Figure 1: The Goglio GCap6 filling machine is ergonomic, noiseless, safe and modular, making it easy to install, update operate, maintain and clean.
(Source: Goglio)
At the inaugural Rockwell Automation Best Future Machine awards, announced at interpack 2017 in Düsseldorf, Germany, Goglio of Milan, Italy, won top honors in the Smart Machines category with its GCap6 filling machine for aluminum capsules. The judges were impressed with the machine’s remote-access capabilities and its use of Rockwell Automation’s Connected Enterprise technologies. Goglio’s smart machine showcased technology-related safety, integration, information, real-time diagnostic, operating efficiency and data tracking.
The awards were created to recognize and reward the high levels of innovation in the packaging industry. Additional categories included Modular Machines, Sustainability, Traceability & Product Safety and Ease of Use. The Goglio filling machine rated well in all categories (Figure 1).
Italy’s Cama Group won the Ease of Use category, as well as the overall Best Future Machine Award for its IF318 Robotised Monoblock Loading Unit, which incorporates cabinet-free technology and ergonomics and uses the iTrak intelligent track system from Rockwell Automation.
Years of being smart
Goglio is synonymous with quality, competence and commitment in packaging. The Italian company has gone through the entire history of packaging. In 1850, the first company of the group, specializing in paper bags, was founded; in 1909, the first mechanized factory was born; in the 1960s, the Fres-Co System was designed to integrate flexible packages with packaging machines and technical service; in the ’70s, new facilities were built in Daverio, Italy, to manufacture flexible packaging material, in Milan, Italy, to manufacture plastic for valves and in Zeccone, Italy, to build machines. The Goglio Group invented the one-way degassing valve, still an important component in coffee applications, as well as in other packaging processes. After a period of expansion in the 1980s, Fres-Co System International in the Netherlands, Fres-Co System Espana and Fres-Co System USA were opened. In the ’90s, the Goglio Group consolidated its presence in Europe with Goglio North Europe located in the Netherlands. New branches in the United States, Poland, Italy, Japan, France, China and Brazil were opened at the beginning of the 21st century and in 2016 the company entered the capsules market.
Today, Goglio designs, builds and delivers complete solutions for the coffee industry. This includes packaging film material, degassing valves, packaging machines, capsules and capsule-filling machines, as well as 24/7 technical assistance and service.
Smart coffee
Figure 2: The Goglio's machine fills aluminum coffee capsules and is suitable for filling tea, infusion and instant-drink capsules as well.
(Source: Goglio)
A good example of Goglio's deep knowledge in coffee is the GCap6, a filling machine for aluminum capsules. In addition to coffee, this automatic line for capsule filling and packing is also suitable for use with tea, infusion and instant drinks (Figure 2).
The GCap6 filling machine includes several modules: a loading system for stacked capsules, a twin-auger filling system, a checkweigher, a tamping and cleaning device, a top lid cut and seal group, an optical camera control and an exit pick-and-place. The capsules are fed to the conveyor through a singulating device and a carousel. A pick-and-place system takes six capsules at a time from the carousel and releases them on the indexing conveyor that transports them to the different stations.
Figure 3: Over a dozen axes of servo motion controls the various modules on the machine, such as this cut-and-seal group.
(Source: Goglio)
In a typical application, the machine fills capsules with ground coffee, which is fed directly from the grinder and pan-feeder. The spinning blender above the twin augers keeps the density of the coffee constant. The weight of each capsule is then checked, and feedback is sent to the augers. The indexing conveyor moves the capsules under the tamping device that presses the coffee with a vertical motion and cleans the upper flange to remove any coffee that could get stuck between it and the top lid with a rotating motion.
The capsules are then brought to the cut and seal group where another vertical movement cuts a circle of aluminum and places it on the upper flange of the capsules in the conveyor (Figure 3). A second part of the group then seals them. A 180° rotating pick-and-place device grabs the capsules that are lifted from the conveyor by a pneumatic cylinder and placed on a tilt device. The capsules are then released on the exit conveyor with the larger flange facing the belt.
Smart control
Figure 4: Servo drives include dual-axis modules with a single-cable connection between each axis and servo, saving space and integration time.
(Source: Goglio)
Goglio designed the automation system of the GCap6 selecting several Rockwell Automation solutions. Rockwell is one of our main suppliers and works with us on a daily basis in the development of new products. It is one of the most important brands and provides a wide-assistance network worldwide, together with great technical support to the machine builders.
The control system on the GCap6 consists of an Allen-Bradley ControlLogix controller, an EtherNet/IP network and several Kinetix 5700 EtherNet/IP servo drives (Figure 4). All of the devices are connected through EtherNet/IP while a Stratix 2000 unmanaged switch allows easy connections within the control network.
The Kinetix drives control over a dozen axes including the rotating table for insertion of stacked capsules, the pick-and-place system inserting the capsules in the conveyor and the indexing movement of it, the augers, the checkweigher lifting movement, the tamping device, the cut-and-seal device, the exit pick-and-place and the reel unwinding. Additional Kinetix ac servo motors are used for the pan feeder blender, the twin auger blender, the cleaning brush, the tamping heads and the exit conveyor.
Coordination of each motor is essential on the filling machine. The use of servo motors allows each function to be fully synchronized and coordinated in an electronic cam and enables noiseless operation. All motorized functions are linked to an electronic cam with a virtual axis within the machine, which runs from 0° to 360° during each machine cycle. Using this solution, the optimal synchronization is maintained, with automation compensation as machine speed varies, improving overall machine performance.
Servo motion provides an automatic speed adaptation among the different functions and guarantees constant timing of each feature, whether a simple or complex motion function. One of the most critical motion-control functions is the top-lid piercing and sealing station because it is a one-step process in a single station. Therefore, the requirements of time and synchronization are very demanding. Any errors can lead to poor cycle time and wasted material.
A motorized unwinder enables use of up to 500 mm reels on the machine instead of the standard 300 mm, which reduces the time and manpower needed to change reels. In addition, the machine’s simplicity and ergonomic design provide easy operator access for maintenance.
Smart integration
Thanks to the Rockwell Automation single-cable motion system, Goglio can minimize wiring to the Kinetix 5700 servo drives. These drives also use dual-axis modules to help reduce the space needed in the electrical cabinets. Even in the complex filling application, this is a simple motion system to integrate as its use reduces the amount of cable installed for each motor by 50%. The dual-axis modules are almost the same size as a typical single-axis drive, reducing the panel space needed by about 50%, as well.
Furthermore, the user-friendly software programming environment made machine development easier. The machine is designed to be configurable to specific application needs, using the PanelView Plus 7 operator interface, while still working in complete synchronicity. Our programmers developed and optimized this software to include different process combinations, and each function is separately accessible for instant customization and machine operation (Figure 5).
Figure 5: An operator interface enables quick configuration and control of machine operation.
(Source: Goglio)
The machine is remotely accessible via Ethernet and can communicate with both a customer's MES and/or with the Goglio developed cloud platform. Production data, including recipes, batch number and quantity to be produced, can be remotely sent to the machine. The design allows a customer to collect all analog and digital data from the machine and then use that data to implement analytic and predictive maintenance applications.
A separate PC allows operators to manage data and information to produce alarm and production reports and display any needed manuals, catalogues and diagrams. The PC also includes the tools needed to manage maintenance and camera visualization.
This Goglio smart filler machine achieved other advantages including reduced training times, improved machine flexibility, better troubleshooting of operational problems and easier testing and validation; it also helped to minimize installation and startup times.
Not only does this smart machine provide high performance and 94-95% overall equipment efficiency (OEE), it looks good, as well. The machine offers very good sealing, cutting and dosing accuracy in addition to precise defect checks. A combination of the machine’s applied design, feedback to load cells, photo eyes and cameras help to detect the presence and quality of capsule components. In addition, the servo technology allows the machine to efficiently achieve high availability, speed and quality.
ALSO READ: Is machine learning smart enough to help industry?
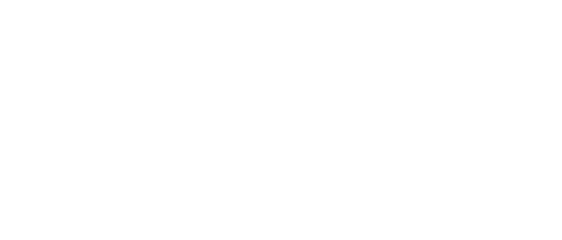
Leaders relevant to this article: