We've always used servomotors to translate rotary motion to linear motion via slides, ball screws and other mechanical components. A necessary upgrade for better reliability and versatility is at hand, and contrary to a lot of market conversation, a more direct pneumatic solution looks promising because of its integration with electronics, manifolds and other controls.
Most of our customers have compressed air systems. But there are equally promising integrated linear motor packages that might save space and be an almost plug-and-play upgrade that our customers might accept. So far, there doesn't look like there's a big cost differential in either case. We'll get an upgrade either way, but is there a prevailing opinion about best bang for the buck here?
—From November '13 Control Design
Answers
Upgrades Usually Electric
Assuming the desired process can be done with either electric or pneumatic solutions with the required repeatability/accuracy and flexibility requirements for future needs, and that any difference in floor space is not a concern, then the remaining considerations would likely be environment, life expectancy, operating noise, air contamination (such as the pneumatics lubrication) and, perhaps most important, energy utilization.
If the environment is a typical inside manufacturing environment with little chance of contamination, your most important considerations between the two technologies are life expectancy of the bearings for the electric solution versus the seals for the pneumatics, and the overall energy utilization to accomplish the job.
The life expectancy of both bearings and seals should be available from the component manufacturer based on some baseline design loading criteria, which you may adjust for each specific application for an even better comparison. If total energy utilization becomes too unrealistic to estimate without actual measurements, it might be easier to estimate the percentage savings of one technology over the other by taking the product of all efficiencies of one technology (say electric) over the other (pneumatic) or vice versa. The total product of the pneumatic efficiencies should include that of the air compressor (even if supplied by the factory independent of the machine), as well as all the other applicable efficiencies in the chain.
It has been my experience that the typical technology change/upgrade has been from pneumatic actuators to electric actuators, not the other way around. But without further knowledge of the specific process or job to be performed and the experience of the machine designer, it is impossible to make a judgment call. Each technology has its niche and, in the end, it is all about risk management of the specific technologies available and their interface with each other with the highest priority given to the process or work to be performed that will generate the best and most energy-efficient machine.
As the environmental and monetary cost of power rise, the designer's goal will be to select the best actuator-drive/control-feedback system for the application with the advantages and disadvantages of all technologies to be used. The potential user savings in power utility payments alone justifies a deeper analysis of each axis for the best design.
Hurley Gill,
senior systems/application engineer
Kollmorgen
Initial Cost or Operating Cost
The primary cost trade-off when considering an electric solution vs. a pneumatic solution is initial cost vs. operating cost. The initial cost of an electric solution will be higher, but its operating cost will be considerably lower, and it could provide more flexibility and higher throughput. Flexibility is realized in quicker changeover times when running different product, and higher throughput can be realized due to high level of control (position and force) that is inherent in electromechanical actuation. If you have been building your "rotary to linear" solutions yourself, you might be able to save space by selecting an electromechanical actuator specifically designed for compactness and power density. These actuators can be configured for stroke length and a host of options to allow it to easily interface with your machine. Of course, there is no substitute for a real cost estimate. In applications that we've worked with users on, we have found that electromechanical solutions save hundreds of dollars on operating costs and can often result in a payback of less than a year on the higher initial hardware costs.
James Marek,
business unit director,
Thomson Linear Systems
Precision Matters
I am not entirely certain of what the reader's "direct pneumatic solution" is, which he only briefly mentions. But if this is a servo-pneumatic control system, that would be the "best bang for the buck" here if the load in the application is large/heavy and relatively (on par with a pneumatic cylinder) high speeds are required, but where the application can tolerate precision that might be on the order of 0.1 to 0.01-in. (depends on the load, speed, tuning, overall length, etc.).
However, if extreme precision, repeatability, flexibility, scalability and reliability are most important, then an integrated linear motor package might be the best solution, since the integrated motor can provide precision down to 0.001 in. or even better, depending on all the applicable variables of the application, and offers optimum positioning flexibility.
But it is important to note that the integrated motor will not provide the thrust and speed performance per bore size of the equivalent pneumatic solution.
Gil Guajardo,
product marketing manager,
Bimba Manufacturing
Simple or Complex?
Selecting a positioning technology amongst electromechanical means (ball screws, lead screws, belt drives), linear motors or pneumatic actuators is typically done by looking at the positioning requirements first. Looking at parameters such as position accuracy, whether or not there's a need to control velocity or acceleration, and whether or not the positioning is variable are the first steps in deciding which technology is best-suited.
For single-positioning applications where high-level control of the velocity and acceleration are not required, pneumatic technology is usually your most cost-effective solution. If the positioning requirements become more complex, then electromechanical and linear motors start to become more appropriate. From a cost perspective, it typically graduates from belt drive, ball screw, lead screw and then to linear motors. Typically, the precision in the actual manufacture of the devices is driving the costs.
Frank Langro,
director — marketing/product management,
Festo
Don't Overlook Feedback and Control
The choice of pneumatic versus linear motors should take into account the inherent differences between the two to see if certain characteristics can work to your advantage. Air has an inherent "give" to it, which can be a real advantage in absorbing shock loads, while linear motors may be better if very tight positioning is required. Both types of systems have fewer wear components than rotary-to-linear conversion systems — the advantage will depend on the particular application — with pneumatics likely the best solution for systems experiencing high cycles with high loads. In either case, make certain that the proper feedback devices are used, and the motion controller is fully capable of doing the type of motion control needed, including tools to allow quickly optimizing axis tuning.
Steve Nylund,
CEO,
Delta Computer Systems
Better Performance With Electronics
Actuators and linear transmission components are used more frequently in applications that require clean operation, such as in the food, beverage, packaging and medical electronics manufacturing industries. Linear actuators are an important product group in factory automation, divided into two main lines: fluid-power actuators that operate on differential pressure (hydraulic and pneumatic) and electromechanical actuators driven by an electric motor. The machine builders' decision to use electromechanical solutions or fluid-powered solutions is based heavily on increasing productivity by improving accuracy, reducing the operating costs of the machine by improving energy efficiency and the cleanliness and noise level of the machine.
Pneumatics is one of the most-important technologies to move machines. Pneumatic-driven actuators have been engaged mainly in applications moving fairly light loads back and forth between two positions. In this case, position control is not so critical, other than at the end positions. In these applications, pneumatic actuators typically offer a combination of low initial cost and high speed, which makes them an ideal choice for simple motion applications.
If more than two positions are needed, or synchronization is required, machine builders more and more move to electromechanical solutions. Leakage is another challenge with air-driven systems. Air systems tend to have leaks that increase operational costs because the air compressor is constantly running to produce air that is being wasted. Losses due to air leaks add to the operating costs of pneumatic systems.
Although pneumatic solutions have the advantage of being able to hold constant pressure without having to apply additional amounts of energy, repeatability is critical to many applications. Due to the fact that pneumatic cylinders are always switching on and off throughout a factory running off the same compressor, it could be more difficult for pneumatic actuators to provide the slow, controlled speeds that are needed in certain applications. Electromechanical actuators are faster and more predictable and result in higher product quality. Also, noise reduction in the workplace is a factor in deciding what technology to use on different applications. Electromechanical systems have significant advantages in this area since they are much quieter than air systems.
Electromechanical systems can offer a better alternative from an economical and energy-consumption standpoint, since air-driven systems are afflicted with more inefficiencies. Machines are becoming more sophisticated, accurate and safe, and increasingly require better control of position, velocity or force throughout the range of motion. In addition, economies mandate saving energy and protecting the climate by using energy in a more efficient way. Improved accuracy and control can be accomplished with pneumatics using regulators and valves, but this considerably raises the cost and complexity of the system.
Abdulilah Alzayyat,
product manager,
Bosch Rexroth
Pneumatic Advantages
When high performance (high speed and high accuracy) is required, then generally electric servo drives have performance advantages, but that comes at a much higher cost than pneumatics. In the majority of positioning applications, accuracy within 1 mm is sufficient. That is where pneumatics have sufficient performance at a much lower cost. In comparison, lower-cost electric drives (vs. high-end electric drives) can overheat in continuous-duty applications (causing premature failures), whereas pneumatic systems can operate at 100% duty without overheating.
Most pneumatic positioning systems control position by controlling directional flow. However, our electro-pneumatic positioning system (EPPS) uses our expertise in direct-acting proportional pressure regulators to control position and can be applied equally well to both piston rod and rodless pneumatic cylinders in a considerable range of bore sizes and stroke lengths. The EPPS uses standard, off-the-shelf components to reduce cost and improve availability. The positioning feedback is provided by a non-contact, Hall-effect sensor mounted externally to the cylinder, thus avoiding the need for an expensive gun-drilled piston rod and internal transducer. Simple analog control (0-10 Vdc and 4-20 mA standard) is applied to a closed-loop controller, with no G-code programming required. The cylinder position tracks the analog input.
Some applications might require a mix of pneumatics and electric. We offer ISO 15552-footprint pneumatic actuators, and our linear motion division offers electric actuators with the same footprint allowing interchangeability between pneumatic and electric solutions. In addition, the RTC rodless pneumatic cylinder offers the same interface as the electric modules from the linear motion division, allowing for a mix of pneumatic and electric axes.
Phil O'Neill,
product manager,
Rexroth Pneumatics
Advantage Swings to Electronics
As the total cost of ownership between pneumatic and electronic actuation converges, the trend will be increased adoption of electronic actuation technologies. The main motivators for this shift are increased performance, increased reliability and expanded capabilities that electronic position control (servo and stepper) actuation technologies bring to the market.
In past years, the acquisition costs of pneumatics have been significantly lower than their electronic equivalents. Customers would choose electronic actuation only in applications requiring the increased performance or capabilities provided by more expensive technologies. As more machine operators consider the sustainability of their operations, they also consider the total cost of ownership and the long-term cost of maintenance on their equipment. In this context, the value proposition shifts from a narrow look at acquisition costs to a more holistic view of the productivity of a machine. Coupled with the ever-decreasing costs of all things electronic, we see a future that has a much higher concentration of electronic actuation technologies vs. older technology pneumatic alternatives.
Mike Cromheecke,
marketing manager, Kinetix Motion Business
Rockwell Automation
We posted the problem to LinkedIn's Motion Control Fundamentals Group and received the following comments:
Likes Linear Servo Approach
Linear servos are a direct-drive system, drawing power on demand. Pneumatics have a compressor that would have to be charging the air lines. Costs would have to take into account any leaks across the system and maintenance keep up the air system. Seal friction might limit very small moves, so the application's resolution requirements would need to be reviewed. Also, if there's a leak in the system, would that cause drift or servo dither on the pneumatics? Linear servo motors commonly enable 5 to 10 µm resolution systems for high-speed applications (5-7 m/s), but finer resolutions (0.5, 0.2, 0.1 µm) are available (though with less top speed possible), and with 1 V peak-to-peak in which the drive can interpolate for applications needing both high speed and fine resolution. As these are direct-drive, dc servos, they're capable of very precise and repeatable motion and better than 90% efficiency.
Jonathan Hoagland,
senior applications engineer,
Parker Electromechanical
Compare Those Costs
You say the costs are the same, meaning up-front costs are equal? What about long-term running costs? Aren't air compressors very inefficient? Won't the electric bill go up? With fewer components, higher efficiency and nearly drop-in replacement, I'd go with linear motors.
Cameron Anderson,
automation and control system sales,
Aerotech
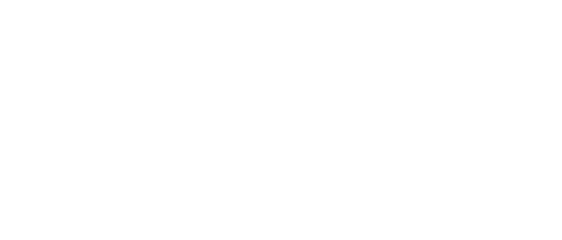
Leaders relevant to this article: