By Jim Montague, Executive Editor
Some folks are still debating and waiting to see if wireless is really useful in process monitoring and control. Many others jump in with both feet and solve problems as they come up.
One of the jumpers is Western Refining's refinery near Gallup, New Mexico, which recently upgraded its tank operations and process units with a mesh networking solution and went way beyond just saving on cable.
Based in El Paso, Texas, Western is an independent oil refiner and marketer, and has a combined crude oil processing capacity of approximately 221,000 barrels/day. Its refineries and affiliates serve customers in Arizona, California, Colorado, Nevada, New Mexico, Texas, Utah and the central East Coast of the U.S. Its high-value, light products include gasoline, diesel and jet fuel.
To produce these products, however, the Gallup refinery operates in a very rocky, very windy, very dusty environment that is also at about 6,000 ft in elevation.
And, as if that weren't enough, the refinery is also located next to a 600-vehicle truckstop, whose many visitors all have powerful base radios that can create huge amounts of potential interference.
More Monitoring
"The Gallup refinery uses a legacy TDC 3000 distributed control system (DCS), but our management also wanted to extend monitoring capabilities to remote tank farm areas," says Reginald Joseph, Western's senior process controls engineer, who recently presented Western's story at Honeywell Users Group 2010. "However, the costs of traditional wiring and conduit for monitoring outside storage units were estimated at $15,000 to $22,000 per tank. As a result, starting in 2008, we began implementing Honeywell's OneWireless. First, we completed a site survey with Honeywell to determine the project scope and challenges, and then we implemented a multi-function wireless mesh network to support a variety of applications in one network. Wireless technology was then employed for tank gauging, and it's now being introduced for high-level analog and digital indications in our process units. Monitoring data is then integrated into the existing DCS and advanced applications."
Joseph says Western Refining's primary motivations for adopting wireless include:
- Saving up to 90% of the installed cost of measurements, which usually go for cable, conduit and related construction
- Traditional wired infrastructure is largely unnecessary with wireless field devices
- Wireless reduces costs for comprehensive process monitoring
- Connects to points that are physically or economically difficult to access
- Allows easy expansion for added measurement or actuation points for simply the cost of the transmitter
- Offers robust security, predictable power management and multi-speed monitoring
- WiFi coverage is available at no additional cost.
Though they can be adapted to specific needs and environments, there remain several basic steps for getting wireless up and running in any application or facility, according to Penny Chen, Ph.D., principal systems architect for Yokogawa of America's (www.yokogawa.com/us) IA global marketing division. Dr. Chen says this list should include:
- Understand your process application's needs, and use them to direct you toward the appropriate wireless solution for it
- Develop your wireless and update your wired integration strategies together and employ your overall networking needs to help pick the right standardized wireless technology for your application
- Perform a site survey to gain a thorough understanding of your facility's environmental conditions, limitations or likely interference sources, such as buildings, walls, steel structures, water, deep forest, long distances, short distances with emissions or dead angles; changing antenna technologies can help transmit or receive optimal signals
- Start your wireless sensor network with a small trial at the beginning
- Implement wireless to fulfill your application's needs for today, but design your network so it can be expanded, scaled up or made to accommodate more sophisticated types of data in the future
- Educate and train field personnel in the skills they'll need to gain the most benefit from your new wireless system, and encourage them to come up with new places where future wireless signals and nodes may be useful.
"At the refinery, Honeywell's XYR 5000 wireless transmitters replace outdated pneumatic devices that are used for valve positioning and process variable indication," says Joseph. "Meanwhile, optimized wireless infrastructure with narrow-band radio frequency hopping ensures maximum performance. Wireless devices transmit measurements to a base radio connected to the plant control system. These wireless transmitters break down barriers to monitoring variables in areas where traditional hardwired transmitters are too costly and difficult or time-consuming to implement. Our wireless instruments are designed for applications with no access to power, that are remote or difficult to access, that require frequent changes in instrumentation schemes or where manual readings are typically taken."
Consequently, wireless has become a desirable alternative to traditional copper wiring at Western Refining—wiring that not only adds cost, but also requires high maintenance and causes unreliability, according to Joseph. "ISA100 wireless transmitters can monitor a variety of processes and assets in hazardous and remote areas," he states. "In addition, data can be used in a variety of systems, while wireless frequency-hopping, spread-spectrum technology adds security and ensures that noise interference at any one frequency doesn't block the communications or cause security concerns. A single, scalable wireless network conserves spectrum and power, too."
Joseph says that by 2011, Western will install more than 100 wireless transmitters throughout the Gallup refinery for various process monitoring tasks, as well as non-critical control applications. "Wireless instrumentation will be installed on at least six additional process units," explains Joseph. "The first control-related wireless applications will be in off-site blending. Honeywell's wireless applications have helped us optimize plant productivity and reliability, improve safety and security and ensure regulatory compliance. This is much more than just avoiding the cost of wire. The key value of wireless is in its ability to integrate valuable data into existing control systems and advanced applications, while also sharing that data with other networked applications."
Coordinating Communications
Though external or environmental interference can be a pain, sometimes an application or facility itself can be even more difficult for wireless—until a good solution is found.
Ternium Siderar's (www.terniumsiderar.com) steel plant in San Nicolas, Argentina, recently adopted a wireless solution to improve its furnace operations and save 50% on cabling and installed costs. Five transmitters collect and send data from electrodes soldered near tapholes onto the hearth's shell. The devices transmit continuous data to a Smart Wireless Gateway from Emerson Process Management located 50 m away in another room, which sends the information to the facility's SCADA system.
As a result, Emerson's self-organizing wireless network delivers reliable electromotive force (EMF) data directly to Ternium Siderar's SCADA system despite harsh conditions that include temperatures as high as 60 °C and high electromagnetic noise. The EMF measurements allow the plant's engineers to achieve smoother and safer furnace operations. "We've improved furnace energy efficiency, process stability and safety," says Esteban Pagliero, Ternium Siderar's electronic engineer. "Knowing the EMF enables calculation of the amount of iron and slag inside the hearth, which enable the improved operations. This allows us to avoid raising the operation level by too much, which considerably increases the risk of serious accidents."
Beating the Traffic
Of course, sometimes distance and too many devices communicating simultaneously can be as bad as traditional electrical interference. Cano Petroleum and the Cockrell Ranch Waterflood project inject pressurized water into formerly tapped wells in the Texas panhandle. Boss Automation (www.deakinelectric.com) in Spearman, Texas, developed and implemented a discrete automation platform and SCADA system to monitor pressure and flow into the wells.
"In a radio network of this size, it was imperative to be careful in setting up the PLC messaging," explains Patrick Haga, ProSoft's wireless engineer. "If all the radios tried to communicate at the same time, we could have swamped our bandwidth with RF collisions and retries. With this in mind, we created a polling-style network instead."
As a result, the Cockrell Ranch Waterflood project went live in spring of 2008 and has had near zero downtime since then. "The process is incredibly reliable and consistent and makes for an essentially self-managed site," says Chris Deakin of Boss Automation. "From the main SCADA monitoring station, the operators are able to see virtual diagrams of the wells and what's going on within them, as well as all the data collected by the RTUs and control units. The wireless network is so seamless and reliable that it's virtually transparent to the user."
Moving Big Boxes
While it's always important to install wireless equipment carefully to get the best reception and avoid interference, the devices being linked are usually fairly stationary. Wireless becomes even more of a challenge when the equipment it's on is moving around a large facility. That's the case at the AutoStrad terminal at the Port of Brisbane, Australia, which is reported to be the world's first free-roaming, robotic stevedoring facility.
Operated by Patrick, Australia's largest port services and container terminals operator, the 1x0.5 km terminal is occupied by 110-ton AutoStrad units that remotely transport shipping containers between ship-to-shore cranes and trucks.
To improve its 24/7 operations, Patrick recently developed its remote control operator station (RCOS), which relocates its operators at terminal truck grids more than 500 m away into one control center, where they remotely control an AutoStrad to pick or place containers with an accuracy of 25 mm. Patrick worked with Crisptech to build its RCOS, and Crisptech helped install Moxa industrial video encoders on every AutoStrad unit for real-time visual management. The devices feature high video resolution, wireless tolerance, low latency (less than 200 ms from photon capture to visual user display) and real-time video for events.
In addition, Moxa's industrial gigabit Ethernet switches are installed in every electrical cabinet near the loading grids and feature remote management, redundant fiber links, multiple UTP ports with VLAN functions, DIN-rail mount and various voltage inputs, and they can operate in extreme environmental conditions including high humidity and wide temperature range of -40 to 70 ˚C.
Conveyor TALK
Finally, not only can wireless help operate moving vehicles, but it also can help build the vehicles, too. For instance, Mahindra Vehicle Manufacturers deployed ProSoft's wireless EtherNet/IP radios and devices in November 2009 to run the electrified monorail system (EMS) that conveys newly assembled light trucks through work stations on the trim, chassis and final line at its new plant in Chakan, Pune, in India.
The plant's engineers worked with system integrator Precision Automation and Robotics India to coordinate control data moving between the EMS's I/O modules and variable frequency drives and its programmable automation controllers (PACs). The team says their resulting system allows real-time communication of I/O status between the EMS's 33 carriers and PACs, but without the rigid copper bus bars and brush collectors that other conveyors must use.
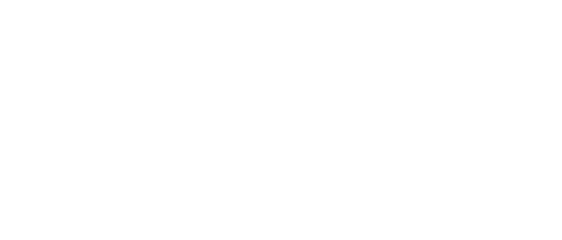
Leaders relevant to this article: