By Jim Montague, Executive Editor
Stepper motors always have been the feisty "little engines that could" of the motion control world. So, it should be no surprise that some steppers are being festooned with or linked to software and components, such as PLCs, that allow them to do jobs traditionally done by servo motors.
For example, Roger Klisch, who owns Machine System Integrators near St. Paul., Minnesota, was asked by the University of Minnesota's Bell Museum of Natural History to help animate a wildlife exhibit. "One of these landscapes was a scene of an eagle in its natural environment, along with a gopher that was slightly popping out of its hole," says Klisch. "The request was to make the gopher move when a person walked by. One of the larger challenges was the budget—the customer had only $800 for this project. Since I am a small integrator and my costs are low, I decided to do it, and I stayed well within the budget."
To accomplish this feat, Klisch used one of AutomationDirect's (www.automationdirect.com) PLCs for the primary control and its stepper-output function to drive a small step motor attached to a simple, plastic rack and pinion. The pinion was on the stepper and the end of the rack was attached to the base of the gopher. "I used a small step drive and motor from Superior Electric and a photoelectric sensor to detect a person walking by the exhibit," says Klisch. "The photoelectric sensor was inconspicuous because it was buried within the landscape. It was a hit. The animated gopher taunted visitors and then ducked out of sight. It really added extra spice to an exhibit that can inspire kids to further explore the museum."
Servo-Like Steppers?
While the traditional view of stepper motors is of an open-loop device with no encoder or other positioner, some developers are using PCs to control steppers in some servo-like ways. This usually means using an encoder for feedback to help create a closed loop with the PC.
[pullquote]Christian Fritz, National Instruments' (www.ni.com) motion and mechatronics marketing manager, explains that stepper motors and servo motors are coming together because steppers are gaining sophisticated controls that allow them to act like servos, while at the same time servos are simply getting easier to use. "This is why some applications of steppers and servos are overlapping. There used to be clear differences when to apply one or the other, but that line isn't as clear anymore," says Fritz. "For instance, one of the main weaknesses of steppers has been eliminated by adding microstepping functions, which are handled by a built-in controller, and can help steppers operate at low speeds. Also, more steppers are using non-encoder feedback devices, such as sensing resistors, which can gather data about the rotor, help create closed-loop algorithms and then apply a filter to help the stepper eliminate noise and rough performance at low speeds."
For instance, CNC-enabled plasma cutting machine builder Dynatorch (www.dynatorch.com) in Paducah, Kentucky, recently implemented AutomationDirect's C0-05DD Micro PLC, so it could use a stepper motor and drive in a closed loop in its Technogon torch height controller (THC) for controlling a CNC plasma cutting head's height over a plate. The company reports that its cutting machine's control accuracy is less than .021 in., which produces consistent cuts and lessens the need for operator observation and intervention. Dynatorch adds that its low-cost PLC and stepper motor were key to making its CNC plasma cutting head possible and that its system is half the price of its competition.
Evolving Diversity
Though commonly used in the medical device and factory automation realms, stepping motors branched out in recent years into the wafer-handling aspects of the semiconductor industry and recently into plasma TVs, LEDs and solar components manufacturing, according to Nick Johantgen, engineering manager at Oriental Motor (www.orientalmotor.com), who adds that future applications could be in small machine tools and food processes requiring washdown-enabling motors.
"We always work on making our stepping motors more efficient, but as they achieve higher resolution and smoother rotations, we find ways for them to compete with servos," says Johantgen. "A stepping motor is a positioning device that moves in discrete, incremental steps and runs in an open loop, and so stepping motors generate all their torque with each step. On the other hand, servos only apply enough current and generate enough torque to meet what is being required, and so they're more sophisticated and cost more, but they run cooler and can be used in continuous duty applications."
Figure 1: Sitexco uses a stepper motor and a small drive unit to precisely control its laser cleaning system for large printing roller and cylinders up to 6 m.
Sitexco
Despite these hard differences, Johantgen reports that Oriental Motor developed a stepping motor that can run in continuous duty, too. Its PKE high-efficiency stepping motor line was introduced in Japan about a year ago and launched in the U.S. three or four months ago. "We use slightly different rotor and stator materials and a different lamination stack," says Johantgen. "We also assemble PKE differently, so the motor creates less heat, even while running at the same power as other motors. There are gray areas between stepper and servo motors, and so PKE helps to shrink them because it can work in some servo-type applications that have many short, quick moves. Some users are thinking about using stepping in place of servos, but they aren't doing it yet."
New Settings—Lots of Lasers
While stepper motor types and related technologies are diversifying, the types of applications where they're showing up is even more varied. For example, Spanish machine builder Sitexco (www.sitexco.com) uses B&R Industrial Automation stepper motors and a micro drive unit for precise positioning in its new laser-based, automated cleaning system for gently and quickly printing industry cylinder and anilox rollers up to 6 m (Figure 1). The cleaning system operates by turning the cylinders on two other rollers, while a laser beam volatilizes residue deposited on its surface. Sitexco's SXL 2900 cleaning system uses an X2X Link connection to provide high-speed data transfer between the machine's X20 I/O modules, a frequency inverter and its micro drive. A panel PC operates the stepper motor for position control, while an SDC library allows the stepper motor to be controlled like a servo motor.
Figure 2: MiniTec's laser-welding head uses stepper motors with encoders to reach accuracies required for manufacturing solar thermal absorbers for thermal flat-plate collectors.
MiniTec
"In the past, we had to use servo motors because stepper motors didn't provide reliable positioning," says Erico Cruz, Sitexco's general director. "Now we use a stepper motor with an integrated encoder, which gives us precise and dependable control at a good price/performance ratio."
Similarly, to manufacture solar thermal absorbers for converting solar radiation into energy, Switzerland-based MiniTec (www.minitec.de) developed its SunLaser laser-welding system to allow automated production of full-surface absorbers for thermal flat-plate collectors. SunLaser has a multi-axis portal, and its axes are controlled throughout their operating range by Beckhoff Automation's servo drives. The portal also has a laser-welding head on its z-axis with two laser lenses and a feed roller for the tubing to be welded. The two laser lenses are focused and positioned by a stepper motor that carries out the adjustments within a mechanically predefined positioning range (Figure 2). To guarantee precision, each stepper motor also has an encoder that detects the action of the welding heads and facilitates monitoring by the axis controller through a feedback signal.
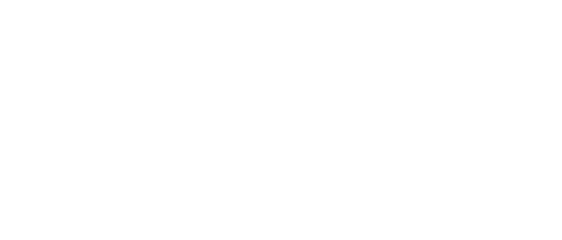
Leaders relevant to this article: