We build most of our machines by combining modules, so machine-mount controllers and I/O have been particularly effective because they allow us to test each module separately. But the cost and time required to wire the modules together at our customers' sites is a concern, and we're wondering if wireless is the right solution. Can anyone relate their experiences with machine-mount wireless controllers and I/O?
—From February '13 Control Design
Consider Carefully
In my discussions with our customers, only a few today are seriously investigating wireless I/O. If I move past the initial request for wireless I/O and inquire more about the actual problem they are trying to solve, I find out:
• For a machine builder, it is typically that they want to reduce the time, hardware and labor costs of installing the I/O products and simplify the connections required.
• For an end user, it is typically that they want to dramatically reduce the downtime caused by simple cable failures and connection issues.
A few months ago, you printed a column about a material handling system builder that brought its panel building jobs back in-house. We've been thinking about that, too, for similar reasons. We're trying to either bring it all back so we get the benefits of volume, or just do the custom, one-off builds that have more complexity, but high value and high importance to be perfect. I'm sure we're not alone. Anybody have some ideas, experiences to share about this?
Editor's note: The column referred to is "Panel Build More Efficient In-House."
Send us your comments, suggestions or solutions for this problem.
When I run into the rare customer that has implemented a wireless I/O solution, it is typically fraught with new problems like completely dead communication zones, intermittent connections, limitations of proprietary systems and, the biggest trouble of all, they still have to get power to these devices. So, although the wireless communication solution in theory seems to be cable-free, power connections still have to be run through the machine.
For the past few years, many device manufacturers and consortia have been discussing the possibility for not only a wireless I/O solution, but a wireless sensor actuator network (WSAN) or wireless sensor network (WSN). These types of networks would have a master data collector communicating with the controller, a cohesive communication between all the sensing devices, and the master via an open standard. But today, in my opinion, developments still need to be made in battery and power technologies to make it cost-effective and reliable in mainstream industrial designs.
For machine builders looking to implement wireless I/O technologies today, I would suggest they consider three things:
1. Think simple. What am I actually trying to solve by implementing wireless? Is there a simpler solution available?
2. Predict problems. What is the potential for noise, communication interference or dead zones in my design?
3. Consider power. How will I get power to these devices? Cables, batteries, wireless? What is the total cost of ownership of the solution I selected? Is it energy-efficient?
Will Healy III,
marketing manager, networking,
Balluff
Not Zero
Wireless is nice because — at least on the surface — it looks like a way to get rid of the cable needed for the I/O. But looking at this a bit more carefully, the sensors (and outputs) have to somehow be powered. Consequently, at least two wires (let's say +24 Vdc and GND) need to be brought to the I/O.
Although this is of course better than having to run dozens, if not hundreds, of cables for power and data, the number of wires is not zero. The other concern is that data over a wireless connection is, in most instances, slower and less reliable.
In a situation where a user wants to drastically reduce the number of wires on a machine, I typically suggest AS-Interface, which is a two-conductor power and data network. Modules are connected to those two wires, receive power over those two wires (just as in the case of the wireless approach), and exchange I/O data. In all fairness, I have to say that outputs are typically (but not always) powered from an additional two-conductor auxiliary power cable, so worst case, four wires will give this customer everything that is needed with the following benefits:
• High data rate and deterministic update times in the order of milliseconds (248 input update every 10 ms, 248 output update in 20 ms)
• The possibility to connect digital I/O and analog I/O
• The ability to connect functional safety devices up to Cat. 4/SIL 3/PLe to the same solution (mix and match standard and safe hardware as needed)
• Low cost
• Many I/O modules are rated at IP68/69K and suitable for washdown applications
• Simple setup (Watch "How to Build AS-Interface Network" for a step-by-step demonstration).
Helge Hornis,
manager, Intelligent Systems Group
Pepperl+Fuchs
Makes Sense in Places
Wireless is a great solution, but it really depends on the machine or application. There are also many different types of wireless, including Wi-Fi, Bluetooth, Zigbee and proprietary systems based on these or similar standards. However, these standards are very different.
For example, Wi-Fi has data transfer rates in the range of 54 Mbps (or higher), but has a limited range of 30 ft at this speed. On the other hand, proprietary long-range systems can easily cover the largest plants, but only handle a few bytes of data from endpoints. This is because of physics; fast data rates require strong signals, while long-range systems average the signal over time, which slows down the data rate.
Obviously, the major advantage of wireless over wiring systems is the savings of time and money. Therefore, wireless is naturally suited to machine locations where wiring is a significant cost. For example, long distances, cable tracks or slip rings usually can be done less expensively and more reliably using wireless.
An ideal application for wireless is monitoring the status of a fleet of machines on the production floor. If the machine status is reported wirelessly, there is no need to install control wires to the machine. This also has the benefit of reducing the cost and time required to reconfigure the production layout on the plant floor. The machines can be moved quickly and easily with no rewiring. The wireless system can track the machine status and production parameters in real time, allowing the end user to improve production.
A wireless approach is also an ideal option when the entire sensor can be made wireless and eliminate both control and power wires to the sensor (this also eliminates much of the PLC I/O card and control cabinet as we know it). To achieve this, the sensor needs to be battery-powered. Today, many sensors, including magnetic reed sensors, photoelectrics, temperature sensors, pressure sensors, limit switches and more, can last for years on a single battery.
Additional optimal applications for wireless include automated guided vehicle (AGV) or mobile applications. Wireless allows continuous access to the AGV's status and provides the ability to control the AGV remotely in real time.
Bob Gardner,
senior product manager,
Banner Engineering
Try a Hybrid Approach
We have been able to overcome the complexities and costs associated with long-distance communications and process control setups by using a combination of wireless and wired solutions. Wiring costs are often overlooked in the early stages of projects. More times than not, all the costs associated with wiring and labor are not fully realized until quotes are gathered from the installation contractors. It is then that many of our customers contact us for alternatives to the mounds of wires and marshaling cabinets.
Once our customers accept wireless communication methods as a viable alternative, we strongly recommend bench setups and verification of communication links. This greatly simplifies the field portion of the installation.
After the initial application assessment, we find that wireless communications is not the sole remedy for jobs that incur large wiring overhead costs. The best communication link solutions can vary by application and distance. Consolidating multiple signals over Ethernet has advantages of being able to move large amounts of data at very high speeds. This also allows the simultaneous transfer of program updates and even data-logging files when necessary. Serial is slower, but usually less expensive because a twisted pair only can be used to support several remote sites, which is valuable when only a few bytes of information need to be moved.
Wireless of course has a higher initial investment per site, but significantly overcomes virtually all complications of trenching, drawings, permits, and communicating short to long distances. Hybrids of these systems are common without introducing complexities or difficulties.
An example is a major water district that uses intelligent controllers at remote sites with one control room. Communication is via Ethernet for nearby sites. Wireless Ethernet radio pairs are used interchangeably with Ethernet cables (without any modification to any addressing or message content) when it is necessary to communicate to those sites with no Ethernet cable. These wireless and non-wireless Ethernet communications links are used to download programs into several of the remote site controllers. These controller sites manage water tank levels, flow rates, pump motors and valve/position feedbacks.
Periodically, a remote site uses the communications link to access the time of day from the control room to make the decision if this is the most economical time (price of electricity varies during the day/night) to pump water into particular reservoirs or divert to alternative tanks. Via the same communications link, the control room status and panel automatically accesses remote site internal alarms, channel setups, set points and tank activity.
Should a remote site incur an aberration, the control room uses the wireless link to monitor all remote error messages, including such details as a broken wire on a field sensor. During periods of extended quiet activity, the control room downloads the various remote site internal data logger files or uploads new set points for tank levels.
Another example is an oil company with an extended field of wells. Each well required a PLC-controlled cathodic protection system with its rectifier, voltage, solar panel controls and also product flow and tank levels. Initial testing for the nearby sites used RS-485 twisted-pair cable between all of the nearby remote sites and the control room.
Data consisted of RS-485 serial devices from multiple vendors, including the PLC. This is normally a potential nightmare, but proper bench and prototype field testing was performed to optimize setup parameters for Modbus RTU communications. For expansion to literally hundreds of remote sites, wireless radios were assigned to individual remote sites or to one radio to a cluster of remote sites. The hybrid wireless system communicates from a single host computer and a single twisted-pair cable to both nearby sites and wireless remote sites.
Increasingly, wireless and hybrid wireless solutions as mentioned above are used to reduce the overall cost of remote site and multi-vendor equipment integration.
Jim McConahay,
field applications engineer,
Moore Industries
Wireless With Machine Mount
There's no doubt: On-site wireless can be very beneficial for machine-builders. However, minimal data transmission delays mean it's not perfect for all applications, such as time-sensitive conveyors or packaging machines. Hardware redundancy is another factor to consider — will additional routers or other networking hardware be needed for reliable machine-to-machine communication? If so, project costs and commissioning time can both escalate rapidly.
If timing isn't an issue, wireless machine-to-machine coordination backed by localized IP67, machine-mount controls can be the right solution. We have a system, for example, that places IP67 PLCs and related I/O right on the machine. This localization ensures there is virtually no delay time for run/stop commands, preventing scrap or rework.
Machine-mount I/O is also incredibly simple to wire via M12 connectors that handle both communication and power. Within this architecture, you can tie in an IP65 Bluetooth Ethernet Gateway to enable machinery to wirelessly transmit operational status information between each other.
The larger the project scale, the greater the benefits; imagine this IP67/wireless blend in a processing facility with multiple lines of machinery.
Charlie Norz,
product manager — Wago-I/O-System,
Wago
Mixed Offerings
We had explored offering a machine-mount wireless I/O system for discrete applications, but we felt we could offer more competitive solutions with a mixed offering, which includes standard I/O technology, plus newer network technology such as IO-Link.
With IO-Link, we can combine multiple discrete devices, such as solenoid valves, and integrate them with a single M12 connector interface. With an appropriate controller, the installation time and costs can be reduced by up to 50%.
IO-Link provides a reliable, point-to-point interface which is fast enough between a controller and typical machine I/O. The link is also bi-directional, which allows for diagnostic or parameter data to be transferred as well, providing additional benefits.
Frank Latino,
product manager valve terminals and electronics,
Festo
Play It Forward
Although wireless technologies offer a perceived advantage over wiring, you might be looking a little too far forward. Properly designed and installed distributed I/O systems should offer you a substantial savings on hardwiring costs — up to 40% in many cases.
Building your machine in a modular method also lends itself to machine-mount I/O control. Machine-mount I/O allows for the use of pre-engineered I/O modules designed for machine vibration and environments to be assembled to pre-engineered and tested cables for power, sensing and valve control, limiting errors and reducing your wiring time.
We offer a system that reduces your communication and power cable to only one combined cable that you simply daisy-chain together between your choice of I/O modules. Attaching the device cables is a matter of tightening down industry-standard M12 or M8 connections, so you can avoid a lot of the hardwiring pit falls.
Wireless technologies on the whole have not settled on constant communication standards and are still, in general, only used in non-critical applications like monitoring or status notifications. With each wireless technology you try to implement, the learning curves are relatively steep — distance, interference, integration and speeds become subject to a number of unknown equations.
I do believe wireless technologies are improving and are worth experimenting with, but machine-level control and deployment might not be what you are expecting.
Aaron Henry,
marketing manager,
Murrelektronik
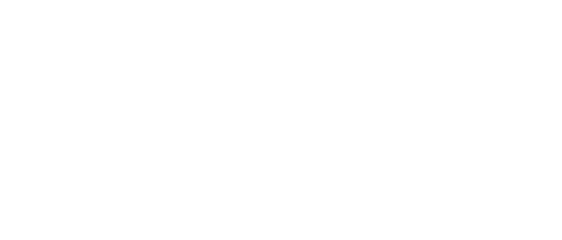
Leaders relevant to this article: