We use a micro PLC to control our metal-cutting machines with good results. When customers see that we use a PLC, they want to specify brand, causing us multiple headaches in design, programming and after-sales support. There’s very little variability in the operating parameters from machine to machine, so we're actually thinking of switching to a preprogrammed relay that would be set up and delivered by the vendor ready to go with its own part number. If a machine needed something a little different, we would order it preprogrammed accordingly. Are we mortgaging future versatility for fewer headaches right now?
—from April '10 Control Design
ANSWERS
How Do You Compete?
There is the possibility of "mortgaging future versatility" when changing a controller platform. This possibility often is application-dependent and influenced by future plans for the machine design. Any decision in controller-platform selection should be market-driven. Consider how you plan to compete against other machine builders in satisfying your customers’ requirements. If the market you’re serving won’t require much automation, then a programmable relay is a good migration. If not, then the scalability of a PLC is a better choice. In either case, the decision should consider evaluating a supplier that understands both controller categories.
Programmable relays generally do not receive as much customer brand loyalty as PLCs. That can be a significant benefit to the OEM. By having a commodity type of controller, machine builders can reduce engineering costs and software maintenance if they stay with the same programmable relay for all customers and markets. These relays could also offer easier program loading, program protection and configurable access through a built-in keypad and LCD for basic end-user maintenance.
For example, our industry-original programmable relay includes know-how-protect technology with a variety of memory cartridge choices, enabling program loading and configurable protection on power-up. This could alleviate the additional cost for part number customization and vendor pre-loaded software because this can be automatically accomplished during the power-up checkout of the machine before shipment.
Paul Ruland, product marketing manager,
Automation Systems, Siemens Industry,
www.usa.siemens.com/industry
Quantity Over Quality
Feel good about your decision and reduce costs by working with a manufacturer with a depth of both engineering services and manufacturing resources, as well as a willingness to work with you to design and develop a specific engineered solution. Volume is the first consideration. If this is a high-volume opportunity, your experienced supplier is more likely to absorb the added cost of special handling and help you and your customers get a winning custom solution that is both scalable and cost-effective. On the other hand, if the purchased quantities are small or the number of variations large, the efficiencies gained by scale are lost and you could end up with a more costly solution.
When you select a manufacturer, it is important to make sure they have the technology that meets your requirements. A smart relay can meet your current needs, while allowing for future versatility. With common hardware and software platforms, an off-the-shelf smart relay has implementation flexibility for custom applications—limiting headaches and costs for everyone involved. Working with your supplier’s technical services, an intelligent relay can be programmed for standard applications and saved to a memory module. This memory module can be used to quickly and easily configure each intelligent relay during commissioning. Changes can be made to the configuration/program of the intelligent relay and saved to other memory modules for unique applications. By taking this approach, a library of possible solutions can be developed for a spectrum of requirements; you can specify individual, customized solutions as you need them.
Michael Foley, Product Manager,
Programmable Logic Products,
Eaton, www.eaton.com
Enter the Gateway
It can be frustrating when a customer attempts to get you to switch to a specific PLC when they see what you currently use in your system. However, going from the functionality of a PLC to a programmable relay seems like a step back in time. Most programmable relays have very simple programming capabilities and limited retentive memory available. If you are accustomed to using a PLC, you could be very disappointed in what you actually get with a relay.
Perhaps a better solution would be to use a programmable gateway product that is not a full-blown PLC, but gives you the flexibility to grow and expand as you need to. This solution gives you an alternative to the PLC situation, without giving up functionality, and it could be purchased as a preprogrammed unit.
Karie Daudt, Senior Product Manager,
Turck, www.turck.com
Modification and Revision
The decision to change a significant process is not an easy one. When you weigh the cost vs. benefits, you might want to consider the following questions.
How much versatility is expected in the future? It might be difficult to predict, but designing a scalable and flexible product is crucial to the product lifecycle and evolution of your products.
What is the modification and revision process? When the need does arise to vary the program, it is important to identify and clearly document the process. This will provide valuable statistics that could help justify the costs or risk involved.
What is the impact on lead time and costs for the preprogrammed devices? The costs and lead time might increase as a result of preprogramming. Understanding how this could impact you will let you determine the amount of variability you can offer.
How much involvement would you like to retain? The amount of technical knowledge and support that you pass along to your vendor might leave you with limited expertise in the future. When minor modifications are needed, your involvement could be necessary to help avoid many other unforeseen headaches.
There might be many other questions to consider when determining what the costs and benefits are for procuring a preprogrammed relay instead of internally developing the programs. A well-developed plan will hopefully alleviate your headaches, not cause more of them.
Dan Zarnick, Design Engineer,
c3controls, www.c3controls.com
The Other Side of the Control
I was one of those pesky specifiers, telling OEMs which PLC to use, and for good reason. As a system integrator company, we often wrote the specifications and were the gatekeepers for our clients’ control platforms. Keeping the cats and dogs to a minimum reduced maintenance costs and made system integration less expensive and far easier.
When we diversified and started a custom equipment manufacturing company, I found life as an OEM conflicting. We respected our customer standards—heck, we wrote several of them. The issue was that some of these standards would require using more-expensive and less-capable control platforms when our clients wanted lower cost and greater performance.
The correct solution depends on the problem. If there is a performance or capabilities problem with a specified control platform, then be honest and set a reasonable price and reasonable reduced capabilities. They will not like it. The specified hardware provider will probably argue. If it is truly important, then it is worth the premium. The client always can hire someone to convert the system and take over responsibility.
Tom Schwieters, President and CEO,
Automation & Control System Solutions,
www.acss-inc.com
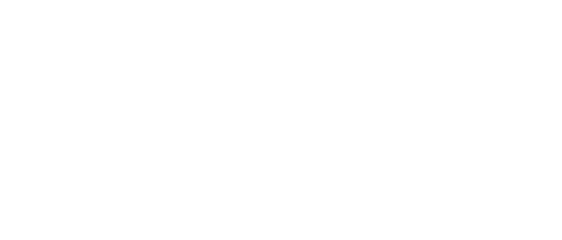
Leaders relevant to this article: