In 2016, during the commissioning phase of new extrusion line packages at a low-density polyethylene (LDPE) revamping project in Russia, a challenging problem developed—extruder motors winding temperature measurement (Figure 1).
Figure 1: A challenging problem developed during the commissioning phase of Russian extrusion line packages at an LDPE project.
Each extrusion package’s motor had six built-in winding temperature sensors installed inside; three of them were connected to a variable-speed drive (VSD) panel and distributed control system (DCS)/emergency shutdown (ESD) panels, and the other three were spare. The main aim of these sensors is to protect motors form overheating, and a relevant logic was implemented. When temperature reaches high-high (HH) level, a respective interlock in DCS/ESD is activated, triggering motor trip. Subsequently, the whole extrusion system also stops, and, later on, the whole plant has to be stopped (Figure 2).
Figure 2: Each extrusion package’s motor had six in-built winding temperature sensors installed inside; three of them were connected to a variable-speed drive (VSD) panel and distributed control system (DCS)/emergency shutdown (ESD) panels, and the other three were spare.
The system included an ABB 1,350 kW, 3.3 kV, three-phase motor; a PT100 temperature sensor; and a WIKA passive, 4-20 mA temperature transmitter, which was later replaced by an Endress+Hauser transmitter.
At the very last stage of the commissioning phase, several tests of the extrusion line were done. All test runs have been successfully performed without any load—knives were not connected to die plate. However, during the next step, which is the test with a fully loaded drive, the motor was suddenly stopped by PSD trip within 20 minutes after start.
Everyone had strong suspicions there were some problems in the logic implementation; however, thanks to available trend and alarm logs, it was quickly discovered that the reason was a high level of winding temperature signals registered by controllers (160 °C). Further investigation revealed that the real temperature was quite normal and 160 °C is just a substitution value, which the controller generates in case of signal over-range. Therefore, the primary task was to understand what leads to this over-range.
Step 1: VSD panel modifications
First of all, an alarm log in the VSD panel was carefully checked. Unfortunately, there were a lot of alarms, and it was virtually impossible to figure out possible causes. After a short consultation with the manufacturer, some specific parameters in the VSD, such as switching frequency and time delays, were adjusted, but during the following test start the same problem occurred.
Based on previous experience of having some problems with electronic control cards inside VSD panels, it was decided to examine the voltage level in the 24 Vdc power supply. This experiment showed that the voltage drops down to 14-15 Vdc within 10-15 minutes after the motor starts. Additionally, following DCS and ESD log analysis, demonstrated that this problem happens only when motor operates in a certain range of speed: 300–400 rpm.
Further detailed studies of the internal VSD log of events and electrical schemes showed that a possible reason could be a failure of the internal electronic board in the VSD, which provides temperature transmitters with the power supply. Moreover, stability of the similar bearing temperature signals of the same motor, which was energized directly from the DCS cabinet, also supported this idea.
Therefore, it was decided to provide the winding temperature transmitters with the power supply directly from the separate reliable power-supply unit installed in the VSD.
However, all of these modifications weren’t successful and, following test start, showed that the problem still remains.
Step 2: Elimination of installation omissions
At the same time, all details related to cable installations and connections were thoroughly scrutinized. As a result, several deviations from design solutions were discovered.
Cable between the junction box installed on the motor cover and the intermediate junction box was without individual screens, only with overall screen.
Cable shields were earthed in several points in the close distance near the motor, whereas in the VSD panel they were isolated. These deviations were eliminated—wrong cable was replaced, and all shields and spare cores were connected to each other inside junction boxes, isolated at field side and connected to instrument earth inside the VSD panel. Additionally, at this stage the very resistance of all PT100 sensors was checked, as well as shield isolation of control cables inside the motor.
Nevertheless, these actions didn’t help to solve the problem, and the temperature signals still were off scale when the motor was in the 300–400 rpm range. It was decided to identify the possible source of problem by splitting all possible reasons into two separate areas. Obviously, there were two sections where disturbances might have affected the chain:
- from the PT100 sensor to the transmitter
- from the transmitter to the VSD panel.
Considering all previous tests results, it was hypothesized that most likely the problem was in the first part of the circuit—from the sensor to the transmitter (Figure 3).
Figure 3: It was hypothesized that most likely the problem was in the first part of the circuit—from the sensor to the transmitter
Step 3: Experiment with a different PT100 sensor
In order to verify this supposition, it was decided to disconnect the internal PT100 sensor and connect another similar sensor from the warehouse to the same circuit, putting it externally, just near the motor cover.
Keeping in mind that the motor has six built-in sensors—three for use and three for spare—another built-in PT100 sensor was connected to the second circuit in order to exclude the very malfunction of the originally used PT100 sensor from the pool of possible reasons.
This experiment demonstrated that the signal from the external PT100 sensor was very stable, while all other signals had the same problem. Therefore, it was concluded that the assumption was right and the source of the problem was localized in a certain section of the circuit (Figure 4).
Figure 4: The experiment demonstrated that the signal from the external PT100 sensor was very stable, while all other signals had the same problem.
Step 4: Electromagnetic disturbance suppression
Based on all existing information, it was decided to try to reject the electromagnetic noises in the resistance-temperature-detector (RTD) measurement circuit. Two different technical solutions were tested simultaneously in different circuits:
- ferrite rings installation
- resistor-capacitor (RC) filters installation (Figure 5).
Figure 5: Two different technical solutions were tested simultaneously in different circuits.
However, the experiment showed that these measures only mitigate the frequency of signal over-ranges and do not provide complete noise elimination; therefore, they weren’t acceptable.
Step 5: Transmitter
Finally, it was decided to adjust the damping-time parameter in the transmitter for one circuit and completely replace the transmitter for another circuit. Modification of the dumping time was useless, whereas another type of transmitter demonstrated very stable operation. Apparently, the problem was caused by the transmitter and, in order to confirm this, all three transmitters were replaced. The following test start demonstrated the validity of this assumption, and that is how the root cause of the problem was finally identified (Figure 6).
Figure 6: The problem was caused by the transmitter and, in order to confirm this, all three transmitters were replaced.
Conclusion
Sometimes it’s difficult to identify the problems in temperature measurements, especially for winding temperature of powerful motors. In this case, it took eight days to find out the reason and unravel the problem.
Obviously, the main issue was the very installation of the built-in PT100 sensors and cables inside the motor. This led to severe electromagnetic disturbances in the RTD measuring circuits in a certain range of motor speed and, consequently, the inability of transmitters to operate normally.
ALSO READ: Sensing Technology Advancement Trends
Moreover, this problem highlighted another issue—the electronic card in the VSD panel wasn’t able to provide sufficient current to transmitters when all three of them were in over-range mode. This card was classified as broken and replaced on a warranty basis later.
In this case, the technical solution was to replace the temperature transmitter with a similar one, but from another vendor. Apparently, these two types of transmitters have a different design of input circuits—RC filters, amplifiers, digital filters. Finally, despite all difficulties and relatively long delays, the challenge was successfully addressed and the production line was launched on time.
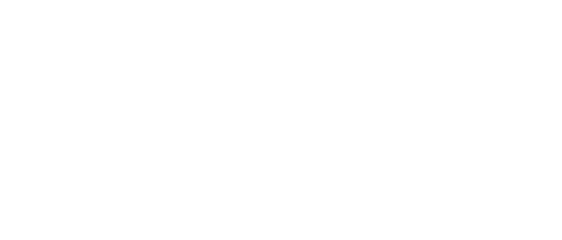
Leaders relevant to this article: