In 2012, Aaron Hand was managing editor of Control Design and Industrial Networking. He joined Putman Media after almost 20 years covering high-tech industries, including semiconductor, photovoltaics and related manufacturing technologies.
Although Plasma-Therm was organized in St. Petersburg, Fla., just three years ago as an acquisition from the Oerlikon Etch Strategic Business Unit, its original founding actually dates back to 1975 in New Jersey. After decades of developments in plasma etch technology, it was acquired in 2000 by Unaxis and later rebranded as Oerlikon before being reestablished in 2009 through a management buyout.
Working with a range of industries that includes MEMS, solid-state lighting, wireless, photomask, renewable energy, nanotech, photonics and data storage industries, the machine builder finds that automation needs differ considerably from market to market. "In some markets, the cost of the end product as it passes through our system is so high that loss due to operator error or handling-system error is significant enough to justify higher-end automation," says Joe Barraco, software engineer at Plasma-Therm. "Conversely, some markets that are primarily R&D do not necessarily have the capital to justify large-scale automation, so lower-cost systems with less automated controls are justified."
The amount of automation is driven not only by cost but also by the types of operations that occur in each industry, Barraco explains. "A photomask system might require full factory automation connection, so operators can simply load and unload material into and out of the system while a centralized host computer selects recipes, executes jobs and collects data as the material is being processed," he says. "However, some renewable-energy startups could be more interested in being able to dynamically switch between two sets of RF power supplies in order to serve parallel research efforts being performed by two teams on the same tool."
With cost as a key driver, however, automation can change with the economic cycles. Although companies might not have the resources to purchase new equipment during downturns, they could still justify improving automation to prolong equipment life or increase yield. "One Plasma-Therm customer experienced a product loss of several hundred thousand dollars when an operator accidentally ran the wrong recipes on some material," Barraco recounts. "This went unnoticed for weeks. The customer could easily justify the integration of a barcode scanning system and custom software solution to prevent that kind of loss from happening again."
In the LED and MEMS markets, some customers start so small that they have only enough capital to get manually loaded wafer systems, Barraco says. "Our Versaline product allows these customers to grow their systems along with their businesses," he says. "These systems can be initially configured as a single-wafer tool, and later converted to a full cassette-to-cassette multichamber system as the customer moves from initial development into full production."
The processes associated with these markets often have unique needs, such as the plasma-enhanced chemical vapor deposition (PECVD) systems that require automated cleaning of the process chambers. "The system periodically estimates the thickness of excess material that has built up in the reactor, and then automatically triggers a cleaning process when the process chamber is idle," Barraco explains.
MEMS production uses deep silicon etch (DSE) reactors to etch deep yet narrow features with very smooth sidewalls—requirements are typically in the tens-of-nanometers range. "Very fine control of the process is absolutely necessary to achieve these requirements," Barraco says. "Our control systems dynamically manage all of the parameters within the reactor, including pressure, reactor temperatures, gas mixtures, RF energy, electrode positioning, and process timing. In the MEMS market, timing is especially critical." Barraco says that a 250 ms variance in timing in a DSE process can mean the difference between a good final product and scrap.
In the industries that Plasma-Therm serves, there is never a shortage of automation challenges. "Yield means everything as our customers move into production," Barraco says, adding that beyond reducing process times, engineers strive to improve handling systems. "There are many techniques here, beyond the obvious 'faster robots.' One area where we've achieved significant improvements is in control algorithms that more efficiently schedule material movements. For example, our tools look ahead and pre-stage wafers to be loaded as soon as a process module is available."
Working in a vacuum environment also adds to the challenge. "Our systems have to handle delicate materials, so we have to depend heavily on optical and other remote sensors to minimize contact while maintaining process control," Barraco says.
Despite the seemingly complex technologies it works with, Plasma-Therm's software development philosophy is to keep it simple. "If it sounds too complex, it is," Barraco says. "Just because something was difficult to implement doesn't mean it should be difficult to use."
Along these lines, Plasma-Therm's engineers have learned that it's usually best to avoid proprietary systems. "We once used a proprietary embedded computer running VxWorks and outsourced development of the board support package (BSP)," Barraco recalls. "This proved to be very expensive, and when the supplier learned that it would be very costly for us to change hardware platforms, they raised their prices dramatically. On top of that, the custom-build kernel turned out to be buggy. At the time, Windows PCs didn't have the horsepower to meet our controls timing needs, but thanks to Moore's Law, it wasn't long before that changed. PCs now run unbelievably fast processors with large amounts of memory. Our timing concerns had been addressed, so we made the switch and now control most of our equipment with industrial PCs running Windows."
Although a PLC-based solution can be developed rapidly, the controls team has steered away from it for several reasons, not least of which is the tendency to be pushed into another proprietary framework. "In our experience, these systems are not very flexible or expandable," Barraco says. "You quickly run into hardware driver compatibility issues, poor user interfaces, and a proprietary hardware set. Our next-generation control system has been written from the ground up in Visual Studio .Net. We have taken the time to develop a reusable and extendable control system foundation with our end users in mind. We have intentionally designed a distributed hardware system; our industrial PC controlling computer running Windows 7 does not have any specialized hardware. All bus interfaces to and from the controlling computer are Ethernet. As the computer industry advances, we benefit without having to re-architect, or wait for a PLC vendor to incorporate the advances into its product."
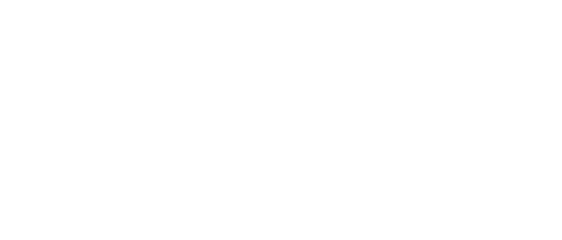
Leaders relevant to this article: