We build small systems for chemical processing applications and pull a lot of analog signals out of sensors in high electrical noise areas. Measurement inconsistencies are a too frequent complaint, and we need to minimize them. We can't easily mount signal conditioners, let alone sensors, in protective, grounded enclosures all the time. We'd like some best practices about signal conditioning device selection and even tips about the installation and wiring where that's a critical issue.
āfrom November '10 CONTROL DESIGN
ANSWERS
Good Quality Counts
In 25 years of doing installations at chemical facilities, I have never had analog noise problems nor have I needed special signal conditioning provided I used shielded wiring and grounded those shields at one point. If the system had a 24 V power supply, I left the negative floating off ground to avoid ground spikes from the noise floor. I used metallic, well-grounded conduit and a metallic, grounded box for any control equipment, and bought good-quality instrumentation.
There is strong incentive as a skid manufacturer to purchase lower-cost sensors and transmitters. However, if that equipment is not adequately shielded, the output of the device will spike with RFI noise and no amount of conditioning will resolve that issue. As a test, take a plant radio and key it next to the device while monitoring the output. If you see a spike, consider a different manufacturer.
P. Hunter Vegas, Senior Project Leader,
Avid Solutions, www.avidsolutionsinc.com
Free Signals
To begin with, choose devices that can be DIN rail-mounted and be provided power from adjacent modules through a daisy chain. This helps keep signals free from ground loops, electrical noise and other interference.
A simple two-wire setup for input and output is easier and more reliable in industrial environments. Our modules provide these features while accepting voltage, current, thermocouple and RTD as input and pass voltage or current as output, detecting all analog signals from the sensors for further analysis.
Peishan Juan, I/O Product Manager,
Advantech, www.advantech.com
Best Practices
You can take a variety of actions to help maintain the integrity of analog signals in these environments. First, use a twisted-pair cable with shielding to decrease the amount of electrical noise interference. Second, the type of analog signal that you transmit can have a direct effect on how much noise you see. Low-level voltage signals are more susceptible to noise. If you use a thermocouple (mV), wheatstone bridge (mV), standard 0-5 Vdc or 0-10 Vdc signal, use a signal conditioner to convert them to a more robust 4-20 mA signal.
If you already use 4-20 mA, you could be experiencing issues with ground loops that occur with a difference in potential between your monitoring instrument ground and field device ground. A good solution is to insert a signal conditioner into the signal loop to provide galvanic isolation. One or all of the above best practices should help reduce the inconsistent measurements you are seeing on your analog signals.
Christopher Welker, Product Marketing Engineer,
Rockwell Automation, www.rockwellautomation.com
Remote I/O Modules
Remote I/O, or distributed I/O, offers an advantage over the traditional local I/O found on a PLC. It allows you to locate the I/O modules close to the process that is being monitored or controlled. This greatly improves noise immunity, as the weak sensor signals are converted to digital signals before being transmitted long distances through a noisy plant environment. Our universal remote I/O modules use a simple two-wire RS-485 link using Modbus RTU/ASCII protocol, which is supported by most PLCs.
Barry Faust, Engineer,
Omega Engineering, www.omega.com
Grounding Guidelines
Grounded loops (in signal and power lines) are the most common source of problems (ghosts) in instrumentation/signal management, especially low-level signal. Check them out and route them separately from other cables, preferably using shielded cables. And don't forget to ground the shield only at the receiving end.
Otto Fest, President and CEO,
Otek, www.otekcorp.com
Field Exposure
A critical consideration when selecting signal conditioning devices for use in high-electrical-noise areas is the degree of isolation protection they offer. Transformer isolation, field-side input protection, and transient protectionāall are essential for measurement accuracy and consistency.
Equipment located in the field is exposed to a much greater range of electrical noise, power surges, temperature, humidity and corrosive environments than equipment in the control room, yet the field is where process variables are measured and where measuring and some signal conditioning equipment must be located. Because the wiring that connects the field and control room might be near heavy electrical equipment and run hundreds or thousands of feet, the likelihood of outside interference is greatly increased.
To help protect I/O signals, instrumentation wiring that connects field devices to the control room typically consists of heavy-duty (16-18 AWG) pairs, which are often twisted together to reduce magnetically coupled interference and run with other signal wires in a separate wiring tray. Another effective way to reduce the risk of data contamination, as well as to cut the high cost of system wiring, is the use of data concentrators. These devices collect large numbers of signals close to their origins in the field, perform signal conditioning and digital data conversion locally and then send the digitized information by communication links to a local area network or directly to control room equipment.
John Lehman, Engineering Manager,
Dataforth, www.dataforth.com
Isolation Technology and Form Factor
Three-way galvanic isolation, common to isolation amplifiers in advanced signal conditioners, enhances system safety and eliminates typical transmission problems. Three-way isolation with test voltages of 2.5 kV between input/output/supply decouple signals transmitting from potential to potential for clear transmission. Smaller overvoltages resulting from switching also are dissipated, helping protect downstream equipment such as a PLC. DIP switches, found on comprehensive signal conditioners, optimize signal filtering by eliminating disturbances in a process signal. Via DIP switches, isolation amplifiers can be fine-tuned to match the exact frequency range of signal-garbling disturbances.
Form factor is the final piece of the puzzleāpitch, wiring and multiple features within a common profile greatly impact the overall application. A 6-mm pitch significantly reduces panel space, bringing more isolation and amplification capability into compact enclosures than previously thought. Another hallmark of well-developed signal conditioners is a jumpering system with slots at every connection point within a common outline. This enables potential commoning with a single in-line jumper, eliminating redundant wiring. Units that accommodate pluggable relays further conserve spaceāthe more features in one unit, the better the signal protection is.
Shield screening is a simple noise abatement solution for applications unsuitable to signal conditioners. Adapted to connections stemming from high-noise areas, shield screens intercept, redirect and dissipate disturbances. Typically, they consist of a shield clamping saddle, carrier, carrier rail, insulated mounting foot and mounting accessories.
Shield screens create large noise dissipation surfaces via low-impedance grounding of the line shielding, absorbing any interfering signals created by excessive noise. This noise, which normally penetrates line shielding, is directed to a functional ground through the termination point for signal protection.
Michelle Goeman, Product Manager,
Terminal Blocks and Electronic Interface,
Wago, www.wago.us
Isolation Considerations
Isolators are available in a variety of electrical variations and physical packages. First, consider the electrical function of the isolator with regards to your application. Will you need to convert, linearize, split, or otherwise change the signal in addition to isolating and noise filtering?
The power available to supply the isolator is another consideration that will help you decide on an appropriate isolator. Common choices are to power the isolator from the loopāmost commonly on the signal output side of the isolatorāor the unit can be line-powered from a separate ac or dc supply.
Physical characteristics of the isolator packaging are often as important as the electrical characteristics of the isolator. A metal case or enclosure will help block radiated electrical noise as will the design of the circuitry of the isolator. Typical isolator formats are DIN rail-mounted single- or multi-channel units installed in a control panel, or "hockey puck" style units that can be installed in a field-mounted housing supported by conduit or pipe brackets. Some manufacturers of isolators even offer high-density remote I/O systems with suitably high levels of isolation that offer the ability to convert signals to a serial or Ethernet format.
Last, follow accepted wiring practices for signal wires; use good-quality shielded twisted-pair cable, and keep signal wires in separate conduit or wiring troughs from ac wiring and other sources of high electrical noise like motors and drives.
For more information, read our white paper, "Signal Isolators, Converters and Interfaces: The Ins and Outs," at www.ControlDesign.com/signal.
Greg Feliks, Applications Engineer,
Moore Industries, www.miinet.com
10 Tips
Industrial pumps, motors and transformers create a noisy environment for electronic measurement equipment, but there are several techniques that can be used to make your signal more reliable. Here are 10 tips for measuring in a noisy environment:
- Do not run signal wires next to large electric motors or lines that carry power. The flow of current is the main source of measurement noise. Signal wires should be run in separate conduit from power lines. If power and signal wires need to cross, they should do so at a 90° angle to minimize noise intrusion.
- Use shielded cable and ground the shield to earth at the measurement end.
- Use twisted-pair cable and make a differential measurement instead of a single-ended measurement. This is a change in how the instrumentation may be set up. With this configuration the signal (+) and signal (-) lines are each sampled using separate channels. By measuring the difference between the two, any mutual or "common" noise is eliminated. Twisted-pair lines ensure an even spread of noise between each wire from the sensor.
- Use a higher-level voltage output setting from the sensor. By increasing your signal level, the noise will be proportionally smaller and have less of an impact on your measurement.
- Use shorter wires. In other words, move the measurement system closer to the signal being measured. Once the measurement has been digitized, it is much less susceptible to noise. For example, if you have to measure over a distance of 50 ft, it is better to run 49 ft of Ethernet cable and 1 ft of signal wire than 1 ft of Ethernet cable and 49 ft of signal wire.
- Oversample and average. If you can, sample at a faster rate, then take the average to get to your desired measurement rate. For non-Gaussian noise (say noise at a single frequency), oversample rate/N = factor of rejected frequency. So oversampling at 1 kHz and averaging 100 samples gives a factor of rejected frequency of 10 Hz. This filters out both 50 and 60 Hz, since 10 is a factor of both.
- Use a software filter. If your control unit has enough processing power, you can employ a software filter. Using a software-controlled filter is advantageous because you can adjust your software filtering or smoothing algorithm based on the specific noise in your installation. Some systems on the market today use FPGAs to allow for in-line filtering at hardware speed with software flexibility.
- Use a hardware filter. Some I/O modules have filtering circuitry built in. One advantage of a hardware filter over a software filter is that it is a drop-in solution, but the disadvantage is that you have to know the frequency of your signal and your noise before purchasing because most I/O filtering modules have discrete settings.
- Remove the errors with calibration. With your wiring installed, disconnect the sensor and short the signal (+) to the signal (-) of the leads coming from your measurement system. Run the acquisition channel as fast as possible. You should read zero. The signal that does appear on the line is the noise that is specific to your installation. Analyze this signal for frequency components, dc offsets and cyclical transients. Use this information to remove these features from your sensor once you reconnect it. The faster you can sample, the more information you will be able to gather from your calibration signal.
- Use current-based sensors. Many sensors have an amplifier option that will output a 4-20 mA signal, which would be immune to the noise caused by flowing current.
The tips above can also provide some guidance as future systems are purchased. Measurement and control units that can sample faster, are freely programmable, and have faster processors or programmable FPGAs might be more expensive at first, but can recoup the cost when it comes to working through noisy environments.
Brett Burger, Product Marketing Manager,
Data Acquisition Systems,
National Instruments, www.ni.com
Disturbance Strategies
Even in signal conditioning, prevention is the best medicine. Don't tell my manager I said this, but why spend the money on a signal conditioner device if not needed? I'm looking at this also from an accuracy viewpoint. Why go through the hassle of changing something back to the way it was originally to only get close? It just isn't the same.
The first place to start should be in selecting the correct wire size, type and jacketing insulation for your signal cabling. Though the exception (already) is when it comes to extending thermocouple wiring, it might be best to convert the signal to a more robust 4-20 mA signal. When in doubt, use shielded twisted-pair (STP) cable. If you must use multi-pair cable, try to keep your low-voltage signal wires separate from power wiring, even low-voltage power conductors.
Part of the design layout should consist of strategically planning to route your low-voltage signal wiring. When possible, around high-voltage or electrical-noise areas, do not run low-voltage analog signal wiring (<30 V) parallel with higher-voltage and discrete wiring in the same conductor or wire duct. Just following these low-cost measures can help avoid signal disturbances caused by inductive coupling.
The other issue concerning the wiring medium and protecting analog signals from electrical noise influences is the connection. When stripping off the jacketing and un-shielding the individual conductors, try to keep the individual conductor exposure to a minimum. Best practice is to terminate the drain/shield wire in the higher-level enclosure and at the sensor or junction box end, cutting and taping off the drain/shield immediately as it is exposed at the cable jacket. The exception to this would be in cases where the sensor itself is grounded, such as a grounded thermocouple sensor. Before terminating the shield or drain wire, cover it with shrink tubing to protect any transferring of coupled electrical noise.
For further information on proper cabling and connection techniques, see IEEE 518, "Guide for the Installation of Electrical Equipment to Minimize Electrical Noise Inputs to Controllers From External Sources." For grounding and bonding standards, I also recommend referring to the NFPA 70.
Once these non-invasive, less costly measures are done, look at the analog signal itself. Industry has pretty much standardized on the 4-20 mA signal because of its comparative robustness, live zero aspect, and historical issues. Compared to voltage analog signals, current signals are not as easily affected by noise and voltage drop due to resistance in the conductor. That said, if the cable runs are short enough, a voltage drop/signal difference might not be noticeable. This is one reason you'll find more voltage analog signals (e.g., 0-10 Vdc, -10 to +10 Vdc) used in machine building and factory automation than in process automation, where long conductor runs are more common.
Millivolt-range analog signals will be a bit more easily influenced by electrical noise and conductor resistance, so it's best to convert them to a 4-20 mA signal as soon as possible, before going past any electrical noise influences. Some of the more common devices that transmit a millivolt signal are RTD and thermocouple temperature sensors, and strain gage sensors and load cells. If it is determined that converting to a 4-20 mA signal would be best, you will probably have to change the controller analog input that the signal goes into, or convert the 4-20 mA signal back to the original analog type.
In machine and factory automation, this should bring us to the point where, if the analog signal is not in an acceptable state, a signal conditioner will most likely need to be used. The purpose of most signal conditioners is to convert signals, isolate ground loops, and filter off coupled electrical noise, amplification, and linearization of converted temperature signals.
First, look to see if a signal conversion or matching is needed. Some signal conditioners are known as universal signal conditioners. These will usually be either software or DIP switch, programmable to match multiple signal combinations. They are usually larger and more costly than signal-specific signal conditioners, but usually cover any unplanned signal changes you might run into. If you know what signals you need, are limited by space, or looking to cut costs, then choose a specific signal converter if possible. Some do no conversion at all and just condition the signal. These are usually the most cost-effective.
Filtering of electric interference, or noise, is an unwanted signal that can cause intolerable error in an electronic control or measurement system. The effects of RFI and EMI can cause unpredictable errors in instrumentation performance and can even result in equipment failure. An industrial signal conditioner should include a low-pass filter to prevent noise from causing erroneous errors to the measurement system. Typical low-pass filter levels start below 60 Hz frequency. Some signal conditioners will have selectable options to the level at which the low-pass filter cuts off. This selectable option might be desirable if there is a need for a fast response time. The higher the filter level, the quicker the response to time.
Signal conditioner isolation is another key function, and is used to separate unwanted signals. This could be analog or digital isolation, such as transformers and optocouplers. Both analog and digital isolation see use in some designs, and many signal conditioning modules will contain one or both components. In general, transformers are a little more electrically rugged and can handle larger transient voltage spikes than optocouplers. Transformers can also run at fast speeds, perhaps up to 1 GHz, while optos are limited to <10 MHz.
Proper, accurate process control via analog signals is not rocket science, but it does take some careful planning.
Derek Sackett, Product Marketing Specialist,
Analog Products,
Phoenix Contact, www.phoenixcon.com
Indeed, "cleaning" or "conditioning" analog signals in high-electrical-noise areas is a typical application for most signal conditioners. However, many times in the control system design world, specifically when it involves a high amount of analog signals, it is an afterthought reflected upon while commissioning the system and experiencing those "measurement inconsistencies," rather than at the design phase.
Experienced control system designers typically specify signal conditioning devices in the design, therefore saving painful and costly troubleshooting later. Regardless, when the need for signal conditioners is revealed, one must pay attention to a couple things when selecting them.
The first thing to consider is that the primary function of the signal conditioning device is its electrical isolation capability. In this case, the signal conditioner is working as a signal isolator to break ground loops or to protect the control system from potential hazardous events on the sensor/input side, such as lightning, over-voltage conditions, etc. Unless it is an input loop-powered or output loop-powered device, if powered by ac (115 or 230 V) or dc (24 V), the device must have three-way galvanic isolation: input to output, input to power supply, and output to power supply. If relay outputs are required, then five-way galvanic isolation level is required, between input, output, power supply, relay contacts and ground. The most common type of galvanic isolation used for signal conditioners is optical, using optocouplers. Most decent signal conditioners nowadays do offer this type of isolation, but given the abundance of different manufacturers, it's important to check the data sheets to make sure that is the case. Also, the level of isolation must be considered. A typical level of isolation is around 1500 V. Usually, the higher the isolation level of a particular device, the longer it will last in an electrically noisy environment.
Secondly, if the signal conditioner is supposed to work as a signal converter or as a signal transmitter, then the accuracy, stability and response time of the signal output is something to look at before purchasing. A typically good level would be ±0.05% of output full scale for accuracy, ±0.01%/°C for stability and 100 ms for output response time.
The signal transmitters are usually loop-powered devices (also called a two-wire device) used primarily in remote locations, relatively far from the control system, but close to the sensors to reduce input signal error readings. In this case, the output loop-powered option (two-wire only used for both output and power) is also crucial for saving wiring costs. The typical signal output is a 4-20 mA signal, which can travel with relatively minimal error on an 18-20 gauge shielded twisted-pair wire up to 1000 ft away, using 24 Vdc loop power.
If mounting space is an issue, then the multi-channel type devices can provide some help. (two or four channels per device, fully isolated). Considering that the quality of your process measurement or the safety of your control system is only as good as the quality of your signal conditioner, it is important to consider only trusted suppliers for all your signal conditioning needs.
Regarding the wiring and installation of signal conditioning devices, it is important to consider that poor wiring practices can make good, high-quality signal conditioners useless or ineffective. This can occur if the signal leads share the same conduit as the power mains. If a signal conditioner voltage output must drive two or more loads with a voltage signal, it is recommended to have individual leads from the signal conditioning output to the input of each driven load. This will avoid additional ground loops at the device level.
To avoid magnetic coupling issues, the signal leads must be kept away from ac magnetic field sources such as motors, transformers or large relays. If there is no way around these devices, then use a twisted pair of conductors for each signal, with 10-12 twists per foot.
To avoid capacitive coupling issues with the signal leads from sources such as SCR drives, relay coil circuits, welders and fluorescent lamp conductors, a shielded cable must be used, and the shield should not be connected to anything. If the signal conditioner is mounted near such sources, it is highly preferable to have the signal conditioner provided with a metal housing. This will also prevent radio interference issues.
Dan Dudici, Business Development and Product Manager,
Invensys Operations Management, www.invensys.com
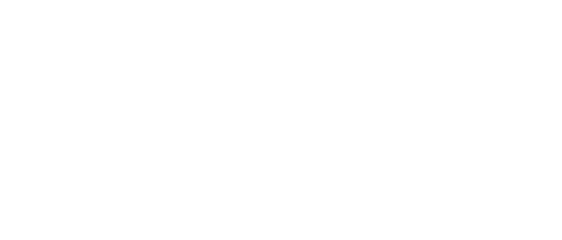
Leaders relevant to this article: