ll Variable Frequency Drives With Standard Induction Motors Give the Same Performance as Stepper Motors?
We've always used stepper motors in our semiconductor processing machinery with great success, but we're looking to cut costs. I've heard that it's possible to combine some of the newer VFDs with standard induction motors and attain performance close to stepper levels for less money. Does anyone have any experience with this type of an application? If so, what are the pluses and minuses?
ANSWERS
Questions Beget Questions
There are a couple of things to consider in determining which technology is the best value. In terms of TQ-per-dollar stepper motors are virtually unbeatable, often selling for under $30 in volume. The mating drive, however, may add to the system price, if not carefully selected. This brings us to Question 1.
1) How many axes of motion are on your system? If multiple axes, then one can deploy a dc input stepper driver with said motor. The combination of stepper motor and driver can sell for under $150 per system in volume. Commercially available off-the-shelf (COTS) ac inverters wire to the ac line. Such an ac inverter may be similar in cost to an ac-input stepper driver, but is more expensive than a dc-input stepper driver. So if you have multiple axes, a stepper motor may be less-expensive.
If you must use ac-input drivers, then another question might arise.
2) Are you trying to precisely control velocity only, or velocity and/or position? Stepper motors and drives are terrific at precise velocity control, as well as position control. If you must precisely position, or accurately control speed —especially at low speeds— steppers will perform well, while ac motors will not.
3) If you are trying to precisely control velocity but it is always a certain fixed speed, a stepper motor variation —the ac synchronous motor— may be a less-expensive bet than either of the above-mentioned technologies.
In short, an ac inverter may be as cost-effective as a stepper solution if you are wiring the driver to an ac line and you are trying to control velocity. Otherwise, stepper will still be the best bet for your application.
Scott Evans, Business Unit Director
Kollmorgen, www.kollmorgen.com
Low-Frequency Operation
Stepper motors are unique, in that they have preferred rotor positions such that when energized they rotate in a discrete number of degrees or radians. These movements are called "steps." This action is repeatable and predictable. Unlike a high-performance, low-inertia, ac-induction motor, which is designed with skewed rotors to prevent the occurrence of what we call "cogging" at low speeds, which could be called a form of stepping, stepper motors are designed to perform with a pronounced cog or step. Drives are made now to operate at very low frequencies, and motor designers have come along, as well, with motor designs to prevent these discrete movements at these low frequencies. Your typical ac motor and drive today can operate at 1 Hz, or 30 rpm for a four-pole machine, with very smooth rotation.
Mark Kenyon, product marketing manager
LV Drives, ABB, www.abb.com
VFDs Aren't for Positioning
Step motors are at the bottom of the motion control—positioning—food chain. There is no cheaper solution to getting something to make a controlled position move than a step motor and controller. The controller can be as simple as a single chip, or on the higher power end, a $50 module. VFDs are not inherently positioning devices, so to make them control position would involve adding feedback to the induction motor and an additional layer of control, adding dollars and complexity, which ultimately take the form of added cost. And it still won't be very good at positioning. At best, there could seem to be a cost crossover in some very specific applications on the higher power end (>1 hp), but, there again, the added complexity will bite you later.
Robert Bigler, CEO
Animatics, www.animatics.com
Stepper Still King
As with most questions on automation, the best answer depends on the specific details of your application. If you are dealing with a velocity-regulating system, then the advances in VFD technology can produce a competitively priced solution that can do a fine job of maintaining desired set point even down to a very low speed. There are a large number of manufacturers of VFDs, with most of them making quality products. This provides great flexibility for the engineer in laying out his system. There are some manufacturers who are offering rudimentary positioning in their VFDs, but this is not seen in the low-cost base models.
For cost-effective motion control, stepper motor technology is still king. Especially with the trend toward integrated stepper technology, with the motor, drive and, in some cases, motion controller integrated into one package. Not only does this allow for inherently low-cost components, but it also saves when considering installation, wiring and panel space requirements. Stepper motor technology has also advanced, allowing steppers to infringe upon many applications previously reserved for servos.
In conclusion, the answer depends upon your application. For low-cost speed control, VFDs can be a very effective answer. For positioning, stepper technology is still the best cost-effective, high-performance solution.
Clark Hummel, Applications Engineering Manager
Intelligent Motion Systems
Lost Torque and Vibration
The stepper motor is a synchronous motor, meaning it precisely follows the electrical signal it receives. This allows users to control the stepper motor's position without feedback. Its control system typically consists of a stepper motor positioning system and an amplifier that sends pulses to the stepper motor. For example, if a user wants to move the machine 100 ft, a stepper motor that receives 1,024 pulses/ft would require 102,400 (1,024x100) pulses from the control system. The stepper motor then steps through the pulses to arrive at 100 ft.
Stepper motors have two disadvantages: susceptibility to lost torque and vibration. If the load is too high, the stepper motor can "pull out." The stepper motor loses the ability to produce torque, causing it to stall out and lose its position. When this happens, the system needs to be "homed" to a known position. Stepper motors also have issues with vibration due to its "stepping" process.
When considering a variable frequency drive (VFD), users should think about the positioning precision required for the application. Applications requiring high-precision positioning will need a high-performance VFD that has a position loop and feedback capabilities. These capabilities allow VFDs to position a standard induction motor with encoder feedback.
The position loop is given a position command, an acceleration rate, top speed and deceleration rate. Using these commands, drives ramp the motor to the desired speed and decelerate it to the correct the position. With the encoder, the drive does not pull out like a stepper motor. Instead, it remains in a stalled condition and doesn't lose the actual position.
VFDs offer bottom-line results, as well. By precisely matching motor speed to load requirements, VFDs reduce energy consumption, improve process performance and preserve equipment.
Todd R. Jaremko, Senior Project Support Engineer
Rockwell Automation, www.rockwellautomation.com
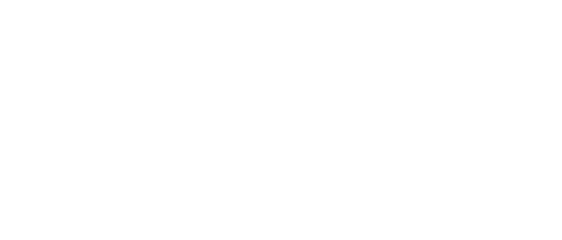
Leaders relevant to this article: