A few months ago, you printed a column about a material handling system builder that brought its panel building jobs back in-house. We've been thinking about that, too, for similar reasons. We're trying to either bring it all back so we get the benefits of volume, or just do the custom, one-off builds that have more complexity, but high value and high importance to be perfect. I'm sure we're not alone. Anybody have some ideas, experiences to share about this?
—From April '13 Control Design
SEE ALSO: Control Panel Build More Efficient In-House
Answers
Seek Out Specialists
The question of whether to build panels in-house or outsource them is part of the reason why we exist. Our customers are very good at building machines, conveyors and other equipment, often with some assistance from system integrators (SIs). However, they usually don't have the manufacturing expertise to build panels. So, they frequently outsource the panel building and PLC programming to us; the SIs do more programming and test them here; and then they're shipped to the builders or into the field for installation and more testing.
We provide a lot of after-sales support for our machines. One of our headaches is control circuit (24 V) protection, particularly identifying and troubleshooting blown circuits. The other part of this that's becoming a pain is stocking and supplying lots of types of fuses and circuit breakers. We know we can justify the extra costs for both our customers and ourselves if we migrate to electronic curcuit protection. How do we make that case to our customers?
Send us your comments, suggestions or solutions for this problem.
Overall, we see more outsourcing of panels coming to us now because we have the everyday expertise and machines to do it faster and with better quality. We have the CNC metalworking machines and powder-coating equipment that a lot of builders and SIs don't have. I think we're doing more work outsourced to us because many machine builders are in more specialized niches, and so it's a better decision to outsource.
To decide whether to build a panel in-house or outsource it, you have to look at the project's true material and labor costs. If you think it's not that hard to do it yourself, then check out the tools and time you're going to have to invest. If you're going to tie up resources to build a panel, you also have to consider whether it's worth for you to be taken away from building your core-competency machines, which are probably a lot more profitable.
It's true that panel building is getting easier with PLCs that are simpler to program and use, terminal blocks that are quicker to install and have more accessories, and with pre-fabricated cordsets and wire management solutions. However, panels must still comply with U.S. National Electrical Code requirements like NFPA Standard 70, which requires securing UL or other third-party testing and listings, and that can be another barrier to freelance panel building.
Ken Schultze,
engineering manager
Easter-Owens
Be Sure About This
We constantly deal with this from a perspective of 1) pulling in high-volume panel builds that might be being built for ABB at a third-party extension of ABB's manufacturing, and 2) helping a good customer improve profitability, quality and aftermarket support by having ABB provide the panel.
Moving panel business from a subcontractor in house is no small task, and it's not for the weak of heart. Bringing panel business in house is a large organizational commitment that will require a cross-functional team and managerial commitment from all areas of your business, including sales, marketing, engineering, production, operational excellence, IT support and finance. If company middle management have divergent goals from your panel project, it will make the project more difficult than necessary. Following a product development process and narrowing the process scope to the specific needs of the project is important. A critical aspect of evaluating the project viability of moving it in house is knowing how your panel builder contracts have been set up and, do you, as the buyer, own all engineering, including panel layouts, bills of material and metal-fabrication drawings? Knowing this up front will allow you to know if you are localizing manufacturing, or developing a product.
Also, a key factor in the evaluation of bringing panel production in house should be: Is this your core competency, or would company resources be targeted more profitably in another way?
John Tisdale,
product line manager, enclosed drives,
ABB Low Voltage Drives
More Than You Can Chew?
How big of a bite to take is always a huge issue. It definitely has a lot of complex considerations that you will need to take into account.
Based on our experience, it is very difficult to maintain a panel shop that can handle all the volume of your peak business and not be a hardship for the company when the sales cycles are low. You need to look heavily at your average build needs, and size around that regardless of the type of build you're looking at.
You'll also need to look at other ways your panel shop staff can positively impact the company. Inventory management, shipping and site technical support are all tasks that allow the panel shop to continue to deliver value to the company during the low part of the sales cycle, while maintaining a staffing level that can handle more volume when needed.
SEE ALSO: Outsourcing Is In
To manage the company's peak needs successfully, an overflow partnership needs to be maintained with a company that can augment the internal panel shop's building capacity. The best option is to set it up as a labor-only-type relationship that allows the internal panel shop to purchase and procure all the major components for shipment to the partner. This strategy will help the company maintain its volume buying power.
Partnering with another local panel shop is usually most ideal, but adding temporary labor to your internal shop is another option. Every company's situation and condition will be a little different, which means there are a lot of factors to consider when moving forward with an internal panel shop. The considerations discussed here are some of those that we have worked through in making our internal panel shop a success.
Tom Conrad,
vice president,
Wynright Control Solutions
Might Make Sense to Control It
We have many customers who decided to design and build their own panels to maintain control over the selection of components used in the application. Some panel builders quote a price, and then try to increase their profits by using lower-quality components. This can have ramifications during the entire life of the panel.
Take, for instance, the power supply used in virtually every control panel. This component is the heart and soul of every application, and can have dramatic effects on the overall performance of the panel. The price of a power supply should not be the only concern as there are other features offered in some supplies that can offset this cost difference, and in the long run can end up saving substantial money.
Up until just a few years ago, power supply efficiency was often overlooked because on the surface it appeared to add no value. However, increased power supply efficiency impacts numerous aspects of a control enclosure and not just the power supply. Extremely efficient supplies produce less heat and are often smaller in size, which can result in choosing a much smaller enclosure. It's easy to overlook, but just going up to the next size enclosure can cost more than what was saved by going with a lower quality supply. Less heat in a panel puts less stress on the components, which can lead to a longer life and less maintenance, along with the possibility of not requiring a cooling method in the panel. High efficiency along with active power correction results in a lower operating current producing significantly lower energy costs.
Typically, end users understand their application needs and requirements better than a panel builder. Knowing the application details and applying the best, most suitable components should result in a lower total application cost, despite a slightly higher price for some components. Taking control of a panel design, affords the opportunity to make the right choices, which in the long run can produce less headaches and less maintenance with substantial cost savings.
Ed Merkle,
engineering manager,
Puls Power Supplies
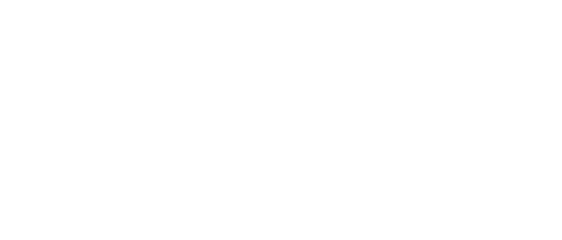
Leaders relevant to this article: