"We have an excellent reputation for supplying rugged, easy-to-clean specialty batching systems of 10–1,000 liters. Measurement of temperature, viscosity, heat transfer, and a few reaction rate tests have been un-automated samplings and readings for off-line analysis. We think we can expand into more-sophisticated markets, but we need to know more about entry-level, but accurate, automated sampling systems, and variable monitoring. Price is critical. How do we best evaluate cost vs. capability?"
—From June '12 Control Design
Answers
Added Value
Chances are most vendors in the market can come up with a solution for your application; however, you must consider what other value the vendor will bring to the table. Think about factors such as product scalability, ease of setup and use, sustainability, interoperability, reliability, and available diagnostics.
We've used basic PLCs and I/O for machine control for a long time. Our machines have to do more than before, and we need more connectivity options and a more COTS, standards-based approach to hardware and programming. Some customers are on the PAC bandwagon and think it's the next step for them and us. There are different opinions of what a PAC is. PLC vendors say they make PACs. So do PC-based control suppliers. Does it matter?
Send us your comments suggestions or solution for this problem.
Industrial automation controllers also allow for easy conversion from analog values to scaled engineering units. These values can then be logged for later use or shared to other systems for evaluation. If you choose to log the data, you can export the stored data from a controller via a USB port or compact flash. If you would like to share the data with another system for evaluation, consider a controller that can act as an OPC-UA server or something similar.
OPC-UA is a manufacturer-independent standard, developed and monitored by OPC Foundation, which allows you to exchange data from a controller to other devices. OPC-UA allows for up to 20,000 data modifications per second while using B&R Industrial Automation controllers. You can also connect to a WAN to share this data with devices such as PCs, smartphones or tablets by using HTTP messages.
Obsolescence concerns must also be addressed. How long will the vendor keep the products available to you? How long will the vendor service and support these products? It is important to ask the same questions of yourself. How long are your systems expected to last in the field? How long will you service and support them?
Investing in an interoperable automation and control system is vital for solving this batching application challenge. By choosing a vendor that supports all prominent fieldbus and field instrument signal types, you are setting yourself up for an easy path of migration for future improvements and a sustainable solution.
If a control system already resides within the facility where the batching system is needed and it supports today's fieldbus technology, you might be able update this application without having to add a new controller. For example, you might want to upgrade to a best-in-class IP67-rated industrial I/O solution. This allows you to obtain a more accurate reading from your sensors, while using your clients' existing controller(s) and control software to monitor, log and share the batching system information.
Tyler Spoolstra,
sales engineer—fieldbus I/O,
B&R Industrial Automation, www.br-automation.com
Keep It Simple
To keep costs low for both you and your customers, it's best to stick with commercial, off-the-shelf technologies for acquiring and delivering data. For example, use standard networking like Ethernet, so components can be easily obtained and maintained, and integration with other systems like PCs is simplified. Also, consider standard protocols and technologies like ASCII files, FTP or OPC, giving you a wide choice of systems to evaluate.
Perhaps the least expensive way to get data where it can be used is to write a routine in your PAC/PLC that automates the readings of your measurements and test, then writes a simple ASCII file to local storage, such as the PAC's FTP server. You could also automatically FTP this file to a PC or other FTP server periodically. Or, if your system has an SD card for data storage, store the data there for periodic removal. This method is very inexpensive for you, but carries some expense in time at the customer's end, as they have to manipulate the data so it is usable — for example, importing it into an Excel file and manually creating the reports.
At a slightly higher cost, you could use software that runs on a PC and acquires the measurements and tests using OPC, then sends it to a database like Microsoft Access or SQL Server. This method costs a bit more up front, but can be more convenient for your customer. Reporting tools are available to make reporting easy and automated.
Both methods are used frequently by our customers, and add significant value to the system overall.
Benson Hougland,
vice president of marketing and product development,
Opto 22, www.opto22.com
Cost vs. Capability
Size, safety and usability are excellent in helping machine builders scrutinize what they're getting in relation to their investment.
Size should be one of the first variables to consider when guiding an existing design into a new market. Will the existing cabinet/enclosure have to be modified for new equipment? The costs associated with changing an enclosure aren't always apparent. However, this doesn't necessarily mean simply specifying the most compact device or control unit you can find/afford.
Consider the capabilities bundled in that footprint. At some point, control expansion will have to be considered as part of machine expansion.
Increasingly sophisticated board-level components are enabling tech suppliers to incorporate specialty functions into the Ethernet controllers that automate samplings/readings. One example is data logging via SD card. Integration into existing designs is simplified, freeing machine builders to focus on how the controls can support a move upmarket. Process data is easy to retrieve and transferable via SD. So are programming changes.
Focus on the value of interoperability and scalability. With an SD-capable controller, for example, a machine builder can graft in specialty I/O to customize solutions for higher-end customers who understand the value of additional functionality and subsequent convenience.
Just as important is what you're using to interface and relay information from your measurement instruments to higher-level systems. For instance, DIN-rail-mount signal conditioners for transmitting measurement data to standard analog I/O.
A 6 mm DIN-rail signal conditioner and relay package for commonly used RTDs and thermocouples should readily fit most existing designs. These packages can even work with other signal types such as frequency and voltage as you move forward. This is a great starting point for machine builders taking existing designs upmarket.
As with I/O, look at the capability of any compact device. Safety is also important. What types of safety features are bundled into that package? Does the compact package offer via three-way isolation or input circuit protection against overcurrent? Upmarket customers will value these types of safety features.
Usability and programmability should complete the cost vs. capability evaluation. The user interface is a pretty critical part of the puzzle, especially when moving into a more sophisticated segment. How these devices are programmed will impact perceived value.
Michelle Goeman,
product manager — electronic interface and rail-mounted terminal blocks,
Charlie Norz,
product manager — I/O system,
Wago, www.wago.us
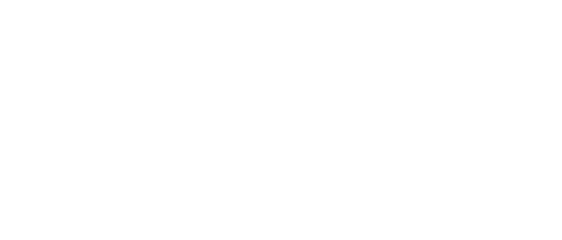
Leaders relevant to this article: