The machines manufacture primarily automotive, off-highway, agricultural and oil field components. For example, EMAG machines are involved in transmission components for agricultural vehicles, such as gears and gear shafts. "If you look at a dozer from the outside, you have a chain," notes Peter Loetzner, CEO of EMAG's U.S. subsidiary in Farmington Hills, Mich. "There are two large precision wheels that drive that chain. There are idlers on the bottom. Our machine can make all these components."
EMAG's equipment differs from typical machining centers, whose head stock is mounted, typically horizontally. A turret then turns to do the machining. "Our turret is mounted in a concrete base, so it's not moving," Loetzner explains. "We have a head stock that moves outside of that design. That gives us better precision and better tool life."
The machine builder takes pride in its ability to produce high-precision parts. In one example, Axle Alliance in Redford, Mich., needed to hold to a 25 µm tolerance for 390 mm diameter steel ring gears during hard turning, which is done prior to grinding the gear teeth. EMAG worked with Axle Alliance to develop a probing process that ultimately delivered a variation of less than 15 µm. Axle Alliance now uses six machines built at EMAG's headquarters in Germany, each dedicated to a part line.
A touch-off probe checks workpiece position before processing to ensure precise material removal.
Source: EMAG
Loetzner gives much of the credit for the machines' capabilities to long-time partner Siemens. EMAG has standardized on the Siemens Sinumerik 840D CNC platform, specifically the solution line and power line. Loetzner likes, in particular, that the CNC controller is an integral part of the HMI, and they are able to do almost everything through the CNC, including making it look like a PC for the operator. The common look and feel for the operators makes for easier onsite commissioning and cross-training, Loetzner adds.
In one recent case study, EMAG needed to provide grinding, turning and turn-grind machines to a major agricultural equipment builder, and the machine builder relied on the 840D CNC. "We needed to devise a control solution that would satisfy all the needs of the various machines we were supplying to this demanding customer, based on a common platform, to enable easier design, integration, startup, commissioning on-site and training for our customer's operations and maintenance personnel," Loetzner said at the time.
(It Breaks the Mold on Machining)
Similar control technologies are used on EMAG's newer-technology machines, including laser welding and electrochemical machining centers. These technologies have little impact on the control or automation schemes, Loetzner notes, because they still are essentially performing the same task, whether in a dry, lubed, gas-cooled or underwater environment. Only the sensors and encoders need to change to accurately feed the relevant data to the control. In fact, the controls are often much simpler because the axes of motion are fewer, though more multi-axis and workpiece manipulating machines are being developed.
Newer electrochemical machining techniques have had little effect on machine control, which relies on a standardized CNC solution.
Source: EMAG
More than 75% of the EMAG machines at this customer site are equipped with robotic devices. The lights-out capabilities this provides make remote monitoring that much more important. Remote monitoring can be done directly through the CNC in a one-on-one exchange with the customer, Loetzner notes, or even a three-way exchange involving Siemens as well.
While happy with the precision capabilities, EMAG's focus on future development is trying to decrease the downtime between producing components. "On the automation and the part handling, the challenge is you want the machine to run and make parts all the time, right? But once a part is done, you have to take it out and put the other in," Loetzner says. "Those non-productive times are the biggest enemies."
EMAG reduces those times partly by use of the Japanese chaku chaku principle. Meaning "loading loading," the idea is to bring various process steps as close together as possible to improve the speed between the processes. EMAG's vertical machining centers not only fill a much smaller footprint on the plant floor, they also improve chip flow. Also, all of EMAG's machines are self-loading, with a servo-controlled shuttle traveling through the machine, but not through the work envelope, Loetzner notes.
"While we have shown the industry we can master any part to highest precision, over the last five years we've been more and more focused on tightening non-productive time," Loetzner says. At IMTS in Chicago in September, EMAG will show a new machine generation that significantly reduces the non-value add times. "Our chip-to-chip time is between 6 and 7 seconds for typical automotive gear," Loetzner says. "Now it would be a second or less." EMAG's booth will be in the North Hall, booth 6846.
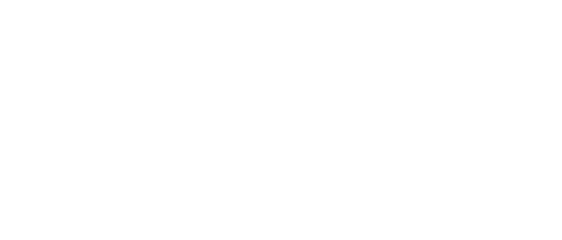
Leaders relevant to this article: