Our "Leap of Faith?" August 2004 cover story on automation trends discussed globalization at length. Its words still ring true: "As the world globalizes, machine builders are selling more to customers outside of North America. These customers often demand compliance with their own regional standards, and industrial OEMs must comply."
In "Confluence of Influences," August 2008, we noted, "Geographically speaking, the level of machine control intelligence is driven by varying demand for customization in different markets. Generally, North America is highly innovative and entrepreneurial; Europe is R&D-intensive and more likely to use a consortium approach to manufacturing complex products; and Asia remains more volume-oriented and price-driven."
Factors Out of Their Control
At the time, we saw that strategies existed for machine builders to overcome barriers to exporting that were otherwise out of their control. A couple of the major barriers then, and now, are currency valuation and third-party quality standards.
We learned from that 2004 article that, increasingly, the valuation of international currencies impacted a global business environment in which many other barriers have been lowered by factors such as technology.
"We want to have the flexibility to adjust our businesses to stay competitive, and if we have to move from one site to another to accomplish that, we have the flexibility to do that," said Richard Curless, CTO in the MAG Americas division of MAG Industrial Automation Systems, Sterling Heights, Mich. "When a customer looks at a MAG product, it wasn't necessarily built at one site; it means it could be built at multiple sites and built to standards."
For U.S. manufacturers, a potential downside definitely exists in offshoring production because of communications and logistics issues, Curless argued. As a result, he said, many MAG customers had begun producing domestically again.
Mike Harrington, director of R&D for Alliance Machine Systems International, Spokane, Wash., said price is the dominant competitive factor for his company's foreign operations in the paperboard packaging industry. "Our European operation faces intense competition from OEMs in Europe as well as Southeast Asia," he said. "The primary competitive force is price. In some cases, we can obtain slightly higher prices because of location, service and machine quality. However, the quality aspects are becoming harder to distinguish between competitors."
China Not the Answer
In June 2009, we noted growing evidence that sourcing and manufacturing in China could be risky business. AMR Research (now part of Gartner) analyzed the global supply chain. "Concerns with China's product quality and safety record continue to rise from quarter to quarter," reported Noha Tohamy, AMR's vice president of research and author of the report. "This will ultimately limit China's play in high-value, labor-intensive manufacturing outsourcing."
China earned most-risky honors in 12 of the 15 risk categories identified in the report. Respondents cited China the most about intellectual property infringement (59% of all respondents), product quality failure (55%) and regulatory compliance (34%). Some 49% of these U.S. companies sourced from and manufactured in the U.S., and 14% sourced from and manufactured in China. In addition, companies continued to look near-shore for sourcing and manufacturing, with three times as many respondents planning to increase that activity.
Maybe so, but our InDiscrete news section in December 2009 included a report from IMS Research that China would become the world's leading producer of industrial machinery in 2011.
Cross the Ts
In our August 2009 cover story, "Welcome to the World," we explored a "check list" that machine builders should be mindful of as they embark on competing in the global marketplace. In addition to understanding the critically important variations in regional machine safety standards, which we'll explore in the next section, we heard that minimum local language understanding and more-powerful computing were factors in providing easier-than-ever programming, configuration, networking and communication functions to standardize operational needs in many markets.
Gloucester Engineering in Gloucester, Mass., told us its Symphonix DCS extrusion control offers several language options, but it also has in-line text editing for customized translations, so users can input words and phrases that best meet local preferences. "For instance, the word 'head' often is used for the end of a barrel," said Paul Brancaleone, Gloucester's software and controls manager. "We call it 'end of barrel,' but now a company that wants to use 'head' can do so, which could be the best word for its application and the most clearly understood by its operators. Likewise, where we use 'pressure,' another user's local word might be the translation for 'push.' We also tried to make Symphonix more graphically intuitive, so it wouldn't need as much text and translating."
Where and What
In an August 2010 cover story, "Make a Splash," we reported on the experiences of global market machine builders as they decided "where they'd do what." For the most part, that boiled down to total control or strategic partnering.
Peter Brahan, automation team leader at Hypertherm in Hanover, N.H., told us that shipping is a problem for some of its customers, but not for his company. Hypertherm builds plasma cutting machines, which it sells to various manufacturing companies and to other machine builders.
Hypertherm has only one manufacturing plant, located in the U.S., but its equipment goes all over the world. "Manufacturing in one location makes it easier to ensure that customers are getting a product built to the same standards no matter where they are in the world," Brahan said. "In many cases, the engineering staff is located with the production staff, so customization and problem resolution can happen very quickly."
On the other hand, he noted, "Our customers make very heavy equipment. It's very costly to ship the product around the world."
Once built, Yaskawa offices around the world integrate the robots into a solution for customers locally.
International Wheel & Tire (IWT) manufactures tire balancers for the automotive OEM and tire industries at its sole plant in Oak Park, Mich. Kevin Kerwin, IWT vice president and CEO, said you must choose between setting up your own office and people or partnering with a local automation supplier. "While the partner option is initially the cheaper route, it's often not the ideal solution because you could be creating your own competition," he noted. "Ideally, you'd set up your own office in each region with the right people and local suppliers, but that can be very expensive."
Although you might or might not choose to partner up in various global regions, our August 2011 cover story, "Handle With Care," made the case that you certainly need some level of dependable local guidance.
For example, packaging machine builder Z Automation in Arlington Heights, Ill., long considered establishing a presence in Europe, but held back until 2010, when it opened a sales office in Frankfurt, Germany. "In the past, we were pushed by multinational end users that we supply equipment to in the U.S. to help them in other parts of the world," stated Randy Spahr, Z Automation's executive vice president. "We resisted opening an international office until the economic downturn in 2009 made the exchange rate between the dollar and the euro better for us. The European packaging market began to change at the end of 2008 when the overall business environment started to slide, and many big OEMs cut staff and business activity. The downturn and relatively weaker dollar made it hard for them to sell in the U.S., but made it easier for us to begin to sell there."
At the same time, Spahr found and now partners with two local machine builders in Germany. One makes pouch-forming machines and the other makes labelers. In exchange, he added, Z Automation plans to help them break into the North American market. "We'd been talking with them for years about moving into Europe, and they said to let us know when we were ready," Spahr explained. "Now they're helping us do service, support and production-line integration. They build primary packaging equipment and we do the secondary packaging, mainly cartoning and case packing."
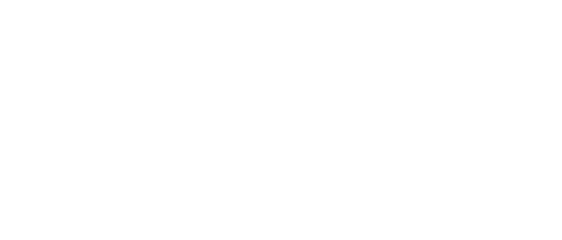
Leaders relevant to this article: