We think it makes sense to have zero tolerance for energized work in the panels and MCCs in our new machine designs, since our technicians are more involved in customer-site troubleshooting. NFPA 70E is tough to work through, but it appears we can do things such as restrict high voltage to one enclosure access and employ non-contact test points through the enclosure door and have everything else at 24 V. It seems we then can lock out panels without the technician having to do live-dead-live tests in full PPE. What can somebody tell us about this?
—from January '10 Control Design
ANSWERS
Zero Tolerance
We applaud the zero tolerance policy toward energized work and separating 24 V control circuits from higher working system voltages. Be careful though about using permanently mounted testing methods to determine the presence of voltage. The NFPA 70E technical committee makes it perfectly clear that permanently mounted devices must not be used to confirm the presence or absence of voltage.
Vince Saporita, Vice President, Technical Marketing,
Cooper Bussmann, www.CooperBussmann.com
Absence of Voltage
I'd rephrase the question. "Can I use an interface (through the door or otherwise) to make absence of voltage tests?"Yes, for an initial test, but no to a through-the-door voltage indicator/test point. You would be relying on an interface and not testing circuits or conductors directly. My dad would always tell me, "Never trust your life to a mechanical device."He was talking about using a hydraulic floor jack without jack stands, but it's great advice for any electrical or mechanical device. The question is not whether they going to fail. The question is "When?"That cannot be answered until the device does fail, and then it's too late. So direct testing for absence of voltage is necessary. Go to the OSHA website and review the Letters of Interpretation.
Unfortunately, there are several companies selling through-the-door voltage detection devices and advertising them as a way around direct contact testing. They are not.
I suggest that you perform a hazard/risk analysis before each testing session/task and carefully evaluate the probability that the upstream protective device would work according to the manufacturer's specifications. If you cannot answer "yes"to that question, it could very well be unsafe to proceed with any type of energized task.
Jim White, Training Director,
Shermco Industries, www.shermco.com
Sound Practice
The concept of bringing the test point out to a safer access location for technicians makes sense but involves additional costs and change in design.
There are a variety of important issues to recognize and address. Where technicians will be working, it is critical to perform live-dead-live tests on recently energized equipment. That said, the tests ought not to be performed with 24 Vdc as the only connection points, as that does not seem to meet industry standards. When troubleshooting energized equipment, 24 Vdc test points are sound practice.
For lockout-tagout (LOTO) or de-energizing and testing for the absence of voltage, a design that provides a clear line of sight to the potentially energized bus is necessary. This could be accomplished using a Lexan-like material, similar to the IR viewing portals, surrounding the "test point,"ensuring that the bus cannot be contacted by anything: broken part, falling bolt, finger or tool.
To isolate the (600 V class) danger to the inside of an enclosure, while enabling accurate voltage readings from the outside, touch-safe test jacks coupled with bayonet fuse holders that use current-limiting fuses are means toward meeting both the safety and maintenance concerns.
In a preliminary analysis at our facility, the proximity meter we have doesn't detect an energized bus (480 V or 208 V) through an existing panel door. However, placing a ¾-in. sheet of the Mycarta between the proximity tester and insulated, energized cable had no effect; the flux-type tester sensed the voltage correctly. Moving the energized bus close enough to the structure wall—to be sensed through the wall—doesn't seem to be safe and sound practice.
Wallace Tinsley, PSE, Senior Engineer,
Frank Ashley, Specialist-Engineering,
Eaton Electrical, www.eaton.com
Hazard/Risk
This question points out a widespread issue with many PLCs, control computers, data collection systems and other non-hazardous control equipment that coexist in the same panels as three-phase motor circuits. This requires that all work be performed to the highest hazard/risk category of the panel. Many technicians who program, adjust or troubleshoot such equipment are not necessarily qualified to work in those panels.
The ultimate would be two separate panels. However, a two-door enclosure with a barrier that complies with UL 508A enclosure material and construction requirements, creating two compartments in one enclosure, would provide the equivalent protection. As long as it contains no voltages over 120 V from a typical control transformer circuit, the control compartment would most likely be a Hazard/Risk Category 0, according to NFPA 70E Table 130.7(C)(9), requiring no arc flash PPE. Insulated gloves and/or tools might be required if contact with 120 V is possible. Reducing all voltages to below 50 V should make that compartment electrically non-hazardous, allowing any employee to work on it regardless of qualified status. A full evaluation of the actual panel design is necessary to confirm this.
Benjamin D. Miller, PE, President/Owner,
B. Miller Eng., www.bmillerengineering.com
Practical Implementation
NFPA 70E changes both how we design panels and maintain electrical systems. The goal is to find ways to remove voltage exposure for workers. Here are a few practical examples that can be implemented today.
Why open a control panel? What maintenance functions can be moved to the outside of the panel? Through-door data-access ports are more commonplace because they allow programming with the panel door closed. A more recent example is an unmanaged Ethernet switch mounted outside the panel. This unique device allows full through-door access for a worker to troubleshoot and reset the Ethernet switch. What other devices can be reengineered around through-door electrical safety? Perhaps putting certain branch circuit breakers on the outside of the panel is a good application?
For control panel design, providing a physical separation between the power and control compartments within an enclosure might become a standard. Voltages under 50 V are considered safe, so reducing the control power to 24 Vdc makes the control power section safe to work on while it is energized.
Mechanical lockout/tagout (LOTO) procedures requiring electricians to verify zero energy before performing mechanical maintenance needlessly exposes workers to voltage. Since all voltages do not create mechanical motion, through-door voltage checking devices as part of a mechanical LOTO procedure will eliminate voltage exposure. Three-phase voltage indicators (40-750 Vac/30-1000 Vdc) provide visual voltage indication, and through-door voltage portals allow non-contact test points to be used with a non-contact voltage detector.
Philip Allen, President/Owner,
Grace Engineered Products, www.graceport.com
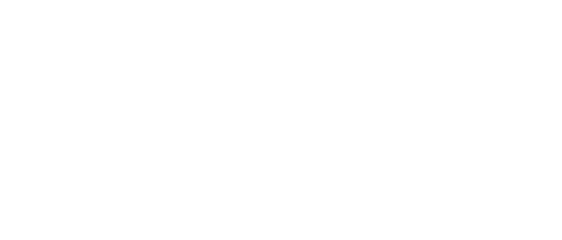
Leaders relevant to this article: