We build most of our custom, one-off control cabinets in-house. We've had success using vortex coolers to control the enclosure temperatures when we have heat issues. Now we're getting into markets that place our systems in hazardous environments. What's the experience with adding purging capabilities to vortex coolers? Are we better off with conventional gas-purge systems or another approach? We need an effective, but still cost-responsible solution.
—from July '14 Control Design
Answers
A Common Solution
This is a very common solution for us. Most of the time customers prefer to use a purge system to protect their equipment over the use of an explosion-proof enclosure due to the large cost. The rating of the hazardous location that the enclosure is located in will determine which type of purge system you would need.
One concern customers have when adding a vortex cooler or AC unit to a purge system is over-pressurizing the enclosure. You just have to make sure that the vent used on the system can handle the combined air flow of the purge system and vortex cooler. Depending on your application, we have systems that can monitor the temperature inside of the enclosure, and turn the vortex cooler on or off depending on the temperature settings entered into our purge unit. So if you have an enclosure in a hazardous location, and it has a vortex cooler, then using a purge system is normally more cost-effective, and you get all of the extra benefits of the temperature monitoring and pressure compensation features.
Brent Dean,
Product Engineer,
Pepperl+Fuchs
[We received the following responses after posting the question on LinkedIn's Industrial Automation and Process Controls Network.]
Purge Will Have to Work Harder
Just use instrument air that is dry and filtered for the source of air for the vortex cooler. This would be the same source used for a purge system.
Also Read: Current Signal Conversion Experience
The purpose of the purge is to actually pressurize the enclosure to prevent the ingress of ignitable vapors. The vortex cooler will cause the purge to work harder, since it will have to make up pressure (just a few inches of water column) to compensate for the air that is constantly flowing through the enclosure via the vortex cooler. Contact your purge system vendor to ensure the purge has the capacity needed to offset the demand of the vortex cooler. If possible, use all Div 2/Zone 2-rated components if you're placing the enclosure in a Div 1/Zone 1 environment. This will permit you to use a less-expensive Y purge instead of an X purge.
Robert Burgman,
Principal Engineer,
Electrical, Instrumentation and Process controls,
Ashland,
Good Combination
Is this for purging systems such as standard atmosphere or concentrated atmosphere such as nitrogen? General positive pressure designs would strike me as a great vortex combo application as long as you're not pushing moist air in. Any other gas would seem questionable. An exact application would help me answer with specifics.
Theodore Sharpe,
Machining Group Supervisor,
Ford Motor
Maybe Move the Enclosure
If you're a one-off manufacturer of an enclosure, you will find it difficult to satisfy the regulatory bodies that the enclosure meets the required rating for use in hazardous zones. Simply adding a purge is not sufficient. You have to contain or limit energy. Allowing the internals of your cabinet to vent, and thus forcing any energy out of the cabinet into the hazardous zone, is not acceptable. If all of your components and equipment are in their own hazardous-zone-rated enclosures, and you add a purge of sorts, also rated for hazardous zones, then you stand a chance of your entire installation being suitable for the hazardous-zone installation. If not, then I suggest that you just keep your enclosure out of the hazardous zones. Work with the site to determine your non-hazardous areas. They should have classification drawings that can guide you to where they are.
Andrew McKeown,
Specialist Process Engineer,
Carter Holt Harvey
Purge Controller Handles Both
We recently provided modifications to an existing customer panel. From the beginning, the customer wanted both a vortex cooler and purge controller.
Once the final installation was completed, our mutual conclusion was the purge controller could provide both functions—cooling and safety purge for C1/D1 area.
Jim Robinson,
Control Systems Engineer,
M.G. Newell
[We received these responses after posting the question on LinkedIn's Automation Engineers Group.]
Purge + Vortex Pepperl+Fuchs (Bebco) makes purge systems that can work in combination with vortex coolers. We use them at my shop, and it is a good product.
Noel Jull,
I&C designer,
IDT Systems
Vortex Gulps Air
Vortex coolers place quite a demand on an air system. I would use a purged enclosure per NFPA 496, and then use something like a Noren air-to-water heat exchanger approved for use with purged enclosures. This is how I've done it before.
Brian Rogers,
Senior Electrical Engineer,
Transfuels
Our multi-machine workstations haven't changed much beyond the sophistication of the HMI software and better tactile input methods. The operators now spend more time at the workstation and less time patrolling the machines with clipboards since we have much more operational data feedback at the HMI. We need an ergonomic "tune up" to make sure the operators are safely paying attention to the increased amount of operating data without being too comfortable to be attentive. Any experiences to share?
SEND US YOUR COMMENTS, SUGGESTIONS OR SOLUTIONS FOR THIS PROBLEM. We'll include it in the November '14 issue and post it at ControlDesign.com. Send visuals if you'd like—a sketch is fine. Email us at [email protected]. Please include your company, location and title in the response.
HAVE A PROBLEM YOU'D LIKE TO POSE to the readers? Send it along too.
Vortex Alone Works
I have no experience using a purge system in conjunction with a Vortec unit, but Vortec does make two units specifically for hazardous locations, the HazLoc Vortex A/C.
Here are links to the operating and safety instruction sheets: Operation and Safety Instructions Models 7515, 7525, 7535, 7215, 7225, 7235 and Models 7570, 7270, 7570BSP and 7270BSP. They have some useful information regarding sizing and using the two systems together.
Fred Manning,
Pneumatic Product Manager,
FCI Automation
They'll Work Independently
You can use the vortex cooler as part of purging systems, but you need to be aware of the fact that all the components that make up the purging system will operate independently from the vortex.
Also, you should use air where possible, since placing cooling or purge gases in contact with people could harm them.
Alejandro Varga Meder,
Project/Construction Management,
Devco USA
[We received this response after posting the question on LinkedIn's Automation.com Group.]
Vortex + Ex-n
On previous projects, per customer's requirement, we supplied IP65 stainless-steel panels with vortex coolers and Ex-n components.
This is not a cheap solution, but allows operating the cabinets with the doors open in any situation, including the presence of gas, not needing purging or de-powering.
George Eric Wootton,
E&A Solutions & Engineering Manager,
Wärtsilä Brasil
[We received the following response after posting the question on LinkedIn's Panel Building and System Integration Group.]
Go Ahead
If you're asking can you use both a vortex cooler and a purge system for your hazardous location requirement, the answer is yes. It's not an uncommon practice.
If your heat dissipation is too great, explosion-protected air conditioning units can be used effectively. If heat is a smaller concern, sometimes just using continuous purge (versus compensative) can assist. Hope that helps.
Craig Yoss,
Director of Marketing and Business Development,
R. Stahl
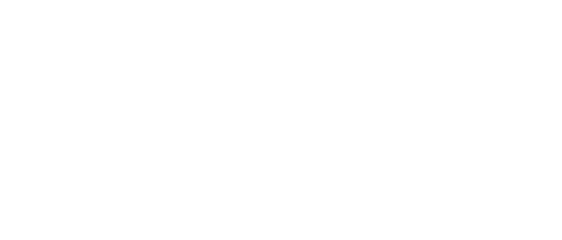
Leaders relevant to this article: