We’re contemplating a switch to machine-mount I/O from cabinet-mount I/O for some areas of our larger printing presses. We know that machine-mount I/O is more expensive, but we think we can make up some of the difference because we won't have to design, purchase and install remote I/O cabinets. Are there any other savings from using machine-mount I/O as opposed to conventional cabinet-mount I/O? Are there any safety or other issues that we should be aware of before we make the switch?
—From February '10 Control Design
Answers
Significantly Less Costly
In our experience, machine-mounted I/O is significantly less costly than cabinet-mounted solutions, especially if they are used with a suitable low-cost networking strategy. For example, based on list pricing, a four-input AS-Interface IP68/69K machine-mounted I/O module is just $2 more than the equivalent IP20 enclosure-mounted module.
It is absolutely correct that additional savings can be realized because the installation is much simpler and requires less ancillary materials. In fact, machine-mounted I/O has the potential of additional savings when a networking solution with a high degree of granularity is chosen. In this case, the number and length of sensor cables can be reduced.
For machines with low I/O density, "single piece" modules with the "connect and done" technology are available. These types of modules do not even need additional cord sets. Another advantage of using "connect and done" technology is that such modules might make mounting in the conventional sense completely unnecessary.
Helge Hornis, manager intelligent systems,
Pepperl+Fuchs, www.pepperl-fuchs.us
Not for Everyone
There can be significant savings when switching to machine-mount I/O, but it's not the answer for every application. Machine-mount automation products and I/O are a good fit for applications that include several pieces of modular equipment that need to share intelligence over a long distance. In many cases, printing press lines, with their often extensive in-feed and discharge associated equipment can benefit from machine-mount automation products, depending on their configuration.
One area where machine-mount components provide substantial savings is in the wiring and associated labor cost. On machines that traditionally use a cabinet-bound centralized control system, each sensor or actuator must be wired back to the control cabinet in conduit or cable tray. With machine-mount devices, sensors and actuators can be locally connected to machine-mount I/O. This I/O can either be connected to a local machine-mount controller or connected back to a central controller. Additionally, cabinet-bound automation components inherently require extra troubleshooting steps, often to gain internal cabinet access while complying with plant safety procedures.
In either case, the connection back to the central controller from the local machine-mount I/O or the local machine-mount controller can be made via a wired or wireless network. If the network is wired, just one cable is required for connection of many I/O points back to the central controller. If the network is wireless, then no wiring is required back to the central controller. This approach saves machine builders the costs to design, purchase, install and commission extensive cable and wiring systems. Commissioning costs are usually very high when many I/O points are wired back to a central controller and relatively much lower with the reduced wiring of a decentralized control system.
Paul Ruland, product marketing, automation systems,
Siemens Industry, www.industry.siemens.com
Cutting the Cable
With machine-mount I/O, the sensor cable lenghts are drastically reduced and can be connectorized at both the sensor end as well as at the I/O point right next to the sensor. Although a cable with connectors at both ends is more expensive in general than one with a connector at only one end, it's important to consider the benefits. The sensor cable running back to a main panel is usually 10–100 ft long. A cable that's connectorized at both ends between a sensor and a machine-mounted I/O module can be as little as 0.5 m long, or shorter is some cases. That's an impressive reduction in expensive shielded cable for analog I/O or in multiconductor, non-shielded cables for digitals.
As an added benefit, machine-mount I/O modules are out in plain sight where even an untrained operator can look at the inputs and directly note if a photo sensor, proximity switch or any other input sensor is really working. In the past, when those same inputs had to go back to an electrical panel, it was taboo for an operator to open any electrical panel door. Even knowing where to look in the panel to note the status of a sensor was an issue. Today, troubleshooting has become so simple that the operator can quickly note what equipment on the machine is not functioning. When the operator notifies maintenance, they can accurately suggest what might be wrong and the electrician already knows what to focus on and can possibly even bring required replacement parts in advance. Replacement of parts is fast and easy because with machine-mount I/O, everything is plug-and-play between the I/O module and the sensor.
In this scenario, all the conduit material and wire running from the individual sensors back to the main panel also go down in cost. With machine-mounted I/O, only the communication cable and DC power are needed to run the I/O on the machine.
When it comes to concerns about safety, the old adage holds true—location, location, location. Consider: What nearby equipment could potentially fall onto the machine-mounted I/O? Is the machine-mounted I/O going to get washed down? Water might be OK and not harm the I/O modules, but some aggressive cleaning solvents might cause damage. Is the location of the machine-mounted I/O such that if an operator has to climb on the machine they could step on or trip over the I/O or cables and rip the equipment apart or possibly lead to a workplace injury? Of course, proper precautions and safety considerations should be made with these questions in mind.
Kurt Wadowick, I/O systems product specialist,
Beckhoff Automation, www.beckhoff.com
Ensuring Safety
In the case of machine-mounted valve manifolds, you also save on the installation time of hardwiring each individual solenoid to an output device, and subsequent troubleshooting of each solenoid. Use a supplier that provides manifolds factory-assembled and tested before delivery; this should assure there are no faults in the solenoid connections. Also, look for products that provide integrated diagnostics for their I/O and pneumatics. If used properly, this will also save troubleshooting time and money during commissioning and after-sales support.
Safety should not be different than it is for conventional cabinet-mount I/O. However, since they are no longer locked inside a cabinet, there is always the potential for the I/O to be handled. If devices have hardware settings, and they can become misadjusted, this usually will result in the device not operating, but should not cause outputs to turn on inadvertently. If pneumatics are included, be aware that manual overrides are now exposed. You can select pneumatic valves with overrides blocked.
For troubleshooting purposes, some manifolds today provide an HMI or other local means to actuate valves locally during troubleshooting, electronically replacing the overrides. If safety is a concern, machine-mount I/O can be combined with a safety relay, provided there is an isolated source and common for outputs.
Frank Latino, manager for valve terminals and electronics,
Festo USA, www.festo.com
More Expensive—Not
If you're thinking machine-mounted I/O is more costly because it needs to be ruggedized or otherwise specialized I/O, then I would say shop around for better I/O. There are plenty of vendors whose standard lines of I/O offer wide vibration and temperature operating specs and all the other rugged features that you need.
Also, when you choose machine-mount over cabinet I/O, you save on the cost of the remote cabinet(s), but you also cannot understate the tremendous cost savings you enjoy by not having to bring all the wiring from all those individual I/O points back to cabinets. Plus, you're also gaining flexibility and perhaps saving costs in the future since cabinet I/O is expensive to change, rearrange and troubleshoot (lots of wires to trace).
Cabinet I/O also locks you into a fixed physical location because your machines are all wired back to their individual I/O cabinets. Conversely, machine-mounted I/O is attached to the machine. So if you choose to rearrange your factory and/or move a particular machine, its I/O goes with it. Traceability is never an issue because the I/O is local (making troubleshooting easier), which can save even more time and expense.
Tom Edwards, senior technical advisor,
Opto 22, www.opto22.com
Consider the Environment
For cost savings to be realized with machine-mounted I/O, one must first consider the installation environment. Notable areas of consideration would be the environmental conditions in which the machine is located, vibration, distance from the host system, the number of points to be controlled or monitored, plant RFI/EMI, and of course whether the installation area is in a hazardous area.
I assume that a printing press would not be located in a hazardous environment, so let's list some of the installation considerations that would affect installation cost:
Environmental: Temperature, humidity, moisture and vibration should be reviewed. Most remote mounted I/O will already include, or will require, some type of enclosure because the electronics typically have ingress protection ratings of no better than IP40. Because temperature is the main culprit of failed electronics over time, ensure that the I/O you select will meet ambient conditions plus additional heat generated by the machine itself. Many, but not all, remote I/O manufacturers make I/O that operates in temperature ranges of -40 to 85 °C. Lastly, vibration should be considered. Most manufacturers will have some vibration specification associated with their equipment or at least will have some type of empirical test data that shows how the electronics will withstand vibration or acceleration.
RFI/EMI: Most cabinets in manufacturing facilities are metal. Therefore, most cabinet-mounted I/O was not designed for direct exposure to high levels of plant noise. Field instruments, on the other hand, have been designed to be impervious to most levels of plant-related noise. Equipment's noise rejection capability is often referenced to some international electrical standard or is sometimes stated in volts per unit of distance. Variable frequency drives (VFDs), switching relays, welding and walkie-talkies all emit high levels of noise that can interfere with electronics that are not suitably protected. Choose remote I/O that has been designed for these noisy environments or make sure that it is placed in a metal enclosure attached to your machine.
Distance from remote cabinet and number of I/O points: Obviously, cost of wire and the number of points that are to be monitored has to be reviewed in order to realize any real cost comparison between the two installation methods. If the distance is short and the points are few, then the cost savings in mounting the I/O directly is probably not going to yield high returns. However, if the point count is high and the distance long, you could consider using machine-mounted I/O that incorporates some type of digital communications capability. Discrete points are commonly multi-dropped on a digital network like AS-i bus or DeviceNet, and analog points are commonly monitored over a number of networks to include Modbus RTU, Modbus TCP, Profibus-DP, Profibus-PA and Foundation fieldbus. Implementing one or multiple of these fieldbus protocols can reduce your cost exposure as it relates to wire. Of course, the host system has to be equipped to handle the network and physical medium chosen.
Tina Lockhart, director of engineering,
Moore Industries, www.miinet.com
Placement Flexibility
For large printing presses like yours, machine-mounted I/O is a great option because it allows you to place machine-mounted I/O very close to the sensing or actuating devices. This provides flexibility in terms of where the I/O can be sited. Often, depending on the product selected, I/O can be mounted on the machine structure and be highly distributed. Considering the premium put on plant floor space, machine-mounted I/O offers advantages over in-cabinet I/O, where space and location are factors.
Today, most of the available machine-mounted I/O carries the same operation specification and industry certification as in-cabinet I/O. In choosing machine-mounted I/O, however, be sure to choose compatible cordsets and connectors to use between the field devices and the I/O. If your system has incompatible ones, you make them compatible by using a software selection tool for I/O cables and cordsets that connect sensors and other field devices.
In addition, although machine-mounted I/O sometimes costs a little more upfront, it provides increased productivity and cost-savings through easier design, testing, deployment and maintenance. For example, with large machinery like your printing press, you can save time and labor costs with machine-mounted I/O because wiring from the field devices to the I/O can be completed before the entire printing press is in place. In addition, you can test the devices and I/O on each section individually, and then simply connect them together once testing is complete with network cables.
See Tow Seng Kian, business manager, distributed I/O,
Rockwell Automation, www.rockwellautomation.com
Distributed Control
We've found that the machine control productivity can be optimized by using distributed or remote control systems that incorporate multiple controllers tailored for the jobs that they perform. There might be a central PLC, but typically the central PLC is best used for supervisory functions and program downloading and not active control of critical machine cycles. By using a closed-loop motion controller that is designed to accept sensor inputs directly and directly connect to the motion actuators, the central PLC is unburdened of the higher-performance task-specific control functions that are best suited to be performed by motion controllers. Often a less expensive PLC can be used, sized optimally to perform the less intensive functions of supervisory control.
Locating motion controllers in close proximity to the machine (typically by DIN rail mounting in a panel that is affixed to the machine or located very close to it) ensures short wire runs for time-critical signals and maintains highest signal quality, and typically eliminates the cost and potential signal delays caused by intermediate I/O conditioning or concentrating modules used in an environment where all control is centralized.
Distributed controllers such as motion controllers typically communicate with a supervisory PLC over a network such as Ethernet or Profinet. The use of networks such as Ethernet make for easier machine maintenance and expansion, and save costs compared with the old point-to-point wiring methods.
Bill Savela, application specialist,
Delta Computer Systems, www.deltamotion.com
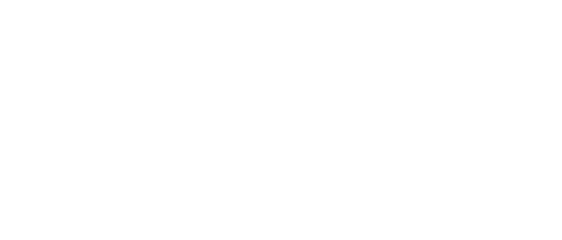
Leaders relevant to this article: