We never seriously considered line regen braking on our centrifuge systems (VFD-driven ac motors) because of initial cost. We dump the energy to choppers. We're being told that partly because of hybrid car advances and demands in industries with high energy consumption, it has become much more cost-effective. There's interest in both new installations and refit projects. What can anyone tell me about ROI these days to use regen drives?
—From December '12 Control Design
Document the ROI
Equipment suppliers in many industries wrestle with how to sell efficiency in the face of higher upfront costs — the reality of losing an order to a less expensive competitor makes the case against upgrading to energy-efficient equipment every time.
So what has happened to pricing for variable-frequency drives (VFDs), particularly regenerative drive units? The concept of putting the power back onto the line instead of dumping it into brake choppers is a slam dunk, right?
We build most of our machines by combining modules, so machine-mount controllers and I/O have been particularly effective because they allow us to test each module separately. But the cost and time required to wire the modules together at our customers’ sites is a concern, and we’re wondering if wireless is the right solution. Can anyone relate their experiences with machine-mount wireless controllers and I/O?
Send us your comments, suggestions or solutions for this problem.
As a result of this increased competition in the "regular" drives business, machine builders have undoubtedly seen an influx of attention from those ready to offer up their VFDs as a better mousetrap, and the price for these regular, ordinary drives has consequently gone down.
This means the go/no-go decision to switch to regenerative drives from an inverter plus chopper set is unlikely to look more attractive than it did in the past. The reality is absolute cost has gone down for all drive types. As long as the brake chopper is still less expensive than the converter section, the regenerative drive will fail to deliver a lower initial price tag.
So where does that leave the demand for regenerative drives in a society where going green seems to always better both business and the planet? What is the ROI on a regenerative drive anyhow? If the absolute cost has come down, we know ROI must be more attractive.
And it is. The challenge in trying to quantify the ROI in this situation is the number of variables. Machine variables, like the fluctuating inertia of the centrifuge, are just one piece of the challenge. To be frank, I would be wary of blanket statements regarding ROI from VFD manufacturers unless the application is a fan or pump. My advice for a machine builder that wants to market or position itself as a green player is to document energy consumption in identical end user installations — one machine with a regenerative solution, and the other not.
Demonstrate success with a single case study, and even the most reluctant customers warm up to paying a little more up front. The energy czars are out there and they are ready to listen!
Don Cameron,
senior product manager,
Mitsubishi Electric Automation
Where Does the Energy Go?
A high-inertia load traveling at high speed contains significant kinetic energy. When this load is decelerated, this energy needs a place to go. As you might suspect, this issue affects not only VFDs, but also brushed and brushless dc motors, servo systems and, to a lesser extent, stepper motor systems.
To understand the issue of regenerative energy (usually referred to simply as "regen"), it is important to understand what happens to that energy during a hard deceleration.
Modern pulse-width modulation (PWM) motor drives efficiently transfer energy from the power source into the motor to produce high-performance, high-efficiency motion.
PWM drives also do a great job returning energy from the motor and load. But where does that energy go? In the case of an ac-powered system, the power source is your local electric utility, and the power bus is quite stiff; it is not usually possible to return the energy to the power grid without highly specialized (and very expensive) equipment.
This leaves the drive's internal bus capacitor as the most likely recipient of regenerated energy. That's OK to an extent, but as the recovered energy charges the bus cap, the bus voltage increases. If it goes too high, the drive will either shut down unexpectedly, or it will be damaged.
DC-powered systems typically get their power from a switching power supply, which can absorb some regen, but will shut down to protect itself when its bus cap exceeds the safe voltage.
Just to get a feel for the numbers, let's consider a 400 W servo system driving a 5X inertial load. The rotor inertia of an Applied Motion M0400 Series servo motor is 340 g-cm2, so the total inertia will be 2,040 g-cm2. For this example, assume the motor max speed is 3,000 rpm (314 rad/s). We can easily calculate the kinetic energy:
During deceleration, some of this energy will be consumed by the motor windings and iron losses. The drive has losses too, but it would not be unusual for 50% of the kinetic energy of the load to return to the bus cap in cases of hard deceleration. The capacitor charging formula:
Solving for the voltage, assuming a typical bus capacitance of 330 µF and assuming that 50% of the 10 J of kinetic energy makes it to the bus cap, the voltage rise will be:
That is certainly enough voltage to damage most systems if action is not taken to direct regenerative energy to a safe place. There are two common approaches. One is to add a "resistive regen clamp" that will dump the power into a resistor. Many ac-powered drives have such a feature built in. This approach is somewhat less expensive than adding bus capacitance, and more compact, but the power sent to the resistor is wasted.
Another common approach is to simply add enough bus capacitance to safely absorb the energy without exceeding the voltage rating of any drive or power supply components. This can be expensive in terms of size and cost, but has a "green" benefit: In higher-throughput systems where acceleration and deceleration cycles are frequent, the energy stored in the bus caps can be reused on the next cycle. Whether this saved energy can compensate for the added cost must be evaluated for the individual application.
Jeff Kordik,
CTO,
Applied Motion Products
Centrifugal Heat
Manufacturers of centrifuge systems have been using variable-frequency drives (VFDs) on their machines for a number of years. This alone has provided such benefits as cycle time improvements, reduction of mechanical stress, energy efficiency gains, and more precise regulation of speed and torque, just to name a few. However, one challenge when applying VFDs to the different types of centrifuge systems is how to effectively deal with the regenerative energy inherent to their operation.
A common method for dealing with regenerative energy has been to dissipate this energy as heat through the use of dynamic braking choppers and resistors (Figure 1). Although other methods have been available for some time, because of their higher initial cost or larger required footprint, these methods might not have been feasible for many centrifuge systems.
Even with advances in regenerative drive technologies, in most cases, the initial hardware cost is still higher than a traditional drive solution with dynamic braking chopper and resistor. When evaluating ROI, there are some common factors that should be considered to select the best solution. Other than initial hardware cost, some of these common factors are the required footprint, application requirements, quantification of regenerative energy to be handled, and required cooling for the drive system. Consider the following examples.
For a standalone centrifuge system, perhaps a decanter centrifuge, commonly used in a wastewater treatment facility, some of the factors that may need to be considered in the ROI analysis include requirements for a low harmonic solution and the impact of poor power factor to your utility bill. Additionally, both harmonics and power factor can potentially have an impact on the power distribution hardware within the treatment plant. In these cases, a regenerative drive solution using an active front end (AFE) may offer some interesting benefits. In general, an AFE solution allows regenerative energy to be transferred from the drive/motor back onto the power mains. This results in savings over a traditional chopper-based system by allowing the regenerative energy to be reused by other equipment (as opposed to being dissipated as heat). Additionally, the AFE solution is a low-harmonic solution also offering the capability to operate at unity power factor.
For this same application, with slightly different requirements, a different solution may yield the best ROI. Perhaps the centrifuge runs almost on a continuous basis and harmonics and power factor are not a concerning factor. In this case, a standard VFD driving the bowl connected by its dc bus to another standard VFD driving the screw conveyor might make sense (Figure 2). The continuous regenerative energy from the screw conveyor drive can be used directly by the bowl drive, reducing the amount of power consumed from the power mains. The regenerative power produced by the inertia of the bowl when stopping might be highly intermittent as the centrifuge is operated on an almost continuous basis. Therefore, dissipating this as heat with a chopper and resistor could be acceptable.
Another factor mentioned earlier that could also impact ROI is the heat generated by the drive system. Drives with integrated air-cooled heatsinks have largely been the standard solution for years. When this type of drive is installed in an enclosure, the heat generated by the drive is dissipated within the enclosure. The result is an enclosure large enough to accommodate this heat or an additional means to cool the enclosure. In many cases, air conditioners are used, consuming additional power and maintenance dollars.
Some drives provide the option to extend the air-cooled heatsink to the outside of the enclosure. This is commonly referred to as a feed-through design and will remove most of the drive-generated heat from the enclosure and transfer it directly to the air outside the enclosure. Though this might eliminate enclosure air conditioners, if the enclosure is located in an air conditioned room, the drive-generated heat must still be accounted for in the sizing of the room air conditioners. An additional cooling method available on some drives is a liquid cooling option. In this case, the air-cooled heatsink is replaced by a cold plate that transfers the heat to a cooling liquid. This can greatly reduce the enclosure size and eliminate additional air cooling requirements associated with the drive system. Even if additional liquid-to-liquid or liquid-to-air heat exchangers are required, these typically have a much lower operating cost than an air conditioning unit.
Corey Morton,
solutions architect,
B&R Industrial Automation
Make It Cost-Effective
Many applications with electric drives that incorporate frequent deceleration of high-inertia loads, lowering of loads and unwinding material cause motors to generate energy. There are two common ways to dissipate this generated energy.
One way is to dissipate the energy into a large resistor. This practice converts the electrical energy into heat energy. Another alternative is to convert the dc voltage to ac voltage and put the energy back into the power lines.
With today's focus on energy conservation and high energy costs, regenerating the power back into the power lines is an attractive alternative to heating up a large resistor. Of course, regenerating power back to the power lines has to be cost-effective to be practical. The cost of the regenerative power supply has to be less than the cost of the power regenerated back to the power lines in a determined payback period.
We developed a drive sizing software tool that can calculate the amount of energy that is regenerated in an application. With it, the parameters of the application are entered and the amount of energy that is used in the application is calculated. If the application regenerates energy, the energy is summed over the payback period to calculate the total amount of recoverable energy. This determines if the regenerative power supply is cost-effective. The energy level also can be calculated for multi-axis applications that share a common dc bus.
Craig Dahlquist,
automation product leader,
Lenze Americas
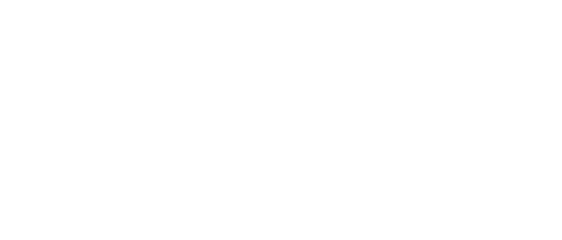
Leaders relevant to this article: