Empowered by high-performance and open PC-based control technologies, Houston-based ARC Specialties aims to deliver more affordable custom robot solutions to automated applications.
Although the company serves a diverse range of industries, some 90% of ARC Specialties' systems are deployed in the oil and gas industry. We count several globally active oil and gas OEMs headquartered in the Houston area as significant customers.
To create the most advanced solutions possible, we have a full-featured lab to test and demonstrate new ideas, and a skilled team of craftsmen to fabricate, machine and assemble the equipment. "The ARC Specialties team strives to manufacture best-in-class custom automation equipment with standard, off-the-shelf technologies that ensure long-term availability," says John Martin, senior project manager, ARC Specialties.
Improving Manufacturing
For 29 years, ARC Specialties has designed, developed and commissioned automated systems to increase manufacturing efficiency and improve product quality. Because of this history, the company was commissioned to create a fully automated robotic welding system for assembly of fluid-purification products.
The project challenges were unprecedented: one machine that would include large-product manipulation, robotic assembly, robotic welding, fixturing, servo motion control, and simplistic operation. Along with the technical challenges, there were manufacturing requirements that included reducing cycle time, improving product quality, and lowering unit cost. The system also needed to handle a wide range of other highly automated tasks throughout the manufacturing process.
All of this was integrated into one embedded PC-based control platform that allowed for single-point control. "The ARC-11RB automated system incorporates many of the same components we use on our standard products," Martin explains. "Using our past experiences, we were able to provide a solution to a very complicated task that is simple to use."
The project advanced through ARC's preferred path, starting with a proof of concept and weld procedure development on a robot inside ARC Specialties' R&D laboratory using the customer's actual product. Once we proved the concept, we went to work bringing the system to life using complete in-house design and manufacturing capabilities. ARC mechanical engineers designed the various material loading and gantry structures while programmers created procedures for the robotic arm. Simultaneously, ARC's adjacent manufacturing facility fabricated the system, machined customized tooling required for precise fit-up, and wired electrical panels. After completion, we invited the end user to our shop for demonstration of the system before shipment. What they witnessed was a system that exceeded their expectations.
PC Provides an Edge
Our company's control philosophy is centered — by design — on open systems. "Many of our competitors manufacture their own proprietary controls," says Gary Ewin, ARC Specialties' chief electrical designer. "That can be a fine solution for a few years, but some years later this can be a major problem, considering support and repairs needed to maintain the control system."
We're a builder that incorporates PLC, CNC, PC and robotics into our turnkey automation systems, ranging from process controls to multi-axis coordinated motion applications. "We have systems operating all around the world and have been providing automation solutions for more than 28 years," Martin says. "In the past, we would have used PCs to run the user-interface applications, while a PLC or CNC ran the machine control. Now, with a multicore PC, we run all of these applications on one piece of hardware that sits inside an environmentally controlled enclosure, and have an inexpensive monitor exposed to shop floor conditions."
ARC customers don't have any real issues with relying on PC-based controls. "A lot of times the customer doesn't even know it's a PC handling the motion control," Martin states. "We've used industrial PCs for 10 years as the HMIs for our CNC systems. Our customers have become familiar with the look of this control, the visualizations look nice, and operators are more accepting of the system. And an 'Internet-looking' HMI looks like it was created this decade. Most of the canned HMI programs provide a fast means of creating a user interface, but look like graphics from the original Nintendo video games."
The only issue Martin has seen with PC control is boot time. "Industrial PLCs boot immediately, while a PC takes at least a minute," he observes. "But the cost, programmability and power of the PC totally outweigh the minute of lost production once a month."
The ARC-11RB robotic welding system is equipped with a Beckhoff CX1010 Embedded PC with Windows XP Embedded operating system (OS). Beckhoff's TwinCAT NC PTP software runs on the CX1010 and controls the entire machine and robot, positioning the six EtherCAT-networked servo axes, controlling the welding process and synchronization of the robot programs. The operator interface visualizations also run on the CX1010.
"We write all of our own software for operator interface visualizations in Microsoft Visual Studio and C#," Martin says. "This helps us give operators the familiarity and comfort of a Windows PC, but with the specialization needed for custom equipment." The system's HMI elements communicate with the rest of the system using TwinCAT ADS.
We put a lot of effort into the machine's user interface. We understand the importance of having information displayed in a logical and easily understood format. Many integrators use dedicated HMI platforms, but we have found that the limitations placed on canned development environments do not allow us to customize the user interface to the application. The application might require a remote process monitoring feature or camera integration, and PC control allows us to develop custom operator interface applications with these features as well as control machine functionality.
The embedded PC controls a Fanuc ArcMate M710iC/50 robot and a Lincoln Power Wave R350 welding power supply via DeviceNet. This connectivity is established using a CX1500-M520 DeviceNet master fieldbus connection module on the embedded PC, which simultaneously features a direct connection to EtherCAT I/O terminals. ARC Specialties also uses a number of analog EtherCAT I/O terminals for controlling welding power supplies from a variety of manufacturers that do not use the DeviceNet interface or where fast response times are needed.
"With the high performance of EtherCAT, we can monitor essentially any drive parameters we want on the ARC-11RB," Martin explains. "This decreased wiring and helped us more efficiently write our code to handle custom applications. This is very important for ARC Specialties, as the majority of our business involves one-of-a-kind, application-specific projects."
The multitasking embedded PC system controls this entire welding application with a single controller. In addition to the overhead gantry, robot functions and HMI, the CX1010 also controls an induction heater, starting and stopping of the parts conveyor, all pneumatic processes, and monitoring tasks by connecting to various detection sensors.
Technology Seals the Deal
Despite the complexity of the application, electrical design for the new ARC-11RB welding robot with embedded PC controls took only four weeks, and build and assembly time took just three weeks. ARC Specialties achieved a 30% increase in production throughput for the end customer because of the automated fixturing. Before this, workers laboriously fit fluid-purification product components together by hand (Figure 3).
ARC Specialties also experienced considerable benefits from Windows Embedded functionality in the PC control architecture. "Our customers can connect these controls easily and securely to their local area network for remote access and using services such as WebEx, for example," Martin explains. "This remote connectivity helps us support machines anywhere in the world to troubleshoot and modify the software right here from our headquarters in Houston. That saves tens of thousands of dollars in travel expenses. With standard PLC hardware, this would be much more difficult to accomplish."
Another benefit of PC control is that the program development environment changes from the manufacturer's dedicated application to a Microsoft Visual Studio add-on. "The Visual Studio environment tools allow more streamlined integration of visualizations already written in the environment," Martin says. "We can code both TwinCAT 3 and Delta Tau's Power PMAC in the Microsoft Visual Studio environment. One program environment is a huge time saver for me, and decreases the learning curve for new programmers already familiar with Visual Studio."
We looked into other vendors' PC control platforms. There were some very good products that would fit our needs. However, we were concerned about the lack of other vendors adopting the particular communication networks. We felt we might be locked in to one vendor for PC, servo drives, remote I/O, everything. If we have issues with their servo drives, then it's not just a quick changeover to another manufacturer; it's a complete control system changeover.
"The other thing we saw with Beckhoff was the foresight to integrate the programming environment into Microsoft Visual Studio with TwinCAT 3," Martin adds. "Since we use this programming environment extensively, it seemed like a good fit."
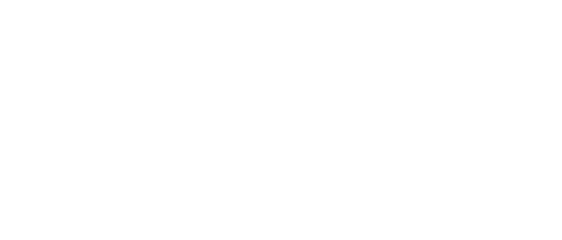
Leaders relevant to this article: