By Mike Bacidore, Managing Editor
Connectors are the glue that holds an industrial network together. Whether you rely on fiberoptic cable, copper cable or wireless communications, the connectors you choose will have a profound effect on the reliability and dependability of your network. And the environment can dictate which type of connectors is the best fit.
"Our biggest industrial environments have the same three problems—dust, vibration and water," explains Tom Prokop, manager of infrastructure and remote services, Consol Energy (www.consolenergy.com), Pittsburgh, Pa., which uses primarily fiberoptic cable at its sites. "If we know it's a high-vibration environment, we find connectors with good mechanical locks on them. We tend to migrate more to an SC barrel connector on our fiber, rather than an SC connector that might just slide in. For the electrical side, we look for things we can mechanically fasten. We use a mix of fiber and copper. All our backbones are fiber. That can be about 70-80% of our cable. Typical fiber runs might be a mile to 12 miles. In terms of connectors, it's probably 50-60% fiber."
Joe Roegner, SCADA technician for Orange County (orangecountyfl.net) in Orlando, Fla., sees similarities between his water and wastewater treatment environment and the wiring done on sea vessels. "With an ocean-going ship, vibration and corrosion are common, so using things like butt connectors to join wires are taboo, while ring connectors for terminations are preferred," he explains.
Alice McWilliams, PE, senior instrument and controls engineer at Chevron Phillips (www.cpchem.com) in Pasadena, Texas, thinks high-vibration environments are one of the more difficult environments to handle. "They can cause connections that intermittently are bad," she says. "When the connection is good 95% of the time, it's very hard to find the source of the problem."
Any environment with harsh temperature, vibration or moisture conditions could potentially cause issues, warns Matt Finlinson, sales engineer at Molex (www.molex.com). "Choosing connections that have proper IP ratings to guard against dust and water is essential," he says. "For instance, in a factory setting, these connections might be subject to machine washdown."
Even a small amount of contaminants has the potential to cause havoc in networks if the connectors are not properly sealed, cautions Nick Clute, product specialist at Turck (www.turck.com). "Any sort of mechanical disturbance—for example, high vibration—can cause network issues in regard to the connectors," he says. "But it may not be clear to all users why an IP67-rated M12 connector should be used instead of a standard RJ45 IP20-rated connector for Ethernet in a standard manufacturing environment."
The three main culprits are vibration, temperature cycling and corrosive gases, summarizes Michelle Goeman, product manager—terminal blocks and electronic interface, Wago (www.wago.com). "Applications and environments prone to severe or extended vibration are among the most problematic, especially for screw terminations," she explains (Figure 1). "In industrial settings, we've seen failed control panel connections halt production. A shift's worth of time and productivity are lost to a 30-cent screw terminal. As machinery ramp up, they create vibrations that may cause screws to back out—hence, the need for extensive preventive maintenance programs, where lines are idled so connections can be checked either with thermal imaging technology, which is expensive, or retorquing to spec, which is time-consuming."
Control panels rely on high-voltage terminal blocks and pluggable connectors. In certain environments, connections require ensured reliability against excessive vibrations.
Source: WAGO
Test the Network
Network validation tools are available to test point-to-point and end-to-end runs, but knowing when to use what and whom to trust can be the trickiest part of validating the system.
"Several years ago, our construction contractor made the connections that assembled the communication network for our DCS highway," recalls Chevron Phillips' McWilliams. "After startup, we began to experience communication problems on both the active and redundant highways. When the connectors were examined, they were so misshapen that it became very apparent the wrong tools had been used. We then contacted the DCS company and asked them to check and repair our highway. However, this was only after we had experienced a lot of tense moments concerning our communication between the DCS consoles and the DCS controllers. It would have been better to use the correct contractor the first time. The situation could have been taken care of before startup if we had thought to inspect these connections as part of a startup checklist instead of taking for granted that they had been correctly put together."
Consol Energy's Prokop prefers to build up your calibration curve by doing point-to- point and then joining the segments and doing an end-to-end run. "By just doing the end-to-end, because of the distances we're dealing with, it may take you a half hour to get to the point you need to find," he explains. Prokop suggests using the optical time-domain reflectometer (OTDR) or the copper equivalent for cable testing. "You want to test for signal quality," he says. "If you just do the first-level test on connectivity and you try to run 10 GB of data, although the connector's on, it might not be on right. Make sure you can test with the types of signals you'll be carrying."
Turck's Clute says it may not be necessary to test each individual run on many industrial networks. "Many times, it's not required until there's a problem," he says. "That being said, it's not enough to say that the network is running properly, so everything must be working. It's imperative that during final checkout the actual data is looked at with a hardware tool that is capable of keeping track of network errors and connection timeouts. It's more important to test a network after it is fully laid out. Oftentimes, network issues occur as it grows, so testing individual segments before the system is complete could be meaningless."
Charlie Norz, product manager—Wago-I/O-System, recommends looking at advanced, managed Ethernet switches for validation of large-scale, critical applications. "These switches utilize cable test menus to virtually validate physical copper links connected in each port," he says. "An onscreen menu will indicate which ports are carrying a properly terminated link. If a link is disconnected, the switch will indicate which link is open and estimate the distance from the port to location where the circuit is open. This streamlines commissioning and can save a significant amount of time in the event of lost link."
Using industrial-grade connectors with distributed I/O blocks, like in this assembly application, can make it easier when validating each leg or section of the network to ensure all cable or fiber runs are fault-free and terminated correctly.
Source: BELDEN
"It's important to have an inspection of the final work," says Orange County's Roegner. "Test everything and document the readings. A follow-up inspection before the end of the warranty period also will help catch problems that need to be addressed."
There's No Time Like …
When you test the system can have significant advantages or disadvantages. While some prefer to test as part of the installation procedure, some others would rather wait until the system has been operational for a few months and then test.
"Make sure to budget time, money and resources in the business case or ROI planning process, and be certain that you baseline your system at initial optimized performance and invest in monitoring and diagnostic tools to maintain the system throughout its useful life," advises Molex's Chris Zimmerman.
"I'm a true believer in getting a baseline test, agrees Consol Energy's Prokop. "That way you know it's as good as the day you built it or it's starting to degrade. If you wait months, you don't know that. Getting a good baseline test is very critical. Depending on the data's criticality and what kind of external forces they may be subject to, do you need to do any ongoing testing? In most of our underground lines, once they're tested we just run them. We don't test again until something fails to work or if there is suspected mechanical damage like if a piece of equipment hit a cable or someone accidentally pulled the cable down. If you know you're running long spans that are stretching your basic design parameters, you might want to test more often, too"
Baselining a system upon initial commissioning provides the user with a known set of network values or parameters of an optimized system, reiterates Zimmerman. "During the course of day-to-day operation, outside system variables, as well as within systems, device performance can change," he explains. "In addition, comparing live network or system performance against the original optimized system performance values allows the user to quickly identify problem areas on the network that contribute to downtime or underperforming equipment."
Testing and validating can add substantial time to a network installation and startup, explains Belden's Burkard, but it ensures, once the network is up and running, there will be minimal issues, if any. "It is best to test and validate a network when first doing the initial installation, before startup," he says. "It gives the chance to replace cabling or connectors, make changes to settings in the infrastructure devices and work out any bugs that always show up on a newly installed network. By waiting and validating or testing the network after startup, you compromise the ability to make certain changes to the network without affecting the current processes. By waiting until the system is operational, you almost certainly ensure there will be problems with the startup, making it much more worrisome in the short- and long-term time frames."
Turck's Clute agrees it's extremely important to test as you go. "If you install a number of nodes and then try to commission the network, it's very difficult to determine where to start if there's a problem," he explains. "All networks should be built one node at a time to verify that no new issues are introduced with a single node. That being said, it is only once the network is completely up and running for some time before it is advantageous to do a complete network communications test, because only once everything is up and running will you have the standard amounts of noise, cable length and communication running which will give the network a true test."
DIY or SI?
Sometimes, it might be appropriate to contract a system integrator to implement network solutions, specifically pertaining to connectors. But how do you know when you need help?
"When we use an SI, it's a new or complex technology that we may not have the tool set for," explains Consol Energy's Prokop. "We'll rely on them to help define the connectors and help to prove the concept. Once we find out that it does work in our environment, we'll make the investment for specialized tools and specialized training. Also when something is done infrequently, it might be better to pay. A good example of this is when we were first starting to do fiberoptic. Plasma fusion splicers were $20,000-$30,000 investments when they first came out. We found a SI that had those tools."
Typically, system integrators and engineering services companies take the customers mechanical, environmental, electrical and performance requirements and provide a bundled solution, says Molex's Zimmerman. Specifically, an SI or engineering firm would determine, for example, how robust the connectors would need to be, based on a specification, he says.
"The days of the end customer having a control engineering staff to assist in the implementation of a control solution have shifted to outsourcing to aid in reducing cost," says Belden's Burkard. "A system integrator is an economical and complete solution with knowledgeable expertise in system layouts from the control panel to the network devices on the plant floor. An SI eliminates connectivity issues. Network management reports indicate 72% of failures are attributed to the OSI layers 1–3."
Orange County's Roegner advises companies to look at their own levels of expertise as part of the planning. "The use of system integrators, as compared to trying to do the work in-house, when installing fiberoptic networks is preferable, unless of course you do it all the time," he says.
"It wouldn't be necessary to contract a system integrator just for connectorizing a solution," says Turck's Clute. "Many connectorized suppliers are happy to sit down with customers to look for potential hazards and opportunities to improve the installation. However, if a user is concerned about networking problems on a system, chances are they already have a system integrator contracted. The important thing is to make sure that you connect the system integrator with the connectorized solution provider."
Wago's Goeman advises bringing integrators in on the ground level. "This way, they can help select connection solutions that will readily withstand anticipated stresses, such as extreme vibrations or rapidly fluctuating temperatures. Upfront discussions will undoubtedly save time and costs down the road."
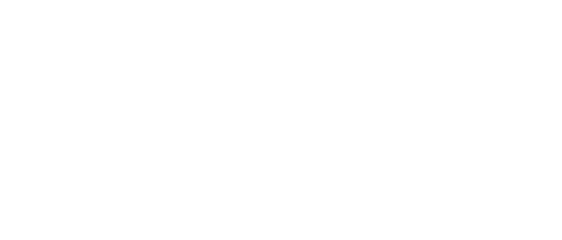
Leaders relevant to this article: