The capability (and complexity) of our packaging machine designs have evolved over time and now have multiple power supplies. We think we should upgrade to newer, higher-efficiency power supplies that we've heard about. We understand that overall machine power consumption will be reduced, but are there any drawbacks in terms of cost, heat generation, form factor, flexibility or other areas?
—From April '11 Control Design
ANSWERS
Selection Guidelines
The change comes with few downsides and many upsides besides the efficiency itself.
Efficiencies vary by load, so look for specifications of minimum efficiencies that will guarantee worst-case conditions. Beware of claims of "up to" certain efficiencies. Although not necessarily false, the claims might drive you to unrealistic expectations.
Heat generation is a byproduct of inefficient supplies, so as efficiencies rise, dissipated heat falls. Space savings and reduced cooling hardware are side benefits from the improved technologies. As less heat is generated, the size of power supplies can be reduced using components that can be smaller and mounted closer together. Mounting options increase because less attention is required to air flow and cooling.
Because of the advanced technologies, built-in diagnostic features for preventive maintenance can be added that would otherwise not be possible or would be cost-prohibitive. Such features include switched alarms or onboard displays for voltage, current, run-time, temperature or life-time monitors. In addition, newer models come with compliance to newer versions of standards—UL, CSA, CE or SEMI—and green standards like RoHS.
Finally, consider block-type power supplies that provide redundant bussed power or smart power supplies that provide multiple output branches with integrated overcurrent protection. These types may be more suitable for applications with multiple power supply requirements.
Jeff Jurs, program manager,
Omron Industrial Automation, www.omron.com
Switch Your Mode
Traditionally, machine builders used big linear power supplies to make up for surges and large current draws from the loads on the machines. But as the technology changed, many of those current-hungry components have become more efficient and allow the machine manufacturer to switch out the bigger, bulkier power supply for a switch-mode power supply to take advantage of the features it brings to the application.
New switch-mode power supplies also provide the flexibility to run on ac/dc input voltages. Many offer a status relay output as an alarm that the builder can use to activate a beacon or audio alarm in case there are issues in the panel.
Andrew Barco, product specialist,
Weidmüller, www.weidmuller.com
Longer Life
Higher-efficiency power supplies might cost a bit more upfront, but the investment can help prolong the overall life of your product, reduce panel-space requirements and improve machine uptime.
Heat generation inside the power supply shortens the life of panel components such as capacitors, eventually limiting the overall life of the power supply. The more heat generated, the faster the capacitors dry out. A temperature increase of just 10 °C, for example, can cut the life of a capacitor in half. Higher-efficiency power supplies consume less energy and therefore generate less heat, helping extend the life of your product.
Derrick Hinds, product manager,
Rockwell Automation,
www.rockwellautomation.com
Benefits Outweigh Cost
With the evolution of machine design and controls technology, the need for more dc power becomes ever more prevalent. Older linear-style power supplies typically had an efficiency rating of 40-60%. Today's primary switch-mode power supply (PSMPS) designs are more than 90% efficient.
With efficiency comes reliability. From input voltage sway tolerance to output regulation and monitoring, the newer power supplies are designed for long service lives. It is not uncommon to see mean time between failure (MTBF) ratings of more than 600,000 hours.
Updated power supply designs also allow flexibility in the cabinet. Many PSMPS available now have the ability to work across the globe on different voltage networks and configurations. Power supplies have dual voltage settings, auto ranging inputs or even ultra wide operating ranges. Also, these power supplies offer an adjustable output voltage, which allows one design to be used in multiple applications. Some 12 Vdc output power supplies can be adjusted as low as 5 Vdc for logic applications or as high as 18 Vdc.
The one typical drawback with today's power supply designs is cost; there can be a substantial cost differential between a linear power supply and a PSMPS. However, with the cost of operation over several years, the stout design and the intelligence built in, the benefits offered easily outweigh the initial purchase price of some power supplies.
Ken Allwine, product marketing,
Phoenix Contact, www.phoenixcon.com
No Downsides
A 240 W load shouldn't need an additional 60-80 W to operate. That 240 W is all that is required and everything else that it takes to operate the load is a waste.
Comparing a highly efficient 240 W supply to a lower-efficiency 240 W supply by using a watt meter shows that the highly efficient supply has a heat loss of only 10 W compared with 42 W on the other. Using one of the many online enclosure sizing software tools, a comparison can be made of the required enclosure sizes. Keeping this simple, only the power supply will be installed inside the enclosure. The outside temperature is 40 °C, and the maximum allowable temperature inside is 60 °C. The result shows that the highly efficient supply could fit in a 6x3x6 in. enclosure. If the lower-efficiency supply were installed in the same enclosure, the inside temperature would be 124 °C, greatly exceeding the manufacturer's maximum operating temperature. To allow a temperature not greater than 60 °C, the enclosure size for the lower-efficiency supply would have to be 10x10x10 in. or 826% larger by volume. This adds substantial cost for sheet metal and takes away valuable real estate on the wall or floor.
Efficiency must be figured in when calculating for operating current, or else everyone's 240 W supplies would measure the same. Power factor also contributes. The formula for calculating input current for a power supply:
Currentin = Powerout / (Voltagein x Efficiency x PF)
A 93% efficient 240 W supply with a power factor of 0.98 operating at 120 Vac has an operating current of 2.19 A. Compare this to a 75% efficient 240 W supply with a power factor of 0.6 and an operating current of 4.44 A. A piece of equipment that uses half the energy costs would make factory managers very happy.
Wasted heat not only degrades the power supply, but also the surrounding components. In some cases, forced-air cooling may be required for poorly efficient supplies. This requirement also adds cost for the fans, wiring and labor and for cost comparisons must be added to the base cost of the supply. It may also inject environmental conditions into the picture, especially if the enclosure has to be vented.
Ed Merkle, engineering manager,
Puls Power Supplies, www.pulspower.us
ROI Savings
The demand for higher-efficiency power supplies is driven by a number of factors, including existing and emerging global "green" initiatives and regulations that are intended to reduce wasted energy in the form of the heat that results from the deployment of low-efficiency power supplies. Also, there are measurable cost savings in the electrical power needed to operate systems with higher-efficiency power supplies. Likewise, state and utility companies encourage the use of higher-efficiency power supplies because the cost and time to build new power plants is high, especially during these recessionary times.
By employing digital control techniques, advanced circuit topologies and state-of-the-art components, we have been able to provide higher-efficiency power products in substantially smaller packages with expanded features, such as digital interfaces for remotely located control stations. Since we can achieve cost and space savings by substituting digital microcontrollers for bulkier analog/discrete circuits, we have been able to provide these higher-efficiency power supplies at prices comparable to lower-efficiency products. However, not everything is free and some added features, if required, such as external digital management/control interfaces, do have added costs associated with them.
One customer reported that by switching to power supplies that draw less current, they saved more than $100,000 in wiring by using a smaller gauge, particularly with the rising costs in copper.
David Norton, vice president,
TDK-Lambda Americas,
www.us.tdk-lambda.com/lp
Power Boost
In addition to smaller form, less heat generation and lower cost, some switch-mode power supplies also offer a power reserve (boost function) for absorbing the transient current peaks required by some applications. This enables the units to provide 50% increased current above their current rating for short intervals, which can be a tremendous cost saver in that you don't have to buy a higher-rated power supply to accommodate an application with a high inrush current.
Linda Sadek, product specialist,
Schneider Electric,
www.schneider-electric.com
Value the Flexibility
Comprehensive power supply product lines are anchored by capable, single-phase units offering wide input ranges (e.g., 85–264 Vac). There seems to be a power supply at virtually every major price point—as capabilities grow, so does price.
While important, costs shouldn't be your primary driver. Imagine your machines with LCD-equipped power supplies compared to competitive machines without. Customers will see the value in the LCD's continuous display of current/voltage output, line monitoring and streamlined diagnostics. Further, LCDs eliminate extra-cost equipment such as operational hour counters or phase monitors, providing savings both upfront and down the line.
Flexibility will be the most noticeable benefit. While basic machinery may only require single-phase power supplies, others would best benefit from the protection of a high-feature unit such as an uninterruptible power supply (UPS). In these applications, you're powering and protecting both machine and connected periphery. For instance, a UPS backs up power to PLCs during extended power outages, preventing loss of production data or protocols. Newer designs also provide watchdog functionality via active signal outputs for additional application support.
Enhanced performance accompanies greater flexibility. Modern power supplies can bring you additional functions to enhance large machine performance. TopBoost provides 60 A of additional 50 ms reserve for tripping miniature circuit breakers. PowerBoost offers up to 200% of rated current for up to four seconds to assist power-up of heavy loads (e.g., motors). These features are also accompanied by programmable overload behavior, which tailors power supplies to each application.
Michelle Goeman,
product manager,
Wago, www.wago.us
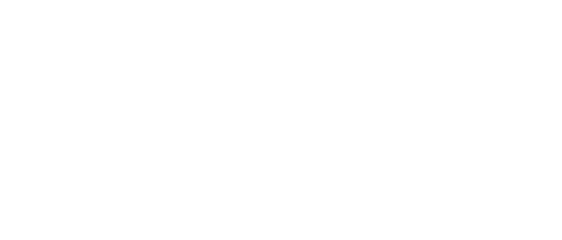
Leaders relevant to this article: