Rich Rogals is sales director for printing, coating and lamination at PCMC, a Barry-Wehmiller company located in Green Bay, Wis.
Competitiveness for OEMs today is all about anticipating total customer needs, and then delivering a complete solution. Our customers buy our printing technology because of quality. There is more we can do to help, and that is why we dove into the motion architecture to find strategic solutions that would not only lower operating and support costs, but also support high throughput.
SEE ALSO: Linear Motion Goes Beyond Point B
Paper Converting Machine Co. (PCMC) is a leading global manufacturer of wide- and narrow-format printing equipment, as well as paper and wipes converting and packaging solutions. In 2009, PCMC began design of Fusion and FusionMax, its next generation wide-web high-speed flexographic printers.
Fusion is an eight- to 10-color, 1,500 ft/min (450 mpm) flexographic press available in 42, 52 and 59 in. widths. FusionMax is offered in 66 and 75 in. print widths. These state-of-the-art printing presses offer a host of benefits, including a 60-minute changeover and full-press, automated washup in four to eight minutes. The press also delivers the sustainability benefits of low solvent use and low energy consumption. Jason Manders, PCMC product line manager, estimates that these machines can be 40% lower in terms of total energy consumption compared to our competition, and use about half as much as our previous generation machines. Solvent usage can be about a third of similar, competitive machines.
"In our development of the Fusion and FusionMax, PCMC went deeper than state-of-the-art printing technology," says Rodney Pennings, value stream leader for PCMC. "The company delivered machines that drive toward lowest total cost of ownership (LTCOO) and highest overall equipment effectiveness (OEE). The triple focus on print, cost, and throughput led the company to identify motion actuation systems as strategic to LTCOO and OEE, and it placed substantial design and engineering resources behind networked pneumatic actuation."
Manders says this initiative was both a response to customer needs and an effort by PCMC to proactively seek competitive advantage. "We're pretty competitive with our pricing," he adds, so these benefits don't really come at a premium for our customers."
Pneumatics Not High on Wish List
Below the surface, the Fusion and FusionMax printers are complex, motion-controlled devices with hundreds of actuated-motion adjustments made automatically throughout setup, operation, and cleanup stages of a print run. "Linear actuators and rotary cam-based motion, both powered by pneumatics, can perform many of the motions on the presses," explains Doug Zilz, fluid power designer, PCMC. "While a single linear or cam motion is relatively simple, groups of actuators can be synchronized for complex multiple-motion operations such as bringing a doctor chamber into position and applying pressure on it."
The doctor chamber force load cylinder(lower left) on the Fusion presss brings the doctor blade chamber into position against the anilox roll. The cylinder in the upper right is the doctor chamber lock-up cam cylinder that provides a positive back stop for the doctor chamber.
Source: PCMC
PCMC designers performed a cost-benefit analysis between pneumatic and electro-mechanical activation for these numerous motions, including the Vortex ink delivery and wash-up systems. The motion tasks include engaging doctor chamber to print roll and locking doctor blade in position. Pneumatic actuation was the clear cost-benefit leader when they considered component cost, small footprint, and overall operational, maintenance, and inventory costs.
There's a lot of interest in migration to electro-mechanical solutions in many machine builder industries because of simplicity. And many companies think a compressed air solution is messier, more difficult, and costly utility to manage. Those options, however, don't come into play here.
"A solvent-based ink environment means motion components have to be classified as Class 1, Division II-compliant," Zilz explains. "Pneumatics makes that much easier than having compliant electronic devices. The variety of complaint devices might not be there in an electro-mechanical solution."
In addition, says Jacqueline MacPherson, Festo industry segment manager for printing, paper and converting, "A designer must always weigh many factors to compare the advantages for the use of electro-mechanical products. Those factors are speed and accuracy requirements, cost comparison and foot print into which the actuator must be placed. With the example of the doctor blade loading the area in which the actuator mounts is very small. An electro-mechanical solution would not fit within this area. Speed and accuracy were not needed for this function and therefore the pneumatic solution was cost effective and fit within the space constraints." MacPherson worked for PCMC during the Fusion and FusionMax development and rollout.
"Customers of our presses simply do not delve into this level of componentry," Zilz says. "Yet cost-effective automated, pneumatically-based motion is at the heart of these state-of-the-art printing presses." He adds that it's somewhat rare in the flexographic press sector when a customer dictates a component brand or choice of applied technology.
This valve bank manifold provides functions that include an air-sleeve exchange, raising and lowering a guard hood, a positive drawer position lock-up, and a web nip.
Source: PCMC
Next-Gen Pneumatic Control
Simply opening a catalog and purchasing pneumatic valves — the components that control actuator motion by allowing pressurized air to flow on automated signal or stop on signal—would not be enough to satisfy LTCOO and OEE objectives. Common solenoid operated valves are typically hardwired with two wires per valve. That would mean connecting, troubleshooting, and maintaining hundreds of wires from control cabinet to valves. "That's a nightmare by anyone's estimation," Zilz adds. "An effective solution meant finding state-of-the-art networked valve terminals, i.e., manifolds wherein multiple solenoid-activated valves could be nested and controlled with a single communication cable. We wanted Ethernet-based communication with all of the speed, bandwidth, and diagnostic capabilities inherent in Ethernet solutions. "Depending on how many valves you have, there's tradeoff of the extra cost of Ethernet compared to the time it takes to hardwire each component," Zilz explains. "Ethernet saves us that time and provides diagnostic capabilities for a near plug-and-play solution. It was a large cost saving for us to wire this with Ethernet."
PCMC wanted to collaborate with a supplier that offered the networked-pneumatic solutions required, and provided the business benefits of global support, rapid product availability, and comprehensive training. PCMC began working with Festo.
SEE ALSO: Is Pneumatics Still a Good Solution?
After a series of initial design conferences, Festo proposed a CPX electro-mechanical/pneumatic control-based architecture. "The CPX is the logic interpreter sitting between a PLC — in PCMC's case a Rockwell Automation PLC — and the Festo valve terminals," says Frank Langro, Festo product manager. "Communication between the Rockwell PLC and Festo CPX platforms would be Ethernet-based. The Festo CPX platform would control both Festo VTSA and CPV model valve terminals. VTSA and CPV manifolds are controlled via a single communication cable. The VTSA can nest an assortment of up to 32 valve positions/32 solenoid coils with flow rates ranging 400–2,900 l/min. The CPV manifolds accommodate an assortment of eight valves with flow rates from 400-1,600 l/min. Plans called for two VTSA manifolds with 40 valves, and eight CPV terminals with 64 valves."
The CPX controller gives PCMC a portal for fast and flexible programming of valve functions during commissioning, and is the portal for diagnostic information and rapid and effective troubleshooting to improve uptime. Troubleshooting can be done at the customer site through the Rockwell PLC, or PCMC can remotely log into the system via the Internet.
The CPV terminals are compact and their small size enabled us to mount the eight terminals on the Fusion and FusionMax frames as close to points of actuation as possible for optimized response time. Close proximity to the actuators also meant shorter runs of tubing for material savings and less chance of air leakage. The VTSA manifolds would mount in the control cabinets. Each valve could potentially have a sandwich-style pressure regulator if needed and this capability gave PCMC design engineers a greater range of available air pressures for actuator control.
"An important feature of these terminals is that different-sized, different-capability valves can mount on one terminal," Langro explains. "This gave PCMC flexibility to select the valve for the air pressure required for the actuation, as well as the type of valve best-suited to the application requirement." These capabilities help PCMC to ensure lowest possible energy usage, optimum component cost, and greater operational effectiveness.
VTSA is ISO 15407-2 compliant, which means it can use any manufacturer's valves that meet this ISO standard, giving customers the flexibility to choose the valve option right for them. "Interestingly, says Langro, testing showed that the airflow of the Festo valves with the VTSA valve manifold was higher than competitive valves when using the sandwich-style pressure regulator as part of the valve stack. This means a smaller Festo valve as compared to a competitor's unit could be used." Correctly sized valves contribute to lower energy consumption.
"We saw that one Festo dual 3/2 valve can be configured to perform two different motion operations at the same time," Zilz says. "For example, a single, dual 3/2 valve could be used for air exchange on an anilox sleeve and for raising a hood guard at the same time. This reduced the number of required valves, lowering the number of components and saving space and component cost."
Festo pre-assembled each VTSA and CPV manifold to the desired specification and sent the assemblies to PCMC, where they could be mounted on the machine or in the cabinet and run on one cable per manifold. All of these features contribute to LTCOO.
Festo and PCMC collaborated on training on all aspects of CPX, VTSA, and CPV so that PCMC technicians and trainers are more than adequately prepared to help support customers.
The Fusion model was introduced in 2010 and the FusionMax in 2011. Both machines feature the same networked-pneumatic valve terminal architecture.
"PCMC applied a multi-step checklist comparison of several brands, and Festo won," says Zilz. "Some of the other brands don't have the Class I, Div 2 rating and Ethernet as we need it, and Festo was entirely price competitive."
Recently PCMC introduced its next-generation, narrow-format printing press, the Aquaflex ELSMax, which uses a valve terminal with pre-assembled multi-pin cable and VTSA valves. "Where it makes sense, PCMC technicians replace non-networked valves with networked Festo valve terminals during maintenance calls on non-Fusion, FusionMax, and ELS-Max printing presses," Pennings says. "This means the new solution with all of its advantages is working its way through PCMC's past and future installed base.
"The total cost of ownership of our machines, including lower energy consumption, has fallen while the overall equipment effectiveness has risen using a Festo platform that features Ethernet communications and state-of-the-art valve manifolds," says Pennings. "PCMC recognized an opportunity to increase the value of our solutions through a re-engineering of strategic motion systems, and we will continue to find new ways to improve this important cost and productivity effort."
Jacqueline MacPherson, Festo industry segment manager for printing, paper and converting, worked for PCMC at the time of this project and was directly involved in evaluating the project economics. Here are her recollections of the project savings:
Wiring Costs – "The PCMC assembly team estimated that it costs approximately $50 per valve to hardwire it in. That cost includes labor to run the wires, cost of the wire, termination strip cost. The Fusion Press has 10 valve manifolds with eight valves per manifold. The cost was 80 valves x $50 = $4,000. By using the Ethernet solution, each manifold is brought back to the CPX communications module by a single cable. So, 10 cables x $15= $150, plus 1 hour of labor at $65, for a total of $215. This equates to a cost savings of $3,785."
Commissioning – "According to the electricians, it took approximately three hours to fully test and commission the hardwired solution. The Ethernet solution took 30 minutes to test and commission. The assembly hourly rate is $65 per hour, so cost of hardwire labor would be $195, while the Ethernet labor cost was $32.50. This equates to a cost savings of $162.50.”
Flexibility– “Customers will ask for additional features to be added throughout the project life cycle. When hardwire is used the addition of valves can create major issues for the OEM as it relates to added costs through assembly (see wiring costs), testing and commissioning."
Troubleshooting – "With hardwiring maintenance must do the troubleshooting for each wired connection until they can locate the issues. This means the machine could be down for hours. With Ethernet, the operator can identify the issue through fault feedback going to the HMI in minutes. This means less downtime of the machine. If a machine goes down it can cost the company thousands of dollars in lost revenue."
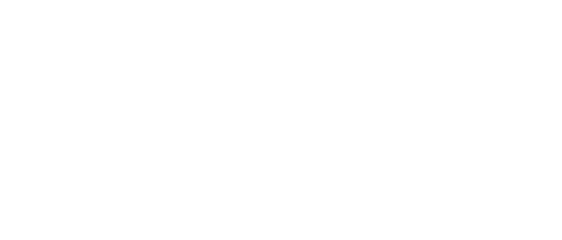
Leaders relevant to this article: