By Joe Feeley, Editor in Chief
To achieve needed performance, machine controls engineers quite naturally focus on the motion components—be they mechanical, electromechanical or electronic. Strict attention to the selection of servo motors, drives and their controllers, or even lineshafts and takeoffs in some cases, is where precision and accuracy of machine motion systems is optimized.
For many applications, however, those same engineers and machine builders have to pay an equal measure of attention to the structural framework in which that motion system operates, particularly for machines and applications in which performance, speed and cost maintain a delicate balance.
That's the case with today's waterjet cutting technology supplied by machine builder Omax (www.omax.com), Kent, Wash. Once considered a specialized and expensive approach, it is now cutting nearly everything from stone and metal to food products and paper.
Omax raised its global market competitiveness recently with a new linear motion and assembly design that resulted in introduction of a low-cost, waterjet cutting machine economical enough for any price-conscious market, including China, where Omax exports and sells machinery.
Broader Use
"People still see waterjet cutting as a specialty technology, which it isn't anymore," says Dr. John Olsen, vice president of operations at Omax. "It's easier to learn to use a waterjet than almost any other machine." Olsen says state-of-the-art waterjets now can do precision cuts and produce fine shapes, while maintaining high speed and throughput, making these machines entirely competitive with other traditional cutting methods. "With waterjet cutting, you achieve great material savings over milling because nesting is possible. It's faster than laser with materials thicker than 1 in., and it can machine copper, stone and other materials not cut by laser," says Olsen. "It might be slower than plasma cutting, but there's no slag and heat-affected edges, and while it's slightly less precise than wire EDM, it's much faster."
Omax, states Olsen, is the only fully integrated waterjet company that designs and produces its own pump, high-pressure plumbing, machine controller, software and tables.
Machine control is accomplished via a standard PC with all computation done in the PC. "The motion profile follows a drawing made on the PC, and the PC manages all acceleration and velocity profiles to control the jet geometry," states Olsen. "The controller anticipates the taper in the cut and tilts the head to produce square edges. Data sent via USB to a real-time microprocessor in turn sends timed signals to motors. Motors are either pulse and direction servos or stepping motors." In newer machines, says Olsen, the motion is provided by a traction drive, like a railroad, with position held by feedback from a linear tape. This, he says, gives the accuracy of a linear motor at greatly reduced cost.
So, What's the Problem?
The conventional approach to making cutting machines involves a lot of machining labor, says Olsen. "The key is to design a machine that has good precision but doesn't require a lot of skilled labor to produce it," he explains. "In China, you're competing with machine builders who have as low an overhead and labor cost as anybody and virtually all of the buyers there focus primarily on price. So between reducing labor requirements and some of our proprietary technology features we've developed, we saw we could offer good performance, but at a lower cost."
As noted, the Omax control system is PC-based. "PC prices are quite low now," says Olsen. "Chinese machine builders, on the other hand, tend to use standard machine tool controllers, so they don't interface with PCs. So if we build our machine structure in China and bring over the automation and controls, we can compete in that market."
Through extensive R&D, Omax developed a new Maxiem line of machines to provide proven technologies in a highly productive, cost-efficient package, adds Olsen. He says Omax focused on reducing its time-to-build, material costs and the need for specialized assembly methods, all the while maintaining machine throughput, accuracy and durability.
Measuring approximately 15-ft long by 7-ft wide, the Maxiem waterjet is a three-axis machine with a bridge gantry that holds the waterjet cutting head as it travels back and forth across the x-axis, with the cutting head moving side-to side and up-and-down along the y- and z-axes (Figure 1).
Figure 1: About 15-ft long by 7-ft wide, the Maxiem waterjet is a three-axis machine with a bridge gantry that holds the waterjet cutting head as it travels back and forth across three axes of motion.
OMAX
A New Framing Approach
Omax designers already were familiar with products to meet these requirements, but in a different context. "Aluminum structural framing from Rexroth (www.boschrexroth.com), often used for guarding, assembly stations and machine support in other industries, appeared easy to configure into a linear motion solution where the linear components are built-in directly to the aluminum profiles," says Guglielmetti (Figure 2). "The framing-turned-linear-motion products used in this application include a stout piece of Rexroth extruded aluminum structural framing coupled with the DGE dynamic linear elements to allow the cutting head to move side-to-side for the y-axis." Four Rexroth eLine compact ball bushings and seal kits on the z-axis complete the framing lineup.
Omax knew the framing could provide the strength-to-weight ratio and the durability we needed. "The Omax design team also knew that these products were simple to use and install, providing reduced assembly and labor costs," he adds. "The anodized extruded aluminum components required almost no machining, drilling or re-engineering and could be assembled quickly using standard hand tools, and that fit in nicely with the Omax lean manufacturing process."
Guglielmetti says the versatility of the framing "makes it easier for us to create different Maxiem machine variations for cutting larger sizes of material. The framing is a standard product, so it can be ordered from a catalog in custom lengths."
In Omax's higher-end machines, the supporting structure is provided by machined circular tubes upon which linear bearings and ball screws are mounted, says Olsen. "Positional errors are of the order of 0.001 in. with the high-end machines and 0.005 in. for the Maxiem."
Normal framing construction usually means welded steel or aluminum. "Weldments require a number of tools, floor space and environmental requirements about painting," says Kirnig. "Weldments don't offer any flexibility, and if a change is necessary it is much more time-consuming to modify a weldment—to drill and tap a new hole or a cutting torch to change the length of the machine frame or beam, for example."
Kirnig claims that the strength-to-weight ratio is very good when compared to weldments. "The same strength can be obtained with less weight," he says. "That reduces shipping and other costs."
Market Splash
The new Maxiem waterjet is well-suited for Omax's target markets. "It cuts large sizes of material with speed and precision, and it also meets the Omax goals for quality and performance at a cost-effective price," summarizes Olsen. "For our end users, the Maxiem offers expandability—new components can be attached quickly to the T-slot framing without machining."
As a result, concludes Olsen, "the Maxiem has penetrated the Chinese market, thanks in part to an innovative new design. Best of all, machines like the Maxiem promise to be instrumental in driving more widespread adoption of waterjet cutting technology in the future."
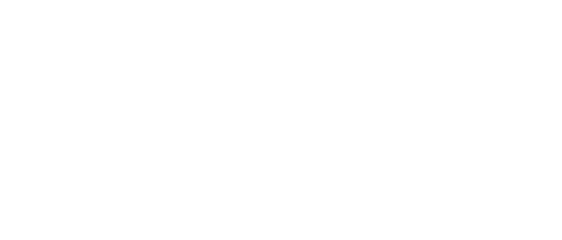
Leaders relevant to this article: