Thinking cabinet-free is nothing new. We’ve always been able to eliminate some parts from the cabinet and integrate them into the machine. Some examples of devices include sensors, switches, vision, safety and identification systems.
More powerful technologies with better IP ratings make components smaller, more intelligent and more mobile. Ethernet or wireless connectivity, along with standard protocols and safety functions, allows for all of these devices to be located directly on the machine.
The benefits of these new advancements can range from simply reducing wiring to providing significant cost savings across the complete manufacturing value chain. Identifying these benefits may reduce the total cost of ownership and could eliminate the need for a cabinet at all.
If you’re thinking of redesigning your machine or designing a new machine, motor-integrated automation technology and cabinet-free technology could be holistic approaches of interest.
Consumer behavior drives manufacturing
Increasing consumer demand for a customized product requires an increase in flexible production, more product variations, smaller lot sizes and even the ability to create a unique customer-specific product. Product manufacturers demand production equipment with flexibility, higher availability, lower inventory, minimal setup/change over time and easy support.
Manufacturers want maximum productivity and flexibility at minimum operating costs. To remain competitive, machine builders (OEMs) must provide innovative production solutions and integrate end-user demands for higher flexibility and complexity. Shorter engineering time, the ability to provide design verification, faster build and startup, reduced machine floor time and open connectivity are important aspects.
More prevalent use of electrical equipment in machinery requires innovative approaches to reduce the size of electrical enclosures. The result is smaller machine footprints, less engineering, and a reduced need for cooling and cabling.
Automation control, drive, I/O and sensor component suppliers strive to provide products with reliable communication based on open standards and increasingly higher integration for cabinet-free installation. The components that don’t require electrical enclosures can enable production equipment solutions.
Evolution of cabinet-free products
Cabinet-free technology has a proven usage in many areas of automation component equipment.
- Hydraulic and pneumatic valves and manifolds, pressure sensors and related components have proven to be reliable over the years, all installed in various areas within machinery.
- Many sensor types available for direct installation into the machine work reliably for many years in a wide range of environmental conditions. Latest advances in open communication, such as IO-Link, enable intelligent sensor design with minimal wiring efforts.
- Machine safety has improved greatly with the use of safety products installed into the machinery environment and conveniently connected with networks, beyond discrete wiring. Safety curtains, scanners and switches provide the reliability and safe operation in production equipment.
- Panel and mobile human-machine interfaces (HMIs) with better protection ratings are increasingly available for installation into the machine without requiring electrical enclosures. They are enabled by HMI software and multi-touch interfaces. The increasing use of mobile devices as machine HMI will further reduce enclosure needs.
- Frequency-converter drives mounted on ac induction motors used for conveyors, sorting systems and other applications reduce cabinet space.
- As servo drive use in machines continues to increase, removing the servo-drive units from the enclosure often represents the greatest possible reduction in enclosure size and cabling efforts. This is especially true, not only for low-voltage drives, but also for higher voltage/power servo drives.
Engineering savings
Machine builders already commonly integrate some components directly into the machine, reducing the need for them in the cabinet. Sensors and switches are used for monitoring, I/O banks and I/O bus technology to reduce wiring. And load encoders measure length/distance, as well as synchronize with packaging. Light curtains, laser scanners, sensors and door locks provide safety, with safe and non-safe I/O data sharing a channel on one Ethernet cable.
The challenge is building a machine that is completely cabinet-free, taking advantage of the benefits a machine redesign can provide to the machine builder and end user, and ultimately providing a better product for the consumer. How do you design a machine like this? The traditional way would be for each module to have its own cabinet for the axes it uses.
The cutting-edge, cabinet-free way would allow axes or modules to be added without the need to adapt the cabinet. This would allow the machine builder to design an entire machine based on modules, offer the complete machine based on modules, offer the complete machine or only individual modules. Then as the customer’s need changes, the machine builder has the flexibility to add additional modules.
Intelligent and efficient
Many cabinet-free products are intelligent with built-in functions for diagnostics, energy savings and configuration. In some cases, hybrid modules combine multiple technologies into one cabinet-free component. For the Internet of Things (IoT), products are IoT-ready, providing access to machine data and converting it to useful information, helping to improve overall equipment effectiveness (OEE).
To share this information, products have standards and open communication, including Ethernet communication protocols. In addition, many cabinet-free components meet the necessary IP rating for industrial environments.
Less electrical engineering
Fewer components and connection points directly save cost for creating electrical and cabling schematics. Successful fieldbus technology eliminates many discrete wire connections, or terminals, and possible points of failure. One in-machine component is often comprised of multiple conventional components that employ modern plug-and-play cabling and connections, reducing the overall cabling effort in the machine.
Reduction of the number of cables and cable length directly result in savings of the number of components inside the enclosure, volume of electrical schematics and installation instructions. Additionally, indirect savings in smaller conduits and cable tracks and the elimination of connection boxes can further help to justify cabinet-free product use.
Noise reduction
The removal of electric-noise-generating and electric-noise-sensitive components, such as electric drives and supplies, from the electrical enclosure reduces the engineering efforts for shielding, as well as component and wire placement. With motor-integrated drive technology, noise is further reduced by partially or even completely eliminating cabling with noisy pulse width modulation (PWM) through the electrical enclosure walls, which dramatically lowers shielding and routing efforts to achieve electrical noise compliance, such as CE marking. Pre-manufactured and tested cabling ensures minimal noise issues and speeds up installation and startup time.
Heat reduction inside the enclosure
Removing components with high-heat generation, such as drives and power supplies, from the enclosure provides the largest benefit. It vastly reduces or even eliminates upfront engineering needed to assess total power converted to heat, natural heat dissipation of the enclosure, cooling methods, condensation concerns and documentation. Cooling-unit installation and subsequent maintenance costs are saved. Finally, there is no longer any need to plan for the additional power consumption of cooling units.
Overall, removing heat sources from the electrical enclosures by converting to cabinet-free technology results in savings during the machine operation and life, reducing manufactured product costs. This helps to achieve reduction goals for power consumption (CO2) of the manufactured product.
Shorter machine-build cycle
Cabinet-free components typically reduce the machine-build cycle because the components are accessible on the machine and require a minimum of connection points. Fewer components, cabling and connections save assembly and troubleshooting time. The results are shorter delivery times, reduced machine build time and a shorter time for testing, as well.
Available products combine many electrical components into one cabinet-free device, making them easier to mount on the machine. The combination of products, such as those with motor-integrated drive technology, is becoming smaller and more powerful. These products have many built-in functions that go beyond just a frequency drive and motor or stepper motor.
Now, the combination can be a servo drive on a servo motor with the space required almost equal to only the motor itself and no need for drive space in the cabinet.
Reduced cost and better logistics
Without a cabinet, the electrical designer no longer needs to define the many components and connection methods within the enclosure, which eliminates costly changes during the build or installation.
The machine builder can reduce logistics efforts by scheduling motor-integrated drive technology and other cabinet-free products directly for machine assembly and not for the enclosure builder. This reduces the risk of not receiving a complex enclosure in time for wiring and possibly delaying startup.
Machine footprint and shipping efforts
Traditional machines require increased space in the enclosure due to more commonly used electric drives. Choosing cabinet-free technology still includes the essential electrical components but instead incorporates stand-alone drives or motors with integrated drives. This reduces the size of the electric enclosure or the number of enclosures required.
The smaller/fewer the enclosures, the easier they are to attach to the machine body, reducing shipment size and volume. Additionally, cabinet-free products no longer need to be connected to the cabinet but can be linked from one component to another, resulting in up to a 90% reduction in cables. All of these factors result in a machine with a much smaller footprint and substantially lower weight, significantly reducing shipping costs.
Machine installation
Installation times in a production plant have traditionally been long and costly. Using cabinet-free products contributes to more modular machine design, requiring reduced wiring and fewer connection points. Fewer components and connections mean faster assembly, less wiring, easier testing and validation and fewer errors. These benefits can result in significant material and labor savings and a competitive advantage to achieve the start of production goal.
Usually, products designed for direct installation into the machine consist of one or very few components, which saves engineering time and installation effort. Placement of cabinet-free components within the machine still requires the assessment of product ratings vs. environment and access for possible replacement, but it reduces overall assembly time.
Footprint and production
With the development of cabinet-free technology, production lines can be expanded with the smallest possible footprints. Thanks to modular integration, end users can operate more machines within the same factory space and have more flexibility with adjustments to existing production equipment. At the production facility, a savings can be achieved with material-handling equipment and conveyors, where shorter distances result from more compact machinery footprints.
Fewer components and connection points of cabinet-free solutions can mean less complexity to troubleshoot. Network connectivity offers more diagnostics to identify the problem. The limited number of connections and components result in less machine downtime, primarily because there is less to troubleshoot while the machine is out of production. This speeds up decision time to replace a component and consequently reduces machine downtime.
Cabinet-free technology provides diagnostics that hone in on the nature and location of the problem. Thanks to closed-loop redundant communication, pinpointing a problem with an axis can be quick. Because cabinet-free machine design makes the axis easily accessible, replacing it requires removing two connectors and mounting screws, replacing the axis and getting it back into production as quickly as possible.
Using Ethernet or wireless communication with standard protocols offers more diagnostics and functionality, which can prepare for IoT connectivity and increase machine availability. Additional savings result from stocking fewer components, reduced maintenance and parts-replacement time, simplified procurement of machine parts and reduced shipping and tracking costs.
Functionally safe
Integration of machine safety is also available with cabinet-free products. Drive-integrated safety brings more flexible operation/setup to the manufacturing floor by allowing safe machine operation while reducing the electromechanical footprint and components of machines. Furthermore, it simplifies troubleshooting and wiring as safety-relevant signals can be transferred via automation buses.
Many integrated products are available with safe torque off (STO). Safe motion functions, such as safe operational stop under power, safe limited speed or safe direction can reduce setup and recovery times and increase productivity. Safety-state information can be accessed via the network to monitor the safety devices in the plant. Using components outside of the cabinet does not limit the safety functionalities on the machine.
Data integration
To integrate cabinet-free products into a company’s IT system, the system must have direct access to power supply, drive and motor parameter values. This is possible using interface technology that allows direct access to products using high-level languages. Information can be accessed via smart phones and tablets to parameterize or to view the product diagnostics and status, enabling the user to monitor production from anywhere.
Using data analysis, processes can be adjusted to improve production and identify quality issues in the end product. The information collected can provide accurate data about the OEE of the plant floor, improving the company’s output.
Also read: On-machine vs. in-cabinet for automation components
Control Design Newsletters
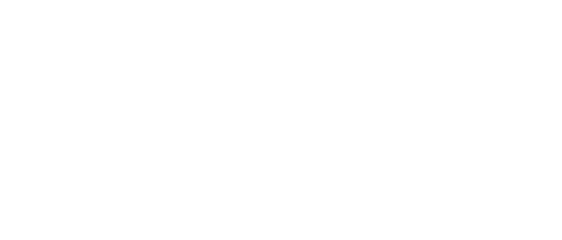
Leaders relevant to this article: