The worst case, of course, is if the cause of the defect isn't found onsite, but rather is discovered by a valued, and now quite upset, customer that has a product quality issue of its own as a result.
Phoenix Closures never wants to find itself in that boat. The company manufactures injection-molded closures primarily for the pharmaceutical and food industries in four facilities, including its company headquarters in Naperville, Ill. The company just recently opened a facility in Greencastle, Ind., to complement its other plants in Davenport, Iowa, and Newport, Tenn.
Phoenix produces some 3 million closures daily at each of the manufacturing sites. The process includes an assembly operation that automatically inserts a die-cut gasket, or liner — also manufactured by the company — inside the cap. The quality inconsistency of that operation led the company to improve its machine vision inspection approach.
Can't Fix What You Can't See
"Most of the quality issues are the improper insertion of the liner, such as being off-center or a cut liner, but issues also arise with the color of the liners," says Merle Smith, Phoenix Closures' senior projects engineer. "Then there can be molding imperfections in the cap, and shorts and mold flash on the caps." Smith says this operation runs at speeds upwards of 400 pieces per minute.
The company had several brands of vision systems in use for a few years, and Smith says there were always problems. "We realized we had to figure out what brand and type of vision solution would work the best for us and why," he says. "The downtime and rework from these undetected defects was simply too much. We had to improve the ability to stop the lines quickly as soon as a problem was recognized."
Who You Gonna Call?
Phoenix Closures conducted an extensive survey of many of the vision suppliers. "They came in, made presentations, and we later went to the vendors' facilities to do some hands-on trials of the systems they recommended," Smith says. "One of the most important things we wanted was ease-of-use. We needed to understand how difficult or easy was it going to be to train our operators and technicians."
Smith is also clear that cost was a factor for them, but dependable technical support was a very important factor in the company's choice. "We needed to know that if a problem came up that we couldn't handle, then the vendor or an experienced local integrator would provide fast support at all our locations," he says.
"We chose an Omron FZ3 color vision system because we saw that it could handle all of our applications," Smith says. "One of the things we're very pleased with is its backward compatibility. We've had one of their earlier F150 or 160 systems, and here we're now up to the color FZ series, but the tools are compatible with the F150. In addition, after we bought the FZ3 series, Omron brought out an FZ4 series that has some newer software tools we could use. All we had to do was upgrade the firmware that they provided us, and we basically had an FZ4 system."
Visible Improvements
"The cap liner insertion process is tied to an automatic diverter to separate the defects from the rest of the batch, so entire batches don't have to be quarantined and reinspected," Smith reports. "If we get an unexpected rise in the number of defects, the system automatically shuts down, so the operators can find and fix what's going on. In the past, we would have to reinspect an entire box or two, and that could be 3,000 caps in each box."
There still are a few machines in the company operating without a vision system, Smith says, and that has occasionally meant reinspection of entire production runs that would number in the millions of caps. "Reinspecting with the vision system means we get that done in a few days rather than the few months it would take to do it manually," he points out.
"We've also been able to use the system to verify and detect color problems in the plastic resin we buy to make caps," Smith adds. "The system can detect subtle color changes that we then verify by discovering that sometimes we're adding more of our own colorants than before. We can take that up with our resin or colorant suppliers."
Training and Operation
"The Omron technical staff do the initial technical training in a one-day session at our place," Smith explains. "That gets our technical people up to speed and then they can walk all the operators and others through it pretty easily."
They also can load in and store recipes in the system's HMI screen on the factory floor, Smith says. "Also, if we develop a new product here in Naperville where our centralized engineering group is located, we have an offline system that we can use to develop recipes and then send those to one of the other sites to use. It's a good way to keep consistency in our manufacturing methods."
There's really no maintenance or calibration required, other than keeping it clean, Smith notes.
"The hardware platform provided the scalability to fit the diversity of Phoenix's applications," adds Alex Nowak, Omron Commercial Engineer for Vision, Smart Sensors, Code Readers, RFID. "The ability to combine true color and grayscale inspection into a single process provides the solutions to a process with changing requirements. The selection of vision tools from circular inspection defects and color analysis strengthened their manufacturing process. The Omron vision controllers allowed simple connectivity to their Omron PLC control platform as well. The combination of inspection and control has helped define their quality process."
What's Next
Looking to the future, Smith says the speed of the vision system would readily handle any increases in production rates. The injection molding rates are the governing limits. "And there still are features in the system that we haven't yet used to their full capabilities," he adds. "Its data collection system eventually will help us with our process improvement, particularly to be more accurate on classifying and categorizing the defect problems."
The company has a project program in place to put this vision system on every liner machine it has, Smith says. "Every cap that we produce will be inspected by a vision system."
Phoenix Closures is also part of a growing trend to have its machine builders provide the vision system. "We've had our lining machine builders partner up with Omron so that now the vision systems and their infeed and outfeed conveyors come already integrated in any liner machine we buy."
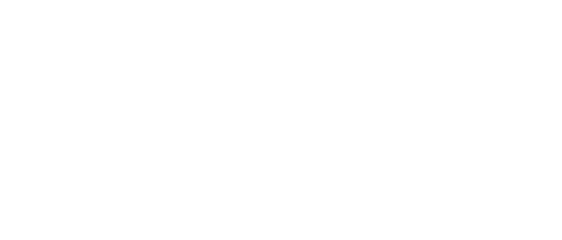
Leaders relevant to this article: