Wynright, headquartered in Elk Grove Village, Ill., was founded in 1972 as WEi. Its Automotion brand conveyor and sortation systems were launched in 1973. Like most conveyor suppliers, Wynright's traditional systems are driven by a belt that makes the rollers turn. The company also makes traditional live roller and gravity conveyors.
But the company really changed its direction beginning in early 2009, when Wynright's chairman Mike Scheck consolidated several different but related material handling companies under the new Wynright name. "That was when we really made our commitment to controls, software and support," says John Dillon, president of Wynright's Control Solutions division in Oak Lawn, Ill. That was also when Wynright formed the control group. "As opposed to it being fragmented or partially outsourced, we really tied it all together and focused on our investment in that area."
Out of that commitment grew a completely different kind of conveyor system in its AutoRoll+, a motor-driven roller (MDR) conveyor released about two years ago. Run-on-demand zones reduce energy consumption and overall noise, and extend the functional life of the conveyor. It also uses Ethernet connectivity, which offers simplified installation, greater flexibility with respect to conveyor controls, enhanced diagnostics, and remote visibility of the overall system.
AutoRoll+ conveyors operate in 5 ft zones that sleep when not in use.
Source: Wynright
Rather than having a 200 ft section driven by a large, noisy 480 V motor, AutoRoll+ divides the conveyor system into a series of 5 ft zones, each driven by a 24 V motor embedded in a roller. "There are a lot more motors, but they're more efficient," Dillon says, noting that traditional conveyor motors require much more torque to start and stop. In the new conveyor system, every zone goes to sleep until needed. "When that happens, you're saving power."
Ethernet also plays a large part in Wynright's technical advances over the past few years. Each zone in the AutoRoll+ includes an Ethernet card with its own IP address, enabling the zones to communicate with each other. The standard mode of the card can handle 95% of the applications, Dillon says. "The firmware is embedded in each card, and tells the cards how to communicate with each other," he explains. Each zone in a conveyor communicates with the other zones, sensing and reporting line-full conditions, jams, and other necessary data to ensure the product navigates the system safely and efficiently. "In specialized situations, such as with a robotic pick-and-place system, we can disable the firmware and control those specific cards strictly through the PLC."
The firmware — which is specified by Wynright — has improved over time so that acceleration and deceleration profiles enable higher speeds and increased flexibility. If a customer's product mix changes, Wynright can easily go into the IP and make adjustments. "We had a situation where, late in the installation process, our client asked if the system could handle some top-heavy cartons, well outside the parameters for which the system was designed. We were able to go in through the EtherNet/IP and fine-tune the acceleration/deceleration profile, making it possible to handle the cartons without tipping over," Dillon says. "In the past, you'd have to make adjustments to each and every card."
Wynright is completely sold on the advantages of EtherNet/IP, according to Dillon. "We've moved more and more to EtherNet/IP across all of our control systems, just in terms of the size of the pipe and the volume it can handle," he says. "It's an exciting time because even Rockwell's rolling out Ethernet on just about everything this year."
Each zone on the AutoRoll+ includes its own Ethernet card and IP address to communicate with other zones along the conveyor system.
Source: Wynright
Although obviously Wynright uses its share of Rockwell parts, the conveyor manufacturer does not let that limit its outlook on control architectures. "Some people prefer strictly PLC and others prefer strictly PC. We're big believers that there's a place for both," Dillon says. "Even as a Rockwell company partner — and I've told them this — the PLC is great for machine control. Where the PC has its advantages is at the supervisory level."
Wynright offers support options to its customers in which the supervisory component has been a key benefit. Support calls now can be done through a VPN connection, going through the IP addresses to look at a specific card's registries to see whether a roller's healthy, Dillon explains. "For example, if a roller that averages 1.2 A is running at 1.7 A, the tracking capabilities of the software help a maintenance person with diagnosis," he says. "In the event a zone won't run, we can get in there and say, ‘Replace the roller' or ‘Replace the card' vs. ‘Well, try this, try that.'"
The next step is to get that data out into real-time reporting to provide daily reports for maintenance, Dillon adds. "We can proactively say, 'Hey, these rollers have run 7,000 hours and are starting to show signs of increased amperage draw.' It's the difference between struggling through unforeseen downtime and planning for non-evasive scheduled maintenance."
Customers in the retail distribution space have reached a point where they are more than willing to provide VPN access to their systems, Dillon says. "If you go back five years ago, you could count on one hand places that would give us the VPN. And now, I can count on one hand the places that won't. It's really come full circle."
However, that's not so true in the manufacturing space, where Wynright's business has grown from about 5% of its total five years ago to about 20% today. "We've been successful in moving to the manufacturing side as we've entered into the robotics arena, with palletizing," Dillon says. "It is a different world, though. VPN's a little tougher to get, and don't say the word 'PC.'"
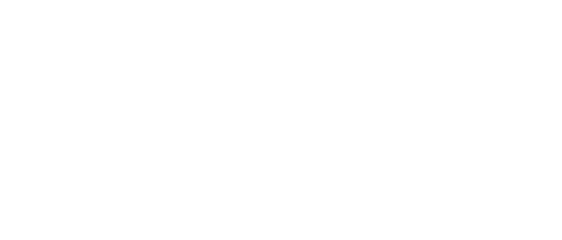
Leaders relevant to this article: