However, the use of complex shaped carbon fiber and other advanced composite materials require testing methods other than X-ray. Machine design companies such as Marietta Nondestructive Testing (MNDT), Marietta, Ga., needed to get creative in their approach to developing testing equipment.
Big Parts Means Big Challenges
Large parts made of carbon fiber are difficult to inspect with X-ray technology, which works well for other aerospace components. Even though we're working with large, complex parts, the limitations of X-ray is not a factor of part size. "X-ray is limited in its ability to determine the defect size and depth in composite parts from one shoot," says Curtis Cooper, director of engineering for MNDT. In order to be able to define a type of defect and the size of the defect, you would have to take multiple shoots of a part in different orientations.
"Some materials just lend themselves better to different inspection technologies," adds Garrett White, MNDT senior mechanical engineer. "In this case, composite parts can be inspected accurately using ultrasonic technology (UT)."
The most common automated ultrasound testing machines use immersion tanks filled with water as a medium through which sound waves travel. As parts became more complex, immersion tanks became impractical. Instead, technicians had to scan complex parts by hand — a slow and labor-intensive process that resulted in overlapping scans that could lead to inaccurate or inconsistent test results.
Challenges Require Innovation
MNDT's new ultrasonic inspection equipment is custom-designed for each client, based on the unique inspection specifications of their parts. The company's challenge was to design an NDT scanning system to accommodate larger, complex aerospace parts, reduce high costs of ownership and reduce maintenance needs, automate the system to increase speed and produce consistent results, and improve accuracy and minimize electrical interference.
Figure 1: Gantry-style AG2 Overhead Scanner is a multi-axis, automated-testing machine for large, sophisticated parts and intricate shapes without using immersion tanks. Precision automation fine tunes a highly rigid mechanical design that minimizes deflection.
To meet the challenges of scalability, reliability and speed, the engineers at MNDT designed the gantry style AG2 Overhead Scanner — a rigid, multi-axis, automated-testing machine capable of scanning large, sophisticated parts and intricate shapes without the use of immersion tanks (Figure 1). With a scanning envelope of up to 60x20x16 ft, the machine can be configured easily to test a wide range of parts for each customer, instead of being designed for one specific part. The scanner's ultrasonic scanning system uses two sets of squirter jets that face each other. During inspection, the jets stream water — the medium through which the sound wave travels — through the part.The precise servo motion control of the system became a critical factor in the design. For the machine to offer multiple axes of motion, component synchronization had to be tightly controlled so the testing would be accurate. "Each nozzle is roughly 3 in. from the face of the part," Cooper explains. "Since the two nozzles face each other, they have to be lined up (Figure 2). We were able to make streams of water, each of which are manipulated by five axes of servo motion, concentric to within 0.02 in. for a 0.25 ft water column."
Critical Components
Seeking precise control, accuracy and reliability, MNDT partnered with drive and control experts from Bosch Rexroth, and its automation distributor, Livingston & Haven.
"We evaluated the applicable technologies of a lot of companies," Cooper explains. "We looked at A-B, Parker, Siemens and [what was then] GE Fanuc, and went through a whole evaluation process." For MNDT, limiting EMI noise was a critical determining factor. "Noise can be pretty easily picked up by the sensors, and that can make ultrasonics susceptible to types of electronic noise that can distort the image," White adds.
Cooper says the Bosch controllers performed best for noise, and the high-quality support and customer service they received from Livingston & Haven also helped tilt the decision to Bosch.
For the most part, Cooper adds, MNDT makes the brand choices regarding the automation and control components it installs on its machines. "Sometimes a customer will specify a certain PLC or drive depending on their internal specs or because they have primarily standardized on a particular brand to make it easier on their maintenance people," he explains. "But for the most part with our larger machines, we can spec what we think works best."
Digital servo drives and controllers, profiled guide rails and pneumatic components allow the machine to follow intricate path planning for scanning complex, curved objects with tightly controlled motion tolerance. Livingston & Haven provided design and programming expertise for the new line of machines.
"The controllers are reliable and easy to program," Cooper says. "They can handle the large number of interpolated axes of the machines." The pneumatic components include a vacuum generator to remove air from the nozzle, which also improves the quality of the ultrasonic scans.
According to Ben Strong, automation specialist at Livingston & Haven, the linear guide rails used in the AG2 also contribute to the overall rigidity and accuracy of the machine. "If the machine is not stiff enough to handle the squirter system, it will begin to vibrate, which adversely affects the testing," Strong says. From a maintenance perspective, Strong thinks the linear guide rails are an ideal solution due to their longer lubrication interval, dual-rail datums and interchangeable runner blocks. In addition, the rails are plated with thin dense chrome to resist rust — a crucial consideration for a machine that incorporates water.
"Designing for frame stiffness is essential to the accuracy of the system," Cooper says. "We still need to incorporate linear encoders for position feedback, but mechanical stiffness is what allows us to keep the nozzles concentric to the needed tolerance. So a mechanically rigid design for minimal deflection in turn minimizes the amount of software compensation needed."
LabView commonly is used for data acquisition, instrument control and industrial automation on a variety of programs, including Microsoft Windows and Mac OSX. "We implemented a solution using TCP/IP sockets that provides real-time communication of position commands," Strong says. "As a result, MNDT can present an image of the machine in real time for remote viewing of the status of the system and for virtual programming of parts."
Speed and Reliability
"Because of the path planning and motion control, this machine is greatly improved over other inspection equipment," Cooper says. "The new squirter-based machine can perform scans accurately and quickly with almost complete part coverage, and we can scan parts at about 25 in. per second, which increases our speed and output."
Because of the number of types, sizes and designs of the parts being tested, there's really no such thing as an average scan time. "Scanning time can range from 20 minutes to 3–4 hours, sometimes even a day," Cooper adds. "It's just very dependent on size and complexity of the part."
The system water pressure and velocity also are monitored and controlled to remain within their required operating ranges. A part recipe is set up beforehand, sometimes based on trial and error, to adjust the scan settings to ensure a good test. Once that's done to the satisfaction of the operator, LabView saves the recipe program in the UT data handling system for future use as needed.
"This really is where the time savings come in," White says. "Once the part program is set up in the system, which can take some time, the rest of those parts move quickly."
Customer-Friendly
Because the programming, software and mechanics are configurable, the machine can easily accommodate a variety of parts from the same customer. Previously, customers had to order separate, custom-built systems to inspect each individual part. The AG2's functionality extends its usefulness and significantly reduces the cost of ownership for customers. The AG2 is scalable in all axis directions if a user requires a new machine that exceeds the current scan envelope.
Cooper says the end user does most of the parts programming, although MNDT, as part of its machine commissioning and factory acceptance requirements, will program a few of their parts, mostly for training purposes. MNDT typically provides a weeklong course for operator training.
"We can connect remotely to do machine diagnostics if the customer provides us with an Ethernet connection," Cooper says. "We rarely have 24/7 access; it's more of a turn it on, turn it off as needed arrangement."
Companies are becoming a little more willing to let these connections in through the firewall, but it varies considerably, depending on the degree of security and network understanding they employ.
In addition, MNDT has orders in house to build what Cooper thinks will be a more versatile version of AG2 that, instead of an overhead gantry, uses a floor-mounted rail system with synchronized towers (Figure 4).
"Overhead gantry-based scanning certainly will have its place," Cooper says. "But this new version might be a glimpse of the future for ultrasonic scanning of carbon composites."
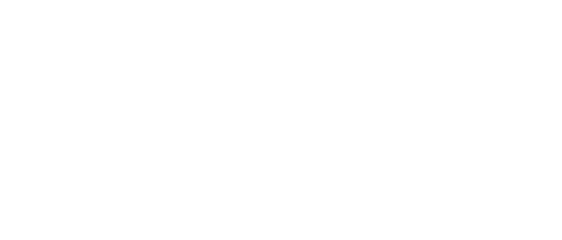
Leaders relevant to this article: