CTR Control Engineer Chu Hoang has been able to leverage the PLC, HMI and drives as a matched package to deliver the required precision and durability.
PLC: ABB AC500 family — PM554-T, PM564-R and PM573-ETH
• Administers the control system code CTR develops for the refill station, providing instructions to the drive that runs the motor and pump
• Constantly runs analog inputs for pressure sensors, pressure transducers and pump speed control
• Will shut the pump down if something falls out of temperature range, a seal leaks, the pump starts to cavitate or some other warning is triggered
• Regulates the cylinder fill to the desired parameters, whether it be to a specified pressure, temperature or weight. The PLC ports pick up any combination of the desired parameters and shut the filling operation off when the specifications are met, filling cylinders to the exact weight each time (Figure 5).
Variable Speed Drive: ABB ACS355 and ABB ACS550 Models
• Controls the speed of the pump/motor so that it isn’t damaged and the cylinders aren’t filled too fast, preventing them from overheating
• Regulates the pump speed and flow to make the operation more smoothly and efficient, feeding the cylinders at a rate where they do not need to stop and start and not filling them so fast that they exceed safe pressure and temperature requirements
HMI: ABB CP450 and ABB CP600 family models
• Enables easy and complete entry of cylinder-fill parameters
• Features an interface to print documentation of how the cylinders were filled — critical for audits by outside agencies and to verify that cylinders are filled properly.
Figure 1: The auto-adjusted pump speed is based on the pressure change on the pump discharge line or the temperature change on the cylinders fill. If the cylinder temperature increases, the pump will slow down. This panel can be fully controlled by the ACE system via Modbus TCP/IP.
Gases with value for their chemical properties are becoming increasingly prevalent in a wide range of industrial and medical applications. The most common of these gases are familiar ones, such as argon, nitrogen, helium, oxygen, carbon dioxide and hydrogen.
On the industrial side, the gases are used in a diverse group of applications that include metal fabrication, construction, computer chip manufacturing and food/beverage processing, shipping and service. Medical gases are used in hospitals, private practices, nursing homes, EMT services and home healthcare.
The molecular structure of these gases, in most cases, changes based on temperature and pressure; ranging from very low temperature, often cryogenic or liquids, to gaseous compositions at significantly higher pressures.
Providers of these gases, such as Airgas, Praxair and Linde, store, transport and distribute these molecules in various forms, often as a liquid in larger volumes to high-use customer sites, or in smaller cylinders as a gas, filled at stations at one of these providers’ many local facilities, for lower- volume users.
See Also: Energy-Saving Mechanicals for Machine Automation
At CTR, headquartered in Rock Hill, South Carolina, we build and repair sophisticated cryogenic equipment for these providers, designing systems for the safe and efficient distribution of industrial and medical gases. Started in 1993, CTR has grown with the industry, expanding on a foundation of cryogenic semi-trailer and bulk tank service and repair.
New Tanks and Retrofit Upgrades
Over the past 20 years, CTR has developed a unique expertise in building and upgrading the gas refill stations that are prominent in the landscape at provider yards across the United States. Refill stations provide bulk storage for gases to be pumped into the smaller cylinders for distribution to customers at job sites, manufacturing plants and medical care facilities. The stations are comprised of three primary components: a bulk storage tank, a vaporizer and a pump.
With the proliferated use of chemical gases, refill stations have become integral to the supply chain, providing local distribution to the high volume of users who consume gas at levels below what is feasible for bulk storage at their own facilities.
CTR has developed automated control systems that ensure gas is transferred efficiently and reliably and that ensure the refill station components are protected from the rigors of constant use (Figure 1).
The liquid in a bulk tank is pumped into a high-pressure vaporizer and brought up to pressure to be fed into the cylinders (Figure 2).
The pumping operation raises the pressure of the liquid from around 100 psi to approximately 6,000 psi as it’s pumped into the cylinders. The liquid warms down significantly during the process.
The design of such systems is complicated because the controls can differ based on the type of gas that is being transferred. Industrial gases may need certain types of control, while medical gases, with more specific regulations, require slightly different methods of control.
Collaborative Systems
“The first upgraded control system we designed was to transfer gases used in the metal fabrication applications, says Jim Payne, CTR vice president of operations. “But we saw the opportunity was there to build similar systems for other gases. Using our initial design and programming, we have been able to conform the system to work for a variety of gases, with the common electrical control components being the PLC and the drive.”
CTR had worked with State Electric Supply in the past and sought its counsel in designing the control system and identifying the most effective components for the automated refill station template. State Electric is an electrical distributor with locations in six states, including one in Troutman, North Carolina, which serves CTR.
Figure 2: The liquid in a bulk tank is pumped into a high-pressure vaporizer and brought up to pressure to be fed into the cylinders.
“We looked at the full scope of what CTR intended to achieve with the refill control systems and knew we had to come up with robust components that could meet the varying requirements of different gases,” says Jan Bernardini, the State Electric account manager assigned to CTR.
“Our team suggested an ABB PLC and an ABB variable speed drive because of their adaptability and because of the outstanding ABB technical support,” explains Bernardini. “We know that, if we have a problem, we can get a quick answer through the hotline and, if needed, we get on-site technical support anywhere in the country. “
Prior to CTR developing the automated refill systems, most existing stations were operated manually, with the decisions on fill pressure and capacity made by a human operator. The fill verification documentation was completed manually, as well.
Operator Control
Figure 3: The ACE system safeguards against possible underfill, as well as overfill, by providing PLC-HMI control. The system provides a complete fill cycle for each single product with no required operator manual adjustment once a product fill is selected.
A new ABB human-machine interface (HMI) has been added as a third control component on recent systems, providing entry of varying fill parameters and an interface to a system that prints post-fill verification documents (Figure 3).
“The most important benefit of the controls is that they make the whole fill process run more smoothly, and they stop, immediately, the fill process, if any abnormalities occur,” says Payne. “This is especially important with the high volume many of these stations experience throughout a typical day. The controls also help extend the life of the pump and help meet FDA purity regulations, which are critical for all medical gases.”
Figure 4: Several hundred of these systems have been installed over the past three years on completely new tanks and controls, as well as retrofit controls for existing tanks.
Centrifugal pumps are used to transfer liquid gas from tank to tank. Reciprocation pumps are used to escalate the gas pressure to fill the individual cylinders. Both pump types feature the ABB controls.
In addition to the control components, an ABB Ethernet TCP and ABB Modbus RTU are used to network between the PLC, drive and HMI, and often with the customer ERP system.
“The use of the Ethernet TCP and Modbus RTU enable the CTR systems to be flexible and powerful, providing robust and efficient connectivity among the system components, and, in certain systems, also with the customer ERP system, at very competitive costs,” says Randall Sorrells, drives and PLC application engineer at ABB/Baldor.
Figure 5: The PLC ports pick up any combination of the desired parameters and shut the filling operation off when the specifications are met, filling cylinders to the exact weight each time.
Several hundred of these systems have been installed over the past three years on completely new tanks and controls, as well as retrofit controls for existing tanks (Figure 4). The systems are built and programmed in Rock Hill and shipped to the site, where a CTR technician is dispatched for final installation and setup.
“The controls are basically standard components; then ABB helps us to modify them to fit the needs of a station for a particular gas,” says Payne. “Both ABB and State Electric have been very supportive in helping us understand what we need to use for our specific applications.”
State Electric keeps a good supply of local inventory of the controls for immediate delivery of the specified components.
Bill Jones is national sales manager at CTR. Contact him at 702/755-8960 or [email protected].
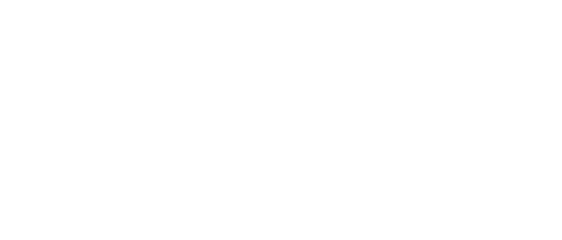
Leaders relevant to this article: