When we talk to customers about controls upgrades, we're starting to get questions about viewing energy usage in the HMI, and sometimes sending energy consumption data to asset management systems. This is mostly about electric motors, but there's a little air consumption involved, too. We make modular equipment that lets users plug in various modules to their line for product flexibility, so some of them are looking for the more energy-efficient scheduling. What can you tell me about how this can be included in open-standard-based automation?
—From January '11 Control Design
Answers
Easing Data Collection
Viewing energy consumption is a critical first step toward reducing usage and cutting production costs, so it's no surprise that many end users across all industries look for quick and easy access to their consumption data. The good news is that existing automation infrastructures can help end users access and leverage that information seamlessly.
Most machine designs include the necessary meters and sensors to gather that energy usage data for regulatory compliance or batch management. But by pulling that information into energy historian software, users can track historical consumption data, monitor real-time usage and build role-based dashboards tailored to display information specific to performance goals.
For example, executives can view high-level KPIs, including total energy costs per plant compared to production output and greenhouse gas emission alerts that are color-coded based on pre-determined baselines. Meanwhile, plant and facility managers can separate energy consumed by the facility itself vs. energy consumed by production assets and can view individual consumption and emissions reports for any line or individual machine in the plant. They can determine the most efficient lines to run, based not only on operating efficiency but on overall costs as well.
Similarly, machine operators can view energy costs per hour compared with other shifts on the same line to promote and reinforce behavioral changes, while maintenance personnel can view fluctuations in the energy signature of individual assets to proactively identify potential problems.
Cliff Whitehead, Manager, Business Development,
Rockwell Automation, www.rockwellautomation.com
Integrated Power Measurement
The largest consumer of energy in most control systems is typically the drives and motors. Today, suppliers offer integrated power measurement capabilities directly in their servo drives, variable-frequency drives (VFDs) and even stepper controllers. In addition to providing current and voltage, these drives offer information on real power, reactive power and apparent power. Drives with active power supplies can regenerate power back onto the main line instead of wasting it in braking resistors. This is done, for example, when decelerating a large inertia. These drives can then provide information on the consumed and regenerated energy as well as the energy balance over time.
Another way to monitor power consumption is with power measurement I/O modules. These modules attach to a PLC much like standard I/O, but have specific capabilities for measuring the three-phase or single-phase power of a system. These I/O modules round out the energy measurement product offering by allowing machine builders and end users to measure energy consumption of non-motion components as well as devices outside the control system, such as furnaces. These modules also can measure the power consumption of drives from manufacturers that don't have this feature built in.
Because these power measurement I/O modules can be used on most common fieldbuses, they can be added easily to any brand of PLC or even retrofitted to machines in the field. Some energy-conscious users have even installed plant-wide energy measurement systems that use these modules on each one of their systems. This is a relatively low-cost solution to monitor production energy, and can be tailored to fit most existing facilities.
All this energy consumption data is readily available to the PLC and can be monitored and trended easily on the HMI. Programmers can work with these values in whichever IEC 61131 language they prefer. The information can be used to generate energy usage reports, calculate operating costs, and create best operating practices. The information can also be shared over OPC, web server, or any standard Ethernet protocol to an asset management or ERP system.
Nathan Massey, Regional Sales Manager,
B&R Industrial Automation, www.br-automation.com
Different Perspectives
This question has three parts:
Can we get data about energy usage to the HMI? There are a wide variety of helpful software options to cost-effectively get energy usage data to your HMI. Today's emerging standard for this is OPC UA, which is a secured method of transporting data from the PLC up to an HMI or across the web to anywhere in the world. If you are looking for direct access or gateway-based access, HMI platforms like those from Indusoft or gateway software from Kepware can operate with Beckhoff controls natively, permitting simplified communications setup via software wizards.
How can we send this information up to management level systems? Again, there are many ways to tackle this, but one way is to use the TwinCat Database supplement. This software package allows the PLC developer to establish communication with an array of databases (SQL, MySQL, Postgress, Access, etc.), both locally on the same PLC or across the network. The configuration for this can be set up using the database wizard and, depending on the requirements, can be done without writing additional code. For more complex implementations, you can perform Insert and Select statements to add data on-demand from the program. Obviously, this provides benefits to the machine builder because it eliminates many layers of communication between the database tool and the PLC, in turn decreasing development time and simplifying supportability in the long run.
Can this be done using open software standards? Yes, the connectivity to the HMI can use OPC UA/DA/XML, all open standards and well-supported by the world's various HMI vendors. Connectivity to a management-level system can be done using standard database communication that is integrated into the Windows OS.
Corey McAtee, Technical Marketing Manager,
Beckhoff Automation, www.beckhoff.com
A Complete Picture
To help understand where energy is being used, Siemens offers PAC meters, overload devices and VL/WL circuit breakers that measure the amount and quality of energy being used by a device. These tools provide an excellent map of energy usage in a plant. As a result, users can make informed decisions to reduce energy consumption.
Another tool for understanding energy consumption in the field is a powerrate option that is offered with the WinCC SCADA system. Powerrate can accurately determine project costs for devices or parts of the plant. It provides an understanding of true manufacturing costs as well as reporting energy usage throughout the day.
Powerrate also predicts power usage for the next billing cycle and compares that to billing levels from the utility. It also helps avoid utility penalties from excess power usage by turning off non-critical systems to keep power usage below set power usage thresholds. Powerrate and the PAC meter can be used to measure and evaluate power usage from electrical, gas, fluid and air to get a complete picture of power usage.
Alan Cone, HMI Product Marketing Manager,
Siemens Industry, www.industry.siemens.com
Industry-Standard Technologies
Energy consumption represents a growing concern in today's society. Energy output is not keeping pace with demand, forcing us to take a closer look at how we transmit and consume the world's energy resources. We see this illustrated in the commercial and residential space with smart grid and "smart home" products that give us visibility into our personal energy consumption. Meanwhile, utilities are making consumption data more visible to customers to promote better usage and load balancing.
But in the industrial space, energy management and balancing are becoming even more important. Some industrial facilities can consume more than 1 MW of electrical power every day, weighing heavily on the utility grid, and even heavier on the utility bills of the facility management team. But the electric bill is usually of little concern compared with the downtime and maintenance costs that would result from machines or systems going down due to lack of power or adequate load balancing mechanisms. Even more concerning, most of these facilities have monitoring and automation systems in place today, but they are not geared toward energy management.
There are several industry-standard technologies that can be used to monitor and even control energy consumption through load balancing. Distributed, Ethernet-based measurement and automation systems illustrate a flexible and cost-effective way to implement real-time monitoring, control and load balancing. These networks can rely on existing Ethernet infrastructure, easing the burden of installation and deployment. With user-defined software, database integration and web services, facility operators can visualize energy consumption across the entire facility through various interfaces, including Windows PCs, HMIs, or even through a web browser.
In addition to Ethernet-based systems, wireless is more prevalent. There are a few standards gaining traction in industry, including WirelessHART and ZigBee. Wireless monitoring systems allow facility operators to make many distributed measurements close to the machines or systems in question. And through back-end Ethernet or serial-based connectivity, these systems can also communicate data to the enterprise level and make data available through HMIs and web browsers.
Not only can these systems provide insight into power consumption, but they can also help perform load balancing and provide an indication of machine health, thereby offering additional benefits to the end user. Online condition monitoring is very prevalent in today's industry. For systems with a modular design, complementing these condition monitoring systems with electrical power monitoring is a relatively simple task.
Nicholas Butler, Product Manager,
National Instruments, www.ni.com
Measuring Is the First Step
Since optimizing energy consumption represents one of the largest opportunities for an industrial facility to reduce operating costs, it is not surprising that machine builders are asked to monitor and present energy data. In most industrial applications today, there is no correlation between the process, machine or system operation and energy consumption. Although numerous process and discrete parameters are measured and often controlled to optimize throughput, quality and safety, energy is typically thought of as a fixed overhead expense, and there is no accountability for its use by departments or operators. A monthly energy bill is sent to and paid by someone completely removed from the manufacturing or process operations.
Rising energy costs, utility incentives for peak demand reduction (demand response), and moves toward dynamic pricing with the smart grid build-out are driving industrial facilities to monitor and visualize energy to better understand it. There are two concepts to note. One is the idea of an "energy event," which refers to correlating and synchronizing a batch or machine to run more closely to the cost of energy, in real time (referred to here as "energy-efficient scheduling"). The other is the concept of "energy intensity," which measures energy consumption per unit of output, so as not to lose perspective if large amounts of energy are needed in order to meet production needs. Energy intensity also figures the cost of energy in the "bill of materials" of a product or material being produced.
The first step to energy awareness in a machine or process is measurement and visualization. You can manage only what you can ably measure. Thus, the role of the automation supplier to the OEM is to provide technology that offers a simple way to capture and present energy data, be it electricity, gas, water, steam or compressed air. And finally, this data should be made available to both plant-level and business or enterprise systems over standard, open networks and technologies.
Arun Sinha, Director of Business Development,
Opto 22, www.opto22.com
Get Data to the People
Although the HMI products plus the PLC and other controls may consume about 30-100 W of power, these controls often influence the output of several motors that consume hundreds of kilowatts of power. Efficient and productive use of the machine as a whole has a very significant impact on energy use and costs over the course of a day, week or year.
PLC programs are set up to control the machine using programmed logic to react to the inputs and produce predictable outputs. PLCs don't make energy-efficiency decisions; people do. Runtime data and reports are used to analyze the process to determine where improvements can be made. HMI is the place where the data is viewed by operators and collected for plant managers to use. In order to have the right information available, the programmer must set up the HMI to provide what the plant manager needs.
Real-time information and operator adjustment are basic uses for HMI. The screens set up to display runtime information in real time should include more than just the basic facts required to keep production in place. The HMI screens should also provide information to answer such questions as: How much product is being produced? What speed is it running at? What is the level? Is the motor running while there is no product? Is something running at full speed when it doesn't need to? The goal here is to see runtime information and history that informs users how to run more efficiently; in other words, to make the most output with the energy, time and materials consumed.
The next step is to use the information to make correct adjustments. Can the machine be put on standby or on low speed? Does it make more sense to run at full output for shorter time periods, thus maximizing output and reducing the spending of overhead energy? Can adjustments be made to reduce energy-wasting hold time for personnel and materials? The HMI provides the interface.
The programmers can be encouraged to set up HMI screens with energy, efficiency and production information with appropriate adjustments in an intuitive way.
On a larger scale and over a longer period of time, the historical runtime data compiled by the HMI can be analyzed for efficiency improvements. If there are days or weeks with low production, these should be compared to building occupancy and work hours. It is not unusual to learn that there were months where personnel worked overtime hours to increase production yet only weeks before in a period of low production. In retrospect, it would have been more efficient to increase production earlier and reduce the extra energy use and cost of the overtime.
To effectively manage this requires additional information to understand the causes of low production and overtime. For example, were there machine breakdowns that caused the low production and created backlog? What caused this? Could the information in the HMI about runtime have been used to schedule maintenance and avoid the breakdown? Think about how much energy waste there is when the whole plant staff is standing around producing nothing because a machine is broken. Meanwhile, the HVAC and lighting are at 100% and associated machines, conveyors, lift trucks and so forth are idling. It would be much better to have things running and to avoid unscheduled breakdown. Maintenance can be done in a scheduled way so that people are not wasting energy. Could multiple machines be maintained at the same time and save even more by reducing the number of maintenance shutdowns or off-hours jobs? For example, maybe the goal is to perform preventive maintenance at 90% but another machine is at 80%. Do both at the same time and pay the overtime costs (in terms of dollars and energy use) only once.
The bottom line is that HMI contributes to efficiency in a number of areas:
- Runtime data allows the operator to run the machine and process better.
- History and trending allows the owner to schedule maintenance and avoid energy-wasting unscheduled downtime.
- History and trending allows management to make larger long-term adjustments to boost productivity.
- Remote access tools such as web browser viewing of HMI screens allows plant engineers to view overall productivity of multiple locations from the office where energy use is understood.
- HMI can be set up to send email or text messages to refill or give attention to machines before materials run out, tanks overfill or breakdown occurs.
- Data sharing between machines that feed materials from one to another can allow the whole process to be coordinated, thus reducing hold time.
Although it is the people who make the energy management and efficiency decisions, it is the HMI that provides the best overall tools to accomplish this task. The HMI provides real-time process status, historical trend data, linking of data between different parts of the process, remote access, notification and the interface for users to make adjustments. Proper use of this interface can boost productivity, reduce downtime, increase efficiency and provide valuable information that can be used to make adjustments to the overall process, thus saving energy.
Jacob Kimball, HMI product marketing,
Schneider Electric, www.schneider-electric.com
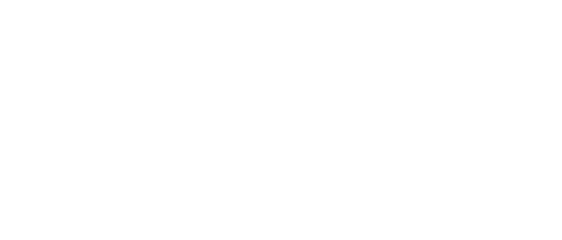
Leaders relevant to this article: