Machine-mount I/O replaces parallel wiring by extending the network into the machine. Despite its upside, adoption has been relatively slow. However, recent changes in terminal nodes, wire schemes and IP protection have made machine-mount I/O more attractive.
"Originally machine-mount I/O was limited in its flexibility with fixed I/O boxes," explains Jason Haldeman, product marketing lead specialistāautomation, Phoenix Contact (www.phoenixcon.com). "Today machine-mount I/O supports a more modular approach, allowing the stations to be customized to your exact I/O needs with the incorporation of multi-network support for digital, analog and even wireless I/O signals."
John Harmon, networking & connectivity product manager, Balluff (www.balluff.com), believes the reduced costs drive the attractiveness of machine-mount I/O. "Initial node costs are about half of what they were just 10 years ago," he says. "And today we have higher-performance I/O networks, more network cable options and an overall acceptance and deeper knowledge at the floor level."
Machine-mount I/O has the ability to concentrate multiple sensor inputs or actuator outputs on one IP67 interface, says Stephen Arnold, senior automation product marketing specialist, Schneider Electric (www.us.schneider-electric.com). "These IP67 blocks connect to the control system with common, open-architecture fieldbus networks such as CANopen, eliminating the expense and support issues surrounding proprietary network solutions," he explains. "These I/O blocks also communicate on Ethernet networks such as Ethernet Modbus TCP/IP and EtherNet/IP. When these networks are used on an I/O block, the application benefits from the speed and bandwidth available on the network but keeps the price of sensors and actuators low since the network doesn't need to be embedded in each I/O device."
The IP67 protection rating is comparable to NEMA 6 and 6P, meaning the devices are resistant to harsh environments, moisture and dust, says Kurt Wadowick, I/O systems specialist, Beckhoff Automation (www.beckhoff.com). "Today, line, tree or star topologies are possible with machine-mounted boxes."
The general concept is to locate the control component as near to the actuators and sensors as possible, explains Bruce Centofanti, sales manager, fieldbus I/O and control technology, B&R Industrial Automation (www.br-automation.com). "This can reduce or shorten wiring runs to devices and results in cleaner design and construction cost savings," he says. "Some manufacturers offer an IP67 I/O that delivers faster update rates to the master PAC, PLC or distributed control system."
Machine-mount I/O has been widely accepted in European markets for several years now, says Aaron Henry, marketing manager, Murrelektronik (www.murrinc.com). "Builders in the U.S. are beginning to understand the benefits of distributed I/O systems," he says. "IP67 is an added level of protection for most machine builders who struggle to reach IP65 with most current field-wired installations. Molded cordsets, captured gaskets and less upfront preparation also allow machine builders to inventory fewer parts, have less pre-assembly time and reduce the number of installation errors."
Several customers have mounted IP65/67 I/O directly onto their machines and reduced installation and startup costs because direct mounting requires no enclosure, as well as less wiring, conduit and space, explains Matthew Thornton, product marketing manager, distributed I/O, Siemens Industry (www.industry.siemens.com). "It also enables faster troubleshooting when tracing out the wiring," he says.
IP67-rated and higher-rated control components have made machine-mount I/O viable, explains Tracy Lenz, senior product supportāWago-I/O-System and advanced electronics (www.wago.com). "While IP67-grade designs make them physically robust, electromagnetic compatibility (EMC) issues play a role in reliability," says Lenz. "Machine-mounting options and layout are what make or break IP67-grade I/O. Does the design provide more than one mounting option? Can it be DIN-rail mounted or directly screwed to machines? Are adapter plates available?
Comprehensive designs provide these and other conveniences such as clips, making it easy to snap components together. Good designs also accommodate international guidelines, such as CNOMO, ensuring assembly drill holes fit standardized machines. Well-developed IP67 components employ integrated shield plates and metallized housings."
In reality, machine-mount I/O can be many different things, explains Karie Daudt, senior product manager, Turck (www.turck.com). "For example, an IP20 I/O node in a small enclosure is technically machine-mount I/O," says Daudt. "The difference is that the points themselves still are physically landed on the I/O rather than terminal blocks. In this solution, you still hardwire the points themselves."
Machine-mount I/O eliminates the traditional junction box, explains Look-Thong Wong, product manager, distributed I/O, Rockwell Automation (www.rockwellautomation.com). "With self-configurable machine-mount I/O, each channel can be an input for a sensor or an output to an actuator without any user configuration," he says.
Additional intelligence also has been added to these remote I/O drops for additional preprocessing and diagnostics, thereby reducing network traffic and increasing response time for time-critical applications, explains Egon Hillermann, product manager, automation, ABB (www.abb.us).
"Decentralized I/O systems are commonly available in the market but require a vast array of wires," says Susanne Walker, product managerāadvanced connectivity, Weidmüller (www.weidmuller.com). "Cable-based solutions, especially for bus communication, can be problematic or even impossible in applications with moving system parts such as drag chains or slip rings. Flexing stress can cause cable breakage and compromise the integrity of the equipment and the entire manufacturing line."
While wireless I/O modules don't eliminate cabling altogether, they do create wireless "islands" that can be incorporated into a standard bus system seamlessly, explains Walker. "Wireless solutions make the implementation of decentralized I/O a viable option for demanding applications such as robotic arms, while reducing the complexity of the wiring needs, simplifying maintenance and optimizing machine up-time."
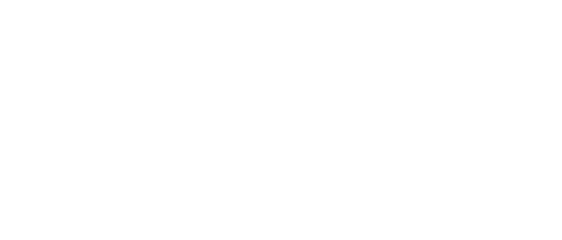
Leaders relevant to this article: