Machine Builder Includes Gantry Robots in Its Longest Wet Bench Cleaning Station
Tony Bertagnolli is chief operations officer at JST Manufacturing. Contact him at [email protected].
Figure 1: JST built a unique 138-ft-long wet bench silicon processing line that uses multiple overhead Cartesian robots to cycle silicon material through a series of chemical etch and rinse baths.
Figure 2: As the gantries move the baskets down the long x-axis, they also move them left and right (y-axis) where the baskets are lowered down into the chemical baths (z-axis).
Although silicon is the key ingredient for semiconductors used in smartphones and other electronic devices, only a purified form can be used to make semiconductor chips. Producing semiconductor-grade silicon involves upstream processing of polysilicon chunks to a purity of 11N, which translates to 99.999999999%. That’s a challenge that JST Manufacturing of Boise, Idaho, helps customers to meet by building advanced wet bench cleaning stations using linear motion and electric drive and control technology from Bosch Rexroth.
JST builds cleaning and processing equipment for cleanroom applications, from single wafer etching to automated wet process equipment. That includes wet bench cleaning stations of all sizes, but typically no more than 30 ft long. But recently for an overseas customer, we built a 138-ft-long line that employs multiple gantry robots (Figure 1). Handling the robot travel requirements for that distance took a combination of linear motion and control technologies with precision, robustness and cleanliness. The new system was developed solely as a custom solution for the overseas customer. The selling cycle took a long time. But, once it was sold, the project took about a year.
Purity Matters
JST’s wet bench cleaning station is deployed at the beginning of the silicon manufacturing process. At that stage, long cylindrical polysilicon rods, known as ingots, are broken into 1-to-3 in chunks — no bigger than a fist. The chunks are placed into special baskets that enter tanks of chemical etch in one station to remove silicon oxides and other contaminants. The chunks are then soaked, rinsed and dried. In a separate process, the chunks are melted in a furnace and transformed into pure monocrystalline silicon cylinders that are cooled, etched and eventually developed into computer chips.
For the front-end chunk-cleaning process, JST’s wet bench station was designed to process approximately 4 tons of silicon chunks in a 22-hr shift. To maintain that throughput, one basket holding 44 lb of silicon chunks has to be cleaned every 6.6 min.
That requires a unique wet bench cleaning station design. We engineered and built a station comprised of two units, the A1 and A2. In the 24-ft-long A2 unit, baskets of chunks are manually loaded through an auto-door. Then two-axis robots cycle the baskets through five acid etch baths and two rinse baths arranged in a single row down the length of the x-axis (Figure 2). As the baskets move down the x-axis, they are lowered into each chemical and rinse bath. (z-axis).
See Also: Robots Become Routine in Machine Designs
After completing the acid etch and rinse steps in the A2 unit, the baskets are transferred automatically through an airlock into the 88-ft-long A1 section of the line, which uses three-axis gantry robots to cycle the baskets through two x-axis rows containing soak and dry baths. At the end of the process, the empty baskets are automatically unloaded using customer-supplied conveyor belts.
What’s unusual is that the A1 unit employs overhead gantry, or Cartesian robots. Overhead Cartesian robots are not often used in semiconductor process systems to avoid generating particles over the product. However, after extensive particle testing in cleanroom conditions, we found that the Rexroth profiled linear guiderails and linear motion modules used in the system generated far fewer particles than the specifications allowed.
Throughout the process, protecting the components against contamination and pitting is critical. The Rexroth seals keep the linear motion rolling strips clean. And they keep the chemical etch from pitting the linear modules. Bosch Rexroth incorporated other features to ensure the system met Class 10 cleanroom standards or better. The motion system components use thin dense chrome plating for corrosion resistance. They were also lubricated with cleanroom grease.
Figure 3: Due to the length of the x-axis, the aluminum framing and profiled linear guide rails on which the gantries travel needed to fit precisely at the joints to guarantee smooth motion of the robots.
Linear Motion
In addition to using an overhead gantry design, the station’s length also posed unique challenges. JST usually builds semiconductor cleaning stations in 12- to 30-ft lengths. To handle the A1 length of 88 ft, each side of the x-axis on which the gantry robots travel is assembled from six 10-ft sections and three 9-ft sections of Rexroth profiled linear guide rails mounted on high-strength Rexroth extruded aluminum structural framing (Figure 3). Due to the length, the framing and profiled rails needed to fit precisely at the joints to ensure smooth motion of the robots.
Each gantry robot carriage is driven down the x-axis using dual synchronized ServoBelt linear motion modules from Goleta, California-based Bell-Everman, with one module on each side of the gantry. Unlike a conventional single-belt drive, each ServoBelt module is powered by a pair of toothed, steel-reinforced T5 polyurethane belts and a Bosch Rexroth IndraDyn MSK synchronous servo motor. The servo motor, which travels with the module as it rides on the profiled rail, turns an upper active belt that engages with a lower, permanently bonded static belt. Stiffness, accuracy and repeatability over this long span are greatly enhanced by the belt-driven design, which provides many of the same benefits as an electric linear motor but at a value comparable to conventional linear modules. The gantry robot-carriage belt design met our requirements. We did not need the speed of the linear motor, and it is less complex.
Figure 4: To ensure accuracy and repeatability over the span of the x-axis, JST used servo drives to synchronize the motion of the ServoBelt modules via a master-slave configuration.
We never considered anything else because we wanted the repeatability. To ensure accuracy and repeatability, Rexroth IndraDrive C digital intelligent servo drives synchronize the motion of the ServoBelt modules via a master-slave configuration (Figure 4). We get smooth and precise travel over the long x-axis length. The synchronization between the two modules is very accurate. As the chunks move through the wet bench cleaning station, control and timing sequences are performed by a third-party PLC control platform.
To move the baskets laterally from one bath to the other as the robot carriages travel down the rails, the gantries incorporate other Rexroth linear motion technology. For the y-axis, each gantry uses a Rexroth CKR belt-driven linear module powered by another Rexroth IndraDyn MSK servo motor. The CKR module has a 48-in stroke as the baskets travel over two rows of soak and dry tanks.
To raise and lower the baskets with the polysilicon chunks into the soak and dry baths, the gantry robots on the A1 unit utilize Rexroth CKK ball screw linear modules. These provide the vertical z-axis movement with a 32-in stroke to lower and raise the assembly that dips the baskets into each bath. Each arm terminates in a J-hook end effector that fits a pair of slots in each basket.
The ball screws have to withstand a certain amount of torque. The Rexroth linear actuators proved to be more reliable and robust than ball screws from other suppliers. Acceleration is smooth and rapid over the z-axis as baskets are lifted from the baths.
The A2 unit uses the same type of dual ServoBelt linear modules to move the gantry carriage assemblies down the x-axis, traveling approximately 20 ft. Unlike the A1 unit, no lateral y-axis motion is required because there is only a single row of baths. To raise and lower the baskets into the etch and rinse baths, the z-axis motion is provided by another set of CKK ball screw actuators.
The biggest benefit of this system was the experience we acquired. And it met the customer’s quality and throughput requirements.
Figure 5: The seed rods that grow the polysilicon ingots are mounted in specially designed cylindrical carriages which revolve inside each etch bath.
Seed Rods
In a separate application for the same customer, JST also created a stand-alone system to clean the “seed rods” that grow the polysilicon ingots from which chunks are made (Figure 5). The seed rods are mounted in specially designed cylindrical carriages, which revolve inside each etch bath. As with the A1 and A2 systems, the seed rod cleaning tool also utilizes a gantry robot to move the ingot-carrying cylindrical carriages through a sequence of etch baths.
For this tool, two Rexroth MKR linear modules mounted on either side of the row of baths are used to move the cylindrical carriage down the x-axis from start to finish. Each MKR linear modules consists of a 23.5-ft-long ball rail and toothed belt drive powered by a Rexroth IndraDyn MSK servo motor with multi-turn absolute feedback.
To raise and lower the cylindrical carriages into each bath, a Rexroth CKK module with side-mount servo motor was utilized, while a rotary end effector on the carriage carrousel spins the rods in the tanks.
For these and other projects, JST works with automation partner, Northwest Motion of Issaquah, Washington, a distributor of Rexroth drive and control products. In this case, the electric drives, rails, and linear modules for the three units were provided via single Rexroth EasyHandling System part numbers to ensure all components worked together as an integrated gantry robot solution.
We really appreciated how the Rexroth components for each station could all be ordered as single part numbers. We had to start building 10 weeks after the design approvals, so this helped us meet our production schedule. When marrying this many sections together, the fit and form of the rails and splicing kits have to be precise to eliminate hangups.
Tony Bertagnolli is chief operations officer at JST Manufacturing. Contact him at [email protected].
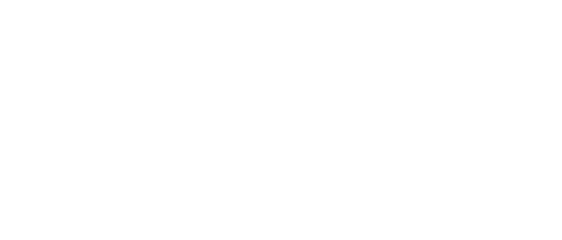
Leaders relevant to this article: