For some motion control challenges, a simple solution might be the best. When movement is between only two points and is uncomplicated, then mechanical motion control often can be the smart solution. A look at several examples illustrates why, for some machine builders, keeping it simple isn't stupid.
Most colorful T-shirts sold at concerts or seen on the streets passed through a screen printing textile press. Years ago, multi-color presses used pneumatics with an indexing cylinder to rotate a carousel, with the number of stops dependent on the number of colors being printed. In an hour, a press might crank out 650–1,000 T-shirts, but that wasn't good enough.
"The market started to require more stable performance and quicker changeover of job setup," says Darek Tkacz, chief mechanical engineer at M&R Printing of Glen Ellyn, Ill. The company is a global supplier of screen printing textile and graphic presses.
M&R Printing's initial solution to this demand involved a direct-drive mechanism with a high-end servo motor and gearbox. The latter had less than 3 arc-min (0.05°) of backlash — an accuracy needed because it had to position a carousel within a stationary fork to lock it. For a 40 in. diameter carousel, the location had to be accurate within less than 0.002 in. The precision of the positioning directly determined the quality of the print, since the colors are layered atop one another.
Though the direct-drive approach worked and offered higher throughput, it was significantly more expensive than the pneumatic method. So M&R Printing opted to try another route — one that exploited mechanical motion control.
"Instead of a direct drive, we installed a crank-type index design," Tkacz says. "The crank is connected through a link to a capture fork, so that rotary motion is converted into linear motion back and forth."
Figure 1: M&R Printing needs only a simple motion that bounces between fixed locations, so uses a crank index system instead of a direct drive to convert rotary motion into linear motion.
Source: M&R Printing
This works for the company's application, he adds, because the machines require only a stop and start point, a simple motion that always bounces between fixed locations. M&R Printing uses a design that has the crank with a 10° starting point and a 170° stopping point (Figure 1), although these two locations can be adjusted if needed. Experience during development revealed that the inertia of the largest and highest-output carousels was too great for this approach. Thus, those machines remained direct drive.
For smaller carousels, which can produce 900+ T-shirts per hour, the crank technique offers some significant advantages. For one, it allows M&R Printing to switch from a pneumatic index to a more cost-effective electric system with servo motor, Tkacz says, explaining that the servo motor made it easier to set up different parameters for different conditions.
"Most important for us was that we have been able to pre-program the speed of the machine for the different sizes of the printing pallets," he says. "Customers very often are changing pallet sizes a few times a day. With the pre-programmed pallet size speed of the machine, changeover is a very easy and fast process."
Another benefit is that the crank design boosts the throughput of some presses by about 50%, with little increase in price over the older technology. That is possible because the crank arm method is more forgiving in what it demands from a gearbox, Tkacz says.
"Using this motion will allow us to go with a gearbox that's not as accurate and not as expensive," he explains. "We've been able to choose a gearbox that can have 10 arc-min backlash and we can still achieve our linear accuracy for the indexing."
The success of the approach can be seen in the fact that M&R Printing has converted its product line almost completely to a crank-based design and away from pneumatic indexing, he adds. In implementing its design, the company specified gearboxes from Lenze Americas.
The biggest trend Lenze has seen is a push for increased energy efficiency, says Steve Greene, central regional sales manager. That has prompted Lenze Americas to move from a worm gear design to a helical gear. Doing so ups gear efficiency from 60% to 98%, and brings other benefits. "You can run the helical gear faster and it's more accurate," Greene says.
Flush Away Problems
Tekno, Cave City, Ky., produces conveyors and material handling solutions for the automotive and other industries. Cost is one reason the company sometimes turns to mechanical motion control, says Larry Mustread, chief operating officer.
Not only is a mechanical solution cheaper initially, it also can cost less to operate because of lower support costs and quicker time-to-repair. That's a consequence of the simplicity of the system and the ability to spot and diagnose problems quickly, Mustread says. "I know that it's going from point to point. If it starts losing that movement from point to point, it's easy to pick up that I'm getting wear somewhere."
Not all problems can be solved with mechanical motion control, though, Mustread notes. In particular, complicated motions are not good candidates. An articulated robot arm executing movement along several axes at once, he says, is not best solved by mechanical motion control. Neither is a motion path that requires anything beyond moving from point A to B.
A leading maker of bathroom fixtures and hardware came to Tekno with a problem. The company needed to automate a packaging process to reduce costs so that it could compete with overseas manufacturers. Tekno streamlined the entire process. A requirement in the overall automated sequence was to flip over a toilet seat so that a label could be placed on it.
Because the motion was a simple 180° flip, Tekno elected to do it using a set of pneumatic grippers and a pneumatic rotary actuator. The former grabbed the seat, the latter rotated it, and then the grippers released, dropping the seat on an indexing conveyor that delivered it to labeling and packaging equipment.
One of the challenges was the variation among toilet sets, says Lance Gatewood, engineering manager. Some were long and elliptical, and others were short and round. They also arrived at the flipping station skewed or off-centered. Thus, the machine had to square the seat and flip it.
"We designed a two-stage gripper, where one side had a shorter stroke than the other," Gatewood says. "The short side would engage the seat first and push it to square it up, then the longer side would do the final squaring and gripping in one motion."
Another issue was cycle time. The entire process had to take place in less than 5 seconds. Hitting that mark meant using the lightest possible materials, consistent with the need for durability. After some experimentation, the Tekno engineering team settled on aircraft-grade aluminum for the platform, with aluminum and high-density polyethylene plastic (HDPE) for the arms and grippers. To get a fast enough turnover, they used flow control to speed up the rotary actuator return stroke, with a hydraulic shock absorber to bring everything to a gentle stop.
The final machine performed to specification and achieved its objectives, according to Gatewood. So too did the manufacturer for whom Tekno built the machine.
Many of the motors and gears that Tekno uses are from Nord Gear. Like others, Mark Jones, Nord vice president of engineering and marketing, sees a growing trend toward energy savings, which is achieved by tighter integration of motors and gearboxes.
Though mechanical motion control can be used for packaging or manufacturing, that is not primarily where it shows up, as illustrated by its use in Nord Gear. "We manufacture here, and we use our products to move our components around," Jones says. "So the material handling side is certainly the largest segment."
Figure 2: A mechanical rail system allows a robot to transfer seats from the assembly line to the drop-off point.
Source: Tech-Con
The Mechanical Slide
Another illustration of mechanical motion control comes from Tech-Con Automation, a system integrator in Burlington, Ontario, that works with automotive and other manufacturers. Simpler solutions are often better solutions, notes Ron Heyden, vice president of sales and marketing. So, for simple movements that do not require multiple stops or a high degree of resolution, mechanical motion control might work best.
Consider the case of a large North American car seat manufacturer. The company had two assembly lines running in parallel, and the output of each needed to be placed on a shipping system pallet at the end of the line.
The offloading could not be handled by one robot. This was not a capacity problem, rather that the robot couldn't reach both assembly lines. One very expensive solution would have been to install robots for each line.
After studying the situation, the company's technical staff mounted the robot on a base and then put the assembly on linear bearings on a machined rail (Figure 2). With a simple air cylinder, they transported the robot between two spots.
Thanks to a hard stop and some built-in fine adjustment, Tech-Con was able to achieve accurate positioning so that the robot could serially service each of the two assembly lines. A shot pin held the robot in place while it performed its task, with sensors detecting the position of the robot and shot pin.
When all was said and done, this example of mechanical motion control paid off, Heyden concludes. "This simple system saved the requirement for a second robot," he says.
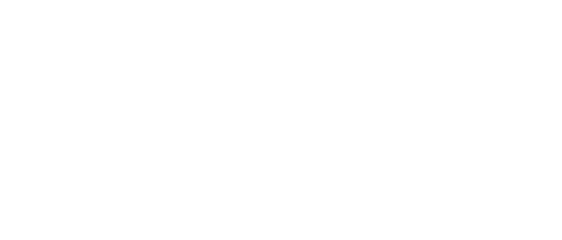
Leaders relevant to this article: