Come Glimpse Reality
I was dismayed to read Industrial Networking's series of articles by P. Hunter Vegas ("The Fieldbus Jungle," www.IndustrialNetworking.net/fieldbus11q1), where he aims to presumably expose the many pitfalls of Foundation fieldbus, Profibus, and a few other industrial networks. I work in a continuous process plant where all the regulatory control—every throttling control valve—is using Foundation fieldbus instrumentation and networks.
Our operators are not "buried" in alarms. Foundation fieldbus devices do not create alarms for operators by default ("every time an instrument thinks it detects a problem"); our operators are only alerted to device problems when they can have an impact on their operation. We are just emerging from a tough, cold winter and our plant manager credits the ability of fieldbus devices to alert us to potential freeze-ups as playing a significant role in keeping the plant running reliably and at near-record rates all winter.
Ironically, after falsely implying that FF devices will bury operators in alarms, in the very next paragraph Vegas says, "The failure rate of field instrumentation is very low." So while that statement is true, he continues, "Advanced diagnostics usually won't detect" failures like plugged impulse lines, fouling or network problems. Where has this man been? Every major supplier's FF DP cell offers plugged line detection. Mag meters and pH transmitters, among others, have diagnostics for fouling. There are several very effective online tools for continuous assessment of network health.
He casts aspersions about FF causing plant shutdowns, but says nothing of its real track record or how reliable it really is. Our plant has been making extensive use of control in the field for more than 10 years, and FF has never been the root cause of a process interruption. On the contrary, it goes a long way to keep us out of the ditch.
Having used fieldbus for more than a decade, we routinely replace or exchange devices from the whole period (three different ITK major revisions, from ITK3 through ITK5) without issue. I use diverse devices from numerous manufacturers, including five different Foundation fieldbus valve positioners, three different discrete valve positioners, four suppliers of pressure/DP transmitters, radar, ultrasonic flow, pH, conductivity—hundreds of devices from more than a dozen suppliers. Fieldbus works. Vegas should come out to Lima, Ohio, for a glimpse of reality.
John Rezabek, Process Control Specialist,
ISP Lima LLC, www.ispcorp.com
Chairman, Fieldbus Foundation End-User Advisory Council
Contributing editor, Control and Industrial Networking
A More Encouraging View
I was somewhat surprised with respect to the rather "dark" view of digital instrumentation and controls upgrades in the article. The author dwelled far too long on the peculiar pitfalls of digital upgrades while missing significant benefits regarding the digitalization of the process control industry. There are particular benefits that might not be as important to some areas of the process control industry, but are of particular and very important benefit to my specific area of I&C. My particular area of expertise is that of instrumentation and control systems for nuclear power plants.
To its credit, the article did identify a number of the problem areas Duke Energy/Oconee experienced with its first Foundation fieldbus-based installation. However, the second and third installations, as well as subsequent smaller additions to the FF system, have been very straightforward and implemented efficiently. Far too much focus was paid to the difficulties, and not enough encouraging or beneficial operating experiences were provided to mitigate the trepidation-based arguments that many uninformed people and organizations offer to endure their obsolete systems or undertake heroic maintenance of the status quo (analog and pneumatics) with respect to power industry process instrumentation and control systems.
The Oconee Major Projects Engineering organization implemented many digital upgrades at the Oconee Nuclear Station and the Keowee Hydroelectric Station between 2003 and 2009. Oconee Nuclear Station's three units began generating in 1973 and 1974. The I&C used is of that timeframe. Oconee today still has many pneumatic and analog I&C process loops, but Oconee is also one of the most digital nuclear power plants in the U.S. Digital systems are the future for power generation, whether an existing plant or a new one, and regardless of the fuel or energy source utilized. Duke Energy has implemented many digital upgrades within its nuclear fleet—most driven by obsolescence issues and a desire for improved performance, monitoring and reduced maintenance.
Michael H. Miller, PE, Oconee Nuclear Station,
Sargent & Lundy, www.sargentlundy.com
A Digital World
I think that the article on Foundation fieldbus misses the point, some key issues, and one unalterable truth. Everything is going digital in this world. Much of what we know of the world today, in spite of the complications, is better and provides value beyond initial cost. Ask any iPhone or BlackBerry user if they would give them up despite the huge upfront cost and the even larger ongoing data plan costs.
What I find almost trivial is the somewhat irrelevant discussion around initial costs. I really didn't need a lot of research to know that if I buy something that has an order of magnitude of choices, the engineering costs would go up. Our first fieldbus project cost us almost three times the cost per I/O of a traditional 4-20 mA loop in a DCS. Our second project cut that cost per I/O in half. I don't believe we will ever reach parity because there always will be more choices. We'll get better at using templates and configurators and software gizmos to automate things because now we can. But if the cost per I/O was the only issue, pneumatics were pretty cheap compared with a DCS project 20 years ago.
As an end user, I can tell you that one of our first reinstrumentation projects with fieldbus cost us about $30 million. On those units alone we have received about $10 million in direct benefits from fieldbus. Those numbers are very conservative because they consist of just the few ad hoc incidents we were able to capture. They come mostly from the prevention of production losses directly related to doing proactive maintenance on devices before they fail. The success stems from widely available onboard diagnostics. They are pre-prioritized based on the potential impact a failure has.
We've elevated and segregated the device alerts and alarms from the operator. In the new culture, the techs and engineers have their own consoles to monitor and report device health. Just this morning, one of our techs produced a report that found a few of our safety systems tested during a unit outage inadvertently had been left with the write-protection off. He knew which transmitter without climbing a single scaffold to check. It's their window into their equipment just as much as the process unit is to the operator.
Many people have heard of the Pony Express. Most people don't know that the Pony Express only existed for 18 months. They very quickly became obsolete as telegraph lines were strung across the plains. The hapless riders used the telegraph lines to guide them from town to town. I hope we're smarter than they were, or we too will become obsolete.
Rick Heiberg, Instrument and Process Control,
Shell Oil Company, www.shell.com
Don't Throw the Baby Out
I was really shocked at the half-truths and out-of-context statements that were published in the fieldbus article. Although there is a grain of truth in some of his statements, overall, his outlook on any fieldbus seemed to be, "Let's stick our head in the sand and stay in the dark ages."
Vegas also seems to insinuate that field technicians and installation personnel aren't smart enough to handle it. It is very obvious that he is not considering the total installed cost (especially where construction labor rates have a huge impact on project costs), and does not recognized the real value in live diagnostics.
Prior to my "retirement," I was chief control systems engineer for one of the world's largest engineering/construction companies. My company very likely designed and installed more Foundation fieldbus systems than anyone else in the world. I lived through the pain of the early years and have seen the vast improvements come about in the last few years. This is a good technology and, if applied intelligently, it can make a difference in cost, schedule and overall lifecycle savings.
Perhaps Vegas should do a little more homework in the real world before he throws the baby out with the bathwater.
David S. Lancaster, PE,
Certified Foundation Fieldbus Instructor
Examining the Facts
I believe there is value in examining both the benefits and the challenges of bus technology. Despite this, I found that there were a number of factual errors about Profibus and Foundation fieldbus.
Comparing the cost of Profibus-PA and 4-20 mA, the author uses the example of 5-10 valves or transmitters for non-IS. In my experience, most non-IS designs will use 15-20 valves and transmitters. This is the number stated in a book I co-authored,"Catching the Process Fieldbus," which was reviewed by Profibus experts from five different countries. By the article's argument, increasing the number of valves and transmitters would make Profibus more economical than 4-20 mA.
The author states that the lead time for fieldbus devices is longer than it is for 4-20 mA devices. This is not true for Siemens. The published lead time for the Profibus-PA, HART, FF and 4-20 mA options for Siemens instruments are the same. The hardware differences between these options are fairly small. It is true that the lead times on the PA and FF components are longer than they are for the HART and 4-20 mA components, but our purchasing department buffers this by having a supply on hand. Our customers never see the difference between communication options.
The author states that, when designing a network, you need to know within a few feet where devices are installed for a fieldbus network. This is not the case for Profibus-PA or Foundation fieldbus. The design rules as laid out in the IEC standard state a maximum limit on the spur lengths based on the number of instruments. For Profibus-PA, this limit is 30 m for about 20 instruments. For FF, most host systems will not let you have more than 16 instruments per segment, so you end up with a 60 m limit. When laying out a network, most sites I've been involved with had little trouble keeping well within the 30 m limit. A few sites had a few runs where they had to be careful.
The author says troubleshooting fieldbus networks is very hard. A number of diagnostic tools are available to troubleshoot fieldbus networks. Several manufacturers—Procentec, Softing, Pepperl+Fuchs, MTL Instruments—make them. The manufacturers' websites can provide customer testimonials on how easy it is to troubleshoot a network with their tools.
According to the author, fieldbus lifecycle costs are high because people do not understand the technology. Further, it is implied that it is hard to train instrumentation people. I have been a technical trainer at Siemens for more than 10 years and have seen things change. There is no doubt that 4-20 mA is easier to teach, but people of all ages are catching on to the new technology. Also, in my experience, young technicians typically find fieldbus easier to understand than 4-20 mA. They are so used to communications networks that having a 4-20 mA instrument you can't talk to seems strange to them.
The author states that the bus wars are over and that Profibus and FF are merging. It is true that FF and Profibus organizations are now cooperating. However, I am not aware of any move to a common control bus. Given the technical differences, I am not sure if this would even be possible.
The author states that GSD files change often. It is possible he is confusing GSD files and EDD files. EDD files define all the acyclic data used for configuration and diagnostics. GSD files define the cyclic data used for input/output. In the case of Siemens transmitters and actuators, GSD files do not tend to change, while EDD files tend to change with each firmware revision. What that means is that you can take an old instrument and replace it with a new one without touching the control system, although you will have to update the engineering station.
The new Profibus profile version 3.02 standard requires guaranteed backward compatibility with both the GSD and EDD files. This standard requires that the instrument auto-adapt to older revisions, making device replacements far easier. All new products are now being tested to this new profile standard.
In ending this letter with talking about the Profibus profile version 3.02, it highlights the importance of end user feedback. Fieldbuses have value and they also have problems. The only way for the standards to move forward is to acknowledge the problems and work toward resolution.
James Powell, P. Eng., product marketing,
Siemens Milltronics, www.sea.siemens.com
* "Catching the Process Fieldbus—An Introduction to Profibus for Process Automation," James Powell and Henry Vandelinde, SMPI Press 2009.
Security Cover Needs Correction
Nice article on security ("Don't Slip Up on Security," www.IndustrialNetworking.net/slip). I think you really capture the core ideas. However, there is an item that could use a correction. In the paragraph where I'm quoted, you also state, "Typically, a dual-homed PC, server or other device has two network interface cards (NICs), which can be located between two different networks, such as the untrusted Internet and a trusted corporate network, and so serve as a firewall and help provide more secure access."
I could not disagree more. Dual-homed PCs are security disasters! I ranted against dual-homed PCs in my blog (www.ControlDesign.com/dualhome). However, this paragraph makes it look like I think they are a good idea. They are not. I think a better wording might be: "Typically, a dual-homed PC, server or other device has two network interface cards (NICs), which can be located between two different networks. Many people think they can act like a firewall and help provide more secure access, but this is incorrect. Hackers typically see them as juicy targets for attack."
Eric Byres, P.Eng, chief technology officer,
Byres Security, www.tofinosecurity.com
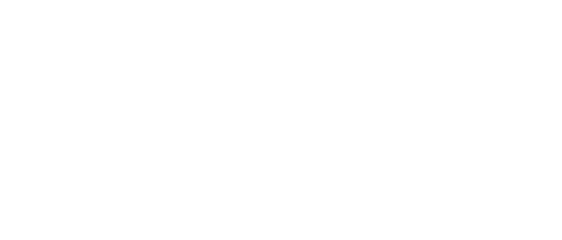
Leaders relevant to this article: