Arc flashes are the most common electrical incidences. Responsible for about 80% of the electrical-related injuries, arc flashes can cause severe personal injury and equipment damage when an arc fault superheats the air around it, expanding and creating a pressure wave within an electrical enclosure. Explosions can be as hot as 35,000 °F, and can send shrapnel and molten metal flying out from equipment (Figure 1).
The NFPA 70E standard dictates the precautions that manufacturers should take with their electrical equipment. Originally developed at the request of the U.S. Occupational Safety and Health Administration (OSHA), it provides guidelines on hazard/risk classifications, personal protective equipment (PPE), arc flash boundaries, and more.
Figure 1: Arc flash explosions can be as hot as 35,000 °F, and can send shrapnel and molten metal flying out from equipment.
Source: Hoffman
Though responsibility for arc flash safety has not traditionally fallen to the OEMs, as standards tighten, users are beginning to put some of the burden back on the machine builder. "Some customers are requiring us to isolate the high-voltage areas from the low voltage that we would use for PLCs and sensors on the machine," says Chris Lovendahl, sales manager for Concep Machine, which makes custom machines and factory automation systems in Northbrook, Ill. "We are physically separating them so that technicians can de-bug or troubleshoot the controls system without the requirements for the protective gear."
Filamatic, a liquid filling and packaging machine maker in Baltimore, also has been separating high-voltage and low-voltage components. "We put logic on one side, power on the other side of the panel," says Jack Chopper, chief electrical engineer. "That way if you need to troubleshoot the logic, you can open up the panel, no problem. You don't want to create a situation where somebody's trying to work on the logic right above a high-voltage area."
Filamatic takes other steps as well, including data taps and/or Lexan windows in panel doors so they don't have to be opened as often, installing interlocks and other hardware that make it harder for users to open panels without thinking, and coordinating fuse protection. A trend toward finger-safe devices also plays a part in improving safety, Chopper says. "It used to be lugs were wide open," he says, describing how easy it would be to create a fault by dropping a wrench across open copper bus bars. "Now the risk is lowered because of finger-safe devices."
It's a growing debate as to just how much responsibility machine builders should take with regard to arc flash safety, according to Wayne Tompkins, global marketing manager for Rockwell Automation. "What we're starting to see is that the end user is pushing back on them saying you need to design me a safe machine," he says. One thing that machine builders are beginning to do, he adds, is to install different levels of breakers. An end user could place a breaker in maintenance mode, for example, so that it would trip faster in the event of an arc flash, reducing the energy incident. "We see customers telling OEMs they have to use these types of equipment."
Lacking Proper Training
These sorts of solutions are increasingly necessary in part because of demands from users who are becoming more aware of arc flash hazards, Chopper says, but also because of just the opposite: more people servicing these units with less training than their predecessors.
Government agencies such as OSHA and NFPA have been trying to raise awareness of the electrical hazards, refining standards to improve safety. In 2007, OSHA changed how it defines a "qualified person" from one familiar with the construction and operation of the equipment and the hazards involved to one who has actually received the proper training and has demonstrated skills and knowledge in the construction and operation of the equipment, and the installations and the hazards involved.
Unfortunately, the "demonstrated skills" are often lacking, according to Patrick Ostrenga, compliance assistance specialist for OSHA. In fiscal 2010, OSHA cited 3,291 non-compliant items in 1,719 inspections, with fines totaling close to $5 million, he detailed in a Plant Services webcast about how to set up an arc flash mitigation program.
"Often I hear, 'Oh, he's been doing that for 24 years,'" Ostrenga said. "But what skills has he had and what training does he have? And oft-times we accept time in place of those real demonstrated skills. And oft-times that leads us to a failure because the arcs are unplanned events that we have a hard time planning for."
Unpredictable
It is precisely because arc flashes are so unpredictable that machine and panel builders are taking what steps they can to keep arc faults from occurring in the first place. "It's a two-tiered approach," says Garrett Potvin, global product manager for arc flash safety products at Pentair Technical Products' Hoffman. "You want to lessen the number of times an electrical worker has to open a cabinet, and also make it safer when they do have to open it."
For the first tier, Hoffman has enclosures that include Intersafe data interface ports, which allow access to the programming devices inside the enclosure without opening the enclosure door; and external data pockets, an alternative to placing reference manuals inside the cabinet.
In his webinar presentation, OSHA's Ostrenga emphasized the need for manufacturers de-energize equipment when working on an electrical enclosure. He urged that there's a difference between such a step being "infeasible" vs. it being "inconvenient." It is that desire to keep production up and running that machine builders try to address with some of the solutions.
Hoffman's second-tier solutions include a disconnect switch that, when a handle is pulled, cuts the power to most if not all of the components inside. Hoffman's Sequestr solution adds a smaller enclosure on the side of the main enclosure (Figure 2). "The disconnect switch resides on a smaller enclosure, which takes power completely out of the main enclosure," Potvin explains. "Instead of having to shut down a whole line or something, now they can isolate the power to the smaller enclosure."
The other side of that equation is arc-resistant equipment, which addresses what happens within an enclosure if an arc flash occurs when the doors are closed and latched. Although arc faults are more likely to occur because somebody has the cabinet open and is working inside it, there is need for closed-door precautions as well. "An arc flash is more likely if people are working with an open door and the system is energized, adding potential for human error," says Pablo Medina, product manager for the tiastar MCC at Siemens Industry. "Arc-resistant gear will not protect you from that because it will only work when the door is closed. But what people tend to forget is that I can have the door open and something happens and there's an arc flash there. If it's severe enough, the explosion can propagate to other units. So yeah, you're going to hurt the person who's opening the door, but if somebody else is around the gear, some other door could open and hard another person. It's very unpredictable."
Siemens' arc-resistant tiastar MCC is an example of a structure that is designed to withstand arc flashes when the doors are closed. In the event of an explosion, it directs the arc blast, including the heat, plasma and pressure, away from workers. "It's true that most of the arc flashes can happen when somebody opened the door," Medina adds. "But if something happened on the main bus, the chances of it being a very severe arc flash are much higher."
The range of solutions — whether mitigating or resisting arc flashes, working remotely or shutting down power — are geared not only toward keeping workers and equipment safe, but also improving productivity. "If implemented properly, you can achieve both," Hoffman's Potvin says. "There may be some upfront costs in getting your plant up to speed, but you have to address it anyway. You should be addressing it anyway."
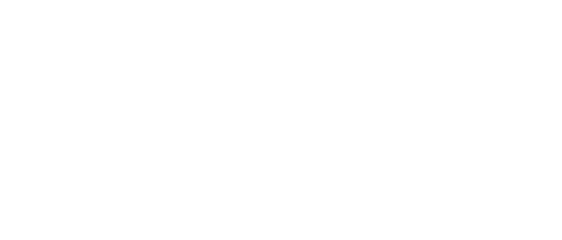
Leaders relevant to this article: