By Jim Montague, Executive Editor
It's a pain in the neck to reinvent the wheel. That's why it's useful to preserve human know-how, so one generation's gains can be built on by the next.
Such is the case with our knowledge of linear motion. Many of its traditional ballscrews, pulleys, rails and guides, and even newer electrical cylinders, have stayed basically the same, but they're steadily tweaked and accessorized for new and unexpected applications. Not surprisingly, linear motion is being assisted by servo motors and drives and more PC-based control, too.
Belts Shape Up Surfboards
To build less costly and more capable surfboard shaping and routing machines, Precision Shapes Northwest (www.psnwsurf.com) in Seattle added a Harmonic Linear Drive (HLD60-H3) belt-type linear actuator with a built-in smart motor to its machines. It combines six pulleys, and uses their resulting harmonic principle to accomplish internal gear reduction and braking without a gearhead (Figure 1). This belt-driven linear actuator allows the company's inventor and owner, Mike Ewaliko, and his Precision Shaper machine to follow CAD designs more accurately, and cut and shape the boards' polyurethane and expanded polystyrene (EPS) blanks more precisely—even over very long lengths.
The company has been building shaping machines since 2004, and is now on Version 8. HLD60-H3 also enables Precision Shaper V.8 to be 25% smaller and more durable. "Shaping a surfboard is a lot like creating airplane wings," Ewaliko says. "Each little concave or convex change in the hull can dramatically affect performance. There's a lot going on hydrodynamically, so shapers must get in tune with their designs and build their boards from the inside."
Serving Smaller Shops
Ewaliko reports that small surfboard shaping shops use his Precision Shaper machine to fight off economic demons on several fronts. "Big production houses use $65,000 to $100,000 shaping machines, but the little guys can't afford them," he explains. "So hand shapers have to get their designs produced by a production house, but they lose profit that way, too. More recently, Asian manufacturers have started mass producing surfboards and making them much cheaper, and this squishes the small shops even more. We build shaping machines that are compact, rugged and attainable for small shops—about $25,000 to $45,000—so they can still do 6–18 ft custom boards, but then record and repeat designs, or do a custom design for each one.
"Of course, there are still many curves on surfboards, so we've also honed in on holding blanks better—not too rigidly and not too loosely—for better registering and better transfer of the design. We're still matching the usual three to three and a half boards per hour that the big machines do. However, where we all used to reject three of every 10 boards for being a fraction of an inch off spec, our improved registration and accuracy means we're rejecting few to no boards now. This ability lets our users realize the true value of their shaping machines as extensions of their minds and their designs."
This happy ending is thanks in large part to the HLD60-H3 linear actuator, but the journey there wasn't easy. This is because previous Precision Shaper versions used stepper motors and servo motors, which used a lot more cabling, had more potential failure points, and were more costly. HLD60-H3 is built by the OEM Dynamics (www.oemdynamics.com) division of Animatics (www.animatics.com), which also supplies a SmartMotor with a 32-bit RISC controller. Precision Shaper also uses Animatics' JenCNC software and CANbus and RS-232 connectivity (Figure 2). These features cost more, but Ewaliko reports they cut job setup time to 30 seconds from 3–4 minutes, and enable more intuitive customization and remote troubleshooting.
Figure 2: Precision Shaper surfboard shaping machine from Precision Shapes Northwest uses a unique linear actuator to follow CAD designs more accurately, and cut and shape the boards' polyurethane and polystyrene blanks more precisely.
Precision Shapes Northwest
It took Animatics several years to develop the HLD60-H3's six pulleys and continuous, steel-reinforced belt, according to Chuck Searcy, senior applications engineer. "Most belt drives have two pulleys, but they need a planetary gearhead. The trick with our six pulleys is that their gears are slightly different sizes, and this design is able to accomplish that planetary gearhead capability and gear reduction by itself," he explains. "Our belt module is also more precise over very long lengths, and has unidirectional repeatability of less than 22 µm over 3.2 m. This allows Precision Shaper to cut precisely over much longer lengths than a ballscrew can handle. Ballscrews are precise at shorter lengths, but at longer lengths they start to vibrate and whip around like a jump rope."
Ewaliko adds that his firm developed its own Accu-Belt rack-and-pinion, linear belt system that's also driven by SmartMotor, and uses it in a cantilevered version of Precision Shaper, which also can handle very long projects. "The biggest trend in surfboards right now is the 12–18 ft standup paddleboards, so we need the ability to handle them," he says.
Happiness? Protected Bearings
Besides limits on length, another old restriction on using linear motion systems was the difficulty of using them in dirty and harsh environments because particles and fluids could get into their bearings and damage them. Improvements in sealing bearings, ballscrews and rails have allowed linear motors to serve in many settings where they couldn't go in the past.
For example, wind turbine towers up to 300 ft tall help generate cleaner electricity, but the mobile weld heads used to join the 9 ft long tower sections aren't nearly so tidy. Welding the outsides and especially the insides of these "cans" produces lots of particulate waste that could quickly damage a welding machine's linear actuators (Figure 3). To solve this problem, welding machine builder Amet (www.ametinc.com) in Rexburg, Idaho, recently adopted CKK compact linear actuator modules in standard 490 and 590 mm lengths and dual guide rails from the Linear Motion and Assembly Technology division at Bosch Rexroth (www.boschrexroth-us.com). The dual-rail system has a sealed rolling strip, which provides more protection from pitting due to particulates than traditional fabric or rubberized bellows. A belt seal encloses the bearings's bodies, and each bearing is full-contact sealed.
In general, the 8–15 ft wide cans are rotated, while the welding machine stays mostly stationary, and the weld head constantly moves small distances along and across the seam on at least two and sometimes three axes. Amet's machine performs circumferential, submerged arc welding across the can's diameter, and also makes longitudinal welds. The linear control actuator mounted at the end of a horizontal arm determines the motion of the weld head, which needs smooth and precise control to within 0.01 in. to avoid bad welds that would have to be redone. The CKK modules move 1.5 m/s with a dynamic load capacity of 25,000 N or about 5,600 pounds and an accuracy of 0.01 in.
Finally, because the CKK modules are preassembled with bearings aligned and prepackaged, they helped Amet shave about two weeks off its 12-week build schedule for the machine. "The CKK modules are precision-machined, so we don't need to do any extra work," Dees says.
Servos on the Line, Too
For instance, following two years of development, VMI Holland (www.vmi-group.com) in Epe, the Netherlands, is using 22 servo shafts and drives for all the movements on its new Maxx tire-building machine (TBM) to precisely position drums, cutting tools and conveyors. This allows VMI Holland to speed up its machine, and manufacture tires much more quickly.
Using materials fed from spools, for example, Maxx TBM builds up tires in a series of reinforced layers on its drums. The servo shafts and drives are synchronized by Rockwell Automation's (www.rockwellautomation.com) ControlLogix software, integrated motion modules and servo drives. In addition, a cap strip tension controller helps affix cap strips to the tire at a constant tension level, and its new controls have been able to increase its speed from 4 m/s to 8 m/s. Maxx also increases its throughout by applying pre-assembly and body plies in one move, as well as using robots to load bead apexes and unload finished tires.
"Naturally, it's important that the time it takes to construct each tire is as short as possible," says Jan Grahius, VMI Holland's R&D manager. "Not so long ago, TBMs required 50–60 seconds per tire. Our new Maxx TBM does it in just 38 seconds."
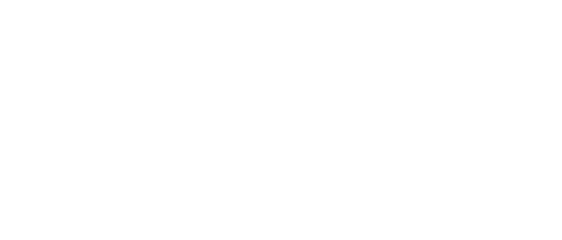
Leaders relevant to this article: