By Jim Montague, Executive Editor
Industrial motors are comparatively mature technologies. Most of their major innovations were introduced and refined decades ago, so motors seem to stand still while younger, quicker advances in drives, controls, networking, onboard intelligence and software seem to swirl around them.
However, it would be a mistake to think that motors aren't experiencing some significant evolutions as well. For instance, Tower Engineering (www.tei-usa.com) in Fort Worth, Texas, uses a specially designed RPM ac direct-drive cooling tower motor and VSI cooling tower drive from Baldor Electric (www.baldor.com) to replace right-angle gearboxes and other moving parts serving high-inertia fans in institutional HVAC systems (Figure 1). This motor combines the power-dense, laminated-frame RPM ac motor with a permanent-magnet, salient-pole rotor design.
"I always wanted to get rid of these gearboxes and all of the other moving parts," says Rod Applegate, Tower's owner and president. "Misalignment, excessive vibration and noise are all inherent problems with this system. With the high speeds, the gearboxes generate too much heat, and the seals and bearings can have very short lives. There are just too many things that can go wrong. Also, when gearboxes run at these high speeds, they generate a lot of heat, and that's lost energy. Based on the test data, we anticipate that the RPM ac direct-drive solution will be 13% more efficient than a conventional drive train. This is an important discussion to have in a time when everyone is concerned about reducing the amount of energy they consume."
Finer Refinements
Just as the recent advent of $4-per-gallon gasoline spurs hybrid and electric autos, other skyrocketing energy costs push users to finally invest in premium and ultra-efficient motors that many suppliers have offered for years. This demand also reinvigorates motor builders to use even better-quality materials and construction to gain a few more percentage points of efficiency. And, although better steel and copper certainly can reduce power losses, better designs and assembly methods help achieve even greater gains in efficiency.
"We always seek new materials to reduce power losses and increase flux in our motors," says Nick Johantgen, North American technical product manager at Oriental Motors USA (www.orientalmotor.com). "However, we also recently developed better assembly techniques for our rotor and stator laminations, which allow us to preserve more of the electrical isolation in our motors. As a result, we've released a stepper motor that can produce the same torque as our existing stepper, but with 50% less power. And, because our motor accomplishes these gains by reducing losses, it runs much cooler."
Magnetic Events
Besides improved winding and lamination methods, the biggest shift in motors has been the recent move to greater use of permanent magnets (PMs) and rare-earth magnets (REMs). These magnets help increase torque and efficiency, and typically allow motors to deliver more horsepower in a smaller package.
"All the drill-rig, traction, test-stand and other applications that use our motors of 1,000 hp and less always seek more motor density and torque in smaller packages," says Rich Schaefer, product manager for variable-speed and specialty motors for Baldor. "This means using more costly steel and copper to build motors, but it also means using REMs made from neodymium iron boron (NdFeB).
NdFeB technology has been available for many years and it's scalable, but it was more costly and produced in lower volumes, making it hard to justify its use in larger motors, Schaefer explains. "REMs only recently have been adapted for larger motors, machines, hybrid cars and computers, and these higher volumes fuel use in more diverse applications," he adds. "Now, in applications where induction motors would be too big, too heavy and completely ineffective, machine builders can use smaller, lighter PM motors. I think it helps to think of PM motors as large-scale servo motors."
PM technology advanced rapidly over the past 20 years with the use of ferrite and aluminum nickel cobalt (AlNiCo), samarium cobalt (SmCo) and NdFeB magnets, says Curt Wilson, engineering vice president at Delta Tau Systems (www.deltatau.com), noting that the advances seemed to plateau recently. "While possible supply issues for the last two rare-earth metals have been in the news lately, it's not clear whether this is just typical commodity volatility or something more serious," Wilson says. "In industrial positioning control, PM brushless motors have taken away the market almost completely from brush motors during the past 20 years, and now dominate in the power range from 0.2 hp to 10 hp. Below that, there's still a market for brush motors, and above it, induction motors under field-oriented control provide a good cost advantage."
Reduced hardware and software control costs enabled motor users to take advantage of brushless motor capabilities, including no brush wear and replacement, better heat dissipation, and higher power density, Wilson adds. "In designs of PM brushless motors, there's been more interest recently in interior PM (IPM) rotors over the traditional surface PM rotors," he explains. "IPM rotors bury their magnets inside the rotor, focusing the magnetic flux through rotor laminations to the stator. This condition creates varying magnetic reluctance around the rotor, and with the proper sophisticated control algorithms, this provides an extra torque-producing mechanism as the rotor ‘seeks' the minimum reluctance position with regard to the stator phases, in addition to the Lorenz torque from the permanent magnet fields interacting with the stator phases. Also, they permit more of a dynamic tradeoff between torque and speed—not as widely as an induction motor with field-oriented control, but much better than brushless motors with SPM rotors."
Although PM motors are similar to servos and other motion technologies, they have many unique requirements and design challenges, Schaefer notes. "Many software programs have grown to allow developers to design, test, build and apply PM motors, and they also help enhance and fine-tune designs, as well as to change models when needed," he explains. "On the controls side, designers also have to recognize that PM motors need different software to synchronize the drive with the motor, and prevent it from falling out of sync. The drive must know the position of the PM motor to correctly rotate its magnetic field, which enables the drive to control the motor's torque and speed. More software is being developed to better handle interior PM motors. One of the best methods to coordinate PM motors with drives is to use a preprogrammed parameter in the drive, so it knows the motor's parameters ahead of time."
New Rules
Most recently, the ongoing push toward greater motor efficiency was turbocharged by the U.S. Department of Energy's (DoE) implementation of the U.S. Energy Independence and Security Act of 2007 (EISA), part of which requires minimum efficiency for many common types of motors. The law went into effect in December 2010, and many motor manufacturers have been scrambling to bring their motors and related products into compliance. It covers general-purpose 1-500 hp motors, with 1-200 hp motors required to be premium or high-efficiency, depending on subtype, while all 201-500 hp motors are required to be high-efficiency.
"Every company that builds motors has reevaluated its products to make sure it meets these minimum efficiency requirements," says Tim Schumann, corporate engineer for SEW Eurodrive (www.seweurodrive.com). "For many, this meant further refining already-available technologies such as using higher-quality steel for laminations, more copper and windings and rotors, and sometimes even using diecast rotors. Also, while many manufacturers promote PM motors, others use switched-reluctance technology to give users the capabilities they need. However, there's only so much efficiency you can get out of motor hardware, and so we're also using panel-mounted drives and decentralized electronics to increase efficiency. DoE doesn't consider this a way to make motors more efficient, but they're looking at it and other factors contributing to efficiency losses in the future."
John Malinowski, Baldor's senior product manager for ac motors, mentions other considerations in relation to EISA. "Besides coming up with new winding and electrical designs, EISA's big challenge for everyone had been how to fit 15-20% longer laminations in the motors' stacks, as well as to achieve 40% greater lamination stamping capacity," he says. "We also see more motors being designed for niche applications, such as for food and beverage manufacturers that need motors they can wash down regularly." Laminations are the metal frames that hold a motor's windings, and stamp capacity is a measure of the stamping and annealing process that joins the laminations together.
Motors and Friends
Besides their performance benefiting internally from better assembly techniques and materials, motors also are being designed to integrate more closely with formerly distinct design elements. "We used to see motors, gearheads and lead screws implemented separately, but now everyone is combining these technologies into more unified packages," Johantgen explains.
For instance, to accommodate a larger and more powerful servo motor in their Phoenix II 275G gear grinding machine, engineers at Gleason (www.gleason.com) in Rochester, N.Y., combined it with a compact rod-style screw actuator. The servo motor and actuator were needed to move a 50 lb manifold of coolant jets in small increments.
The machine's old stepper motor couldn't produce enough torque dependably to do the job. It would stop and sometimes lose position. "This would cause the machine to send a message to the operator to investigate the situation before the start of the next cycle," says George Chamberlain, Gleason's design engineer. "The machine would indicate a positional error, and then you would have to re-reference the position of the coolant. The most important factors in choosing the new actuator were its overall torque and its compact design. Most rod-style actuators have a screw that is driven by a motor connected inline. Tolomatic's RSM actuators have a reverse-parallel drive in which the motor is mounted alongside the actuator and drives the screw through a toothed belt and pulley assembly."
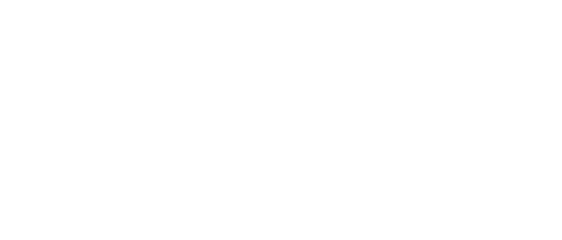
Leaders relevant to this article: