have slightly different training needs, and these are usually spelled out during the beginning of the project. Spare-parts requirements are defined during the engineering phase of the project, and they are ordered and shipped with most machines. The spare parts are then typically ordered as the machine runs in production. The use of Web-based services such as Webex or GoToMeeting helps to provide clear communication with the customer about the service needs of the machines as they mature in production. They also are invaluable for the discussion of tooling changes to the machine as the product design is changed during its production life."
The continued pressure on shortened lead times and leaner budgets has led Concep to use more off-the-shelf devices in its machine designs, explains Lovendahl, who sees three primary trends as most influential on the way his organization will design machines in the future. They include the standardization of communications being used for a wider array of integrated devices, the increased reliability of devices and the availability of devices. "Of current impact is the availability of controls devices that used to be stocked locally," he says. "Suppliers have reduced their inventories to very low levels." Over the long term, Lovendahl believes these trends will contribute to simpler, more robust machines that will be more reliable and easier to maintain in the future.
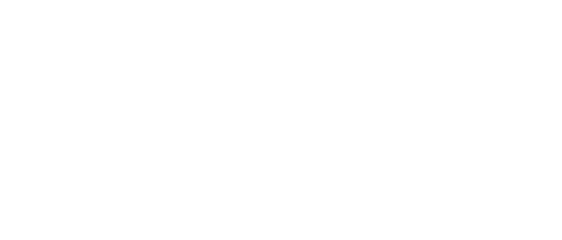
Leaders relevant to this article: