Making the boxes that the boxes of granola bars go into is a process that has been made more energy-efficient by design, according to Dan Aubertin, senior product manager at Pearson Packaging Systems, Spokane, Wash. Doing so also upped throughput by more than 40%.
This tale illustrates what's possible when systems are designed to be more energy-efficient. Pulling off such an improvement could require using the latest technology, which can enable sleep or other efficiency-boosting modes. Solutions might demand system-wide changes, such as swapping out one mode of motion for another. A final design-related area that could be a part of the answer is automation. That can allow savings to be realized without impacting production.
Airing Savings Out
In the case of Pearson Packaging, all of these techniques were used or are being considered for use. The company designs, produces, integrates and services an array of secondary packaging automation solutions. A system can take materials such as cardboard flats, fold and erect them into rectangular shapes, and seal them to create a container. Into these boxes are placed food, beverages and other types of goods for shipment from manufacturers to warehouses or retailers.
Traditionally, the motions required to fabricate these secondary containers have been handled by pneumatics, with air-powered cylinders using force to shape and manipulate cardboard as needed to erect the boxes. However, Aubertin thinks this is not the most efficient way to do the job, in part because of flaws in the basic system design.
Also read: Gain the Upper Hand With Energy-Smart Machine Design
"Compressed air goes through several energy conversions," Aubertin says, listing these as electrical energy driving pumps to compress air, which then drives pneumatics. "You have three energy conversions. Every one of those is inefficient."
FIGURE 1: By design, Pearson Packaging replaced pneumatic with servo motion, saving energy and boosting throughput its family of machines.
The total efficiency of multiple energy conversions to produce compressed air is somewhere south of 20% and can be much less. In contrast, servomotors come in at around 80% efficient, Aubertin says. He adds that most pneumatic motion can be replaced with servomotor-driven movement, a design change that by itself can boost efficiency.
But servomotors allow even more improvements to be done. For one thing, they have closed-loop feedback. That enables acceleration and deceleration profiles to be tuned, cutting even more energy waste. To that can be added sleep modes, which are times when the system is idle and consuming little energy, but is ready to quickly resume processing product.
Pearson Packaging redesigned its CE50 family of case erectors (Figure 1) with the new design using servomotors rather than pneumatics. That reduced air consumption to nearly nothing, a key customer request. The changeover also upped throughput from 35 to 50 cases per minute, Aubertin says.
An important feature to design in is the capability to put a machine in the right state.
"It's really around the ability to go into operational and non-operational energy management. That's the aspect of taking it beyond just efficient motors and to making sure I'm only on when I need to be on, and I'm off when I don't have to be on," says Phil Kaufman, business manager for industrial energy management at Rockwell Automation.
Figuring out how to make a machine move illustrates the design tradeoffs impacting energy savings and other green objectives. For motion, the choice is between electric, hydraulic and pneumatic.
For environmental and other reasons, there's a trend away from hydraulics, says Rockwell Automation's North American OEM commercial manager, Andy Pringle. In the event of a spill or leak, hydraulic fluid can be a safety or environmental hazard. Also, machines requiring oil are a logistics burden, since the fluid has to be replenished.
When it comes to compressed air, reducing or eliminating pneumatics in an individual machine can save significant energy. In new plants, those gains can be multiplied across the entire factory.
"If you had a greenfield site, and you reduced the requirements of the pneumatic compressors, the end user could benefit from that from an energy cost savings standpoint," Pringle says.
However, he adds, for older plants, any energy savings could be reduced, perhaps substantially. That's because compressors that are already in place have been sized for the original maximum load. Even if part of the load is eliminated, it might not make sense to change out the compressor. Consequently, any machine-level energy savings could be washed out by the overall factory situation.
It also can be the case that energy savings or green concerns are not the overriding factor in a decision. A machine maker or an end user may opt to standardize on a particular motion technology because it makes support and other aspects of running a factory easier.
"More and more the trend is to reduce the number of disciplines on the machine," says Bosch Rexroth's director of service for factory automation, Arnold Mueller. "Now you get to hear 'I need an all-hydraulic solution,' or 'I need an all-air solution,' or 'I need an all-electric solution.'"
Some of the methods to do this are found in the control system, while others arise from the design and architecture of the machine. For instance, with regard to design, there might be a choice of materials and construction for a heater. One configuration might take 45 minutes to reach and stabilize at temperature. Another approach might do the same in 10 minutes. If the production process has repeated 15- to 45-minute idle-time windows, then the faster-acting heater could end up saving energy.
Other aspects of machine design can determine what energy-saving strategies can be pursued successfully. Take the case of a machine engaged in batch processing. Shutting the system off can save power, but any restart should not be a lengthy process. Some basic design and technology choices can make this possible.
"The way to do that is to have absolute feedback devices on the machine, not relative feedback," says Andy Pringle, North American OEM commercial manager for Rockwell Automation. "If you do power down, then when you power back up, you know your position, assuming no mechanical changes have occurred in between. You're in a faster ready-to-start position than if you have to home and recycle the machine. Also, you have not interrupted the flow of the product."
Other energy savings can arise from designing with alternative actuator technologies, he adds. For example, replacing a mechanically driven system with a linear motor can save energy, and it might allow the actuator to function outside of an environmentally controlled cabinet, further reducing energy demands.
If pneumatics must be used, then design choices can minimize waste and maximize energy efficiency. For instance, locating and identifying air leaks can correct energy waste, says Kurt Wadowick, I/O and safety specialist at Beckhoff Automation. He notes that his company's EtherCAT box enables differential pressure measurement over a 0 to 15-psi range with a resolution of 0.015 psi, and devices like this can improve a design by their adaptability to specific situations. "This solution can be machine-mounted or placed on robot arms for flexible pressure measurement right at the source," Wadowick says. "This box has four pressure inputs with integrated 6-mm fittings to connect the hoses."
Design Savings in the Wind
Friedrich Wenner of Versmold, Germany, also works with cardboard. The company manufactures food cartons, which today not only have to hold product, but often have to provide point-of-purchase advertising and promotion. The packaging must be customized and changed on the fly.
FIGURE 2: Plant automation using separate screw compressors helped Friedrich Wenner shave energy consumption by 10%.
Wenner's automated punching, printing, folding and gluing operations consume around 1.5 million kWh of energy annually, either in the machines directly or in the supporting building. With the right design choices and use of automation, that energy consumption was slashed when a plant-wide automation upgrade project was completed.
"We were already able to lower our electricity consumption by 10%," stated Stephan Porthoff-Wenner, managing director at the time the project finished. "Gas consumption also has been significantly reduced.
Some of the reduction came from redesigning the compressed air system (Figure 2). Instead of opting for a single, large secondary unit, the company went with five smaller screw compressors, making it easier to scale the compressed air supply up or down in response to a changing load and demand. Wenner enabled the compressors to exchange data with one another and the rest of the plant, so the system knows which compressors are under load and can therefore supply heat, converting what would otherwise be waste into something useful.
The systems that make such energy savings possible for both individual machines and whole plant floors require the right measurement capabilities. This combination is achievable with PC technology and EtherCAT I/O terminals, notes Beckhoff's Wadowick. "It's possible to save money without an enormous initial investment by using measurement technologies that are integrated with the overall control system," he says.
Examples of this can be seen in a Beckhoff EtherCAT terminal that offers high-frequency time-stamping. Temporal precision can make the operation of a standard solenoid valve faster and more accurate. As for energy savings, the solenoid can be opened quickly and then maintain this position with very little energy, if solenoid parameters are properly tuned, Wadowick says.
When it comes to tuning the machine as a whole and optimizing its design, it's important to make decisions based on data that's as complete and accurate as possible. To that end, Beckhoff Automation offers monitoring terminals for three-phase power, enabling machine builders and manufacturers to determine possible areas for improvement.
The speed and control of EtherCAT figured into energy-saving design decisions made at W. Müller in Troisdorf, Germany. The company makes extrusion retrofit control systems that enable older machines to be adapted to new uses, while boosting productivity. The manufacturing process involves heating, cooling and plastic extrusion.
In discussing a completed company product upgrade, James Birt, controls expert with Müller, reported that the trend in the industry is to move to all-electric machines. Doing so results in more energy efficiency because servomotors are thriftier than pneumatics when it comes to power consumption. They also offer the possibility of energy recovery.
Reuse Energy by Design
The recovery of what would otherwise be waste is another way in which design choices can impact energy consumption. Arnold Mueller, director of service for factory automation at Bosch Rexroth, notes that this process begins with the choice of electrics to drive motion.
"Let's say you have a servo system, anywhere from four to eight axes or more," Mueller says. "Put that on a common power supply. So when we have modes in our systems where one motor is accelerating, and another motor is decelerating, I don't need to take any more energy off the mains. I can use the energy within our dc bus system."
Variations of this approach can help even when the load speeding up can't consume all of the power generated by a load slowing down. Traditionally, the excess heat generated by braking would be dissipated across resistors, increasing the cooling load. With the right design, that energy can be regenerated and potentially placed back onto the bus and even the grid, thereby reducing overall power consumption.
More efficient servo and other types of electric motors on the market can be combined with technology that monitors the load on those motors. That can then allow them to go into hibernation or sleep, saving even more energy, Mueller says.
Brenton Engineering, Alexandria, Minn., used such strategies in its Mach-2 (Figure 3) series of side-loading case-packing machines. According to Mike Grinager, vice president of technology, the design of a new machine took out pneumatics and more than 200 moving parts, cutting air usage to nothing and energy consumption by an estimated 25%. The machine makes use of Rexroth integrated servomotor/drives and associated motion control logic, with communication via SERCOS.
More Efficient Use of Technology
Of course, it's possible to design in more efficiency by using new technology. A case in point comes from drive maker SEW-Eurodrive's new Movigear technology. This can achieve more than 90% total efficiency, depending on operating conditions. Tests by customers and independent third parties on the use of the new technology have shown that it can lead to energy savings of 20-75% as compared to traditional induction gear motors, says Chris Doyle of the company' product support group.
It's possible to substantially slash final energy consumption by taking care during the design of a machine or automation solution, says Frank Langro, director of marketing and product management at Festo. The company is a subsidiary of the global automation firm that supplies pneumatic and electromechanical solutions.
For instance, doing a task analysis and then correctly sizing the bore of a pneumatic cylinder can pay off. "Just going down one bore size in a cylinder—from a 40-mm bore to a 32-mm bore—and performing the same type of motion, you can get roughly 30% savings on energy cost," Langro says.
He adds that the available software uses empirical and theoretical data to account for friction and other losses, thereby ensuring accuracy if parameters are correctly specified. That makes getting the size right—and potentially going smaller—easier to do.
Other energy savings involve the spot use of a pressure booster, which could allow use of lower pressure for most of the system. More savings are possible if piston retraction is done via a spring, rather than through the use of compressed air. Also, designing in sensors that look at absolute and differential pressure of the air supply can improve overall machine operation and energy efficiency.
Correct design of drives and components was listed as one of the most cost-effective ways to save energy in pneumatic systems, according to a 2012 report by Energy Efficiency in Production in the Drive and Handling Technology Field, EnEffAH, funded in part by the German Federal Ministry of Economics and Technology. For electromechanical drives, the key areas to attack in design of machines are mass and friction. The report stated that both should be minimized, with this listed as the most cost-effective approach to saving energy.
Another good bang-for-the-buck area is the movement profile, according to the report. That implies that the design be such that the motion trajectory is sufficiently adaptable to handle needed adjustments. Another potential benefit of a more capable motion system is the elimination of vibration, which the report rates as being one of the most important areas to consider after the top-tier issues.
The technology achieves this, Doyle says, through the use of permanent magnet motors and an efficient helical gearbox. It has a self-powered dynamic braking system instead of inefficient mechanical brakes. Still more energy savings are possible by mounting an electronic drive on the motor and removing the cooling fan.
Energy efficiency was a primary goal in the design of the motor. That focus can extend beyond the motor and into the design of the supporting machinery. "Electronics allows the output power to closely match the required motor power, instead of turning the motor on at full speed and wasting energy," Doyle adds. "Smaller permanent magnet motors also require significantly less energy and can do the same job as induction motors in many applications."
If it's not possible to design in new technology, the next best thing is to make better use of what's there. An example of this can be seen at AcmaVolpak, a Bologna, Italy-based maker of high-performance horizontal flow pack machines. These machines can package a range of products measuring from 1.30 cm to more than 100 cm in length.
According to Giuseppe Marcante, commercial director, in its SP2 NG line the company "created a machine that uses up to 30% less energy compared to traditional machines and delivers a noticeable reduction in energy consumption per produced unit."
Schneider Electric provided the automation for the product, with its PacDrive technology forming the basis for the machine. This technology combines a PLC, motion control and IT in one hardware platform. An integrated IEC 61131-3-compliant program generates all machine functions and is capable of synchronizing as many as 10 to 15 servo axes simultaneously.
FIGURE 3: Electric drives recover energy in Breton Engineering’s case packers.
Most of the AcmaVolpak machine's energy savings arise from design changes to the conveyor belt, which uses vacuum suction to hold product in place. Relatively energy-intensive, the vacuum pump had to be sized, by default, for the worst-case conditions. Running it at that rate all the time was inefficient in most situations. So the new design implemented a frequency converter to enable control of the pump power level. Regulating the vacuum pump resulted in as much as a 20% energy savings, or two-thirds of the total initial savings.
Making the most of any technology can demand intimate knowledge of a process and operations. Consequently, designing solutions to address energy consumption often can cross the line between machine maker and operator. Rockwell Automation's Kaufman recalls a customer that left equipment running overnight in order to get 16 additional units out a day. However, the cost in electricity and natural gas was significant, making those extra units expensive indeed.
Clearly, energy reduction can be achieved by designing in process-specific power savings. The challenge is that any adjustment to operating parameters can't be done in such a way that human mistakes can upset the equation. For example, in another instance, Rockwell worked with a customer to figure out ways to reduce energy consumption by, among other things, manually idling equipment when the last shift of the day was done. With no investment, the customer achieved substantial energy and cost savings.
A year later a follow-up visit showed that all of those changes had vanished. Likewise, the benefits and savings were gone—all because of a choice made by the end customer. "They didn't embed it into the automation and make it part of the fabric," Kaufman says. "They left it up to the employees. One day an employee forgot to do something. He forgot to plug the equipment in. The next morning they came in and couldn't manufacture right away. They decided manufacturing was everything." He adds, "We told them flat out, the only way to make this stick was to put it in to your automation. But that was an investment."
Looking Ahead
In the future, achieving energy-efficiency is likely to be more important, but just who will have to spend the money to do so remains to be determined. Reid Hunt, product line manager at high-efficiency motor maker Kollmorgen (www.kollmorgen.com), notes that most machines are specified in terms of having to yield a certain number of units per hour or some other equivalent measure of productivity. Today, only a few operators analyze machine efficiency and make that part of the purchase criteria, he says.
Upping efficiency might currently come about only as an indirect consequence of design choices that target productivity. "Avoiding downtime and decreasing waste is the major gain; energy consumption is secondary," Hunt says.
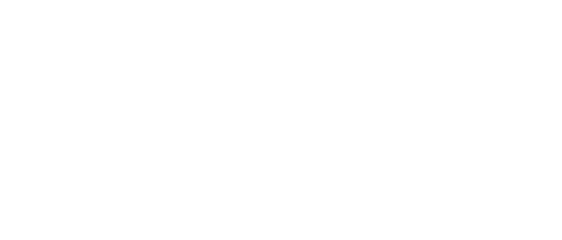
Leaders relevant to this article: