Over the several years we've surveyed our audience regarding its particular uses of mechanical components in its machine designs, the respondents are quite consistent about the chief challenges they confront while facing relentless pressure to improve machine performance, flexibility and reliability. They rank these challenges by importance thusly:
1. Integration of electronic and mechanical components
2. More precision/less drift
3. Faster updates/better synchronization (this was fourth on list in 2009)
4. Integration of digital safety with motion (third in 2009)
5. Migration to more electronic components and away from mechanical
6. Combining electronics with pneumatics and/or hydraulics
7. Migration to more electronic components and away from pneumatic and hydraulics
SEE ALSO: Integration Tops Motion Challenges
Our audience often reminds us that an entirely electronic solution isn't always the best solution. In a recent article, "From A to B With Mechanical Control," Tekno, a builder of conveyors and material handling solutions, told us that cost is one reason the company sometimes turns to mechanical motion control. A mechanical solution usually is cheaper initially, and it can cost less to operate because of lower support costs and quicker time-to-repair. "That's a consequence of the simplicity of the system and the ability to spot and diagnose problems quickly," said CEO Larry Mustread. "I know that it's going from point to point. If it starts losing that movement from point to point, it's easy to pick up that I'm getting wear somewhere."
Similarly, Darek Tkacz, chief mechanical engineer at M&R Printing, a screen printing machine builder, said his company's initial solution for a demanding indexing requirement involved a direct-drive approach with a high-end servo motor and gearbox. The latter had less than 0.05° of backlash — an accuracy needed because it had to position a carousel within a stationary fork to lock it. For a 40 in. diameter carousel, the location had to be accurate to within less than 0.002 in. Though the direct-drive approach worked and offered higher throughput, it was significantly more expensive than the pneumatic method. So for its lower-range machine, "instead of a direct drive, we installed a crank-type index design," Tkacz explained. "The crank is connected through a link to a capture fork, so rotary motion is converted into linear motion back and forth."
He said the crank design boosts the throughput of some presses by about 50%, with little increase in price over the older technology, partly because the crank arm method is more forgiving in what it demands from a gearbox. "We've been able to choose a gearbox that can have 10 arc-min backlash and we can still achieve our linear accuracy for the indexing."
AGR Series motorized rotary worm-gear-drive stages claim accuracy to 20 arc sec, with 8 arc sec bi-directional repeatability, 30 rpm maximum speed, and 360° continuous or optional limited travels. Tilt error motion is 10 arc sec, axial error motion is 5 µm, radial error motion is 10 µm, and maximum axial load is to 425 kg. Apertures are available at 50–200 mm diameter. Vacuum-compatible versions for pressures to 10-6 torr are available.
Aerotech
(412) 963-7470
Dodge Maxum XTR concentric reducer with precision, carburized, ground gearing meets AGMA Q11 standards and AGMA 2301 cleanliness specifications. O-ring sealing and steel shims eliminate gasket creep. The reducers are available in nine case sizes, with torque ratings 9,800–575,000 in-lb torque. Reducer accessories include internal high-capacity backstops, shaft-driven fans, scoop motor bracket package, or top motor mounts.
Baldor Electric
(479) 646-4711
Original Line Electric Thruster (OLET) guided electric cylinder combines the Original Line Electric (OLE) cylinder with the strength of the legacy T/TE pneumatic thruster, with speeds to 24 in./s and thrust to 350 lb general-duty and heavy-duty versions offer three bearing options.
Bimba
(800) 44-bimba
New 9/16 in. bore stainless steel cylinder in stud or universal mount, double, single or reverse acting, rotating or non-rotating rod has standard stroke lengths to 4 in. It has polished I.D. stainless steel tubes; machined aluminum heads; sintered bronze bushing; ground, polished and roller burnished 303 stainless rods; Buna-N U-cup piston seals; and Buna-N U-cup rod seals.
Clippard Instrument Laboratory
(877) 245-6247
400 Series Profile Rail Linear Guides are available in 4 m lengths with rail sizes 5–45 mm in 5 mm increments. They include double-faced, ball-track bearing arrangements with standard or ball-cage carriages that use the same rail design. Guides are rated to handle loads 9800–129,500 N.
Thomson
(540) 633-3549
Mini-MAG (MMG) linear positioning stages offer sustained throughput to 2,000 moves per minute for XY sample positioning. 25, 50, 100 or 150 mm travel are available with accuracy of 3–6 µm and analog or digital encoder resolution ranging 1.0 µm to 1 nm. Each model has repeatability to ±0.4 µm, and is rated for 10 kg load capacity. Integral anti-creep linear guideway can increase uptime by eliminating homing moves.
Dover
(800) 227-1066
SureGear PGA servo gear reducers have a concentric shaft design with a maximum 5 arc-min backlash rating, and are available in 5, 10, 15 and 25:1 gear ratios. Additional features include helical-cut planetary gears and uncaged needle roller bearings. Mountable in any direction, the PGA series is maintenance-free.
AutomationDirect
(800) 633-0405
K90 linear actuator dimensions and form-factor consistent with ISO Metric pneumatic cylinder specifications directly replace pneumatic and hydraulic actuators. Three models offer two grades of planetary roller screws and one Acme screw. They allow complete flexibility in the type and style of motor selected to drive the actuator, including dc motors, stepper and servo motors.
Exlar
(952) 500-6200
Harmonic gearhead replaces larger, high-ratio planetary gearheads using the latest harmonic, strain-wave gearing technology. Advantages over planetary gearing include high torque, true zero backlash and precise positional accuracy. Low-friction design delivers 99%+ efficiency at high speeds to 11 m/s.
Nexen Group
(651) 484-5900
LDAT-Series Integrated Linear Thruster has a moving-magnet, iron-core, linear-motor actuator with a built-in linear guide to carry a load. The motor is capable of 5 m/s, and peak thrust forces range 187–4,306 N.
It can be used with any Allen-Bradley servo drive, and uses SpeedTEC DIN connectors.
Rockwell Automation
(414) 328-2000
The BGS06 ball guide screw linear rail uses size 17, single-stack or double-stack stepper motor linear actuator and precision rolled 303 stainless steel lead screws. Lead screws are coated using Black Ice TFE. Maximum stroke length is 24 in., maximum horizontal load is 135 lb. Its moment load capability is 11.62 lb-ft roll, 7.93 lb-ft pitch, and 9.15 lb-ft yaw.
Haydon Kerk/Ametek
(203) 756-7441
DGSC microslide for small spaces has positioning accuracy of 0.01 mm due to the preloaded ball-bearing cage guide. The slide has low breakaway torque and travels jerk-free starting at 15 psi.
Festo
(800) 993-3786
Type ES actuator combines caged ball LM guide Type SRS and a rolled ball screw equipped with a QZ Lubricator. Type EC actuator also uses a rolled ball screw equipped with a QZ Lubricator in two models with widths ranging 40–48 mm and heights 48.5–57.5 mm.
THK America
(847) 310-1111
Rodless actuators include OSPE B belt type for light to medium applications with high speeds and long travels, OSPE BHD belt type with integrated ball bearing for rigidity and low-profile, OSPE SB ball screw for light to medium applications for precise positioning and high thrust at 100% duty cycle, and OSPE ST trapezoidal screw actuator for lower speed and highest thrust force transmission with no back drive.
Parker Electromechanical Automation
(724) 861-3252
Design alternative to screw-based linear drive systems, Model RS4 drive nut provides backlash-free linear motion. The linear pitch is factory-set at one of five different linear pitch settings, determined by application requirements. Pitch wedges between the drive bearings hold them at a specific angle relative to shaft to set linear pitch. Change pitch with a different set of wedges without other components, machinery or controls.
Amacoil
(610) 485-8300
Power drawbar holds cutting tool in the spindle taper with gripper fingers that are pulled into the taper with the spring pack. Loss or reduction in hydraulic pressure will not release the tool. The power-off design requires pressure applied to the hydraulic piston and transmitted through the rod to push the clamping sleeve down.
Ott-Jakob/Advanced Machine & Engineering
(800) 225-4263
W37/W47 Spiroplan right-angle gear units with aluminum housings are lubricated for life, and can be mounted in many orientations with the same amount of oil. First-stage helical gearing and second-stage hypoid gearing combination provide high mechanical efficiency and low energy consumption compared with worm gear units.
SEW-Eurodrive
(864) 661-1122
Sigma Trac SGT linear actuators have automatic motor recognition, speeds to 5 m/s, as well as acceleration to 5 Gs. Large integrated cable carrier allows space for peripheral cables and hoses, and covers and additional accessories are available.
Yaskawa
(800) 927-5292
Zero-Max Crown right-angle gear drives with AGMA Class 10 spiral bevel gears and non-magnetic, stainless-steel shafts have precision hardened and ground ball bearings for speeds to 2,000 rpm. The internal gears are permanently mounted to the shafts with locking pins. Standard two- and three-way models have 1:1 and 2:1 speed ratios in shaft diameter combinations of 3/8, ½, 5/8 and ¾ in.
Zero-Max
(800) 533-1731
Geared to Go
Precision planetary gears for synchronous and stepper motors are single-stage for gear ratios i=3, 4, 5, 8 and 10, and have ≤8–15 arcmin backlash. The gears are offered in two- or three-stage designs. The premium series has backlash ≤1 arcmin as an option paired with high-output torques. The gears are delivered fully mounted on 8LSA, 8LVA, 8JSA and 80MP series motors.
B&R Industrial Automation
(770) 772-0400
Slimline-normal and slimline-long runner blocks replace ball rail with roller rail systems to increase the load capacity of the axis. Corrosion-resistant Resist CR version has a matte silver, hard-chrome-plated steel body. The line sizes range 25–55 in accuracy classes P and SP.
Bosch Rexroth
(800) 322-6724
Camco RSD zero-backlash, cam-actuated drive can be used with both rotary and linear systems. It is compatible with a variety of industry-standard servo motors, and offers ratios of 4:1 to 18:1 in a single stage. Output options are large flange with through hole, 32 mm diameter shaft, external shrink disk for 30 or 40 mm shaft, and internal shrink disk for 30 mm shaft.
De-Sta-Co
(248) 836-6750
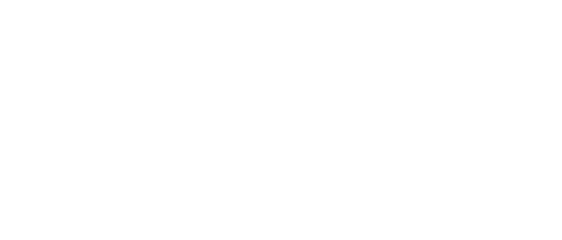
Leaders relevant to this article: