Motion control has evolved into a blend of hardware and software, which is integrated into the controller configuration. From the perspective of an OEM, parameterization allows the engineering of motion-control functions, as well as the startup of a machine, to become more efficient. Startup times can be reduced by up to 80% as only application parameters are set. Even complex motion functions such as interpolating axes, overlaying motion profiles, or robotic movements can be realized with minimal programming and a strong focus on parameterization. A graphical user interface facilitates this process further.
Because of the standardized nature of software modules, the software design becomes more transparent and duplication efforts are minimized. The OEM can offer scalable solutions that are simpler to troubleshoot to its customer. Even nonprogrammers can make parameter changes with ease.
Rick Simer is motion control product manager at SEW-Eurodrive, well-versed in the evolution of motion control.
RICK SIMER
Motion Control Product Engineer
SEW-Eurodrive
Q: Motion control has become a blend of hardware and software. What has brought them together, and how does that integrate into a PLC configuration?
A: In recent years, we have seen a shift in the motion control market place. Many motion control suppliers have broadened their expertise: software and PLC-focused companies add motors and drives to their portfolio while motor and drive suppliers complement their products with software offerings. Many customers don’t look for product offerings, but rather look for complete solutions in the market. When offering blended hardware and software motion control solutions, all components need to integrate seamlessly and have to create value-add for the machine builder and ultimately the end user.
SEW-EURODRIVES’s MOVI-C modular automation system is such an example. It is a one-software, one-hardware automation platform that combines fully integrated drive components, control electronics and automation software from a single source. The key to the MOVI-C platform is that each of those components is designed to work together perfectly. In the past, engineers have ordered control electronics from one source, software from another, and drive components from yet another. Getting these building blocks all to work together is another story. The MOVI-C platform offers a complete automation solution without all the headaches of mismatched components and complexity.
Machine builders will appreciate the seamless integration and the availability of proven and value-adding software kits tailored to the customer’s application from conveying to robotic kinematics. Combining MOVI-C’s ease of use and MOVIKIT’s flexible pre-built modules is the most intuitive way to integrate state of the art drive technology into the machine. The idea behind this: by standardizing motion control functions, applications, and machine types, SEW-EURODRIVE can offer standardized software modules that focus on parameterization instead of programming.
The motion control system consisting of software and hardware components can be integrated into the upper-level PLC configuration in different ways.
SEW-EURODRIVE’s solutions are compatible with Ethernet IP, PROFINET, PROFIsafe, EtherCAT, and FSoE communication protocols.
The goal of MOVI-C is not to replace PLCs, but to make it easier to integrate motion control functions ranging from single-axis solutions to complex multi-axis applications and from open-loop asynchronous motors to closed-loop synchronous servo motors. Using either a pre-defined fieldbus architecture or a standardized process data structure of the software modules is key when integrating into an upper-level PLC configuration.
Q: How do motion-control software modules differ from PLC coding?
A: Instead of the programmer coding the motion control logic, application parameters are set and the software module executes the logic of the motion control task at hand.
Motion-control software modules, such as MOVIKITs, are preconfigured software modules, similar to complex function blocks, and are used for solving simple drive functions such as speed control and positioning, up to complex motion control functions, such as camming or robot control. The software modules are operated on the real-time operating system of the MOVI-C Controller or on the MOVIDRIVE application inverter.
The programmer then ties in the MOVIKIT module with its different functionalities into the overall PLC program using the pre-defined fieldbus interface or process data structure. The MOVIKIT takes care of the motion functions and is the interface to the drives and motors. As a result, the PLC program becomes more streamlined, reduces its cycle time, and works with standardized software modules.
The MOVIKIT software modules are ideally coordinated with the control technology of the MOVI-C Controllers. The corresponding MOVIKIT software modules are directly assigned to an axis or the controller and configured using graphical wizards and editors. In this way, you have access to all the relevant parameters in a parameterization interface, from the motor startup through to the software settings. You can integrate MOVIKIT into the IEC user program at the click of a button, using the automatic IEC code generation function. You can control the software modules from the IEC user program thanks to a standardized, intuitive interface. Every MOVIKIT software module possesses both a conventional variable interface and also an object-oriented interface for implementing modern software architectures (Figure 1).
The process data monitor and RobotMonitor offer looks into the motion.
The process data monitor shown gives an overview of the process data interface “Process Data IN and OUT” of the drive and the PLC in the MOVISUITE engineering software. The user can simulate the PLC and manipulate the Process Data IN or observe both IN and OUT parameters with the PLC in RUN mode.
Q: What types of problem applications are you seeing that are benefiting from software modules?
A: MOVIKIT software modules are applicable to a wide variety of applications: from single-axis movements to multi-axis applications.
Linear and rotary positioning, speed control, two-speed infeed/outfeed movements, electronic camming, and even oscillation-reduction for the cyclical movement of liquids are application fields that can be simplified using the respective MOVIKIT.
On a more complex level, there are software modules for specific machine modules such as different robotics kinematics or Stacker Crane solutions. As an example, the MOVIKIT StackerCrane can be used for implementing all kinds of storage/retrieval systems with up to four travel axes and four lifting axes. Up to 25% of energy can be saved by optimizing the travel cycles of lifting and travel drives. Other functions such as vibration dampening, anti-sway and electronic differentials are available, as well.
The process data monitor gives an overview of the process data interface “Process Data IN and OUT” of the drive and the PLC directly in the IEC project. The user can select different modes such as mechanically or energy optimized operation, jogging or others and observe the process data for all axes at the same time.
Q: Robotics have become a more common motion application. How do you foresee the future of robotics motion-control solutions?
A: Small and medium-sized machine builders will start to integrate robotic solutions into their machine design more and more with a strong focus on open architectures.
So far, we have discovered that small and medium-sized OEMs often struggle to implement robotic solutions. Sometimes, they lack internal robotics knowledge and have to rely on external programming and startup services. When these companies integrate turnkey robotic systems, they limit their own value-add capabilities as a result. Especially for handling applications, such as palletizing or transferring goods or processing tasks, such as plotting, applying glue, or decorating, there is a need in the market for open solutions.
With the MOVIKIT Robotics, SEW-EURODRIVE offers software module for controlling a robot. We enable OEMs to build internal robotics knowledge and work with more than 120 different kinematics, such as gantries, delta robots, or SCARAs.
The RobotMonitor, as a part of MOVIKIT Robotics, is the user interface and 3D simulation in one tool. Robot programs can be created without the need of strong programming skills, simply by focusing on parameterization and drag-and-drop menus.
The software seamlessly integrates with motion control hardware of SEW-EURODRIVE such as controllers, inverters, motors and gearboxes. To complement this approach, we offer the Parallel Arm Kinematics Kit, a modular drive and hardware solution that enables OEMs to build their own delta robot.
The RobotMonitor offers the user one integrated tool for the user interface, the 3D simulation of the robot’s movements, as well as the parameterization interface.
For more information, visit www.seweurodrive.com.
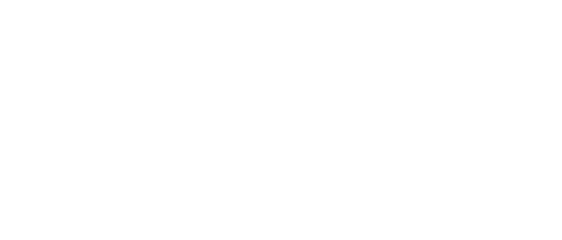
Leaders relevant to this article: