Tags can be challenging to read because the carriers go through ovens where they pick up soot, are sprayed with water and often dented in collisions. The laser scanners that read these tags had read rates averaging 86%. Operators had to stop the conveyor system about 20 times per shift for an average of 10 minutes to fix problems by cleaning the tags or clearing collisions.
SEE ALSO: 10 Reasons to Choose Image-Based ID Readers
Critical Material Handling
The carriers pick up composite filament, called balls of yarn, in the forming department, and move to a washing station where the filament is sprayed with water. Then the carrier goes through a drying oven. The next stop is the fabrication area where the filament is unloaded by operators for further processing. Finally, the carriers are directed back to the fabrication area to pick up more filament. During operation, the carriers reach each of these stations through spurs off a main conveyor loop. The barcode tags on the carriers are read at the entrance to each spur to determine whether the carrier should be directed to the spur or continue on the main line. If the read fails, then by default the carriers continue on the main line until an operator cleans the tags or manually directs them to the correct station.
If the scanner can't read the tag, then the carrier continues looping around the conveyor system, not entering any of the stations. "The conveyor tracks were largely filled with carriers with unreadable tags, generating wear and tear, and consuming power without adding any value," Marges states. "The conveyor system is powered by many chains that needed to be replaced about every two years at a cost of about $25,000 each. The high traffic volume also increased the frequency of events, such as carrier collisions that made it necessary to shut down and manually clear the conveyor system. To minimize these problems, operators were required to regularly clean off the tags so they could be read or manually direct the carriers to the correct station."
A Move to Image-Based Code Readers
Three years ago, the composites manufacturer began to transition from laser scanners to image-based barcode readers seeking higher reader rates, lower maintenance costs and process improvements. The manufacturer worked with Shelley Automation on this project.
"Image-based barcode readers can significantly improve read rates on damaged or degraded barcodes," Marges explains. "Instead of relying on a photocell to monitor the reflections of a single laser beam as it passes across the barcode to generate an electrical signal, image-based readers capture an image, and then use a series of algorithms to make it easier to read. A typical algorithm searches the entire image for the code and identifies the position and orientation of the code for easy reading. Other algorithms handle degradations in code quality, such as damage, reflections and quiet zone violations. A quiet zone is a zone around a code that separates the code from the background. Ideally you want this to be clear of any features that would reduce contrast and impede locating the code."
In contrast to laser scanners, which can demand frequent repair and replacement because they have moving parts to actuate the laser beam across the bar code, Marges says image-based readers are solid-state and don't wear out. As a result, image-based barcode readers provide two to three times the life of laser scanners because they don't rely on a motor-driven oscillating mirror that's subject to failure.
Imaged-based readers make it possible to save "no-read" images for later review. The ability to analyze "no-reads" through image-archiving provides the opportunity for continuous improvement. "Reviewing saved images of parts whose barcodes were not read will generally reveal if the problem resides within the reader setup or the process," Marges explains. "For example, was the tag missing? Was the tag dirty? Was the tag tilted? With visualization, the root issue can be addressed in a continuous process improvement program. Visualization also makes setup easier." Marges says an operator can use a monitor to view live images of what the reader is pointed at. The operator can make sure that the barcode is visible in the camera's field of view, see how crisp the image is, and know immediately how well the reader is performing.
{pb}
Generation Gaps
"The first generation of image-based ID readers offered improvements in read rates, but issues with lighting prevented them from reaching their full potential," says John Lewis, market development manager, Cognex. "The second generation offered additional improvements, but did not provide a continuous trigger needed for this application because of the speed at which carriers move along the track."
When Cognex introduced DataMan 300 ID readers, Marges believed he had everything that was needed to address this application.
"DataMan 300 ID readers use 1DMax code-reading algorithms with our own Hotbars technology to read even damaged linear bar codes at a high rate of speed," Lewis says. "The 1DMax algorithm uses omnidirectional texture analysis to identify areas in the image that could contain the barcode regardless of its orientation. Once neighborhoods are evaluated for the likelihood of containing a barcode, a clustering algorithm joins likely neighborhoods into more complete regions. These regions are analyzed further, and filtered to produce the final set to be subjected to decode attempts. The time budget for texture analysis is just a few nanoseconds per source image pixel on a relatively inexpensive digital signal processor (DSP). Meticulous hand coding of instructions and sophisticated control of memory makes it possible to execute the finder in a handful of processor clocks per source pixel."
Once regions that are likely to contain barcodes are identified, decode attempts can be made, Lewis adds. "Here, the fundamental image analysis operation is the extraction of a 1-D digital signal from the 2-D source image along a line of given orientation, often called a projection line," he explains. "In order to provide high geometric accuracy, good noise reduction, and acceptable resolution, contemporary state-of-the-art methods effectively rotate a portion of the image, so that the projection line becomes horizontal. Methods for rotating a digital image are well known and typically use some form of interpolation to estimate pixel values at points in between squares of the pixel grid."
Interpolation methods are based on a model of rotation in the continuous plane, but a discrete pixel grid can't represent rotation accurately at the small scales characteristic of fine features and the result is some blurring of the signal. "Hotbars technology has as its mathematical foundation a model of the behavior of the pixel grid itself, which allows blur to be reduced while maintaining accuracy and good noise reduction," Lewis says. "Hotbars' enormous signal-extraction speed comes from using a novel and extremely efficient algorithm that is well-matched to contemporary DSP architecture. The efficiency of the computation itself, and the way that memory is accessed, makes Hotbars' signal extraction much faster than even the simplest prior methods. Just as important, the ability to extract many more 1-D signals every millisecond can eliminate decoding shortcuts, thereby reducing failure modes and improving read rates."
Marges says no other brands were explored when making the decision to use Cognex. "The customer had tried every brand out there over the past 10 years," he states. "They had largely given up and settled on the brand that was doing the best it could [approx 85% read rates], and decided to wait for someone else to come forward one day with better technology. That was Cognex."
The DataMan 300 image-based barcode readers are configured with a continuous trigger, so they capture about 50 images per second. "The carriers move at 2 in./s, so the vision systems have approximately 30 chances to read each tag as it moves past," Marges says. "The cameras are configured with LED array lighting and a liquid lens that automatically focuses on the tags as the carriers move past. They're mounted on brackets that are used to aim the reader at the tags. The vision systems connect to the plant network through Ethernet, and communicate with the PLC using the PLC5 protocol."
Marges says no formal operator training is required to use the readers. "They have a self-teach function for setting up the inspection and the electrical wiring, and communications to the PLC is understood by any typical automation technician," he reports. "The only maintenance is wiping the lens cover clean of dirt or debris periodically. The rest of the camera is sealed."
One final advantage of image-based ID readers, Marges adds, is that they also can read two-dimensional codes like Data Matrix that manufacturers increasingly are adopting because they can hold a much larger volume of data to improve traceability. This customer doesn't need it now, but they like the fact that, if they have other applications in the plant requiring a code and they need to incorporate more data, then they have the option of using a 2D code and the same scanner can read it.
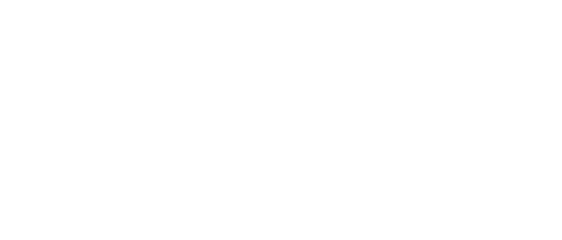
Leaders relevant to this article: