However, reports from the field indicate that cost remains an issue, as do power consumption and data rates. System integration and spectrum conflicts also can be challenging.
In the end, though, what matters is that wires literally can hold manufacturing down. Thus, there's a great benefit to using wireless sensors.
Look, Up in the Sky
"What the wireless buys you is reducing things like cables getting in the way or wrapping around engine hardware," says Ryan Huth, manager of the assembly special process engineering team at GE Aviation in Evendale, Ohio.
In 2012, GE Aviation and its partners expect to deliver more than 3,350 jet engines for a mix of commercial and military customers. The company also will refurbish a percentage of the 24,000 engines currently on wing that it had a hand in manufacturing. Each engine can contain as many as 25,000 parts, some of which must be secured using fasteners.
Huth's team develops processes and practices that make this assembly more efficient and cost-effective. Years ago, they investigated and GE implemented wireless sensor-equipped torque wrenches. These wrenches transmit such parameters as torque value, running torque, torque angle, torque rate, fastener location and fastener count. The measurements must be accurate and repeatable to fractions of a lb-in. or fractions of a degree.
Going wireless made the assembly process easier and safer for GE's workers. There are no wires to become entangled or to cause a tripping hazard. In their work, GE mechanics continuously walk around modules and the engine is flipped through several orientations during assembly (Figure 1).
GE's products are subject to U.S. Federal Aviation Administration (FAA) rules. Every part and assembly step must be tracked, and this history must be available. Wireless sensors transmit digital data, thereby enabling remote quality assurance checks. This data also enables retrieval of the torque parameters for a given fastener in a particular engine.
Wireless torque wrenches have come a long way, particularly when it comes to batteries, Huth says. Although expensive, the tools are ergonomic, lightweight, and easily handle data transmission needs.
The same can't be said for other GE applications. In particular, there's a need for significant improvement in wireless digital metrology tools. GE performs a series of measurements on sub and full assemblies, checking that they meet flatness, roundness or other dimensional specifications.
Engine tolerances are tight, so the metrology equipment must make accurate and repeatable measurements at a number of locations to 0.1 mil. GE would like to handle this chore wirelessly but can't for two reasons, Huth says.
One reason is that both contact and non-contact wireless metrology tools are too power-hungry for current battery technologies. Another is that wireless data rates are too limited and latency too high for meaningful measurements of what can be rapidly moving or rotating assemblies. "We collect real-time data at high sampling rates, and we're collecting a lot of information about surfaces," Huth says. "We need to collect it to a very fine resolution."
GE's experience in actually implementing wireless sensors on a plant floor has uncovered various integration challenges. These have included interference between industrial and office wireless networks, with mobile phones and other gear also in the mix. There also have been issues incorporating the collected data into planning and enterprise software.
For wireless sensor products on the shop floor, all of these matters have been resolved, Huth says. But help from wireless sensor suppliers in tackling integration problems going forward would be appreciated.
Tests have shown this to be robust in the face of electromagnetic interference, even if only one channel is used. However, some vendors running either a wireless networking standard or their own proprietary solution implement additional safeguards.
"There are things like channel hopping (Figure 2), where you're not just sitting in the same spot all the time," notes Garrett Schmidt, product manager in the wireless, I/O and network business unit for Phoenix Contact. "You're moving around the spectrum to try to randomize where you're transmitting and increase the likelihood you get data through."
Various techniques also could provide relief for batteries, says Nicholas Butler, platform marketing manager for wireless sensor network products at National Instruments. "For example, smart sensors could intelligently transmit data only when a threshold is crossed, thereby consuming less power."
Other technologies would allow sensors to live off the land, electrically speaking. For example, many machines vibrate at either 60 or 120 Hz, depending on the local alternating current. These minute oscillations can be transformed into useful power. "If you know what frequency you're at, you can tune your energy harvester to capture that," Butler says. "So the energy-harvesting applications can be structural-health monitoring and machine-health monitoring."
As for system integration, the industry might in some ways be a victim of its success, contends Todd Hanson, director of wireless solutions at Honeywell Sensing and Control. A lot is going on under the hood in terms of the coding and such, but much of this is hidden away, leading to an easy-to-use technology.
"We don't have a lot of system integrators that are involved right now because it‘s actually so easy to deploy and do the pairing process that, in a lot of cases, people are just doing it on their own and they don't necessarily need any integration," Hanson says.
Avoid Pressure Problems
While vendors and standards bodies roll out new solutions, existing products are being put to use. At the other end of the spectrum from GE in terms of size sits Waukesha Machine & Tool, a privately held firm with about 20 employees that manufactures special work tooling for machining applications.
Waukesha helps its customers reduce waste by allowing them to hold parts more securely and thereby position them more accurately. More precise machining can then be done, minimizing scrap.
A recent trend is use of large fabricators, with six or seven fixtures shuttling in and out throughout the manufacturing process.
The problem is that the hydraulic clamping systems holding the parts in place can leak and lose pressure over time. Metal shavings and coolants eat away at seals, which makes the loss of clamping pressure and part position a rare but real possibility. If this happens, machines can be down for days and tens of thousands of dollars potentially lost.
"We needed a way to tell the machine, 'OK, we're losing pressure in this specific fixture,'" says designer Kyle Spuhler. "We need to put the machine into either a slight hold or an alarm state so that problem can be addressed."
A wired solution would have presented multiple problems. In machining applications, wires encounter sharp chips, coolants, blasts of air, and constant flexing. All of these eat away at protective insulation, increasing the possibility of a short. Also, wires can become entangled. Another possible solution involved a mechanical pressure check. However, this could be done only at specific locations, requiring fixture cycling in and out.
After evaluating alternatives, Waukesha turned to wireless pressure sensors from Electrochem. The sensors transmit information every three seconds, three minutes or as needed, Spuhler says.
The devices have their own custom-designed battery, he adds. These are high-rate, spiral-wound cells using proprietary enhanced bromine chloride technology that delivers superior restart, pulse capability and dependable performance over wide temperature ranges and discharge rates, according to Electrochem. The sensors use the ZigBee standard at higher power levels that extend range. Distances to 1,200 m are possible with a 100 mW output from the base station.
At a few hundred dollars each, wireless pressure sensors are much more expensive than a mechanical equivalent, which could cost less than $10. But in the long run, the process, the product and manufacturing security will all be improved and catastrophic failure caused by pressure loss eliminated. Benefits like these could apply in other situations, which points to the future for wireless sensors.
After working as a semiconductor process engineer, Hank Hogan hung up his cleanroom suit and now writes about process control and other technologies from Austin, Texas.
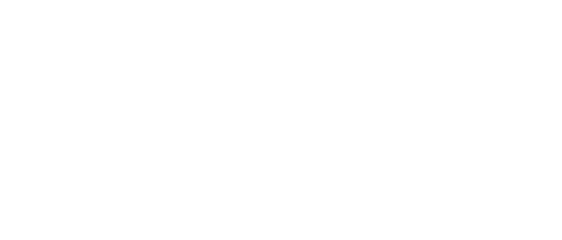
Leaders relevant to this article: